Kumovis ermöglicht dezentrale Fertigung medizinischer Kunststoffprodukte
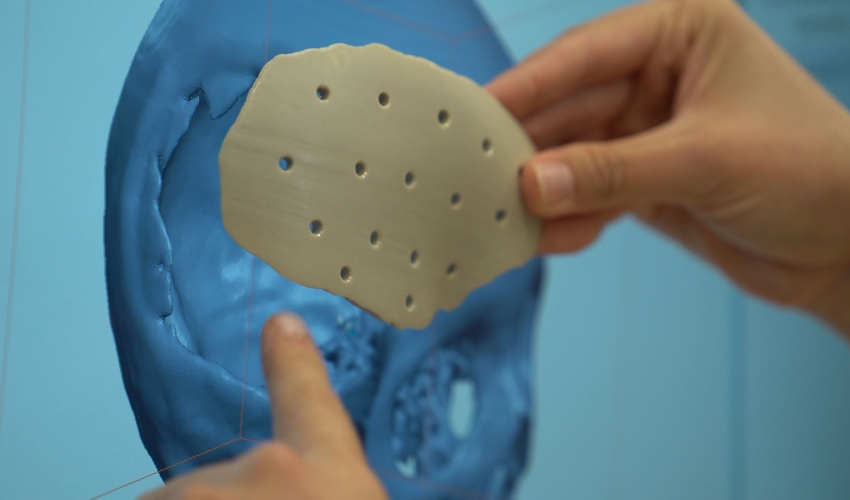
Wer unsere Nachrichten schon seit längerer Zeit verfolgt, wird bestimmt mit dem Start-up Kumovis vertraut sein. Denn 2018, ein Jahr nach seiner Gründung, zählte Kumovis bereits zu den Gewinnern der Formnext Startup Challenge. Ein Jahr später konnte das junge Unternehmen dann seinen ersten eigenen 3D-Drucker, den Kumovis R1, vorstellen, der speziell für industrielle und medizinische Anwendungen entwickelt wurde. Doch, was genau zeichnet das Münchner Unternehmen aus? Welche Mission möchte es erfüllen? Und welche Herausforderungen mussten überwunden werden? Wir haben mit Miriam Haerst, Co-CEO von Kumovis, gesprochen, um diesen Fragen auf den Grund zu gehen.
Können Sie sich selbst und Ihre Verbindung zum 3D-Druck kurz vorstellen?
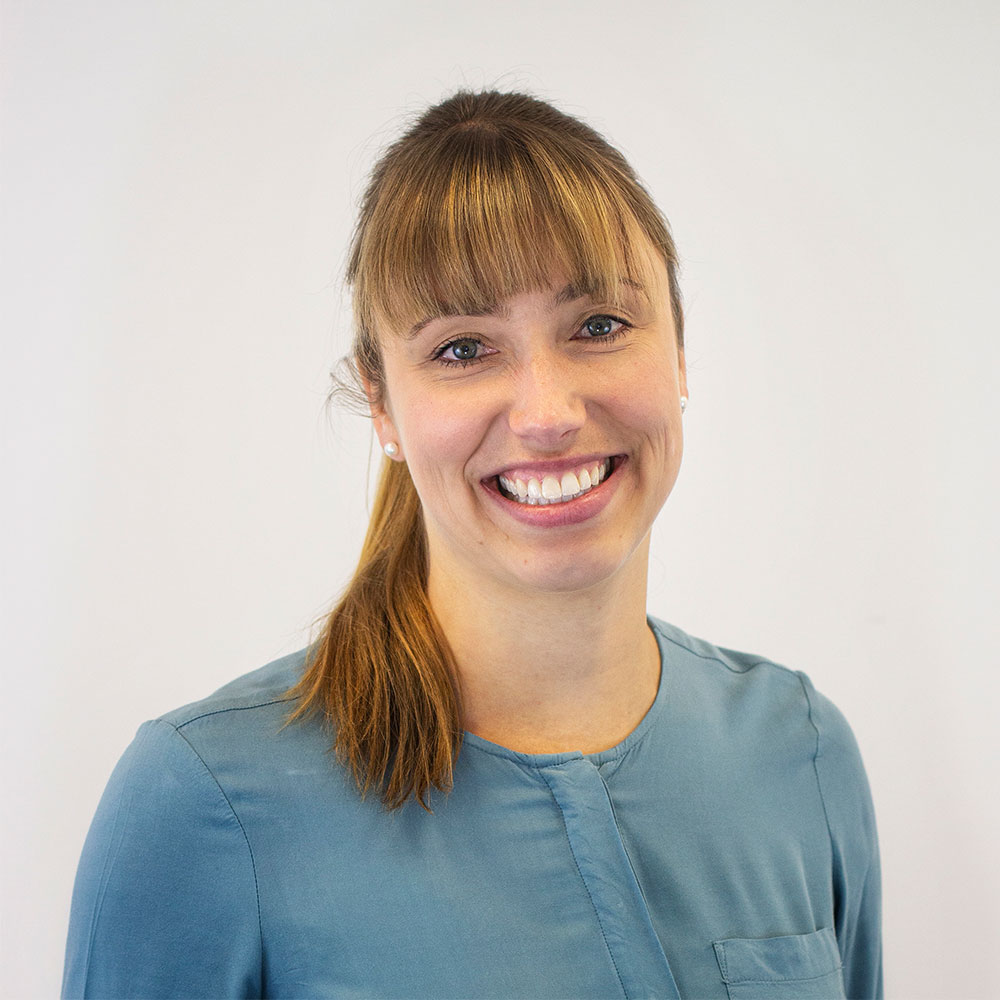
Dr. Miriam Haerst, Co-CEO und Mitgründerin, Kumovis GmbH (Bildnachweis: Kumovis)
Ich heiße Miriam Haerst und bin Co-CEO der Kumovis GmbH. Bei einem Praktikum während des Studiums bin ich zum ersten Mal mit 3D-Druck in Berührung gekommen. Das war im Bereich der Entwicklung patientenspezifischer Hörgeräte. Nach meiner Promotion in der Kunststoffverarbeitung für die Medizintechnik reifte dann die Idee, Kumovis mitzugründen.
