Carbon: Entwicklung innovativer Materialien und die Bedeutung der Nachhaltigkeit bei AM
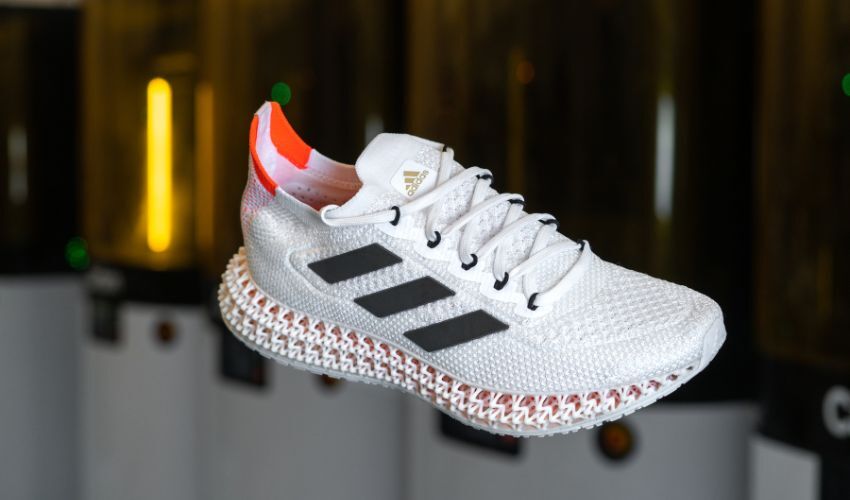
Als Carbon im Jahr 2013 gegründet wurde, setzte man alles daran, die Produktentwicklung und -herstellung mit seinem ultraschnellen Photopolymerisationsdruckverfahren Digital Light SynthesisTM (DLS) radikal zu verändern. Seitdem hat das Unternehmen immer wieder für Furore gesorgt: Unternehmen wie adidas, Ford Motor Company, Becton Dickinson Company und andere nutzen die Carbon DLS™-Plattform, um bessere Produkte in kürzerer Zeit zu liefern. Das Unternehmen hat nicht vor, dabei stehen zu bleiben. Neben der kontinuierlichen Verbesserung seiner Technologie konzentriert sich das Unternehmen auf die Entwicklung innovativer Materialien und darauf, die Branche insgesamt nachhaltiger zu machen. Wir haben uns mit Jason Rolland, Senior Vice President of Materials bei Carbon, zusammengesetzt, um mehr über die Funktionsweise der Technologie, die Materialien und natürlich über die Bemühungen des Unternehmens um eine umweltfreundlichere Welt zu erfahren.
3DN: Können Sie sich bitte einmal vorstellen?
Mein Name ist Jason Rolland, ich leite das Materialteam bei Carbon und bin seit über acht Jahren im Unternehmen. Ich bin schon sehr früh eingestiegen, ich war Mitarbeiter Nummer 8, und jetzt haben wir über 500 Mitarbeiter. Es macht also Spaß, das Unternehmen wachsen zu sehen und all die großartigen Dinge zu beobachten, die seither entstanden sind. Mein Hintergrund ist die Polymerchemie, ich habe an der Virginia Tech studiert und an der University of North Carolina Chapel Hill promoviert. Dort habe ich Joseph DeSimone kennengelernt, der mein Doktorvater war und mich später zu Carbon gebracht hat. Joe ist einer der Mitbegründer von Carbon. Er hat mich schon früh mit der Technologie vertraut gemacht und mich rekrutiert, um das Materialteam und die Plattform aufzubauen. Davor war ich ganz neu im 3D-Druck und es war sehr aufregend, die neue Technologie und das Potenzial zu sehen, das sich daraus ergeben könnte.

Jason Rolland, SVP of Materials bei Carbon
3DN: Können Sie uns mehr über Carbon und Ihre DLS-Technologie erzählen?
