Harz vs. Polymerpulver: Welche Materialfamilie sollte man beim 3D-Druck wählen?
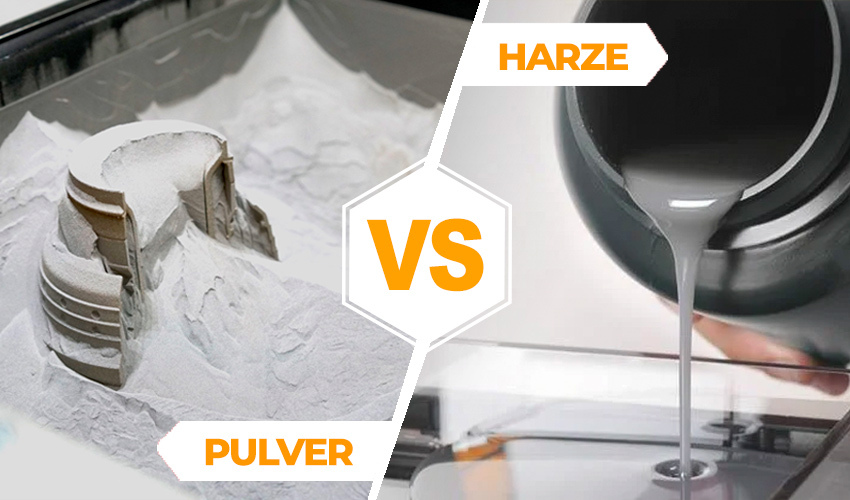
Je nach Anwendung und 3D-Technologie können unterschiedliche Materialien für den Einsatz bestimmt werden, was die Auswahl aufgrund der großen Bandbreite nur noch schwieriger macht. Ob Kunststoffe, Keramiken oder sogar Metalle, das Materialportfolio kann lang und unübersichtlich sein. Daher möchten wir im Folgenden einen detaillierten Überblick über zwei polymere Materialfamilien von Harzen und Kunststoffpulvern im direkten Vergleich geben. Obwohl es heutzutage eine Reihe von Pulvern und Harzen auf dem Markt gibt, wie z. B. Metallpulver oder sogar Keramikharze, werden wir uns heute nur auf Kunststoffe konzentrieren.
Es ist wichtig zu erwähnen, dass es zwei Arten von Kunststoffen für den 3D-Druck gibt: duroplastische Kunststoffe und thermoplastische Kunststoffe, wobei der Hauptunterschied zwischen diesen beiden Familien das unterschiedliche Verhalten bei Hitzeeinwirkung ist. Einerseits zersetzen sich duroplastische Kunststoffe, wenn sie ausgehärtet sind, und bilden sich nach dem Abkühlen nicht wieder neu. Andererseits sind Thermoplaste die am häufigsten verwendeten, die bei Erwärmung die gewünschte Form annehmen und verschiedene Schmelz- und Verfestigungsprozesse durchlaufen können, wobei sich ihre Eigenschaften bei jeder Wiedererwärmung leicht verändern.
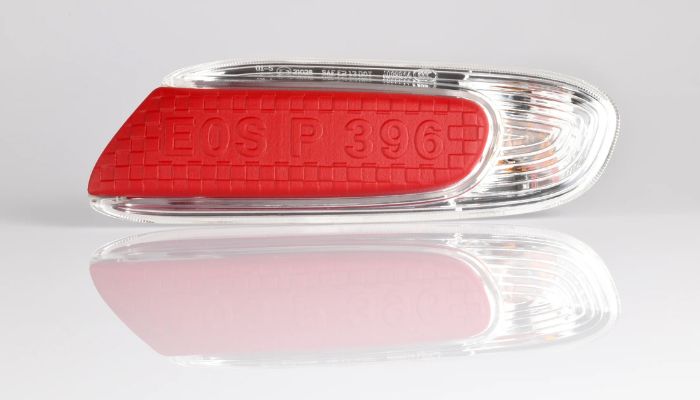
Kunststoffpulver können in vielen Bereichen eingesetzt werden, z. B. in der Automobilindustrie (Bild: EOS)
Laut einer Studie der Forschungsabteilung von Statista gehören diese beiden Materialfamilien zu den am häufigsten verwendeten. Für Kunststoffpulver soll der Markt laut Report Linker bis 2029 auf 3 Milliarden Dollar anwachsen, für Harze wird dieser Wert laut Fortune Business Insights sogar auf über 750 Milliarden Dollar geschätzt. Da es auch um den Einsatz verschiedener Technologien geht, wie SLS oder MJF für Pulver und Material Jetting und SLA zum Beispiel für Harze, je nach der unterschiedlichen Materialfamilie, werden wir Sie in dieser Hinsicht aufklären. Auch über die Nachbearbeitung, die unterschiedlichen Preise, Eigenschaften der Materialfamilien, Hersteller und vieles mehr!