3D-Druck ist für das Gesundheitswesen eine Schlüsseltechnologie, die ermöglicht, Patientinnen und Patienten bestmöglich und individuell zu versorgen. Um diesem Anspruch gerecht zu werden, hat sich Kumovis auf die Entwicklung branchenspezifischer 3D-Drucklösungen für die Medizin spezialisiert. Seitdem der firmeneigene 3D-Drucker namens Kumovis R1 auf dem Markt ist, unterstützt Kumovis Medizintechnik-Unternehmen und Krankenhäuser, Medizinprodukte künftig so zu fertigen, dass diese ihnen selbst sowie Patientinnen und Patienten bedeutende Mehrwerte bringen.
Kumovis wurde 2017 als Start-up gegründet. Wie ist die Idee dazu entstanden?
Wir Gründungsmitglieder von Kumovis haben uns an der Technischen Universität München kennengelernt. Zur Gründungszeit gab es keinen 3D-Drucker, der zum Beispiel ermöglichte, ein Schädelimplantat aus Hochleistungskunststoffen additiv so zu fertigen, dass es branchenüblichen Belastungstests standhält. Daher nahm ich zusammen mit vier Kollegen die Entwicklung einer solchen Maschine selbst in die Hand. Mit derartigen Herausforderungen als Entwicklungstreiber gelang es Kumovis, zwei Jahre nach Firmengründung den weltweit ersten 3D-Drucker mit integriertem Reinraum in den Medizintechnik-Markt einzuführen. Der Grundstein für die dezentrale Herstellung medizinischer Produkte war gelegt – in Form des Kumovis R1.
