Komplexe Strukturen für die Luft- und Raumfahrt durch keramischen 3D-Druck
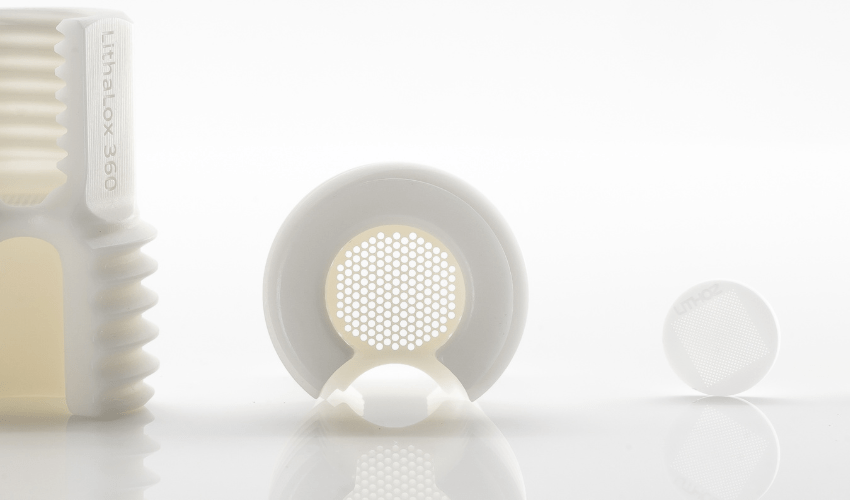
Die Industrie ist zunehmend auf der Suche nach neuen und fortschrittlichen Werkstoffen und Verfahren zur Verbesserung ihrer Produkte und die Luft- und Raumfahrt bildet hier keine Ausnahme. Die Bedürfnisse der Branche entwickeln sich mit der Einführung strikterer Anforderungen stetig weiter. Daher sind neue Technologien gefragt, die innovative und effiziente Lösungen bieten. Die additive Fertigung entwickelt sich zu einer idealen Lösung für Anwendungen in der Luft- und Raumfahrt. Einem Bericht von Research and Markets zufolge wurde der Wert des Marktes für 3D-Druck in der Luft- und Raumfahrt sowie im Verteidigungsbereich im Jahr 2021 auf 1,9 Milliarden US-Dollar geschätzt, mit einer erwarteten jährlichen Wachstumsrate von über 24 % von 2022 bis 2027. Additive Technologien bringen erhebliche Veränderungen und Vorteile für die Luft- und Raumfahrtindustrie mit sich, wie z. B. die Herstellung leichterer, festerer und komplexerer Teile, Designfreiheit, die Möglichkeit, mehrere Teile zu einer einzigen Einheit zu kombinieren, die Reduzierung der Verschwendung teurer Rohstoffe sowie Kosten- und Ressourceneffizienz.
Betrachtet man die innovativen Materialien, die im 3D-Druck verwendet werden können, so ist Keramik das erfolgreichste. Es hat sich gezeigt, dass dieses Material die notwendigen Eigenschaften besitzt, um die Anforderungen der Industrie und die hohen Standards in der Luft- und Raumfahrt zu erfüllen. Zu den Unternehmen, die sich auf die additive Fertigung von Keramik spezialisiert haben, gehört der österreichische Hersteller Lithoz, der die LCM-Technologie (Lithography-based Ceramic Manufacturing) für komplexe Teile mit hoher Auflösung entwickelt hat. Das Unternehmen hat den Verkauf seiner keramischen 3D-Drucklösungen und den Umsatz bis zum Jahr 2022 verdoppelt, was auf das Interesse des Marktes an dieser Technologie in verschiedenen Branchen, einschließlich der Medizin– und Luftfahrtindustrie, hinweist.