Seit den Anfängen von Carbon haben wir uns darauf konzentriert, den 3D-Druck im großen Maßstab in die Produktion zu bringen. Dazu mussten wir zwei wichtige Probleme beseitigen: Druckgeschwindigkeit und Materialleistung. 3D-Drucker können unabhängig von der verwendeten Technologie recht langsam sein, was sich auf die Kosten pro Teil auswirkt, da man nicht in großen Mengen produzieren kann. Um dieses Problem zu lösen, haben wir die Digital Light SynthesisTM (DLS)-Technologie entwickelt. Damit konnten wir die Adhäsionskräfte des Bauteils an der Unterseite der Kassette erheblich reduzieren und folglich die Druckgeschwindigkeit stark erhöhen.
Um Ihnen eine bessere Vorstellung zu vermitteln: Wenn Sie sich eine unserer Maschinen ansehen, haben wir eine Bauplattform, die ähnlich aufgebaut ist wie eine Bottom-up-DLP-Maschine (Digital Light Processing). Wir haben eine Kassette, in der das Harz aufbewahrt wird, und am unteren Ende befindet sich ein spezielles Fenster, unter dem sich das digitale Projektionssystem befindet. Die wichtigste Innovation war, dass wir die Bedeutung von Sauerstoff erkannt haben. Die Durchlässigkeit von Sauerstoff durch den Boden der Kassette kann zu einer dünnen Schicht ungehärteten Harzes führen, die während des gesamten Druckvorgangs konstant vorhanden ist, was die Adhäsionskräfte erheblich verringert und die Druckgeschwindigkeit erhöht.
Durch die Verwendung dieses sauerstoffdurchlässigen Materials an der Basis der Kassette können Sie sicherstellen, dass die Polymerisation genau an dieser Schnittstelle stattfindet und direkt darüber aushärtet. Auf diese Weise entsteht eine dünne Flüssigkeitsschicht, die die Adhäsionskräfte verringert und den Druck erheblich beschleunigt. Bei bestimmten Geometrien können wir jetzt 10-mal schneller drucken als herkömmliche 3D-Drucker. Von da an haben wir angefangen, uns Gedanken über die Materialentwicklung zu machen.
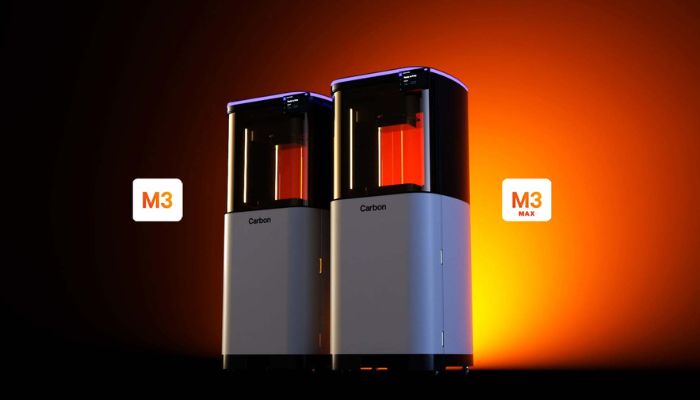
Die jüngste Einführung von Carbon waren die Drucker der M-Serie, der M3 und der M3 Max.
3DN: Was können Sie uns darüber hinaus über die Materialentwicklung bei Carbon erzählen?
Wir haben erkannt, dass wir Materialien benötigen, die mit den Materialien für Spritzgussverfahren oder Schaumstoffe vergleichbar sind, damit unsere Kunden Anwendungen in die Produktion bringen können. Das war ein wirklich schwieriges Problem, weil wir einen Drucker haben, der auf UV-härtender Chemie und der Musterung von UV-Licht basiert, und es gibt nur bestimmte Chemikalien, die mit der UV-härtbaren Chemie kompatibel sind. Man braucht bestimmte Funktionalitäten an den Enden der Polymerketten. Wir sahen dies als eine ziemliche Einschränkung in Bezug auf die Eigenschaften und Formulierungen, die wir herstellen konnten. Um dieses Problem zu lösen, haben wir dualhärtende Materialsysteme entwickelt, die wir anschließend patentiert haben. Das bedeutet, dass wir nicht nur eine UV-härtbare Chemie verwenden, sondern eine Kombination aus UV-härtbarer Chemie und thermisch härtbarer Chemie.
