Gitterstrukturen im 3D-Druck
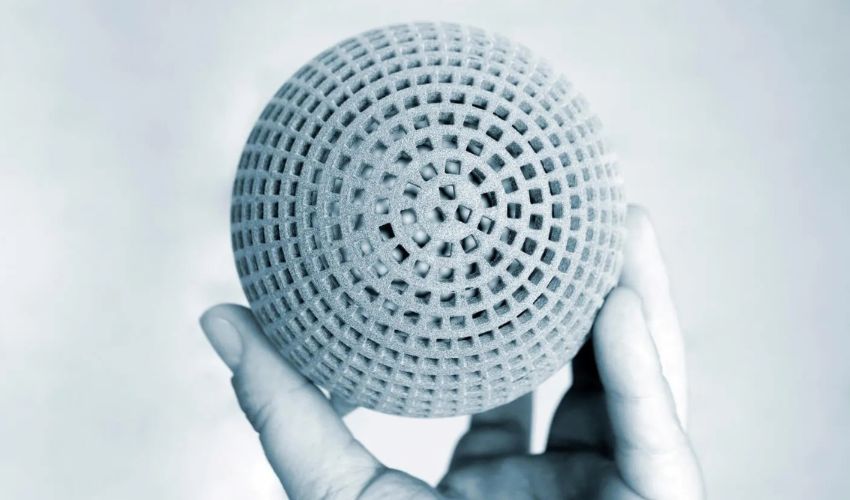
In Automobilteilen, medizinischen Implantaten, Laufschuhen oder Wanderrucksäcken – immer häufiger sehen wir 3D-gedruckte Teile in Gitter- oder Wabenmustern. Man könnte annehmen, diese Gitterstrukturen oder lattice structures wie sie im Englischen heißen, wären der letzte Schrei im 3D-Druck und DfAM. Tatsächlich sind wir im Alltag ständig von natürlich vorkommenden Gitterstrukturen umgeben. Man denke dabei an Bienenwaben, Schneeflocken, Zäune, Schwämme oder den Eiffelturm.
Gitterstrukturen bestehen aus einer Ansammlung von verbundenen Knoten in Mustern (als Zelle bezeichnet), die sich entweder wiederholen oder beständig unterscheiden und Vorteile bezüglich Bauteileigenschaften oder Produktion bieten. In der traditionellen Fertigung sehen wir tendenziell wenige Gitter, da diese Verfahren die komplexen Gitterdesigns nicht umsetzen können. Darin liegt allerdings die Stärke der additiven Fertigung, weshalb Gitterstrukturen und 3D-Druck das perfekte Doppel bilden.
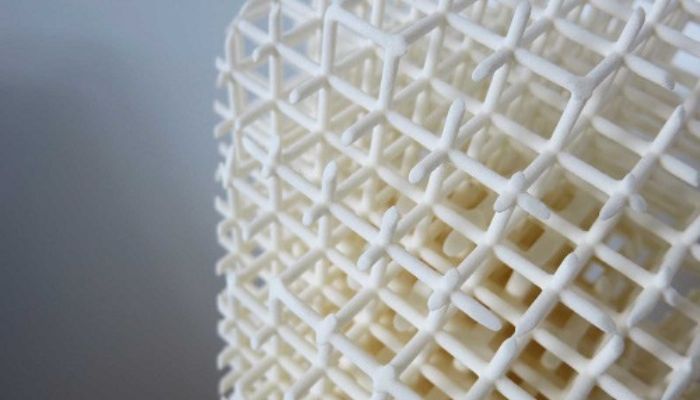
3D-gedruckte Gitterstruktur (Bild: Sculpteo)
Bevor wir zum 3D-Druck von Gitterstrukturen kommen, werfen wir zunächst einen Blick darauf, welche Gitter es gibt. Prinzipiell bilden sich die einzelnen Gitter dadurch, dass Knoten mit Balken verbunden werden. Je nachdem in welcher Weise die Anordnung von Balken und Gittern erfolgt, entstehen die regelmäßig oder unregelmäßigen Muster. Indem die Dichte der Balken und die Geometrie und Größe der Zellen verändert werden, können die Elastizität, Steifigkeit etc. eines Bauteils gesteuert werden. Tatsächlich gibt es eine Vielzahl an verschiedenen Gittertypen und es wird intensiv daran geforscht, immer vielfältigere und leistungsstärkere Gitter zu entwickeln. Dennoch können wir die gängigen Gitter in einige Kategorien einordnen.
