LEDs statt Laser: Neues “SLEDM”-Verfahren verspricht 20-mal mehr Speed in 3D-Metalldruck
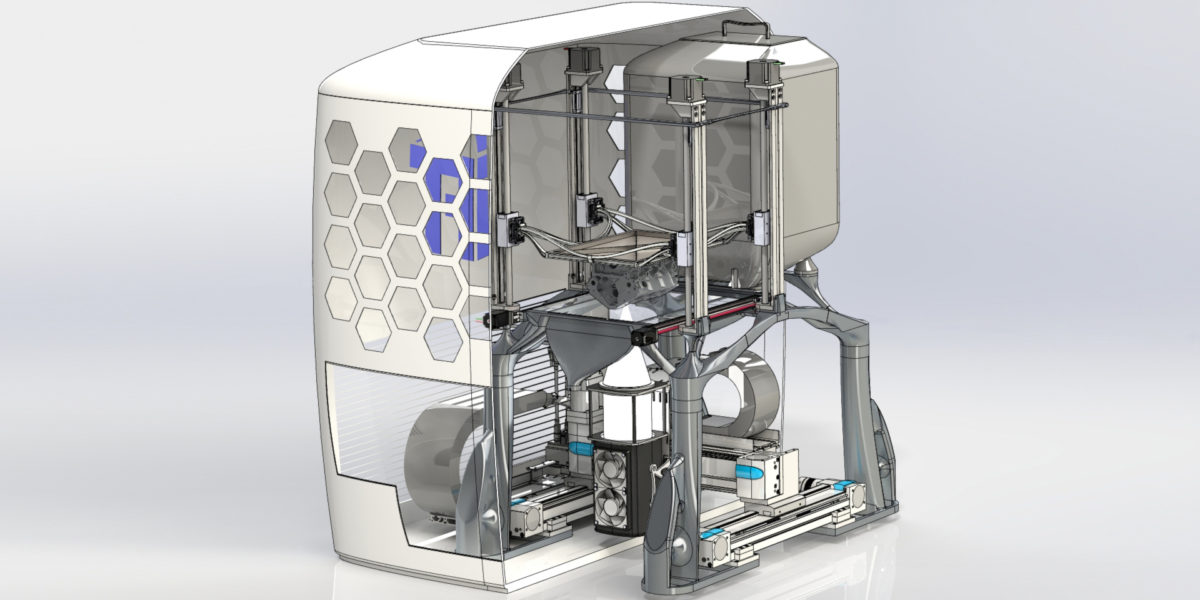
Aufgrund der Corona-Krise befinden sich an der TU Graz seit Mitte März sowohl die Mitarbeiter als auch die Studierenden im Home-Office. Das hat die Forschungsabteilung der österreichischen Universität allerdings nicht daran gehindert, ein neu entwickeltes Pulverbettverfahren für die additive Fertigung von Metallteilen vorzustellen.
Bisher werden in der Praxis die weit verbreiteten Laser- oder Elektronenstrahl-Quellen für die Energieübertragung ins Pulverbett und somit für das Aufschmelzen des Materials verwendet, so wie bei den Verfahren des selektiven Laserschmelzens oder des Elektronenstrahlschmelzens. Mit dem System der TU Graz ändert sich das: Ihre Maschine nutzt eine Hochleistungs-LED-Quelle für das Verschweißen der einzelnen Schichten. Der Name des neuen Verfahrens leitet sich direkt von der Innovation ab: Selective LED based Melting (SLEDM). Es wurde in den letzten Monaten vom Institut für Fertigungstechnik unter Leitung von Franz Haas entwickelt und zum Patent angemeldet.