Was möchte ich damit sagen? Bei thermisch härtbaren Chemikalien gibt es zwei reaktive Komponenten (Teil A und Teil B), z. B. bei Epoxidharz oder Silikonharz. Und es gibt eine ganze Reihe von thermisch härtenden Chemikalien, darunter Polyurethane, Epoxidharze, Hochtemperatur-Duroplaste, all diese Dinge, die nicht UV-reaktiv sind. Wir haben damit begonnen, die zweiteilige thermisch härtende Chemie mit der UV-härtenden Chemie zu kombinieren und Harze mit einem Teil A und einem Teil B herzustellen, die kurz vor dem Eintritt in den Drucker gemischt werden. Der Drucker aktiviert die UV-Strahlung, so dass Sie die Form des zu fertigenden Teils bestimmen können, und schließt dann die thermische Chemie in einem nicht reagierten Zustand in das Teil ein. Am Ende haben Sie ein Teil im grünen Zustand, das dann gewaschen oder geschleudert wird, um Harzreste zu entfernen, bevor es zum Einbrennvorgang kommt. In diesem Einbrennschritt aktivieren wir eine separate thermische Chemie, die nun im UV-Netzwerk gefangen ist. Jetzt haben beide Komponenten reagiert und Sie haben Ihr fertiges Teil. Das hat die Palette der verfügbaren Materialien wirklich erweitert und ermöglicht eine kostengünstigere additive Fertigung in einer Fabrikumgebung mit Hochleistungsmaterialien. Um es klar zu sagen: Das ist etwas ganz anderes als die UV-Fluthärtung, die ein üblicher Endbearbeitungsschritt für UV-härtbare Einkomponenten-Chemie ist. Hier wird lediglich die ursprüngliche UV-Reaktion weiter polymerisiert.
3DN: Welche Bedeutung hat das Thema Nachhaltigkeit für Carbon? Wie arbeiten Sie daran, diesen Punkt abzudecken?
Nachhaltigkeit ist für uns bei Carbon ein wirklich wichtiges Thema, und wir haben mehrere Schlüsselbereiche identifiziert, in denen wir Fortschritte machen können. Der erste betrifft das allgemeine Problem der Erzeugung gefährlicher Abfälle. Dies ist besonders wichtig im Bereich der Flüssigharzdrucktechnologie.
Der Standardansatz ist, dass man das Teil druckt, das mit Harz betropft ist, man hat eine Art Tank mit einem Lösungsmittel wie Isopropylalkohol, man taucht es hinein, wäscht es ab und hat dann ein sauberes Teil. Allerdings hat man dann ein Lösungsmittel mit darin gelöstem Harz, und das muss alles als gefährlicher Abfall behandelt werden. Das mag bei kleinen Mengen in Ordnung sein, wenn man nur Prototypen herstellt, aber wenn man in die Produktion einsteigt, hat man ein großes Problem vor sich. Und das ist nicht nur ein Problem der Nachhaltigkeit, sondern auch ein wirtschaftliches, denn man verschwendet Harz und erzeugt Sondermüll, und das alles kostet natürlich Geld.