- Planare Gitter: diese Gitter bilden auf einer flachen, zweidimensionalen Form aufbauend ein Bauteil in drei Dimensionen. Da die Schichten einzeln gedruckt werden, ist es mitunter nötig, diese danach zusammenzusetzen. Zu dieser einfachsten Gitterart zählen Tetraeder, Voronoi-Gitter, rhombische und hexagonale Gitter (z.B. Bienenwaben)
- Strebengitter: Bei diesem Gitter bilden miteinander verbundene Balken einer Elementarzelle ein Netzwerk, indem Knoten-, Eckpunkte oder Kanten der Zellen miteinander verbunden werden. Die Druckschichten überlappen sich und greifen ineinander. Es kann vorkommen, dass das Gitter mit Stützmaterialien verstärkt werden muss.
- TPMS-Gitter (Triply Periodic Minimal Surface): Grundlage dieses Gitters ist eine trigonometrische Gleichung, mit der die Zelle berechnet wird. Die Grundform der einzelnen Gitter kann variieren.
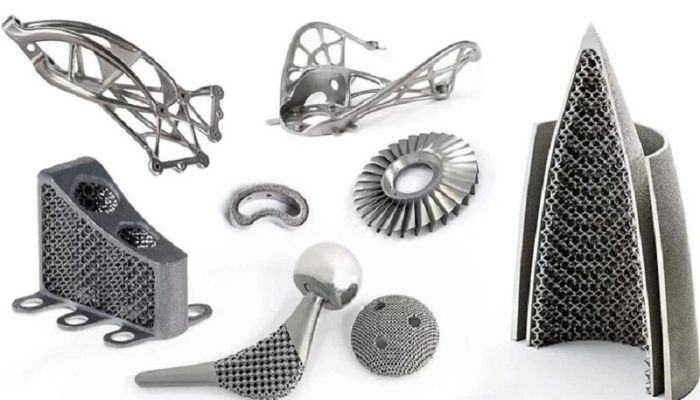
Es gibt eine Vielzahl an 3D-gedruckten Gitterstrukturen (Bild: Shenzhen JR Technologies)
Gitterstrukturen können darüber hinaus entweder periodisch sein oder stochastisch. Bei periodischen Gittern wird das Muster der Elementarzelle über die gesamte Struktur hinweg beibehalten. Bei stochastischen Gittern hingegen variieren die Zellenform und deren Größe und sind auch in ihrer Anordnung nicht gleichmäßig. Dies hat zum Ziel, dass die Struktur in bestimmte Richtungen gestärkt wird.
Wie das jeweilige Gitter ausfällt, hängt eng mit dem Ziel zusammen, wofür das Gitter gedacht ist. Beim Design wird berücksichtigt, welche Geometrie und Größe sinnvoll sind, und welche Steifigkeit sich dadurch ergibt. Ein weiterer Faktor ist das Knickverhalten, das heißt, ob, wie und in welche Richtungen die Struktur nachgibt. Außerdem wird erörtert, ob das Gitter bei Verformung Energie aufnehmen kann.
