Massenproduktion und 3D-Druck: Wo stehen wir?
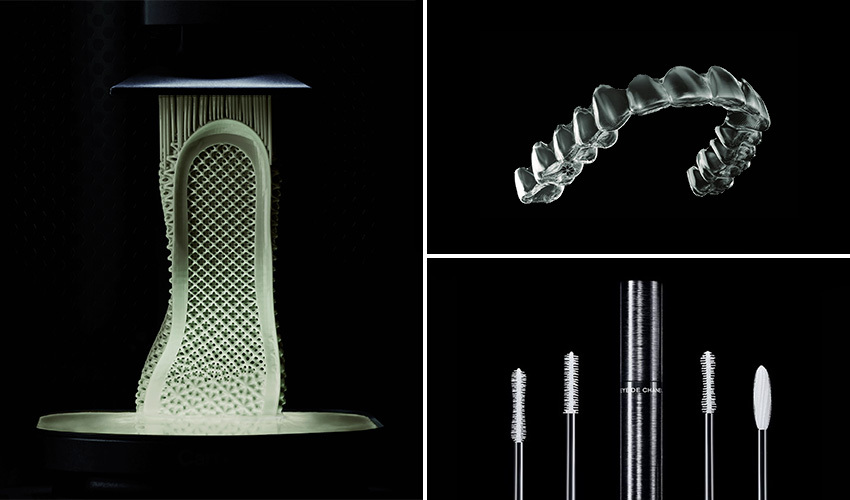
Der 3D-Druck wird nicht mehr ausschließlich für die Entwicklung von Prototypen eingesetzt, sondern hält nun auch Einzug in die Produktion von Endteilen. Obwohl seine Machbarkeit in der Großserienfertigung aufgrund der Kosten und Produktionszeiten manchmal in Frage gestellt wurde, ändert sich diese Wahrnehmung. Immer mehr Unternehmen zeigen, dass es möglich ist, Qualität, Individualisierung und Effizienz in der Serienproduktion zu kombinieren. Von industriellen Bauteilen bis hin zu kundenspezifischen Artikeln setzt sich der 3D-Druck als echte Lösung für die Massenproduktion immer mehr durch. Wir haben daher einige konkrete Fälle untersucht, in denen die additive Fertigung bei der Herstellung von Tausenden von Serienteilen eine wichtige Rolle gespielt hat, die ihr Potential unter Beweis stellen und die traditionellen Produktionsmethoden in Frage stellen.
Adidas und Carbon: Massenproduktion von Laufschuhen
Im Jahr 2016 ging Adidas eine Partnerschaft mit Carbon ein, um die Herstellung von Laufschuhen zu revolutionieren. Im Jahr 2017 brachten die beiden Unternehmen Futurecraft 4D auf den Markt: die revolutionäre Mehrzonen-Zwischensohle, die in einem einzigen Druckvorgang hergestellt wird und eine innovative Netzstruktur aufweist. Gemeinsam starteten sie die Produktion von 100.000 Paar Futurecraft 4D Schuhen mit 3D-gedruckten Zwischensohlen. Auf Futurecraft 4D folgte 2018 AlphaEDGE, bei dem im Vergleich zum Vorgängermodell die Stellen direkt unter der Ferse, dem Punkt, auf den der Läufer beim Laufen den größten Druck ausübt, dicker gemacht wurden. 2021 kam die Adidas 4DFWD auf den Markt, die dritte Generation der 4D-Zwischensohle, die sich die physikalische Eigenschaft der Anisotropie zunutze macht, um den Schuh bequem und funktional für das Laufen zu machen. Die neue Zwischensohle, ebenfalls eine Zusammenarbeit zwischen Adidas und Carbon, wird mit dem Carbon DLS™-Verfahren hergestellt und verwendet das Elastomer EPU 44, eine aktualisierte Version des früheren EPU 41, das im Futurecraft 4D verwendet wurde. Dieses Material der neuen Generation ist hochelastisch, reißfest und dank einer zu 40 % biobasierten Formulierung auch nachhaltiger. Der Adidas 4DFWD ist die neueste Entwicklung der Marke, die technologische Innovation, fortschrittliches Design und Nachhaltigkeit in industriellem Maßstab vereint.