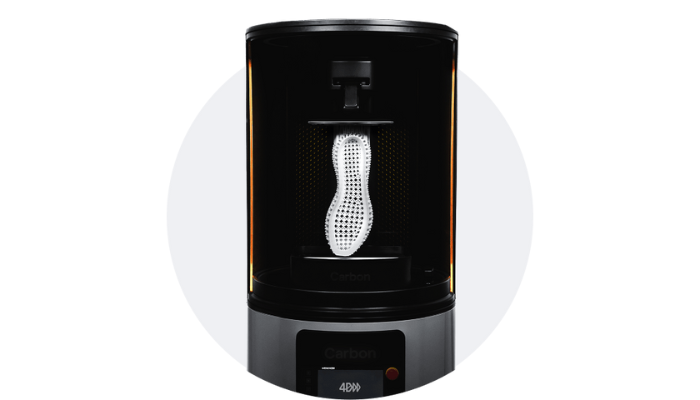
Carbon’s Spinning Post-Processing hat dazu beigetragen, giftige Abfälle bei der Herstellung von Zwischensohlen für adidas zu reduzieren
Stattdessen haben wir eine Schleuderreinigungstechnologie entwickelt, die völlig lösungsmittelfrei ist. Das Ergebnis beinhaltet sehr saubere Teile mit einer sehr dünnen Schicht von Harz, die bei der Nachhärtung beseitigt werden. Diese Art der Schleudertechnik wird in der Großserienproduktion eingesetzt, z. B. bei Tiefziehmodellen für Zahnersatz, adidas-Zwischensohlen und anderen Gittergeometrien. Für unsere großvolumigen Anwendungen gehen wir davon aus, dass mit dieser Spinnreinigungstechnologie bis 2022 insgesamt Tausende von Tonnen gefährlicher Abfälle vermieden werden können. Wenn Wirtschafts- und Nachhaltigkeitsinitiativen aufeinander abgestimmt sind, ist es ein Leichtes, Fortschritte zu erzielen. Denn es ist eine einzige Lösung, die beide Probleme angeht.
Darüber hinaus verwenden wir für einige unserer Harze Rohstoffe aus biologischen oder pflanzlichen Quellen. Es gibt im Wesentlichen zwei Hauptquellen für alle Rohstoffe, aus denen alle Chemikalien der Welt hergestellt werden. Die eine ist Erdöl. Alle Kunststoffe, an die man generell denkt, sind Nebenprodukte der Erdölraffination, die dann in die Bausteine für Polymere umgewandelt werden. Aber man kann auch die Natur als Fabrik nutzen, um die gleichen Bausteine herzustellen. Und es gibt einen großen Trend in der chemischen Industrie, mehr nachhaltige und erneuerbare Ressourcen in Form von Pflanzen zu finden, um Bausteine für Polymersysteme herzustellen. Einer unserer Schwerpunktbereiche sind Polyurethane, und unsere Partner haben Polymere entwickelt, die Teil der gesamten Polyurethankette sind und aus Mais gewonnen werden.
In diesem Sinne haben wir ein neues Harz namens EPU44 entwickelt. Das Material besteht zu 40 Gewichtsprozent aus pflanzlichen Rohstoffen (was zu einer geringeren CO2-Bilanz führt). Es ist hochleistungsfähig und hat eine niedrigere Viskosität, was für den Druck besser ist. Tatsächlich wird es von adidas bereits in großen Mengen für Zwischensohlen verwendet. Wir haben auch ein steifes Material namens RPU130, das zu 25 Gewichtsprozent aus pflanzlichem Material besteht und ein sehr leistungsfähiges Material mit hoher thermischer Stabilität und Schlagfestigkeit ist. Diese Produkte zeigen, dass es möglich ist, nachhaltige Materialien zu verwenden, ohne Abstriche bei der Leistung zu machen. In diesen Fällen konnten wir sogar einen Leistungsvorteil bei der Verwendung nachhaltigerer Rohstoffe feststellen.