Design und 3D-Druck von Gitterstrukturen
Für die Erstellung von 3D-gedruckten Gittern muss im Design-Prozess ein spezielles Tool verwendet werden. Zwar bieten einige Modellierungssoftware-Pakete solche Funktionen an, wesentlich verlässlicher sind aber spezifische Software-Pakete, die auf Topologieoptimierung abzielen oder Software für Generatives Design. Beim Generativen Design wird anhand der benötigten Bauteilqualitäten und des festgelegten Druckverfahrens das optimale Design berechnet. Sollte dieses Gitterstrukturen enthalten, werden auch diese berechnet und die Zellstruktur, Zelldichte und Anordnung wird festgelegt. Ansonsten gibt es mittlerweile zahlreiche Tools auf dem Markt, um 3D-Modelle zu optimieren und lattice structures zu erstellen, darunter Autodesk Within, nTop von nTopology, Meshify, 4D_Additive von Core Technologie, Netfabb oder HyDesign von Hyperganic, um nur einige zu nennen. Das erstellte Gitter wird sich je nach Anwendung, Material und Druckverfahren unterscheiden.
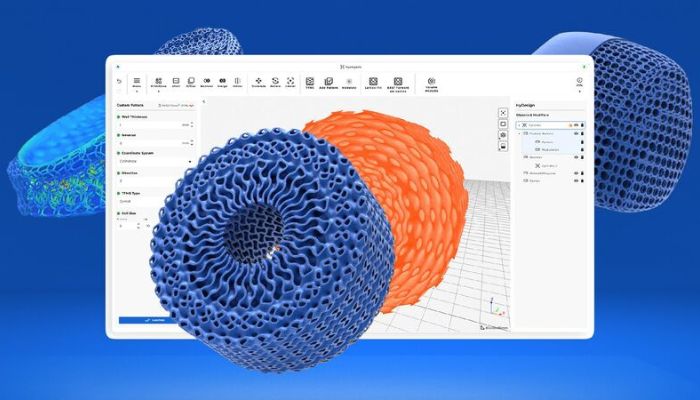
Mit HyDesign von Hyperganic können Sie Gitterstrukturen designen. (Bild: Hyperganic)
Gitterstrukturen sind per 3D-Druckverfahren wesentlich einfacher umzusetzen als bei traditionellen Fertigungsverfahren, da die Gitter oftmals sehr komplex und filigran sind. Darüber hinaus ist der Druck von Gittern auch schneller als der Druck von ausgefüllten Festkörpern. Prinzipiell können Gitterstrukturen mit einer großen Bandbreite an Materialien und Druckverfahren umgesetzt werden, jedoch sind je nach Drucktechnologie einige Besonderheiten zu beachten.
Bei FDM und SLA müssen Stützstrukturen hinzugefügt werden, sollte das Gitter sehr groß ausfallen. Bei Pulververfahren mit Polymeren (SLS, MJF) müssen genügend Zugangspunkte vorhanden sein, damit das Entpulvern kein Problem darstellt und das überschüssige Pulver gut entfernt werden kann. Dies spielt auch bei DMLS eine Rolle. Zusätzlich müssen Stützen miteingerechnet werden, da ansonsten nur Brückenabstände von 2 mm überbrückt werden können. Solche Besonderheiten werden bereits im Design-Schritt miteinkalkuliert.