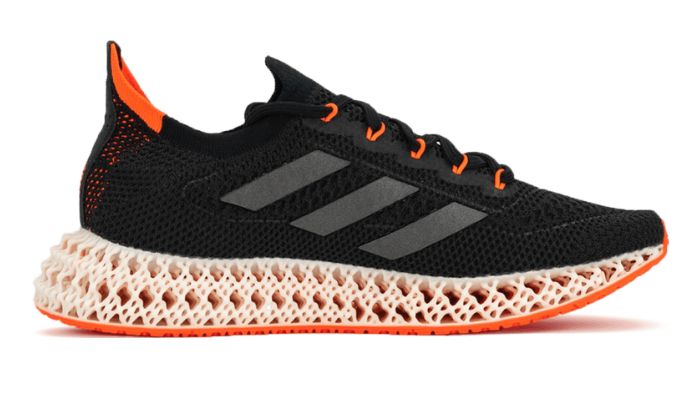
Bild: Carbon
Align Technology nutzt den 3D-Druck für die Massenproduktion von Zahnersatz
Wenn es um Massenproduktion im 3D-Druck geht, ist Align Technology ein hervorragendes Beispiel. Das amerikanische Unternehmen ist ein Spezialist für kieferorthopädische Lösungen, die mit 3D-Druck hergestellt werden, insbesondere als Erfinder von Invisalign. Align Technology war schon immer ein starker Befürworter des 3D-Drucks und des 3D-Scannens, wie die Übernahme des Herstellers von intraoralen 3D-Scannern iTero im Jahr 2011 und des Herstellers von Polymer-3D-Druckern Cubicure im Jahr 2024 zeigen. Der 3D-Druck wird von Align Technology für alles verwendet, von den Formen für die Aligner-Flaggschiffe bis hin zu einem Gaumenexpander, dem ersten direkt in 3D gedruckten kieferorthopädischen Gerät des Herstellers. Wenn man bedenkt, dass das Unternehmen bis zu einer Million Aligner-Teile pro Tag herstellt und sich dabei auf den 3D-Druck für die Herstellung von Hunderttausenden von Aligner-Formen verlässt, ist das keine geringe Leistung. Ein perfektes Beispiel dafür, wie man Individualisierung, Massenproduktion und 3D-Druck miteinander verbindet!
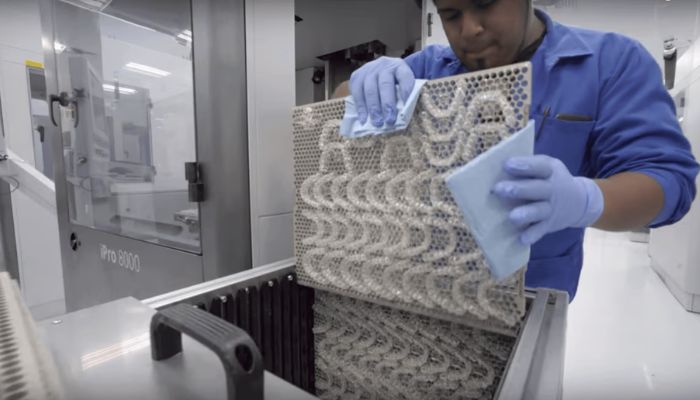
Bild: Align-Technologie
Chanels Mascara-Bürsten
Vielleicht erinnern Sie sich noch an die Volume Révolution Mascara von Chanel: Diese wurde 2018 auf den Markt gebracht und hatte als Besonderheit ein Bürstchen aus dem 3D-Drucker. Das Projekt sorgte damals für viel Aufsehen, weil es sich um eine echte Massenproduktion handelte. Erpro 3D Factory, das Startup, das die Bürsten druckte, behauptete, dass es jede Woche 250.000 Bürsten mit 15 Maschinen herstellen könne. Seit diesem Projekt haben die beiden Marken E.Y.E. eingeführt, einen maßgeschneiderten Service für 3D-gedruckte Mascaras. Konkret kann man mithilfe einer App auf einem Tablet seine Mascara-Bürste aus zehn Modellen auswählen. Diese wird dann mit PA11 im 3D-Druckverfahren hergestellt. Es ist nicht genau bekannt, wie viele Bürsten bisher in 3D gedruckt wurden, aber sicher ist, dass dieses Beispiel alle Vorteile der additiven Fertigung zeigt und dass es möglich ist, Personalisierung und Massenproduktion zu kombinieren!