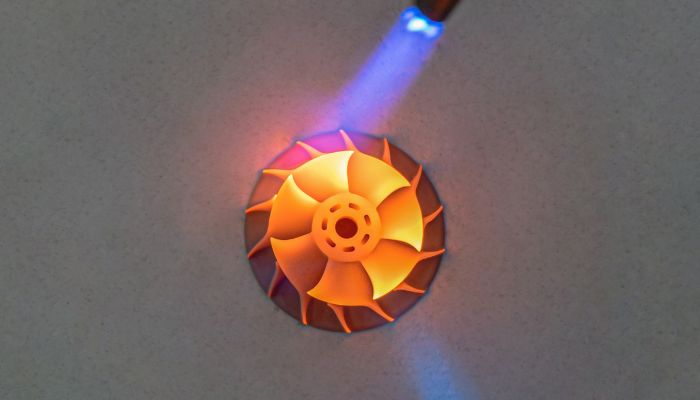
Ein 3D-gedrucktes Keramikteil
Die Vorteile des keramischen 3D-Drucks in Luft- und Raumfahrtanwendungen
Der Forschungsbericht mit dem Titel „3D Printing Ceramics 2022-2032: Technology and Market Outlook“ unterstreicht das signifikante Wachstum des Marktwertes des keramischen 3D-Drucks, der bis 2023 schätzungsweise 400 Millionen US-Dollar erreichen wird. Dem Bericht zufolge sind die Luft- und Raumfahrtindustrie, die Verteidigungsindustrie, die Dentalindustrie und die chemische Industrie am stärksten an der keramischen Fertigung zur Herstellung von Kleinserien interessiert. Keramik ist in der Luft- und Raumfahrtindustrie aufgrund der außergewöhnlichen Eigenschaften, wie hohe Hitze-, Oxidations- und Abriebfestigkeit sowie mechanische und dimensionale Stabilität beliebt. Dies macht Keramik hocheffizient und geeignet für den Einsatz unter extremen Bedingungen, was es zu einem idealen Material für den Bau von Raumfahrzeugen der nächsten Generation macht, insbesondere für Teile, die hohen Belastungen ausgesetzt sind. Wir beziehen uns hauptsächlich auf „fortschrittliche keramische Werkstoffe“ oder „technische Keramik“, welches bemerkenswerte Eigenschaften wie hohe Festigkeit, Korrosionsbeständigkeit und hervorragende thermische und elektrische Isolierung aufweist. Zu den bemerkenswertesten Hochleistungskeramiken gehören Aluminiumoxid (Al2O3), Siliziumnitrid (Si3N4), Siliziumkarbid (SiC) und Zirkoniumdioxid (ZrO2). Mittels 3D-Druck können sogar Ultrahochtemperaturkeramiken (UHTC) verarbeitet werden. Die Materialeigenschaften sind in dieser Branche besonders gefragt.
Keramiken haben sogar einige traditionellere Werkstoffe in der Luft- und Raumfahrtindustrie, wie z. B. Metalle, ersetzt. Auch wenn Metalle immer noch die am häufigsten verwendeten Werkstoffe in der Luft- und Raumfahrtindustrie sind, wird ihre Verwendung für einige Anwendungen in Frage gestellt. Die Notwendigkeit, effizientere Weltraumtriebwerke zu entwickeln, Weltraumabfall zu reduzieren oder präzisere und komplexere Kerne für die Luftfahrtgießerei zu entwickeln, hat zur Suche nach alternativen Materialien geführt. Keramik bietet nun praktische Lösungen für diese Probleme, da es sich weniger schnell abnutzt. Außerdem lassen sich in Kombination mit der additiven Fertigung Teile mit einer höheren Detailtreue herstellen.
Der keramische 3D-Druck hat daher ein enormes Potenzial für die Luft- und Raumfahrtindustrie, wie die verschiedenen Anwendungen der LCM-Technologie von Lithoz zeigen. Ein gutes Beispiel für die außergewöhnlichen Fähigkeiten von Hochleistungskeramik ist die 3D-gedruckte Aerospike-Triebwerksdüse aus Siliziumnitrid des Unternehmens. Diese Düse hat bereits alle Belastungstests erfolgreich bestanden und damit bewiesen, dass sie selbst bei Temperaturen von über 1200 °C erheblichen Temperaturschocks standhalten kann.
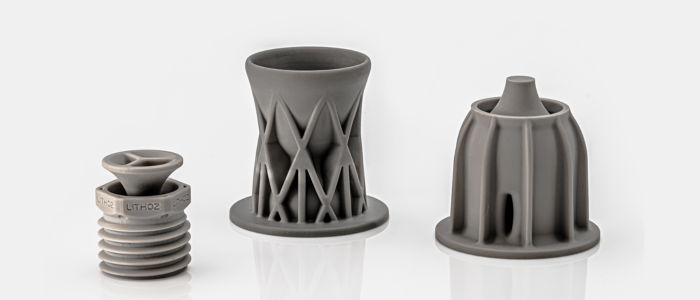
Die 3D-gedruckte Aerospike-Triebwerksdüse
Hohe Auflösung und Detailgenauigkeit durch die LCM-Technologie
In der Keramikindustrie sind Präzision und Genauigkeit von entscheidender Bedeutung, da ein einziger kleiner Fehler zum völligen Misserfolg des Teils und damit der Anwendung führen kann. Aus diesem Grund wurde Lithoz mit Hinblick auf die grundlegenden Werte Ausdauer und Präzision gegründet. Im Laufe der mehr als zehnjährigen Erfahrung ist es dem Unternehmen gelungen, die Technologie so zu verbessern, dass eine Null-Fehler-Toleranz erreicht werden konnte.