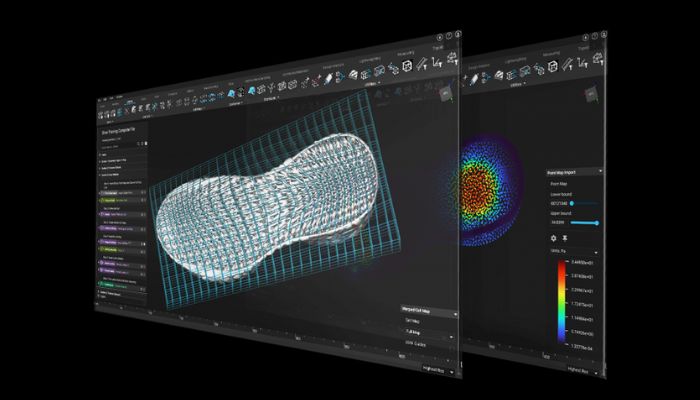
Die gewünschten Eigenschaften des Bauteils und seine Anwendung fließen in das Design der Gitterstruktur mit ein. (Bild: nTopology)
Herausforderungen und Vorteile von Gitterstrukturen
Die Zellausrichtung, Brückenabstände und Winkel zur Bauplatte gehören neben dem Druckverfahren und dem gewählten Material zu den größten Herausforderungen beim Erstellen von Gitterstrukturen. Einerseits muss das Gitter die Ziele des endgültigen Teils erfüllen, andererseits muss es aber auch umsetzbar sein und je nachdem angepasst werden. Während des Design-Prozesses kann es aber auch zu anderen Problemen kommen. Da die Gitterstrukturen sehr komplex sind, fallen die digitalen Dateien sehr schwer aus und können über 1 GB beanspruchen. Auch Simulationen des 3D-Designs sind eine Herausforderung, da eine hohe Rechenleistung erforderlich ist.
Trotzdem überwiegen die Vorteile, denn Gitterstrukturen bieten sowohl einen ökologischen als auch ökonomischen Mehrwert und wirken sich positiv auf die Effizienz des Bauteils aus. Indem durch die Gitter Material gespart wird, können leichtere Produkte erstellt werden, was sich in der Performance der Leichtbauteile widerspiegelt und in einer Kostenreduktion. Diese ergibt sich durch die Materialreduktion und die Einsparung an beispielsweise Treibstoff, weil leichtere Bauteile weniger Antriebskraft benötigen. Weitere ökonomische Vorteile sind die lokale Produktion und schnellere Iterationen.
Auch im Hinblick auf die Bauteilqualität lohnt es sich, auf Gitter zu setzen. Die Gitterstrukturen können zur besseren Schockabsorption beitragen, zur Flexibilität der Produkte, aber auch konträr dazu für stabilere Produkte sorgen und eine höhere Steifigkeit der Teile erzielen. Dadurch werden die Produkte belastbarer und widerstandsfähiger und sind so länger haltbar. Bei speziellen Anwendungen, wie Wärmeaustauschern, dient das Gitter dazu, eine größere Oberfläche zu erzielen.
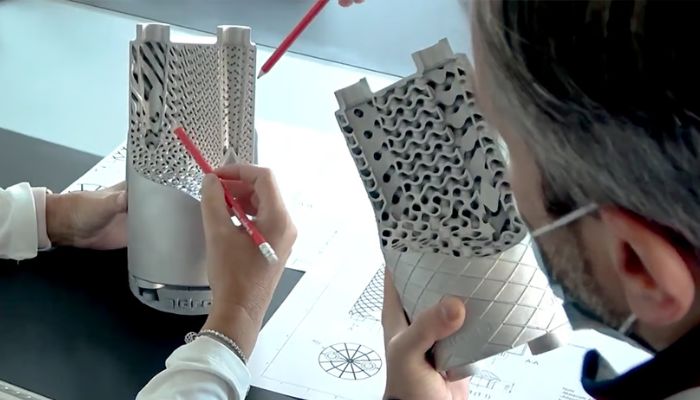
Toucan Beak, ein 3D-gedruckter Wärmetauscher mit Gitterstrukturen im Inneren. (Bild: Aidro)
Ein weiterer Punkt, der vor allem bei Konsumgütern zum Tragen kommt, ist die Personalisierung. In Schuhen, Sitzen, Rucksäcken etc. kann der Härtegrad des Gitters angepasst werden und zum besseren Komfort beitragen. Außerdem spielt auch die Ästhetik der Gitter eine immer größere Rolle bei Design-Anwendungen. Zum Abschluss sei noch die Osseointegration genannt. Es gibt beispielsweise Gitterstrukturen, die dem natürlichen Muster in Knochen nachempfunden sind. Werden diese Gitter in medizinischen Implantaten verwendet, können sie das Knochenwachstum anregen.