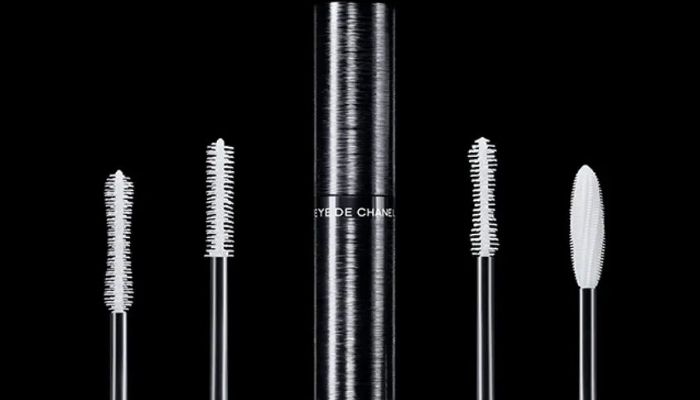
Bild: ERPRO / Chanel
GE Aviation
GE Aviation hat mehrere Meilensteine in der additiven Fertigung erreicht. Das Werk von GE Aviation in Asheville, North Carolina, hat im Laufe der Jahre mehr als 100.000 Turbinenkomponenten aus Ceramic Matrix Composite (CMC) hergestellt, während das Werk in Auburn, Alabama, mehr als 100.000 additiv gefertigte Düsenkomponenten produziert hat. CMC ist ein fortschrittlicher Werkstoff mit Siliziumkarbidfasern, der nur ein Drittel der herkömmlichen Metalllegierungen wiegt und doppelt so hohe Temperaturen verträgt, was zur Verbesserung des thermischen Wirkungsgrads von Triebwerken beiträgt und damit den Kraftstoffverbrauch und die Kohlenstoffemissionen verringert. Das Werk in Asheville ist der erste Standort der Luftfahrtindustrie für die additive Fertigung von Triebwerkskomponenten aus CMC, die 2014 aufgenommen wurde. Das Werk in Auburn begann 2015 mit der Produktion von Treibstoffdüsen und war der erste Standort der Branche für die Massenproduktion von Triebwerkskomponenten mit additiver Fertigung.
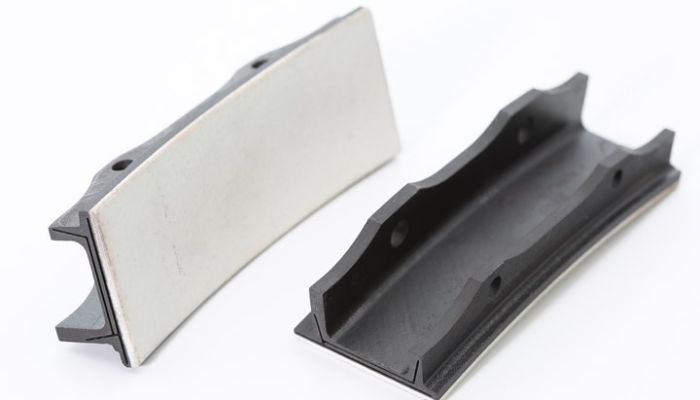
3D-gedruckte Turbinenkomponenten bei CMC (Bild: GE Aviation)
Photocentric druckt 3D-Plaketten für Badgemaster
Ein weiteres Beispiel für den Einsatz des 3D-Drucks in der Massenproduktion ist die Zusammenarbeit zwischen dem britischen Unternehmen Badgemaster und dem 3D-Druckerhersteller Photocentric. Da Badgemaster kurzfristig individuelle Plaketten herstellen musste, wandte sich das Unternehmen an die Harz-3D-Drucktechnologie von Photocentric, wobei die LC Magna-Maschinen zum Einsatz kamen. Mit dieser Methode konnten 30.000 Endteile schnell und in hoher Qualität hergestellt werden, ohne dass herkömmliche Formen oder Werkzeuge benötigt wurden. Die Entscheidung für diese Technologie war zum Teil auf die logistischen Herausforderungen zurückzuführen, die sich aus der Pandemie ergaben und die konventionelle Produktion einschränkten. Diese Zusammenarbeit unterstreicht das Potential der additiven Fertigung, auf die Anforderungen der Industrie zu reagieren und schnelle, flexible und effiziente Lösungen zu bieten, selbst in Szenarien mit hoher Nachfrage.