Merkmale und Eigenschaften von Kunststoffpulvern und -harzen
HARZE
Auf dem aktuellen Markt der Polymere gibt es verschiedene Harze, die je nach ihren Eigenschaften unterschiedliche Anwendungen in den verschiedenen Sektoren haben. Die Verwendung von Harz 3D-Druck ermöglicht die Schaffung von kleinen Objekten mit großem Detail. Zu den Harzen, die auf dem Markt zu finden sind, gehören:
- Standardharze: Diese sind am weitesten verbreitet und am billigsten, leicht auf dem Markt zu finden, einfach zu bearbeiten, leicht zu schleifen, weich im Griff, aber gleichzeitig zerbrechlich und können leicht brechen und reißen. Sie werden für das Rapid Prototyping oder für Haushaltsgegenstände verwendet. Hier finden Sie einige der gängigsten Thermoplaste, die Ähnlichkeiten mit ABS und PLA aufweisen.
- Flexible Harze: Sie werden in der Regel für den Druck widerstandsfähiger Objekte verwendet, die sich biegen oder zusammendrücken lassen. Außerdem gibt es eine große Bandbreite an Flexibilitäten und die Shore-Härte kann individuell angepasst werden.
- Wasserabwaschbare Harze, die, wie der Name schon sagt, nicht mit Isopropylalkohol, sondern mit Wasser abgewaschen werden müssen, so dass die Nachbearbeitung einfacher ist. Sie sind geruchsarm und haben eine trockene und weniger klebrige Oberfläche.
- Industrieharze, die sich für die Herstellung von Teilen eignen, die eine starre und harte Oberfläche erfordern. Innerhalb der Industrieharze finden wir:
- Temperaturbeständige Harze, die bis zu 238 ºC standhalten. Diese Harze werden für die Herstellung von Prototypen verwendet, die eine größere Detailgenauigkeit, Präzision und hohe thermische Stabilität erfordern.
- Gießbare Harze sind eine Art von Harz, das einen hohen Detaillierungsgrad und eine großartige Oberfläche aufweist und dessen Aushärtungsprozess schneller ist als bei anderen Harzen. Das Hauptmerkmal ist, dass das Verfahren nach dem Gießen sauber ist und keine Rückstände hinterlässt.
- Dentalkunststoffe: Für den Dentalbereich gibt es spezielle Harze, sowohl farbige als auch transparente, flexiblere oder steifere. Einige Anwendungen in der Zahnmedizin sind Brücken, Kronen, Retainer oder Schienen, und deshalb müssen diese Harze sterilisierbar sein.
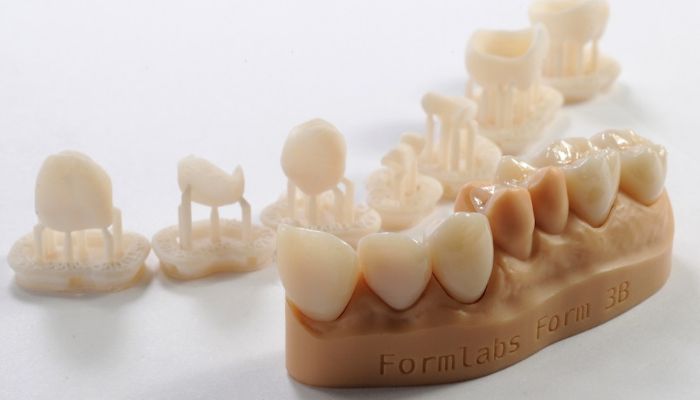
Harze spielen innerhalb der Dentalindustrie eine wichtige Rolle (Bild: Formlabs)
PULVER
Auf dem heutigen Markt für Polymerpulver aus thermoplastischen Kunststoffen gibt es eine breite Palette von Kunststoffen, von denen Nylon der am weitesten verbreitete ist. Es ist wichtig hinzuzufügen, dass Pulver auch sogenannte Perlen enthalten können, wie z.B. HP 3D High Reusability PA 12 Glass Beads, das – wie der Name schon sagt – ein Thermoplast ist, der mit 40% Glasperlen gefüllt ist.
