Weshalb setzen Industrieunternehmen auf den FFF-Keramik-3D-Druck?
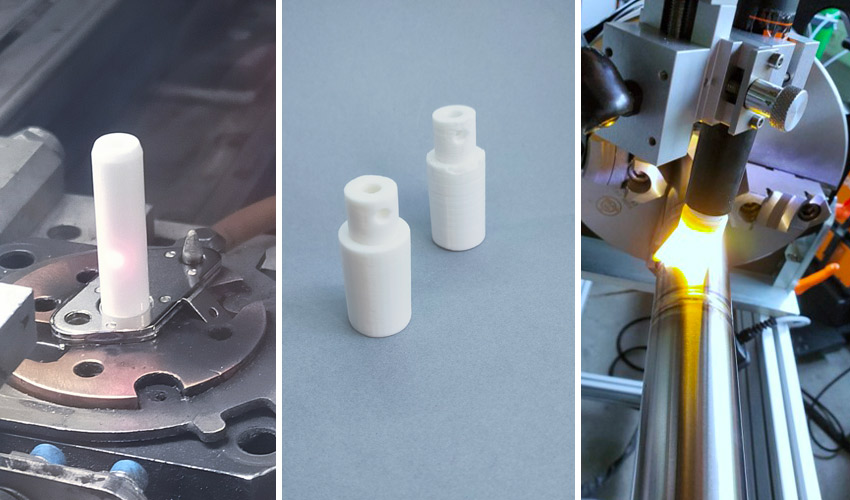
Seit seinem Eintritt in den Markt für die additive Fertigung im Jahr 2018, will Nanoe die Nutzung des Metall und Keramik 3D-Druck dank eines zugänglichen und benutzerfreundlichen Verfahrens demokratisieren. Während sich die Filamente des Herstellers in sämtlichen Laboren und Forschungszentren in Frankreich sowie international bereits erfolgreich etablieren konnten, setze nun auch immer mehr Industrieunternehmen auf die Lösungen des Unternehmens. Denn die keramischen Materialien des französischen Herstellers bieten thermische, chemische und mechanische Eigenschaften, die für anspruchsvolle Tätigkeiten wie das Orbitalschweißen oder zur Herstellung von Teilen für Heizkessel oder für die Fertigung von Drehteilen interessant sind. Dank der Zetamix-Filamente gelang es mehreren internationalen Produzenten ihre Agilität zu erhöhen, indem Produktionszeiten und Maschinenstillstandszeiten verkürzt und Kosten gesenkt werden konnten.
Zu den Anwendern von Zetamix zählen unter anderem die folgenden drei Industrieunternehmen: MGB, SAPCO und Orbital Service. Obwohl diese bereits die Vorteile der 3D-Technologien kannten, waren alle drei von den thermischen Fähigkeiten der keramischen Filamente, unter anderem Zirkoniumdioxid und Aluminiumoxid, begeistert. Alle drei Industrieunternehmen waren in mit sehr spezifische Probleme konfrontiert, welche mit traditionellen Fertigungsmethoden nur schwer oder zumindest nur zu wesentlich höheren Kosten und Fristen gelöst werden hätten können.
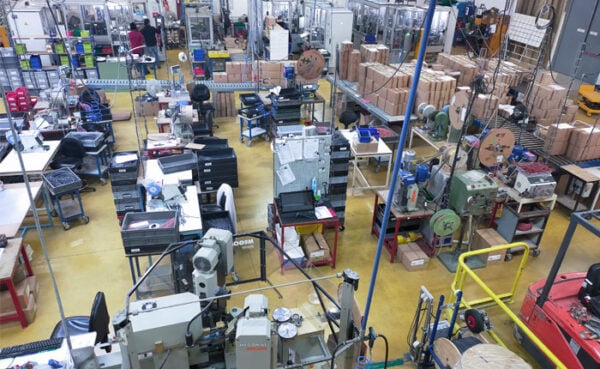
Immer mehr Industrieunternehmen integrieren die additive Fertigung (Bild: SAPCO)
Aluminiumoxid, ein hochtemperaturbeständiges Material für den 3D-Druck
MGB ist ein französisches Unternehmen, das 1956 gegründete wurde und sich seither auf die Herstellung von Drehteilen für die Verbindungstechnikindustrie spezialisiert. Das Unternehmen arbeitet hauptsächlich mit Akteuren aus der Medizin-, Luftfahrt- sowie Elektronikindustrie zusammen, die maßgeschneiderte Schrauben benötigen. Diese verfügen über unterschiedliche Härtegrade, wobei der untere Teil der Schraube in der Regel weniger widerstandsfähig ist als der obere. Damit die Herstellung dieser Art von kundenspezifischen Schrauben gelingt, hat MGB eine spezielle Maschine entwickelt, mit welcher der obere Teil unter Induktion geglüht wird, um die erforderliche Härte zu erzielen.