Anwendungen von 3D-gedruckten Gitterstrukturen
Somit kommen wir zu einigen Anwendungsfeldern, in denen 3D-gedruckte Gitterstrukturen ihr Potential geltend machen. In der Medizin werden lattices wie erwähnt für Implantate verwendet, aber auch für Prothesen und Orthesen, um das Gewicht, die Festigkeit oder den Komfort zu beeinflussen. Gitterstrukturen sind darüber hinaus vor allem in Anwendungen gewinnbringend, wo hohe Leistung und geringes Gewicht eine Rolle spielen, also in der Automobil-, Luft- und Raumfahrtindustrie. Mithilfe von Gitterstrukturen und der nTop “Shell & Lattice”-Funktion konnte Aerojet Rocketdyne etwa einen Vierfach-Triebwerkblock um 67 % leichter gestalten und um 66 % günstiger produzieren.
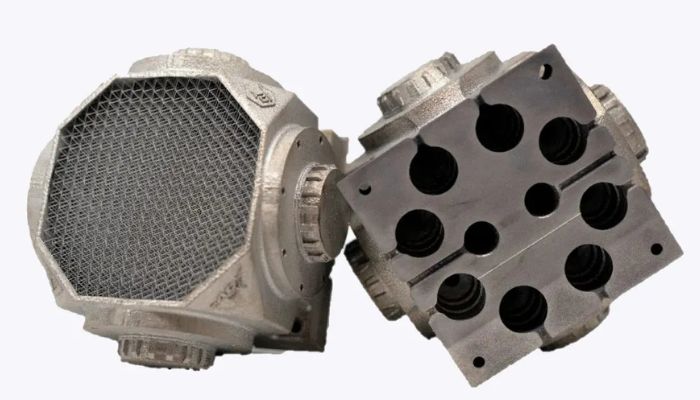
Triebwerkblock von Aeorojet Rocketdyne mit Gitterstrukturen zur Gewichtsreduktion (Bild: nToppology)
Aber auch im Sport und bei Konsumgütern werden lattice structures immer wichtiger und beliebter. So sehen wir zunehmend 3D-gedruckte Schutzausrüstung und Polsterungen in Gitter-Optik. Die Gitter kommen dann in Fahrradsätteln, Helmpolsterungen, Schutzbekleidung etc. zum Einsatz oder auch in Zwischensohlen für Schuhe. Insbesondere bei Laufschuhen wird sich davon eine bessere Energieübertragung und höhere Leistung erwartet. Dies ist auch bei Autositzen oder Rucksäcken der Fall. Der Outdoor-Spezialist Oechsler verwendete beispielsweise das Tool Magics von Materialise, um den Komfort seiner innovativen Rucksäcke durch Gitterstrukturen zu verbessern. Auch Möbel weisen immer häufiger Gitter auf, auch wenn dabei die Ästhetik dem Gewicht vorrangig sein dürfte.
Wie diese Beispiele belegen, finden wir Gitterstrukturen bereits in zahlreichen Anwendungen. Mit der fortschreitenden Industrialisierung des 3D-Drucks und beständig neuen Designmöglichkeiten dürfte sich dieser Trend in Zukunft fortsetzen und sogar verstärken.

Gitterstrukturen zur Schockabsorption und für besseren Komfort. (Bild: Oechsler)
Haben Sie bereits Erfahrungen im 3D-Druck von Gitterstrukturen? Lassen Sie uns gerne einen Kommentar da, oder teilen Sie es uns auf Facebook oder LinkedIN mit. Möchten Sie außerdem eine Zusammenfassung der wichtigsten Neuigkeiten im 3D-Druck und der additiven Fertigung direkt und bequem in Ihr Postfach erhalten? Dann registrieren Sie sich jetzt für unseren wöchentlichen Newsletter.
*Titelbildnachweis: Dassault Systèmes