- Nylon: Auch als Polyamid bekannt, haben wir die gebräuchlichsten unter ihnen gefunden: PA12 und PA11.
- Nylon PA12 wird aus Erdöl hergestellt. Dieses Material hat die Fähigkeit, drastischen Temperaturschwankungen zu widerstehen, und ist beständig gegen verschiedene Chemikalien.
- Nylon PA 11 ist ein biobasiertes Polymer, aber das bedeutet nicht automatisch, dass es auch biologisch abbaubar ist. Wie wir wissen, enthält Polyamid 11 Rizinusöl, hat eine gute Wärmebeständigkeit, eine hohe Elastizität und ist ökologischer als PA12.
Diese beiden Nylontypen nehmen wenig Feuchtigkeit auf und werden beispielsweise in der Automobilindustrie wegen ihrer Widerstandsfähigkeit und Reibung verwendet.
- PEEK: Ein teilkristalliner Thermoplast, der in der verarbeitenden Industrie wegen seiner mechanischen Eigenschaften, seiner Hitze- und Verschleißbeständigkeit und seiner Fähigkeit, bestimmte Metalle aufgrund seines Gewichts/Festigkeits-Verhältnisses zu ersetzen, sehr geschätzt wird. Allerdings ist es ein schwierig zu bearbeitendes Material, das vorherige Schritte erfordert. Aus diesem Grund wird dieses Material vor allem in der Automobil-, Luft- und Raumfahrt- sowie in der medizinischen Industrie eingesetzt.
- Verbundwerkstoffe: Verbundwerkstoffe bestehen aus einem Matrixpolymer und kurzen oder langen Fasern. Die bekanntesten sind Kohlenstofffasern und Glasfasern. Kohlefaser wird durch Mischen eines Polymers mit Kohlefasern hergestellt, wodurch ein leichteres, stärkeres und steiferes Material entsteht. Glasfasern, bei denen ein Polymer mit Glasfasern gemischt wird, sind genauso stark wie Kohlenstofffasern, aber weniger steif und dichter.
- Polypropylen: Dieser thermoplastische Kunststoff (PP) ist ebenfalls teilkristallin und zeichnet sich unter anderem durch seine Beständigkeit gegen chemische Produkte, seine gute elektrische Isolierung und sein geringes Gewicht aus, ist jedoch schwer zu drucken, da seine thermische Behandlung kontrolliert werden muss.
- TPU: Thermoplastisches Polyurethan (TPU), ein Material, das sich durch seine hohe Haltbarkeit und Flexibilität bei der Verarbeitung auszeichnet. Auch hat eine hohe Beständigkeit gegen Stöße, Abrieb und Schnitte, obwohl nicht tolerieren hohe Temperaturen, ein Schritt, den Sie in Ihrem 3D-Maschine und Technologie verwendet berücksichtigen müssen.
Ein eindeutig umweltfreundlicher Aspekt von Kunststoffpulver ist seine Wiederverwertbarkeit. Da es sich bei den für SLS und MJF verwendeten Pulvern um Thermoplaste handelt, können sie gesiebt und nach dem Sinterprozess mit etwas neuem Pulver gemischt werden, um das überschüssige Material wiederzuverwenden und so Abfall zu vermeiden.