In diese Maschine hat MGB ein 3D-gedrucktes Teil aus Aluminiumoxid integriert. Es handelt sich dabei um eine maßgefertigte Halterung, die an einem Ende gestanzt ist die betreffende Schraube einsetzt. Anschließend wird die Schraube erhitzt, während ein Hitzesensor die Temperatur überwacht. Aus diesem Grund musste die Halterung einer solchen Temperatur standhalten können und sich darüberhinaus perfekt an die Form der jeweiligen Schraube anpassen. Außerdem muss das Material dem elektrischen Detektor Widerstand leisten können. Eine Herausforderung, welche ohne die additive Fertigung wohl so schnell nicht bewältigt werden hätte können. MGB gibt an, dass der Design- und Herstellungsprozess für eine neue Schraubenhalterung weniger als eine Woche dauert. Undenkbar, wenn der Hersteller eine subtraktive Fertigungsmethode oder einen Dienstleister dafür beauftragt hätte.
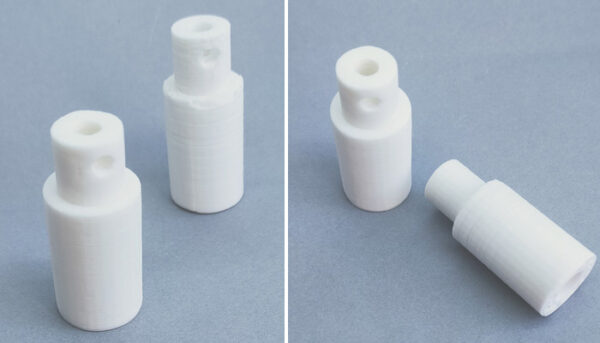
Schraubenhalterungen aus dem 3D-Drucker (Bild: Nanoe)
Zetamix-Filamente verbessern Orbitalschweißverfahren
Orbital Service ist ein deutsches Unternehmen, das sich auf das Orbitalschweißen spezialisiert und auf die Zetamix-Lösung setzt, um maßgeschneiderte Teile zu produzieren. Im Rahmen dieser Tätigkeit stellen die WIG-Schweißvorgänge (Wolfram-Inertgas) zahlreiche Herausforderungen dar, insbesondere weil Oxidation und Luftkontamination vermieden werden muss. Um diese Herausforderung zu meistern, muss das Unternehmen einen Lichtbogen erzeugen und ein inertes Schutzgas um den zu schweißenden Bereich sprühen. Da beim Orbitalschweißen die zu schweißenden Rohre jedoch sehr groß sind, sind herkömmliche WIG-Schweißdüsen nicht geeignet. Dadurch wird die Oxidation begünstigt und die Nachbehandlung der Teile ist erforderlich. Dadurch wird der Prozess erheblich verlangsamt und ist unzuverlässig.
Auch hier bietet die additive Fertigung die Lösung. Orbital Service setzt auf die FFF-Technologie mit Zetamix-Filamenten – insbesondere Aluminiumoxid -, um maßgeschneiderte WIG-Düsen zu entwickeln. Die Düsen erhalten eine konkave Form, die besser an das Volumen der zu schweißenden Rohre angepasst ist. Dadurch werden Schweißfehler vermieden und der Verbrauch von Inertgas reduziert. Der deutsche Hersteller setzt auf Aluminiumoxid wegen seiner Temperaturbeständigkeit und gibt an, dass der gesamte Design- und Herstellungsprozess nur eine Woche dauert.