Die Lithography-based Ceramic Manufacturing (LCM) Technologie von Lithoz basiert auf der Photopolymerisation. Der CeraFab 3D-Drucker gibt eine mit Keramik beladene Flüssigkeit (Slurry) in eine transparente Wanne. Die Druckplatte bewegt sich von oben nach unten und wird selektiv mit blauem Licht von unten beleuchtet. Mithilfe eines digitalen Mikrospiegels (DMD) und eines hochmodernen Projektionssystems wird ein schichtweises Bild erzeugt, sodass der Grünling Schicht für Schicht entsteht. Das Verfahren erfordert eine thermische Nachbehandlung, um das Bindemittel zu entfernen und die Teile zu sintern, dadurch entstehen hochdichte keramische Komponente, die stabil und haltbar sind.
Der Vorteil dieses Verfahrens besteht darin, dass die gesamte Oberfläche gleichzeitig belichtet wird und das mit keinerlei Abweichungen über die gesamte Bauplattform. Das bedeutet, dass die Teile mit Konsistenz und Genauigkeit auf der ganzen Druckplatte reproduziert werden, unabhängig davon, auf welcher Stelle sie gedruckt werden. Diese Präzision der Belichtung ermöglicht es, äußerst komplexe Mikrostrukturen zu erzielen.
Lithoz hat heute acht verschiedene 3D-Drucklösungen auf dem Markt, allesamt Varianten der CeraFab-Maschine, die jeweils ihre eigenen Spezifikationen haben – die CeraFab S25 beispielsweise wurde speziell für hohe Auflösung von bis zu 25µm entwickelt. Interessanterweise wird die Technologie von Lithoz inzwischen nicht nur für Kleinserien, sondern auch für Großserien eingesetzt. So nutzte die Steinbach AG die CeraFab-Systemlösung von Lithoz für die Massenproduktion von Operationsschläuchen. Das komplexe Design der Rohre erforderte den Einsatz der additiven Fertigung vom Prototyping bis zur Endfertigung. Steinbach war in der Lage, 12.000 Teile pro Jahr zu produzieren, was die Effektivität der additiven Fertigung bei der Skalierung der Produktion bis hin zur Serienfertigung demonstriert.
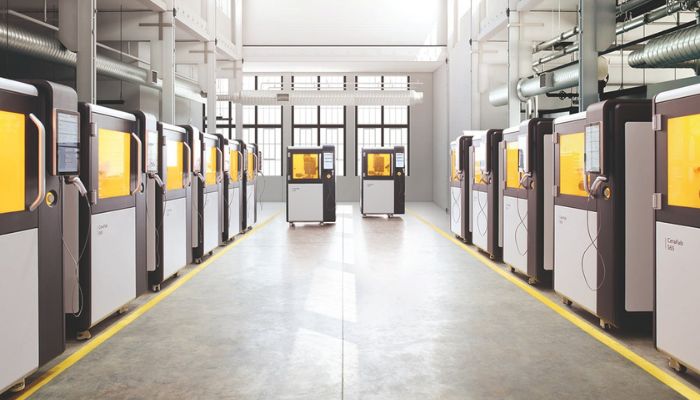
Die CeraFab 3D-Druckreihe von Lithoz
Optimierte Strukturen für die Luft- und Raumfahrt dank keramischem 3D-Druck
Wie bereits erwähnt, ist die Möglichkeit, die Eigenschaften von Keramik mit der Flexibilität des 3D-Drucks zu kombinieren, einer der Hauptvorteile des Einsatzes dieser Technologie in der Luft- und Raumfahrt. Die Möglichkeit, das Design eines Bauteils genau anzupassen, seine Struktur zu verändern und sogar spezifische Funktionen hinzuzufügen, ist etwas, das die Akteure der Branche bei der Herstellung komplexer Teile suchen.
Ein praktisches Beispiel dafür ist die Herstellung von HF-Filtern für Luft- und Raumfahrtanwendungen. HF-Filter sind wichtige elektronische Schaltungen, die die Signalqualität verbessern und Störungen in Kommunikationssystemen wie Satellitenkommunikation, Radar und Avionik minimieren. Der keramische 3D-Druck ermöglicht die Herstellung hochentwickelter Resonatoren mit einer breiten Palette von Formen, Ordnungen und Bandbreiten, die in ein einziges Bauteil integriert werden können, um die Leistung, Zuverlässigkeit und Haltbarkeit zu optimieren.