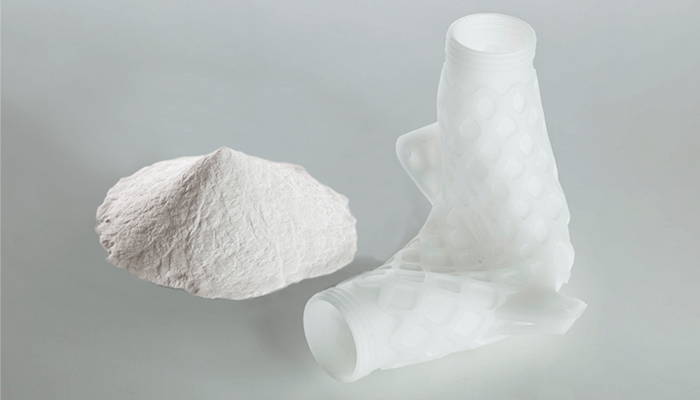
Bild: BASF
Der digitale 3D-Druck-Workflow
HARZE
Kommen wir zum ersten Schritt in der 3D-Druckkette, dem Designprozess, der am Anfang eines jeden 3D-Druckteils steht. Wenn wir uns für ein Teil entschieden haben, das gedruckt werden soll, ist auf jeden Fall zu beachten, dass das 3D-gedruckte Teil während des gesamten Druckvorgangs in der Schale ist, dem – je nach Art, Form, Geometrie und Größe des Teils – in der Entwurfsphase Stützstrukturen hinzugefügt werden muss, die nach dem Druck natürlich wieder entfernt werden müssen.
Für den 3D-Druck mit Harz gibt es zum einen die Vat-Polymerisation, die bei SLA-, DLP- und LCD-Verfahren zum Einsatz kommt und bei der ein ultraviolettes (UV-)Licht zum Aushärten des Harzes verwendet wird, wobei eine andere Lichtquelle und ein anderes Verfahren zur Formgebung des Lichts verwendet werden. Aber auch das Material-Jetting, bei dem mehrere Harze gleichzeitig verwendet werden können, sogar transparente. Für den 3D-Druck mit Kunststoffharzen gibt es, wie bereits erwähnt, SLA, DLP und MSLA, die unterschiedliche Lichtquellen verwenden. SLA verwendet einen Laser, um das Harz Punkt für Punkt auszuhärten, während DLP einen Projektor als Lichtquelle verwendet, der den gesamten Harzbehälter in einer einzigen Projektion aushärtet. Die Material-Jetting-Technologie verwendet ein UV-Licht, das für die Aushärtung des Materials in den ausgewählten Bereichen verantwortlich ist. Was die Toxizität von Harz betrifft, so ist es wichtig zu wissen, dass es bei Kontakt mit der Haut oft zu schweren Reizungen und Allergien führen kann, insbesondere wenn es den UV-Strahlen des Sonnenlichts ausgesetzt ist. Das Einatmen der Dämpfe kristallisiert als weitere toxische Gefahr beim Umgang mit Harz im 3D-Druck. Diese Dämpfe können bei den Anwendern aufgrund ihrer hohen Toxizität Schwindelanfälle auslösen, was daher die Wichtigkeit von optimaler Schutzkleidung unterstreicht.
Wenn Sie mit Harzen drucken, haben Sie vielleicht schon bemerkt, dass sich nach dem Druck oft klebrige Harzrückstände auf der Oberfläche befinden, die durch Waschen in einem Lösungsmittel entfernt werden müssen. Als Lösungsmittel ist Isopropylalkohol das gebräuchlichste und liefert die besten Ergebnisse. Das Entfernen des Harzes wird von vielen Anwendern als lästig empfunden, ist aber laut einer von PostProcess Technologies veröffentlichten Studie mit 42 % die zweithäufigste Nachbehandlungsmaßnahme. Sie müssen auch die während des Entwurfsprozesses hinzugefügten Stützen entfernen. Dies geschieht am besten mit einer Spitzzange. Da nicht unbedingt alle Polymerisationsreaktionen unmittelbar nach dem Druck abgeschlossen sind, müssen die aus Harz hergestellten Teile ausgehärtet werden. Hierfür gibt es viele Methoden, die von der reinen Lichthärtung – z. B. durch Sonnenlicht – bis hin zu Aushärtungsgeräten reichen. Beachten Sie, dass die Aushärtungszeit von Teil zu Teil unterschiedlich ist. Bei der Endbearbeitung schließlich können Sie die Oberflächen glätten, die Teile selbst verstärken oder sogar eine ästhetische Oberfläche schaffen.