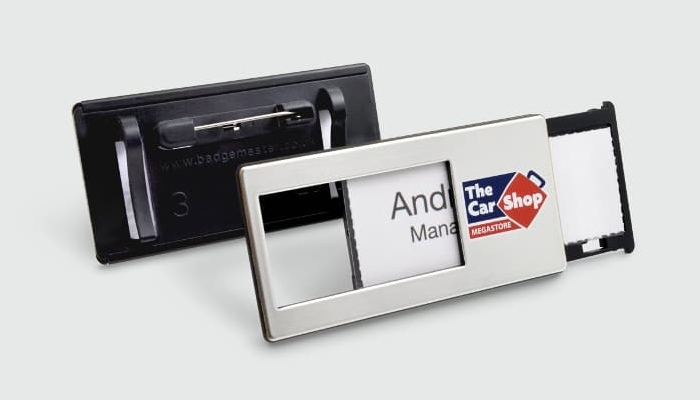
Bild: Badgemaster
Cobra verändert die Welt des Golfsports durch 3D-Metalldruck
Das Unternehmen enthüllte den ersten Putter, der mithilfe der HP Metal Jet-Technologie in Massenproduktion hergestellt wurde, und läutete damit eine neue Ära der Golfausrüstung ein. Sein Ziel: Innovation und Massenproduktion miteinander zu verbinden und dabei die Kosten unter Kontrolle zu halten. Seit mehreren Jahren erforscht Cobra Golf die Möglichkeiten der additiven Fertigung, um immer leistungsfähigere Schläger zu entwickeln. Dank der HP Metal Jet-Technologie haben die Ingenieure von Cobra Golf eine völlig neue Designfreiheit, die es ihnen ermöglicht, Strukturen zu entwerfen, die mit herkömmlichen Methoden nicht herstellbar sind. Früher war der 3D-Metalldruck auf Prototypen beschränkt, jetzt erreicht er eine Qualität und Geschwindigkeit, die für eine Produktion in großem Maßstab ausreicht. In Zusammenarbeit mit HP konnte Cobra die Entwicklung seiner Schläger beschleunigen und sie der breiten Öffentlichkeit zugänglich machen.
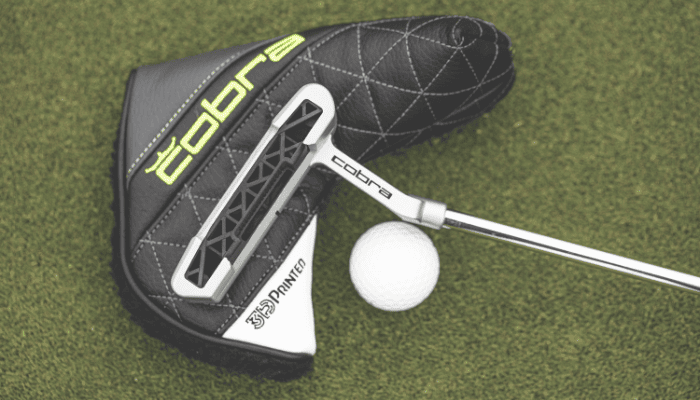
Bild: HP
Stryker druckt medizinische Prothesen in Serie
Eine weitere Initiative, die additive Fertigung und Massenproduktion kombiniert, kommt aus dem medizinischen Bereich. Seit 2013 hat das irische Unternehmen Stryker seine Produktion verbessert, indem es rund zwei Millionen Prothesen mithilfe von 3D-Drucktechnologien hergestellt hat. Dazu hat es ein eigenes Material namens Tritanium entwickelt, eine speziell für den Druck konzipierte Titanlegierung, mit der es sowohl eine zementfreie Knieprothese, Triathlon Tritanium genannt, als auch drei verschiedene Wirbelsäulenprothesen aus Tritanium hergestellt hat. Aber wie funktioniert das Triathlon Tritanium System? Diese Prothese kombiniert ein fortschrittliches Design mit einer hochporösen biologischen Fixierungstechnologie, die mit SOMA-Werkzeugen entwickelt und mit der proprietären Technologie von Stryker hergestellt wird. Durch die Analyse des Lebenszyklus der Knieprothese hat das Unternehmen zahlreiche Vorteile der additiven Fertigung aufgezeigt, sowohl im Hinblick auf die Wirtschaftlichkeit als auch auf die Einsparung von Material und Umweltressourcen. Aber das ist noch nicht alles. Stryker ist der Additive Green Manufacturing Trade Association beigetreten, die sich zum Ziel gesetzt hat, den Einsatz des 3D-Drucks in der Industrie zu fördern, um immer nachhaltigere Fertigungsverfahren zu entwickeln.