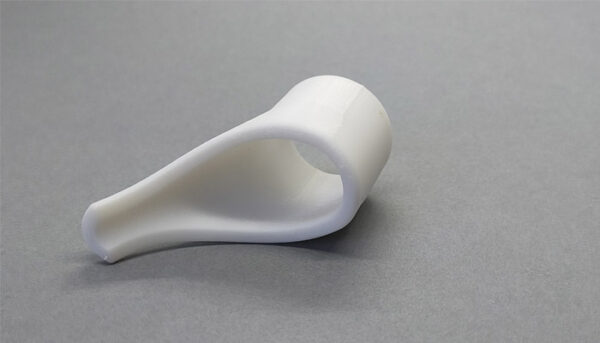
Dank der additiven Fertigung kann Orbital Service geeignete konkave Düsen entwerfen (Bild: Nanoe)
Zetamix-Lösung reduziert Wartungszeiten
Das Industrieunternehmen SAPCO stellt Zünd- und Ionisationselektroden aus Keramik her, die in Heizkessel und Industriebrenner eingebaut werden. Zu diesem Zweck hat das Unternehmen einen automatisierten Produktionsprozess mit maßgeschneiderten Maschinen entwickelt, ein großer Vorteil in der Montagephase. Denn die Montage ist komplex: Während des Schweißens der Elektrode werden zwei Metallscheiben um das Werkstück gelegt, die mithilfe von Kunststoffschweißstiften angebracht werden. Weil diese aufgrund der hohen Temperaturen schnell beschädigt werden, musste die Maschine mindestens einmal am Tag abgeschaltet werden. Diese Ausfallzeit beeinträchtigte den gesamten Produktionsprozess von SAPCO und zwang das Unternehmen dazu, eine andere Möglichkeit zur Herstellung der Stifte zu finden.
Das Unternehmen zog zunächst das Keramikspritzgussverfahren in Betracht, das sich jedoch schnell als unpraktisch, teuer und schwer zu implementieren herausstellte. SAPCO wandte sich daher der additiven Fertigung zu und setzt beim Material auf Keramik anstelle von Kunststoff. Das Unternehmen entschied sich für Zirkoniumdioxid, das Temperaturen von bis zu 800 °C standhalten kann. Die Zetamix-Lösung war ideal, da das Verfahren einfach einzusetzen und zu verwenden war. Innerhalb von fünf Tagen konnten die Teams optimierte Schweißstifte entwerfen und herstellen. Diese müssen nur einmal im Monat ausgetauscht werden, was die Wartung der Maschinen und die Ausfallzeiten erheblich reduziert.
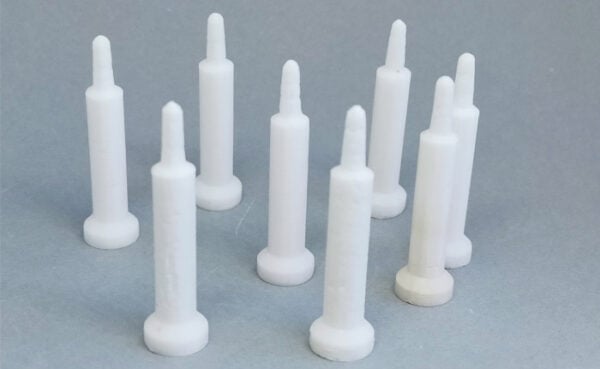
Diese Schweißstifte werden aus Zirkoniumdioxid 3D-gedruckt (Bild: Nanoe)
Keramik 3D-Druck: Die Antwort auf das Problem des internen Toolings
Auch zur Herstellung von Werkzeugen für den eigenen Bedarf, können sich Industrieunternehmen auf den FFF Keramik 3D-Druck verlassen. Mit diesen kann flexibler gearbeitet und die Produktivität gesteigert werden. Die Wahl von Keramik ermöglicht es Branchen wie der Luft- und Raumfahrt, der Automobilindustrie, der Gießereiindustrie oder auch der Schmuckindustrie, extrem hohen Temperaturen und anderen chemischen und mechanischen Belastungen standzuhalten.
Die Lösungen von Nanoe sind im Vergleich zu anderen Keramikdruckverfahren sehr kostengünstig. Darüber hinaus punktet das Verfahren mit seiner Benutzerfreundlichkeit. Das FFF-Verfahren ist einfach anwendbar und kann schnell in bestehende Produktionslinien integriert werden. Insbesondere zur Herstellung von Werkzeugen: Die Zetamix-Lösung eignet sich besser als andere Verfahren (z.B.: Photopolymerisation – die eher für die Herstellung sehr präziser Teile, z. B. in der Biomedizin notwendig ist). Auf der Website des französischen Herstellers erfahren Sie mehr über das Sortiment.
Haben Sie Erfahrungen mit dem Keramik 3D-Druck? Kannten Sie die Lösungen von Zetamix bereits? Teilen Sie uns Ihre Meinung mit und kontaktieren Sie uns. Möchten Sie eine Zusammenfassung der wichtigsten Neuigkeiten im 3D-Druck und der additiven Fertigung direkt und bequem in Ihr Postfach? Registrieren Sie sich jetzt für unseren wöchentlichen Newsletter und folgen Sie uns auf Facebook und Twitter, um stets auf dem Laufenden zu bleiben! Außerdem sind wir auch auf XING und LinkedIN zu finden.