Sie konzentrieren sich auf den 3D-Druck im medizinischen Bereich. Was gilt es hierbei besonders zu beachten?
Die Medizinprodukte, die die Nutzerinnen und Nutzer des Kumovis R1 derzeit in Kooperation mit uns entwickeln, kommen meist in engen Kontakt mit dem menschlichen Körper. Von patientenindividuellen Schädelimplantaten, über Wirbelsäulenimplantate bis hin zu Bohr- und Sägeschablonen für komplizierte chirurgische Eingriffe reichen derzeit die Applikationen. Vor allem mit Blick auf den 3D-Druck im Krankenhaus spielen Aspekte wie Biokompatibilität, Dokumentation – von der Wahl des Werkstoffs bis zum Prozess – und Qualitätsmanagement eine übergeordnete Rolle.
Außerdem sind Unsicherheiten im regulatorischen Bereich ein Thema, wenn es um innovative Medizinprodukte und deren Fertigung geht. Die EU-Medizinprodukteverordnung (MDR), die seit dem 26. Mai 2021 gilt, hat schon in den vergangenen Jahren mit Blick auf das Inverkehrbringen medizinischer Produkte für Trubel in der Branche gesorgt. Die FDA in den USA hingegen hat bereits für etwas mehr Klarheit bezüglich additiv gefertigter Medizinprodukte gesorgt. Um hier möglichst ressourceneffizient Innovationen voranzutreiben, ist mehr als ein branchenspezifischer 3D-Drucker notwendig. Deshalb unterstützen wir unsere Kundinnen und Kunden auch darüber hinaus, mit einem ganzheitlichen Ansatz: Dieser verläuft bei Bedarf von Designoptimierungen über Werkstoffauswahl und Prozessqualifizierung bis hin zu regulatorischen Aspekten.
Im Jahr 2019 konnten Sie Ihren ersten 3D-Drucker, den R1, auf den Markt bringen. Welche Produktmerkmale zeichnen diesen aus?
Kumovis R1 ist ein offenes Filament-System, das auf dem Fused-Layer-Manufacturing-Verfahren basiert. Damit lassen sich mehr als acht Hochleistungskunststoffe unterschiedlicher Hersteller für medizinische Anwendungen verarbeiten. Kumovis ermöglicht so den 3D-Druck medizinischer Produkte mit Werkstoffen wie PEEK, PEKK oder PPSU, ohne auf die bekannten mechanischen Eigenschaften aus konventioneller Fertigung – zum Beispiel dem Spritzgießen – verzichten zu müssen.
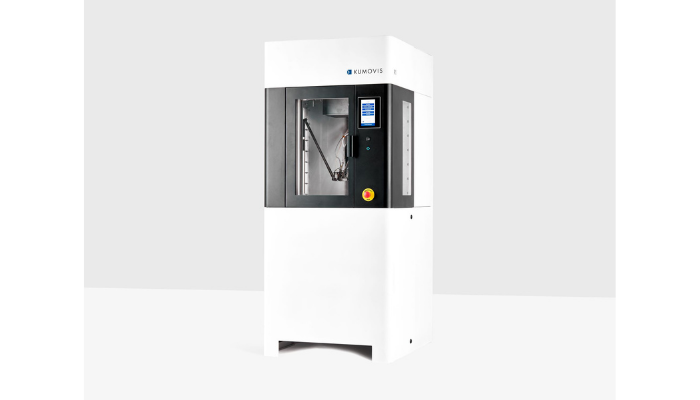
Medizinischer 3D-Drucker Kumovis R1 (Bildnachweis: Kumovis)
Der 3D-Drucker ist mit einem Luftstrom ausgestattet, der ermöglicht, den Bauraum homogen auf bis zu 250 Grad Celsius zu erhitzen. Nur so lassen sich die eben schon erwähnten mechanischen Eigenschaften des späteren Medizinprodukts im 3D-Druck erreichen. Zusätzlich kann mit einem lokalen Temperaturmanagement die Verschmelzung der Schichten individuell beeinflusst werden. Dies ist unter anderem nötig, um Stützstrukturen vom Bauteil leichter entfernen zu können, was wiederum Nachbearbeitungszeit spart.