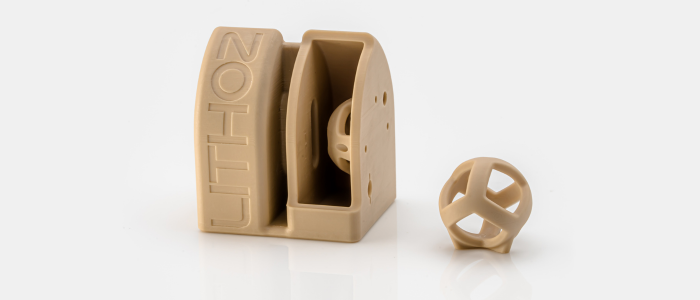
Links ein HF-Filter und rechts der 3D-gedruckte Keramikresonator. Der Resonator kann in verschiedenen Größen gedruckt werden
Doch warum sollte man diese Teile mit Keramik 3D-drucken? In der Luft- und Raumfahrtindustrie spielen HF-Filter eine entscheidende Rolle bei der Gewährleistung einer zuverlässigen und genauen Kommunikation in Hochfrequenzbändern. Aufgrund der rauen Umgebungsbedingungen, denen sie standhalten sollen, müssen diese Filter sehr leistungsfähig sein und strikte Ansprüche an Zuverlässigkeit und Leistung erfüllen. Dank ihrer vorteilhaften Materialeigenschaften eignen sich Keramiken perfekt zur Erfüllung dieser Anforderungen und ermöglichen gleichzeitig die Miniaturisierung dieser Filter zur Gewichtsreduzierung – ein entscheidender Faktor in der Luft- und Raumfahrt. Darüber hinaus weisen Keramikfilter eine gute Temperatur- und Zeitstabilität auf, was langfristig eine zuverlässige und gleichbleibende Leistung gewährleistet.
Kontrolle der Mikrostruktur von keramischen Komponenten
Die keramischen 3D-Drucklösungen von Lithoz bieten einen bemerkenswerten Vorteil für komplexere Anwendungen, da sie eine präzisere Kontrolle der Mikrostruktur und Porosität des Materials ermöglichen, was bei allen anderen derzeit verfügbaren AM- oder konventionellen Fertigungstechniken eine Einschränkung darstellt. Mit der LCM-Technologie von Lithoz lassen sich dank des Zwei-Kammer-Systems auch 3D-Materialien und funktional abgestufte Keramiken drucken. Dieses System ermöglicht im neu entwickelten Multi-Material-LCM-Druckeraufbau nicht nur die Zuordnung eines Materials zu einer beliebigen Schicht, sondern auch die Verwendung unterschiedlicher Materialien in jeder Schicht durch Zuordnung der jeweiligen Materialien zu ausgewählten Pixeln des Schichtbildes. So haben Lithoz und das Fraunhofer IGD beispielsweise Teile aus Aluminiumoxid mit hoher Komplexität und einem definierten Gradienten von dicht und porös in einem einzigen Teil hergestellt. Diese Fähigkeit ist unter anderem für den 3D-Druck von komplexen Katalysatoren für die Luft- und Raumfahrt von großer Bedeutung.
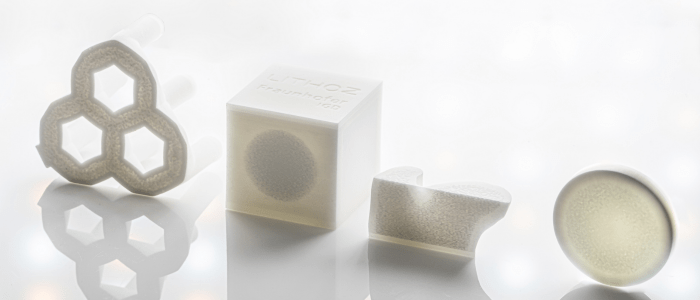
Demonstrationsteile mit dichter bis poröser Abstufung für Anwendungen in verschiedenen Bereichen, wie Katalysatoren, Filter oder Knochenstrukturen
All diese Beispiele zeigen, dass es möglich ist, durch den Einsatz der additiven Fertigung die Eigenschaften keramischer Bauteile zu verbessern, ihre Komplexität zu erhöhen und damit auch ihre Effizienz zu steigern. Dieser Ansatz eröffnet auch neue Forschungsmöglichkeiten in der Luft- und Raumfahrtindustrie. Die Lithoz LCM-Technologie ermöglicht im Vergleich zu anderen Verfahren auf dem Markt die Fertigung von komplexeren und besser aufgelösten Teilen und ist damit die perfekte Lösung für die ständig steigenden Anforderungen an die Geometrien von Luft- und Raumfahrtkomponenten. Mehr über Lithoz finden Sie HIER.
Was halten Sie von der Lösung für den keramischen 3D-Druck von Lithoz? Lassen Sie uns gerne einen Kommentar da, oder teilen Sie es uns auf Facebook oder LinkedIN mit. Möchten Sie außerdem eine Zusammenfassung der wichtigsten Neuigkeiten im 3D-Druck und der additiven Fertigung direkt und bequem in Ihr Postfach erhalten? Dann registrieren Sie sich jetzt für unseren wöchentlichen Newsletter.
*Alle Bildnachweise: Lithoz