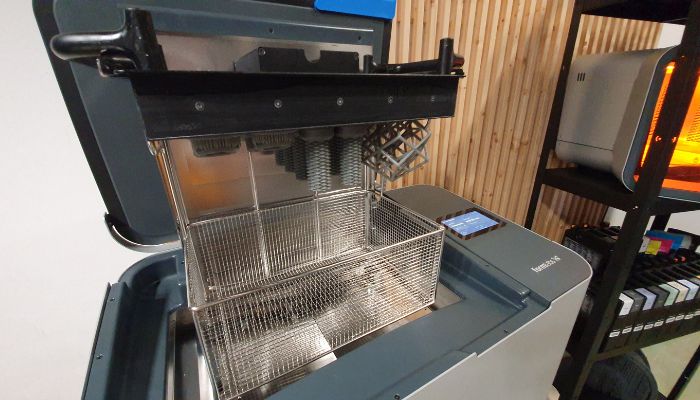
Die Nachbearbeitung von Harzen erfordert sämtliche Schritte, wie hier das Abwaschen (Bild: Formlabs)
PULVER
Wenn Sie mit Polymerpulver drucken wollen, dann sollten Sie wissen, dass – im Gegensatz zur Nutzung von Harz – Sie dafür keine Stützstrukturen benötigen. Der Grund dafür liegt darin, dass sich das 3D-Druckteil während des Drucks im Pulverkuchen befindet und somit gestützt wird. Beim 3D-Druck mit Kunststoffpulvern unterscheidet man zwischen SLS-, MJF-, SAF- und Binder Jetting-Technologie, die Pulver zur Herstellung von 3D-Druckobjekten verwenden. Bei der SLS-Technologie wird nach dem Auftragen einer dünnen Pulverschicht mit Hilfe eines Beschichtungsmessers ein Laser eingesetzt, der das Pulver selektiv sintert und den ausgewählten Bereich verfestigt. Außerdem gibt es noch das MJF-Verfahren von HP, das ähnlich wie die anderen Powder Bed Fusion-Technologien funktioniert, aber einen zusätzlichen Schritt vorsieht: die Zugabe eines Detaillierungsmittels! Nach dem Auftragen der Pulverschicht trägt das Schmelzmittel selektiv die Bereiche auf, in denen die Partikel miteinander verschmolzen werden müssen. Gleichzeitig wird das Detaillierungsmittel aufgetragen und reduziert die Verschmelzung an den Rändern des Teils, so dass scharfe und glatte Kanten erzeugt werden können. Bei SAF – Selective Absorption Fusion – besteht der Hauptunterschied darin, dass bei dieser Technologie eine infrarotabsorbierende Flüssigkeit verwendet wird, um das Polymerpulver zu verschmelzen; Binder Jetting funktioniert ähnlich wie SLS, aber im Gegensatz dazu wird bei BJ kein Laser zum Sintern des Pulvers verwendet, sondern ein Druckkopf, der Bindertröpfchen auf die Pulveroberfläche aufträgt, wodurch die Pulverpartikel Schicht für Schicht gebunden werden. Einige Maschinen, wie die von VoxelJet, erlauben die Verwendung von Polymeren.
Bei der Verwendung von Kunststoffpulvern beginnt die Nachbearbeitung praktisch mit der Entfernung des Pulverkuchens. Dazu gehört ein Abkühlungsprozess, der je nach Teil bis zu 10 Stunden dauern kann. Danach folgt die Pulverentfernung. Diese kann manuell oder automatisch mit einer Maschine erfolgen. Bei der manuellen Entnahme ist das Tragen einer speziellen Schutzausrüstung erforderlich, da beim Einatmen des zu entfernenden Pulvers Gesundheitsrisiken entstehen können. Es gibt zwar eine Reihe weiterer Veredelungsschritte für Kunststoffteile, wie z.B. Galvanisieren, Lackieren oder Schleifen, diese sind jedoch optional. Generell ist es wichtig zu wissen, dass bei der Arbeit mit Polymerpulver eine entsprechende Schutzmaske notwendig ist, da dieses Pulver aufgrund des pulverförmigen Zustandes des Materials in den Lungenbereich des Anwenders gelangen kann. Die Folgen sind etwa Atembeschwerden und Kurzatmigkeit. Auch wenn geschmolzenes Material mit der Haut in Berührung kommt, kann dies zu Hautreizungen führen.