Kumovis R1 ist der einzige FLM-3D-Drucker mit integriertem Reinraum und speziell für die Medizintechnik entwickelt. Konkret heißt das, dass das eingebaute Filtersystem im Bauraum des Kumovis R1 eine Reinraumumgebung schafft. Kontamination während des 3D-Drucks lässt sich damit vermeiden – ideale Bedingungen für eine Anwendung am Point of Care. Darüber hinaus ist der 3D-Drucker nicht zuletzt aufgrund seiner Bauweise für die Produktion in bestehenden Reinräumen geeignet.
Warum haben Sie sich entschieden, bei der additiven Fertigung auf Hochleistungspolymere wie PEEK, PPSU oder PLLA zurückzugreifen? Welche Vor- und Nachteile bringen diese Werkstoffe?
Die Studienrichtungen des Gründungsteams, unter anderen Kunststoff- und Medizintechnik, spielten zunächst eine Rolle. Dass Hochleistungspolymere wie PEEK in der Medizin seit langem etabliert sind, war ein weiterer Grund für die Entscheidung. Doch was den Ausschlag gab, waren mitunter die Vorteile dieser Werkstoffe gegenüber Metallen.
Dies sind beispielsweise die mechanischen Eigenschaften diverser Polymere. Sie sind dem menschlichen Knochen ähnlicher. Mit Blick auf ihre Radioluzenz bieten Kunststoffe Vorteile in der Bildgebung. Und nicht zuletzt ist das Allergierisiko geringer, was Zweitoperationen vorbeugt. Neben diesen Eigenschaften spielt natürlich die Wirtschaftlichkeit eine Rolle: Durch den Einsatz unserer Technologie und des Werkstoffs PPSU lässt sich der Return on Invest um bis zu 20 Prozent erhöhen.
Wenn es um die osseointegrativen Eigenschaften eines Implantats geht, also dessen Potential, Knochen einwachsen zu lassen und so Stabilität und Nährstofftransport zu verbessern, ist Titan derzeit noch der Werkstoff der Wahl. Doch auch dahingehend arbeitet Kumovis an Lösungen. Die ersten Entwicklungen mit Blick auf die Oberflächenfunktionalisierung medizinischer Kunststoffprodukte sind vielversprechend.
Was möchten Sie unseren Lesern außerdem mitteilen?
Die additive Fertigung ist längst über die Produktion anatomischer Modelle und chirurgischer Instrumente hinausgewachsen. Ob in der Industrie oder dem Krankenhaus, personalisierte und funktionalisierte Implantate aus PEEK und anderen Kunststoffen kommen in Zukunft aus dem 3D-Drucker. Dezentral und ressourcenschonend.
*Titelbildnachweis: Bayern Innovativ | Kumovis
Mehr Informationen zu Kumovis erhalten Sie auf der offiziellen Webseite. Lassen Sie uns zu diesem Thema gerne einen Kommentar da, oder teilen Sie uns Ihre Meinung auf Facebook, Twitter, LinkedIN oder Xing mit. Möchten Sie außerdem eine Zusammenfassung der wichtigsten Neuigkeiten im 3D-Druck und der Additiven Fertigung direkt und bequem in Ihr Postfach erhalten? Dann registrieren Sie sich jetzt für unseren wöchentlichen Newsletter.
Vielen Dank für den Artikel! Ich finde es interessant, dass ein 3D-Drucker auch in der Lage ist, einen Reinraum zu schaffen. Meine Tochter arbeitet in einem solchen Labor und es scheint sehr anstrengend zu sein, in einem Reinraum zu arbeiten und die notwendige Qualifizierung aufrechtzuerhalten. Aber die Technik heutzutage ist ja sowieso unglaublich fortgeschritten, da sollte mich nichts mehr wundern.