Studie zeigt, wie maschinelles Lernen für die LPBF-Technologie eingesetzt werden kann
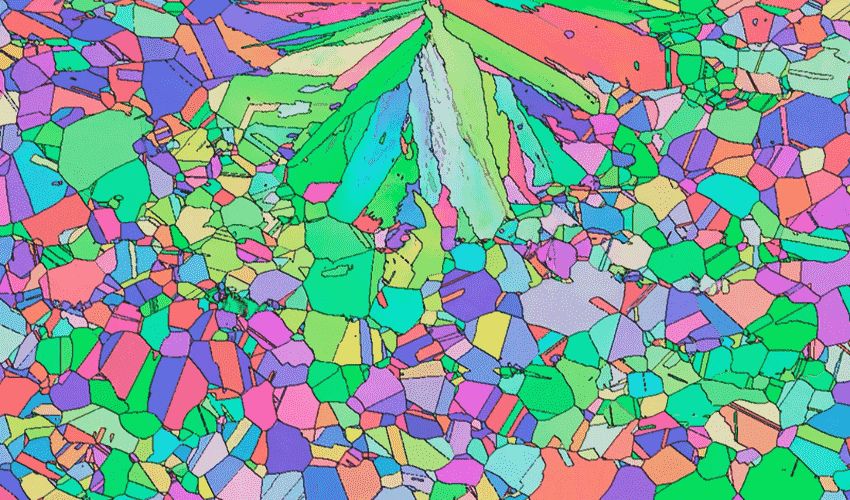
Forscher am Johns Hopkins University Applied Physics Laboratory (APL) haben einen neuen Ansatz entwickelt, der 3D-Druck mit maschinellem Lernen verbindet. Es handelt sich um ein Modell, mit dem sie Simulationen erstellen können, die für die Überprüfung der Produktion von Teilen, die durch Laser Powder Bed Fusion (LPBF) hergestellt werden, nützlich sind. Maschinelles Lernen, auch bekannt als machine learning (ML), gehört zu einem Zweig der Künstlichen Intelligenz (KI) und kann in verschiedenen Bereichen eingesetzt werden, von der Medizin bis zur Luft- und Raumfahrt.
Die vom APL entwickelte Technik ermöglicht es, die Mikrostruktur, die sich auf dem Druckbett bilden wird, anhand von Messungen an der einzelnen Pulverschicht vorherzusagen. Dazu haben die Forscher Modellierung und rechnerische Simulation eingesetzt. Diese Vorhersagen des zu erzeugenden Objekts ermöglichen ein frühzeitiges Eingreifen im Falle von Fehlern. Dies würde nicht nur Zeit, Material und Kosten sparen, sondern auch die Produktion von LPBF-Teilen exponentiell steigern.
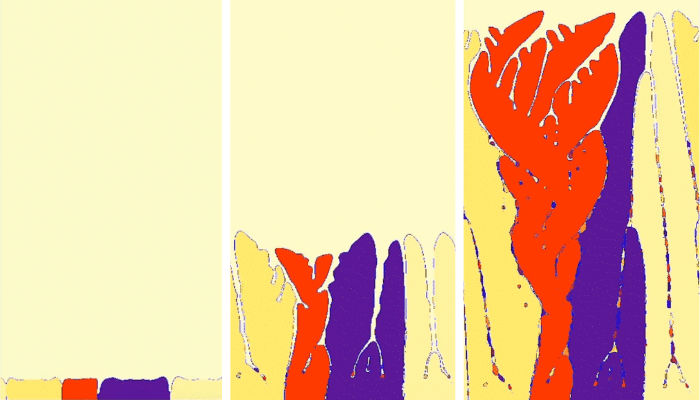
Dieses Bild veranschaulicht den Prozess der Mikrostrukturvorhersage, der durch die Analyse der Auswirkungen von Abkühlgeschwindigkeit und Temperaturgradient auf die Kornorientierung und -größe erreicht wird.