Außerdem haben wir, wie viele Unternehmen der additiven Fertigung, Leichtbau und Materialreduzierung als einen entscheidenden Punkt für die Nachhaltigkeit erkannt. Um dies zu erreichen, haben wir ein neues, eigenständiges Softwareprodukt namens Design Engine entwickelt. Damit können Sie ein solides CAD-Modell eingeben, die Einstellungen für die gewünschten Eigenschaften anpassen und ein Gittermodell generieren, das diesen Anforderungen entspricht und weniger Material und leichtere Teile ermöglicht. Dies ist in Bereichen wie dem Transportwesen von großer Bedeutung. Im Automobilbau oder in der Luft- und Raumfahrt ist jedes Gramm, das man herausholen kann, für die Treibstoffeffizienz von Bedeutung; wenn man also starke, aber leichte Teile herstellen kann, ist das für alle ein Gewinn. Es ist spannend, dass die Material-, Software- und Hardwareseiten unseres Unternehmens dazu beitragen können, Produkte, die mit der Kohlenstofftechnologie hergestellt werden, nachhaltiger zu machen.
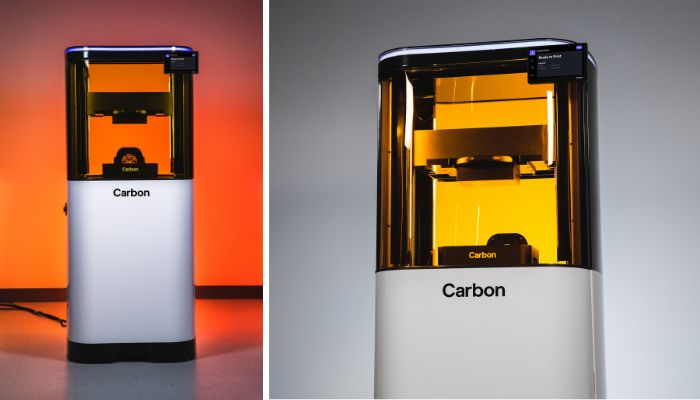
Die neuen, nachhaltigeren Materialien von Carbon können in dessen Maschinen verwendet werden
Der letzte Bereich ist das Recycling. Dies ist ein schwieriges Problem, da der Recycling-Workflow weltweit sehr ineffizient ist und nur ein kleiner Teil tatsächlich recycelt wird. Es gibt zwei Haupttechnologien für das Recycling. Die erste ist das eher traditionelle mechanische Recyclingverfahren. Bei diesem Verfahren wird ein ausrangiertes Teil gereinigt, zerkleinert und mit neuem Ausgangsmaterial gemischt, in der Regel in einer Konzentration von etwa 5-10 %, und in der Schmelze zu einem neuen Teil verarbeitet. Das hat seinen Sinn, ist aber sehr ineffizient. Das Problem besteht darin, dass bei jeder Erwärmung des Polymers die Ketten kürzer werden und einige mechanische Eigenschaften verloren gehen, so dass nur eine bestimmte Anzahl von Schleifen möglich ist, bevor das recycelte Material nicht mehr funktioniert. Aber wir arbeiten auf jeden Fall in diesem Bereich. Zum Beispiel können die Zwischensohlen von adidas in Stücke geschnitten und dann in einem Extruder zu einer neuen Form verarbeitet werden. Etwa 80 % der mechanischen Eigenschaften bleiben bei diesem Verfahren erhalten.
Es gibt auch das chemische Recycling. Das ist sehr spannend, denn anstatt ein Material zu zerkleinern und wieder einzuschmelzen, kann es einen chemischen Prozess durchlaufen, bei dem die Polymerkette aufgetrennt wird und die Monomere, aus denen sie aufgebaut ist, regeneriert werden. Auf diese Weise kann ein recyceltes Polymer mit all seinen Eigenschaften erzeugt werden. Wir haben Harze in der Forschungs- und Entwicklungsphase entwickelt, bei denen wir 50 % des Ausgangsmaterials durch eine Art chemisches Recycling zurückgewinnen können. Dieses kann dann in einer nächsten Harzcharge verwendet werden, und es entsteht ein geschlossener Kreislauf. Wir sind derzeit auf der Suche nach Partnern für dieses Verfahren, und Sie können davon ausgehen, dass wir in den kommenden Jahren mehr darüber hören werden.