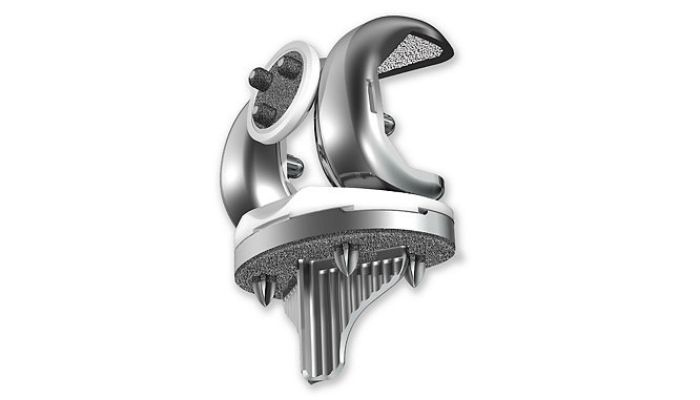
Das Bild zeigt das Modell Triathlon Tritanium, die unzementierte Knieorthese.
Bosch stellt chirurgische Geräte mit Lithoz-Technologie her
Es ist kein Geheimnis, dass Keramik ein wichtiger Akteur in der additiven Fertigungsindustrie geworden ist. Bosch Advanced Ceramics ist es gelungen, die Vorteile dieses Werkstoffs und des 3D-Drucks zu nutzen, indem es die Produktion von hochpräzisen medizinischen Komponenten gesteigert hat. Dabei handelt es sich um Isolierhülsen, eine Komponente von laparoskopischen Instrumenten, die in der invasiven Chirurgie eingesetzt werden. Nach einer erfolgreichen Bemusterungsphase war das Unternehmen in der Lage, 1.400 Komponenten in einer einzigen Charge zu drucken. Mit dieser Menge könnte es eine jährliche Nachfrage von bis zu 20.000 Stück decken. Die Entwicklung dieser Isolierhülsen war aufgrund ihrer geringen Abmessungen – ein Außendurchmesser von nur 1,3 mm und eine Wandstärke von 90 Mikrometern – eine Herausforderung. Um diese Detailgenauigkeit zu erreichen, setzte Bosch Advanced Ceramics die LCM (DLP)-Technologie von Lithoz ein, die auf einem Schicht-für-Schicht-Photopolymerisationsverfahren basiert, mit dem komplexe Geometrien mit hoher Qualitätskontrolle und Präzision hergestellt werden können.
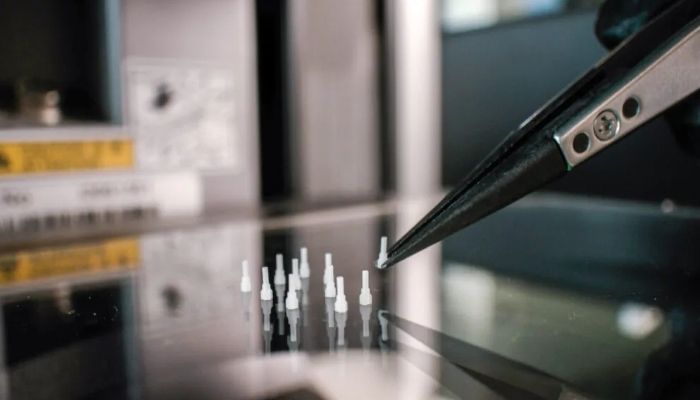
3D-gedruckte keramische Komponenten, die für die Verwendung in laparoskopischen Instrumenten bereit sind (Bild: Lithoz)
Was halten Sie von diesen Beispielen, bei denen 3D-Druck für Massenproduktion genutzt wird? Lassen Sie uns dazu einen Kommentar da, oder teilen Sie es uns auf Facebook oder LinkedIN mit. Möchten Sie außerdem eine Zusammenfassung der wichtigsten Neuigkeiten im 3D-Druck und der Additiven Fertigung direkt und bequem in Ihr Postfach erhalten? Dann registrieren Sie sich jetzt für unseren wöchentlichen Newsletter.