Die Preisspanne von Kunststoffpulvern und -harzen
Der Preis der beiden Materialien hängt stark von den jeweiligen Eigenschaften und Anwendungsbereichen ab. Es lässt sich jedoch sagen, dass der Preis für eine 500-Gramm-Packung Harz bei etwa 25 Euro für ein schwarzes Standardharz beginnt und bis zu einem Liter für knapp 400 Euro inklusive Mehrwertsteuer reicht. Kunststoffpulver liegen in einer ganz anderen Preisspanne als Harze. PA 11 zum Beispiel kostet zwischen 70 Euro und 300 Euro pro Kilogramm. Bedenken Sie aber, dass beim Druck mit Kunststoffpulver dieses zu einem bestimmten Prozentsatz, meist ab 50 %, wiederverwendet werden kann, was sich daher auch im Preis niederschlägt.
Welche Hersteller gibt es auf dem Markt?
Im Vergleich zum Filamentmarkt sind die Märkte dieser beiden Materialfamilien nicht so groß, da es bei Filamenten Hunderte von Anbietern gibt, während Harze und Kunststoffpulver oft direkt von den Herstellern der 3D-Maschinen bezogen werden. Ein Grund dafür liegt in der Tatsache, dass es für diese Materialfamilien im Vergleich zu FDM/FFF-Druckern nicht allzu viele offene 3D-Drucker gibt. Die bekanntesten Lieferanten dieser Materialfamilien sind die so genannten Chemiekonzerne, die für die Herstellung der Rohstoffe verantwortlich sind, und die 3D-Unternehmen, die diese anschließend nutzen oder manchmal sogar gemeinsam mit den Chemiekonzernen entwickeln. Bei den Rohstoffen für Harze sind die Chemiekonzerne Locotite Henkel und Covestro Additive Manufacturing zu nennen, aber beispielsweise auch BASF und Arkema, die mit 3D-Druckherstellern zusammenarbeiten und oft eigene Materialien entwickeln. Beispiele hierfür sind Zortrax, Formlabs und auch EnvisionTEC. Bei den Kunststoffpulvern hingegen sind es ebenfalls die Chemieunternehmen, wobei hier auch Arkema und BASF in Zusammenarbeit mit HP zu nennen sind. Aber auch bekannte Gesichter wie Evonik arbeiten mit EOS zusammen, zum Beispiel an eigenen Materialien. Nicht zu vergessen sind aber auch Unternehmen, die für die Herstellung von druckfertigen Harz- oder Kunststoffpulvern zuständig sind, wie das deutsche Unternehmen AM Polymers.
Anwendungsfelder der beiden Materialfamilien
Um ein tieferes Verständnis für die beiden Materialfamilien zu bekommen, gehen wir außerdem gezielt auf die Anwendungsbereiche ein. Wenn wir über Harze sprechen, lassen sich die Möglichkeiten der verschiedenen Farben wie weiß, blau, grau, orange, rosa, gelb oder sogar transparent hervorragend für Bereiche wie Schmuck, Gesundheitswesen sowie Bildung und Unterhaltung nutzen. Vor allem in der Zahnmedizin werden den ihm große Fortschritte zugeschrieben, da hier die Herstellung von Kronen, Zahnimplantaten und sogar chirurgischen Führungen ins Spiel kommt.
Was die Anwendungsmöglichkeiten von Kunststoffpulvern angeht, so findet man diese auch in der Gesundheitsbranche. Da Nylon biokompatibel ist, eignet es sich beispielsweise ideal für die Herstellung von Prothesen, da es in direktem Kontakt mit der Haut stehen kann. Auch die Fertigungsindustrie schätzt diese Materialfamilie sehr, da sie für Funktionsprototypen, Kleinserien, Brücken und sogar für die Herstellung von Sonderanfertigungen verwendet wird. Zum Beispiel können daraus Zahnräder oder sogar Scharniere hergestellt werden.
Haben Sie bereits Kontakt im 3D-Druck mit Harz oder Kunststoffpulver gehabt? Lassen Sie uns dazu einen Kommentar da, oder teilen Sie es uns auf Facebook oder LinkedIN mit. Möchten Sie außerdem eine Zusammenfassung der wichtigsten Neuigkeiten im 3D-Druck und der Additiven Fertigung direkt und bequem in Ihr Postfach erhalten? Dann registrieren Sie sich jetzt für unseren wöchentlichen Newsletter.
Ich suche ein gutes Unternehmen für solche Kunststoffteile. Beziehungsweise ich bin noch nicht sicher, wer welches Verfahren gut anbietet. Gut zu wissen, was möglich ist in dem Bereich!