Worum handelt es sich beim Future Tree der ETH Zürich?
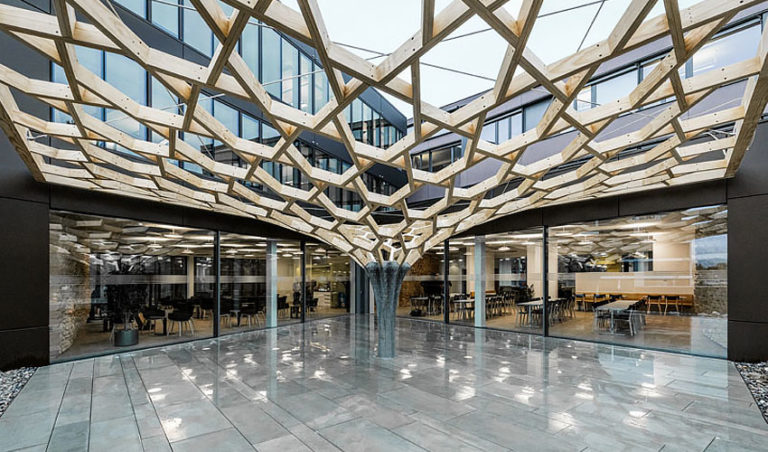
Die Verwendung von Beton im 3D-Druck verändert die Bauindustrie. Vom 3D-gedruckten Haus bis hin zu Krankenhauszusatzkapaziäten bietet die additive Fertigung eine sehr große Gestaltungsfreiheit. Dank der schnellen Produktionsgeschwindigkeit und den niedrigen Kosten könnte der 3D-Druck eine zentrale Rolle im Bauwesen der Zukunft darstellen. Um die Möglichkeiten der Fertigung mit Beton besser zu verstehen, stellen wir Ihnen einen neuen Anwendungsfall vor, die im Innenhof des Gebäudes von Basler & Hofmann, einer in der Schweiz ansässigen Beratungsfirma, errichtet wurde: der sogenannte „Future Tree“, eine gedruckte 3D-Baumstruktur, die als Vordach dient.
Diese neue Konstruktion wurde von der ETH Zürich entworfen, die unter anderem für deren Fast Complexity Technologie im Bereich des Bauwesens sich einen Namen gemacht hat. Diese konzentriert sich auf die Entwicklung von Software- und Roboterwerkzeugen für die Architektur und lädt viele Akteure der Branche dazu ein, die Möglichkeiten des Designs im digitalen Zeitalter zu erforschen. Als Teil von Future Tree wollte das Team fortschrittliche Designtechniken mit neuen Materialien und additiver Roboterfertigung kombinieren, und das alles in einem beeindruckenden Architekturprojekt. Wie war das Team in der Lage, eine so innovative und komplexe gedruckte 3D-Struktur zu bauen?
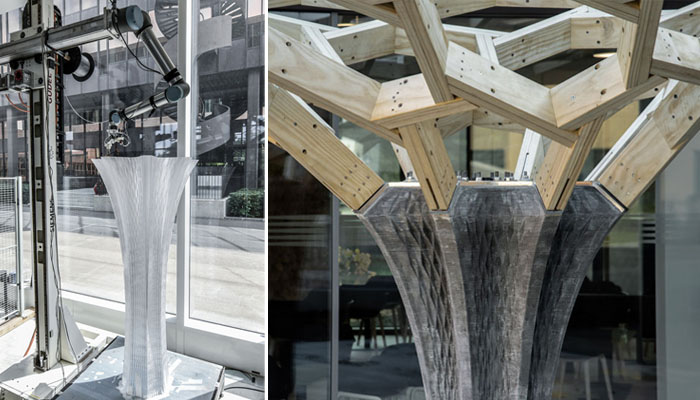
Bildnachweis: ETH Zürich
Die Entwicklung des Future Tree
Der Future Tree besteht aus zwei Elementen: das erste ist die Stützsäule, die die Struktur trägt und aus einer hauchdünnen 3D-gedruckten Schalung in Kombination mit schnell trocknendem Beton hergestellt wurde. Für die Schalung setzte das Team einen sechsachsigen Roboterarm ein. Dieser ist nur 1,5 mm dick und wurde in einem Stück gefertigt. Es wurde anschließend mit Beton befüllt. Was das Design der Säule selbst betrifft, so wurden die Fertigungsdaten aus einem parametrischen Designmodell generiert, was schnelle Iterationen von physischen Prototypen ermöglicht. Das Team verwendete die „Eierschalen“-Technik – mit der FDM-Technologie ermöglicht das Verfahren den Entwurf neuer Strukturen, die optimiert sind und den Abfall minimieren. Tatsächlich wird die dünne Schalung nach der Aushärtung des Betons entfernt und kann recycelt werden.
Das zweite Element ist der verzweigte, baumförmige Teil, dessen Form dem Werk den Namen „Future Tree“verschafft hat. Die Struktur besteht aus Kiefernholz, Schrauben und Spannseilen. Insgesamt besteht die Baumstruktur aus 380 robusten Elementen. Dieser Rahmen kann dank der spezifischen Anordnung der Teile vergrößert werden. Jedes Element hat eine einzigartige Geometrie, die entsprechend den Daten des digitalen Modells zugeschnitten ist. Er wird von der Betonsäule getragen und ist an zwei Seiten am Innenhof des Gebäudes verankert und in der gegenüberliegenden Ecke auskragend befestigt.
Eine der Herausforderungen, mit denen das Team während des Projekts konfrontiert war, war das Schrumpfen des Druckmaterials beim Abkühlen. Sie lösten das Problem jedoch, indem sie ein rautenförmiges Mikromuster auf die Schalung auftrugen. Dadurch wurde die Schrumpfspannung während des 3D-Druckprozesses reduziert und die Schalung ausgehärtet. Weitere Informationen über das Projekt finden Sie auf der offiziellen Website.
Was denken Sie über den Future Tree? Möchten Sie eine Zusammenfassung der wichtigsten Neuigkeiten im 3D-Druck und der Additiven Fertigung direkt und bequem in Ihr Postfach? Registrieren Sie sich jetzt für unseren wöchentlichen Newsletter und folgen Sie uns auf Facebook und Twitter um stets auf dem Laufenden zu bleiben! Außerdem sind wir auch auf LinkedIN und auf Youtube zu finden.