Fraunhofer IAPT optimiert den 3D-Druck für die automobile Serienanwendung
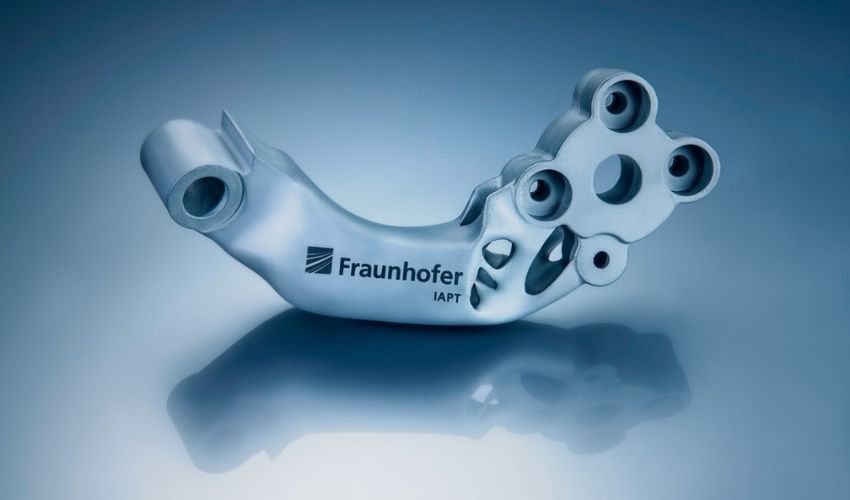
Die additive Fertigung ist heute in vielen Branchen fester Bestandteil des Produktionsprozesses. Vom schnellen und kostengünstigen Prototyping bis zur Herstellung von Endbauteilen, bietet der 3D–Druck Unternehmen ein flexibles Fertigungsverfahren mit zahlreichen Vorteilen. Zu diesen zählt beispielsweise die große geometrische Formfreiheit und die Eliminierung langer Transportwege. Damit Hersteller jedoch das volle Potenzial der Technologie ausschöpfen können, bedarf es der Identifizierung idealer Prozessparameter. Das Fraunhofer IAPT will mit einem »Design to Cost«-Ansatz den Türöffner für den 3D-Druck von automobilen Serienanwendungen gefunden haben.
Die Fraunhofer-Einrichtung für Additive Produktionstechnologien (Fraunhofer IAPT) klärte jüngst über die Bedeutung von Optimierungsmaßnahmen auf. Dank einer durchgängigen Optimierung der additiven Wertschöpfungskette sollen sowohl die technischen Eigenschaften als auch die Kosten des fertigen Bauteils beeinflussbar sein. Anhand einer Fallstudie hat das Institut die Einflussgrößen für die Bauteilkosten einer Türaufhängung für einen Sportwagen Schritt für Schritt ermittelt.
Optimierter Prozess ist Türöffner für Serienfertigung
In einem ersten Schritt haben die Experten das Bauteil mit dem Software-Tool von 3D Spark, einem Fraunhofer Spin-off, analysiert und bei der Festlegung des Designs die kostenoptimale Bauteilorientierung für den 3D-Druck ermittelt. Das Resultat wurde mit dem additiv gefertigten Bauteil ohne Optimierung verglichen. Das Resultat: eine Kosteneinsparung von 15 Prozent, welche aus der optimalen Nutzung des Bauraums und einer Reduzierung der Nachbearbeitung resultiert. Mit diesem Ergebnis wollte sich das Forscherteam aber nicht zufrieden geben. Also wurde der Gelenkarm mit Hilfe der Simulation des Kraftflusses in seiner Bauteilgeometrie optimiert und eine Grundgestalt gewählt, die das Gewicht um 35 Prozent reduziert, was den Materialbedarf und die Druckzeit um weitere 20 Prozent reduziert. Gemeinsam mit der Identifizierung des geeigneten Materials und des stützstrukturoptimierten Designs konnten weitere 20 Prozent in Vergleich zu 3D-gedruckten Gelenkarmen ohne Optimierung erreicht werden.
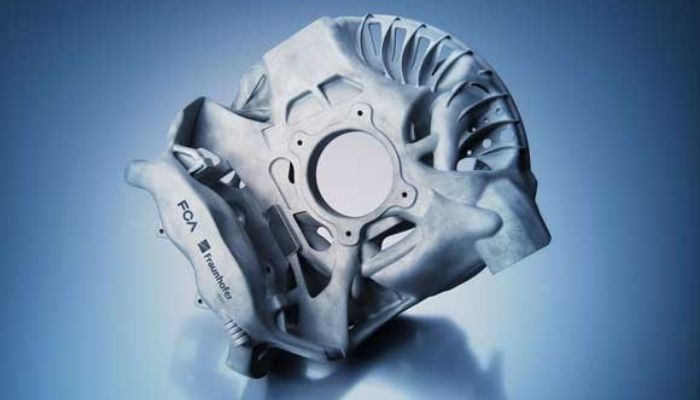
Das Fraunhofer IAPT nutzte den Ansatz außerdem zur Herstellung eines Bremssattel für Fiat Chrysler. (Bild: Fraunhofer IAPT / Fiat Chrysler)
Das Fraunhofer IAPT gibt an, dass weitere Kosten in der Anpassung der AF-Prozessparameter erzielt werden konnten. So soll der optimierte Gelenkarm um insgesamt 80 Prozent kostengünstiger in der Herstellung sein. Der Wert soll sich folgendermaßen aufteilen: Orientierungs- und Strukturoptimierung sowie die Supportreduzierung könnten die Kosten zu 45 Prozent, eine optimierte Materialauswahl, Speed-Parameter und Auslastungsmaximierung im AF-Prozess um weitere 35 Prozent reduzieren. Mit der Fallstudie will die Einrichtung demonstrieren, dass der Einsatz der additiven Fertigung bereits heute in großen Serien bis 5.000 Stück profitabel eingesetzt werden kann. Die Ergebnisse der systematischen Kostensenkung für den Gelenkarm sollen auf eine Vielzahl von Automobilkomponenten übertragbar sein.
Erkennen Sie weiteres Potenzial für den Ansatz des Fraunhofer IAPT? Teilen Sie uns Ihre Meinung mit und kontaktieren Sie uns. Möchten Sie eine Zusammenfassung der wichtigsten Neuigkeiten im 3D-Druck und der additiven Fertigung direkt und bequem in Ihr Postfach? Registrieren Sie sich jetzt für unseren wöchentlichen Newsletter und folgen Sie uns auf Facebook und Twitter, um stets auf dem Laufenden zu bleiben! Außerdem sind wir auch auf XING und LinkedIN zu finden.
*Titelbildnachweis: Fraunhofer IAPT