Diese Studie ist Teil einer größeren Arbeit, die am Johns Hopkins University Applied Physics Laboratory durchgeführt wird und sich auf die Nutzung Künstlicher Intelligenz konzentriert, um die Entdeckung neuer Materialien für extreme Umgebungen zu beschleunigen. Morgan Trexler, der Ansprechpartner für das APL-Programm Science of Extreme and Multifunctional Materials in der Mission Exploratory Research and Development Area, sagte: „Dieser neue Ansatz wird von großer Bedeutung für das Design und das Verständnis der Materialbildung bei additiven Fertigungsprozessen sein und passt zu unserer Gesamtstrategie, die auf die Beschleunigung der Materialentwicklung für die nationale Sicherheit ausgerichtet ist.“
Wie kann maschinelles Lernen für LPBF nützlich sein?
Bei LPBF werden Schichten von Metallpulver mit einem Hochleistungslaser geschmolzen, um dreidimensionale Objekte Schicht für Schicht zu erzeugen. Diese Technologie eignet sich für die Herstellung stabiler Metallteile, die komplexe Geometrien unterstützen. Da sich die Pulver jedoch voneinander unterscheiden und daher verschiedene Eigenschaften haben, können die Bearbeitungsbedingungen stark variieren, angefangen bei den Lasereinstellungen bis hin zu den Wechselwirkungen zwischen den verschiedenen Pulverpartikeln. Infolgedessen können die Eigenschaften der gedruckten Objekte stark variieren.
Um diese Anwendung zu realisieren, verwendete das Forschungsteam unter der Leitung von Li Ma, leitender Ingenieur am APL, ein CFD-Modell (Computational Fluid Dynamics), um Temperaturschwankungen und Abkühlungsraten während des Druckprozesses in Abhängigkeit von der Partikelausrichtung und Partikelgröße genau zu messen. Die numerische Strömungsmechanik (CFD) ist eine Disziplin, die Computersimulationen einsetzt, um das Verhalten von Materialströmen auf der Grundlage der Gesetze zur Erhaltung von Masse, Impuls und Energie vorherzusagen. Dieser innovative Ansatz ermöglicht nicht nur eine Vorhersage der Mikrostruktur des Bauteils vor dem Druck, sondern auch eine Abschätzung der mechanischen Eigenschaften des Materials und der physikalischen Leistung des fertigen Teils.
Ali Ramazani entwickelte das erste Phasenfeldmodell für die Mikrostrukturbildung, indem er die aus dem CFD-Modell gewonnenen Ergebnisse integrierte. Dieser Ansatz verbesserte die Genauigkeit und Gültigkeit der Simulationen. Sein Beitrag war zwar bedeutend, reichte aber nicht aus, um alle Probleme der Datenerfassung zu lösen. Bei der Herstellung eines einzigen Bauteils mit der LPBF-Technologie kommt es zu Millionen von Wechselwirkungen zwischen Pulver und Laser, was einen enormen Rechenaufwand erfordert und die Simulation jedes kleinen Abschnitts extrem komplex macht.
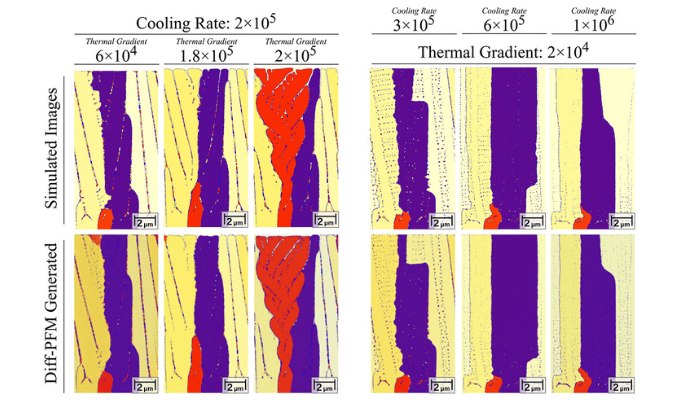
Dieses Bild vergleicht die Ergebnisse des probabilistischen APL-Diffusionsfeldmodells mit den Simulationsergebnissen. Das APL-Modell erkennt die in den simulierten Ergebnissen beobachtete Mikrostrukturbildung und das Kornwachstum genau.