Schließlich bemühen wir uns auch um die Verringerung des Verpackungsmülls, denn bei der Massenproduktion spielt die Größe des Behälters eine große Rolle für die Menge des entstehenden Abfalls.
3DN: Wie sieht es mit der additiven Fertigung insgesamt aus? Wie nachhaltig ist sie?
Die additive Fertigung ermöglicht eine lokale Produktion. Die Hersteller können herstellen, was sie brauchen, wo und wann sie es brauchen, was dazu beiträgt, die Transportkosten und den daraus resultierenden ökologischen Fußabdruck zu verringern. Wir haben bei covid gelernt, dass Lieferketten auf Kosten optimiert werden, nicht auf Effizienz und Geschwindigkeit der Teileherstellung, was zu Engpässen und anderen Problemen führen kann.
Außerdem hat man bei der herkömmlichen Fertigung ein Lager voller Teile, die im Spritzgussverfahren hergestellt werden und deren Temperatur und Feuchtigkeit kontrolliert werden muss. Das ist sehr energieintensiv. Hinzu kommt, dass oft zu viel bestellt wird, weil man versucht, den Bedarf vorherzusagen, und die überschüssigen Mengen vergeudet werden. Alternativ könnte man auch ein Lager voller 3D-Drucker haben und die Teile nach Bedarf herstellen, anstatt zu versuchen, diese komplizierten Lieferketten vorherzusagen. Wie wir bereits besprochen haben, ermöglicht die Leichtbauweise mit additiver Fertigung außerdem einen geringeren Materialverbrauch.
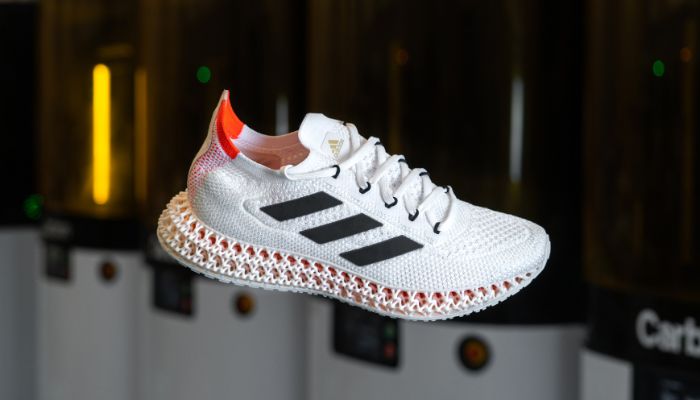
Die nachhaltigeren Methoden von Carbon haben bei der Entwicklung von Produkten für adidas eine Rolle gespielt
3DN: Haben Sie noch letzte Worte für unsere Leserschaft?
Ich glaube, dass die additive Fertigung heute wichtiger ist als je zuvor in unserer Geschichte. Vor allem, wenn es um die Herausforderungen in der Lieferkette geht, mit denen alle konfrontiert sind. Für uns ist es besonders wichtig, Wege zu finden, wie wir Produkte schneller herstellen können. Der Ansatz von Carbon besteht darin, mit Designern und Herstellern von der Idee bis zur Produktion zusammenzuarbeiten und während des gesamten Entwicklungszyklus gemeinsame Prozesse und Materialien zu verwenden. Mehr über uns und unsere Projekte können Sie HIER erfahren.
Was halten Sie von Carbon’s Ansatz zur Materialentwicklung und Nachhaltigkeit?? Lassen Sie uns dazu gerne einen Kommentar da, oder teilen Sie uns Ihre Meinung auf Facebook, Twitter, LinkedIN oder Xing mit. Möchten Sie außerdem eine Zusammenfassung der wichtigsten Neuigkeiten im 3D-Druck und der Additiven Fertigung direkt und bequem in Ihr Postfach erhalten? Dann registrieren Sie sich jetzt für unseren wöchentlichen Newsletter.
*Alle Bildrechte: Carbon