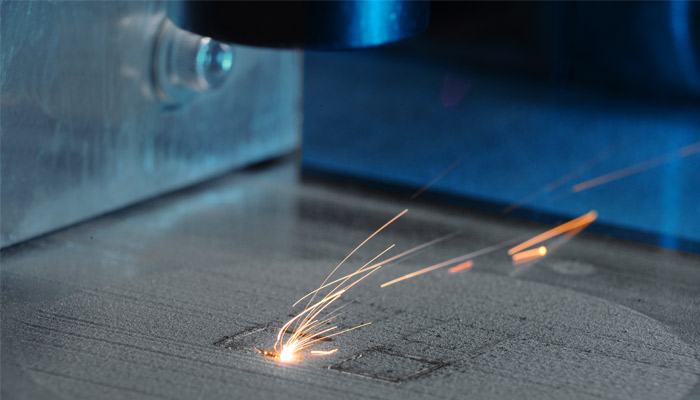
Durch einen variablen Durchmesser des Lichstrahls können großflächige Bereiche schneller gefertigt werden (Bildnachweis: Fraunhofer ILT)
Inwiefern unterscheidet sich dieses Verfahren nun von den konventionellen Metallschmelzprozessen und welche Vorteile bringt es mit sich? Laut dem Institut der TU Graz soll vor allem die verkürzte Bauzeit eine große Rolle spielen. Durch Hochleistungs-LEDs gekoppelt mit einem komplexen Linsensystem kann der Fokusdurchmesser des LED-Strahls variabel angepasst werden, aktuell zwischen 0,05 und 20 [mm]. Somit können großvolumige Bereiche bzw. Bauteile bis zu 20-mal schneller gefertigt werden, da weniger Zeit zum Scannen der Querschnittsflächen benötigt wird. Gleichzeitig muss nicht auf filigrane Strukturen verzichtet werden. Zum Vergleich: laserbasierte Anlagen bieten derzeit einen variablen Fokusdurchmesser zwischen 0,07 und 0,5 [mm].
Ein weiterer Unterschied ist die Druckrichtung. Beim System der TU Graz wird das Bauteil von oben nach unten gedruckt, es liegt sozusagen frei und ist nicht im Pulver eingebettet. Das soll vor allem die benötigte Pulvermenge reduzieren und mühseliges Post-Processing eliminieren.
„Das aufwendige, in der Regel manuelle Nachbearbeiten, wie es bei derzeitigen Verfahren notwendig ist, um etwa raue Oberflächen zu glätten und Stützkonstruktionen zu entfernen, entfällt und spart weitere kostbare Zeit“, so Institutsleiter Franz Haas.
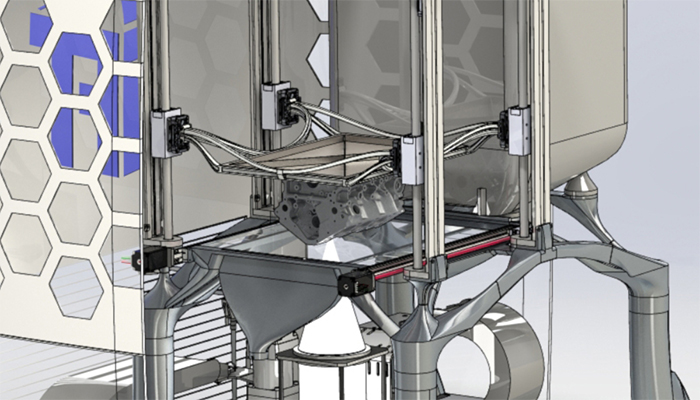
Im SLEDM-Verfahren wird das Bauteil von oben nach unten gedruckt
Auch im Hinblick auf die Gerätekosten soll die Maschine der TU günstiger sein. Genauere Infos hierzu wurden jedoch noch nicht veröffentlicht. Aktuell ist das SLEDM Verfahren auf zwei Schwerpunkte gerichtet: Die Branchen Mobilität sowie Implantatmedizin. Für die Anwendung in der Medizin stellt sich das Forschungsteam vor, bioresorbierbare Metal-Implantate zu produzieren. Das sind unter anderem Schrauben aus Magnesium-Legierungen, welche an den Patienten angepasst sind und sich nach dem Zusammenwachsen der Bruchstelle auflösen. Diese können dann direkt im OP-Saal gefertigt und dem Patienten implantiert werden.
Für nachhaltige Lösungen in der Mobilität der Zukunft stellt man sich die Produktion von Komponenten für Batteriesysteme mit dem SLEDM-System vor. „Wir wollen die additive Fertigung mittels SLEDM für die E-Mobilität wirtschaftlich nutzbar machen und SLEDM in diesem Forschungsfeld frühzeitig positionieren“, so Haas. Der nächste Schritt in dieser Technologie soll dann einen marktfähigen Prototypen “made by TU Graz” hervorbringen. Weitere Infos finden Sie HIER.
Was denken Sie von der SLEDM-Technologie und deren Potenzial? Teilen Sie uns Ihre Meinung in den Kommentaren mit! Möchten Sie eine Zusammenfassung der wichtigsten Neuigkeiten im 3D-Druck und der Additiven Fertigung direkt und bequem in Ihr Postfach? Registrieren Sie sich jetzt für unseren wöchentlichen Newsletter und folgen Sie uns auf Facebook und Twitter um stets auf dem Laufenden zu bleiben! Außerdem sind wir auch auf LinkedIN und auf Youtube zu finden.