Hyperganic entwickelt mit künstlicher Intelligenz ein 3D-gedrucktes Raketentriebwerk
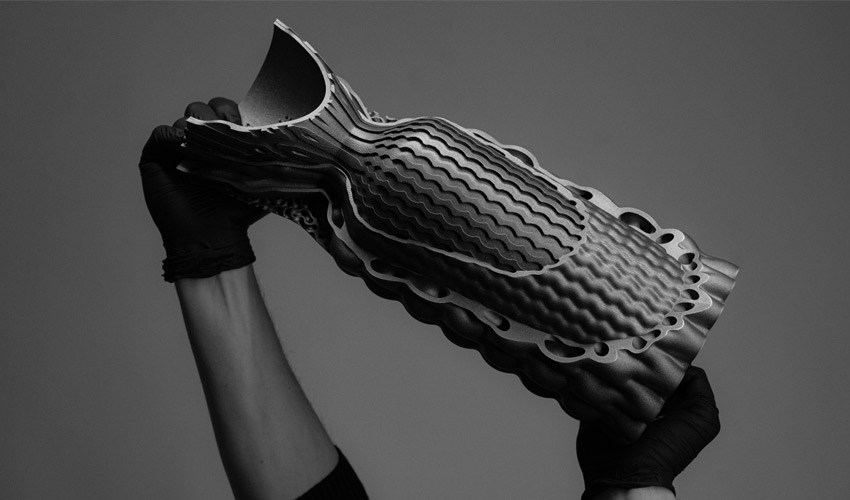
Die Münchener Unternehmen Hyperganic hat vor kurzem einen Prototyp eines 3D-gedruckten Raketentriebwerks vorgestellt, das mit künstlicher Intelligenz entwickelt wurde. Das gesamte Raketentriebwerk wurde als ein einzelnes, zusammenhängendes Teil gefertigt, in dem sowohl die Brennkammer als auch die Oberflächenkanäle eingearbeitet sind. Anstelle einer CAD-Datei wurden die Modellinformationen in einer Programmiersprache erfasst, die nur vom Hyperganic-Algorithmus gelesen werden kann. Hyperganic verwendet dann die Daten, um das endgültige Teil zu entwerfen und es Schicht für Schicht zu kreieren.
Die Verbindung von additiver Fertigung und künstlicher Intelligenz bringt für die 3D-Druckindustrie entscheidende Vorteile. Ein 3D-Drucker mit dieser künstlichen Intelligenz sol das Fehlerrisiko verringern, eine automatisierte Produktion ermöglichen usw. Im Fall von Hyperganic ermöglicht es die künstliche Intelligenz, das Design des Objekts in einem Stück zu erzeugen. Duy-Anh Pham, Leiter der Designabteilung des Müncheners Unternehmens, erklärt: „Wir vergleichen den Prozess eher mit Weiterentwickeln als mit dem Entwerfen. Sie sagen dem Algorithmus, was das Objekt tun soll, und dann lässt der Algorithmus das Objekt irgendwie mit der Leistung wachsen, die Sie im Sinn hatten, mit den Spezifikationen. Der Prozess erstellt also keine Blaupause, sondern die DNA für ein Objekt.“
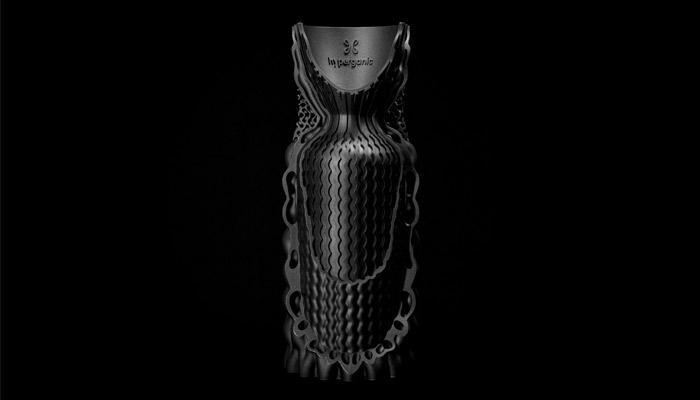
Das gesamte Raketentriebwerk wurde 3D-gedruckt (Bildnachweis: Hyperganic)
Der Herstellungsprozess