Der Durchbruch kam also von Hudson Liu, einem Praktikanten des APL Student Program to Inspire, Relate, and Enrich (ASPIRE) und Highschool-Schüler an der Gilman School in Baltimore. Er entwickelte ein Modell des maschinellen Lernens, das den Bedarf an teuren Simulationen erheblich reduzieren würde. Zusammengefasst hat Hudson Liu mehrere bereits bestehende Modelle des maschinellen Lernens integriert, um ein sogenanntes „diffusion probabilistic field model“ zu entwickeln. Dieses Modell erzeugt Bilder auf der Grundlage der Abkühlungsrate und des thermischen Gradienten des LPBF-Drucks und quantifiziert Temperaturänderungen auf der Grundlage von Parametern wie dem Abstand zwischen dem Laserauftreffpunkt und dem umgebenden festen Metall.
Hudson Liu sagte: „Der Hauptvorteil dieses Modells ist seine Schnelligkeit. Unser Modell kann in Sekunden oder Minuten vorhersagen, was bei einer Simulation Stunden dauern würde“, und fügte hinzu: “Dadurch können die Forscher schnell und zu wesentlich geringeren Kosten eine breite Palette von Parametern untersuchen.“ Das Modell wurde durch eine mikroskopische Analyse des LPBF-Materials validiert. Das Training des maschinellen Lernprogramms erforderte mehr als 400 Simulationen, die am APL durchgeführt wurden.
Ein Blick in die Zukunft
Das Forschungsteam arbeitet bereits daran, neue Modelle mithilfe von Videodaten zu trainieren, die es ermöglichen werden, Mikrostrukturen sowohl in 3D als auch in 2D vorherzusagen. Mit der Zeit wird es dann möglich sein, Vorhersagen über die Mikrostrukturen größerer Bauteile zu treffen und die Ergebnisse mehrerer Laserdurchgänge zu analysieren.
Aber das ist noch nicht alles. Das Projekt, das dank interner Universitätsmittel zustande kam, hat das Interesse des Space Technology Research Institute (STRI) der NASA geweckt, das es gerne für seine eigenen Dienste einsetzen würde. Li Ma sagte: „Die NASA möchte validierte Modelle, mit denen sie vorhersagen kann, was während der Produktion passiert und wie sich das endgültige Teil verhält, ohne auf teure Experimente zurückgreifen zu müssen. Dieser Ansatz ist besonders nützlich, wenn wir an die additive Fertigung auf dem Mond oder im Weltraum denken, wo Experimente so teuer werden, dass sie praktisch unmöglich sind.“ Es wird daher nicht überraschen, wenn wir in naher Zukunft von Anwendungen des APL nicht nur in der Raumfahrt, sondern auch in anderen Bereichen hören werden.
Was halten Sie von diesem Prototyp für den 3D-Druck in der Schwerelosigkeit? Lassen Sie uns dazu einen Kommentar da, oder teilen Sie es uns auf Facebook oder LinkedIN mit. Möchten Sie außerdem eine Zusammenfassung der wichtigsten Neuigkeiten im 3D-Druck und der additiven Fertigung direkt und bequem in Ihr Postfach erhalten? Dann registrieren Sie sich jetzt für unseren wöchentlichen Newsletter.
Beschreibung des Titelbildes: Das Bild zeigt die Mikrostruktur der ausscheidungsgehärteten Nickelbasis-Superlegierung, die zur Validierung des APL-Modells und seiner Vorhersage der Abkühlungsgeschwindigkeit verwendet wurde.
*Bildnachweise: ASM International, 2024.