Hyperganics Ziel war es, ein Raketentriebwerk als eine einzelne Baueinheit zu konzipieren, um ein möglichst geringes Gewicht und eine möglichst effiziente Kühlung zu erreichen. Üblicherweise werden die verschiedenen Komponenten eines Raketentriebwerks getrennt voneinander konstruiert und dann die Kühlkanäle mit der Brennkammer verschweißt. Dies kann jedoch auf lange Sicht Fehlfunktionen und Explosionen verursachen. Mit der neuen Herstellungsmethode ist Hyperganic in der Lage, alles als ein einziges Bauteil zu konstruieren und so die Endleistung des Triebwerks zu erhöhen. Das Unternehmen hat die zentralen Elemente des Motors, nämlich die Brennkammer und die Kühlkanäle, genauestens untersucht und auf der Grundlage dieser Daten hat ein Algorithmus eine Geometrie erzeugt, die alle geforderten Spezifikationen erfüllt.
Sodann hat das Unternehmen einen ersten Metallprototypen aus einer Nickellegierung per 3D-Druck gefertigt. Duy-Anh Pham fügt hinzu: „Wir sind in der Lage, in verschiedenen Materialdichten zu drucken, eine Methode, die bisher im Raketenbau noch nicht eingesetzt wurde. So ist der innere Teil sehr massiv, während die Struktur nach außen hin poröser wird, um Gewicht zu sparen. Jedes zusätzliche Pfund zählt.“ Da der Start einer Rakete in der Tat einen erheblichen Kostenfaktor darstellt, hat die Reduzierung des Gesamtgewichts um nur wenige Pfund eine erhebliche Auswirkung.
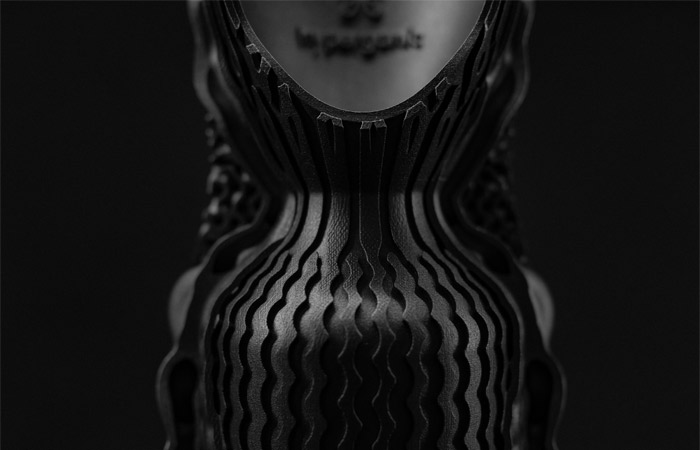
Nahaufnahme von dem 3D-gedruckten Raketentriebwerk (Bildnachweis: Hyperganic)
Hyperganic arbeitet derzeit mit mehreren Luft- und Raumfahrtunternehmen zusammen, um herauszufinden, wie diese den neue Modellierungsansatz in ihre Betriebsabläufe integrieren können. Der Einsatz von künstlicher Intelligenz soll es ihnen ermöglichen, völlig neue Formgebungen zu entwerfen, um das Gewicht der Teile zu reduzieren und die Leistung zu erhöhen. Das Hyperganic hofft, in Sachen Anwendung noch mehr erreichen zu können. Die Softwarelösung soll modular sein und mehrere algorithmische Kombinationsmöglichkeiten bieten. Weitere Informationen finden Sie auf der offiziellen Website.