Formnext gibt Anwendungen und Potentialen von AM in der Raumfahrt eine Bühne

Wie jedes Jahr war auch die Formnext 2024 ein Abzugsbild davon, was die AM-Industrie derzeit bewegt und in welche Richtung die Trends der nahen Zukunft gehen werden. Lag der Fokus im letzten Jahr noch auf Automotive und Nachhaltigkeit, konnten wir dieses Jahr eine verstärkte Präsenz von 3D-Metalldruck-Technologien und Anwendungen aus der Raumfahrt feststellen. Dies zeigte sich einerseits direkt an den Ständen der Aussteller durch vorgestellte Use Cases und innovative 3D-Druck-Anlagen, andererseits auch im Rahmenprogramm, wo zahlreiche Konferenzen und Vorträge sich der Verarbeitung von Metall und der additiven Fertigung für die Raumfahrt widmeten. In einem vorherigen Beitrag haben wir die innovativen Metallanwendungen auf der Formnext bereits beleuchtet. Im Folgenden werden wir daher erörtern, warum AM in der Raumfahrt verstärkt eingesetzt wird, welche Herausforderungen nach wie vor bestehen und welche Lösungen dazu verhelfen, das Potential des 3D-Drucks in diesem Feld auszuschöpfen.
Die additive Fertigung wird in der Raumfahrt vorwiegend für Komponenten für Raumfahrtzeuge verwendet, darunter beispielsweise Teile für den Antrieb von Raketen, Verbrennnungskammern, Injektorenköpfe und Pumpsysteme. Ein weiteres wichtiges Anwendungsfeld liegt in der Herstellung von In-Space-Strukturen, das heißt von Elementen, die im Weltall und teilweise aus Weltraummaterial gefertigt werden. Beispiele hierfür sind Landebahnen und Baukonstruktionen aus Mars- oder Mondregolith.
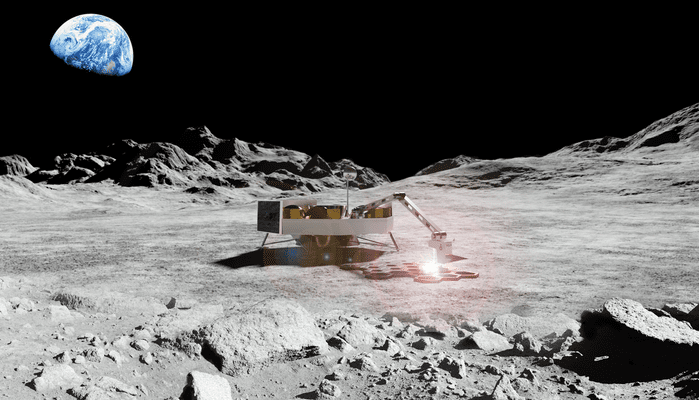
Bild: ICON
AM ermöglicht es, verschlungene, komplexe Designs zu erzielen und bei Raketenantrieben Kühlsysteme in einem Fertigungsschritt zu integrieren. In vielen Anwendungsbeispielen führen additiv gefertigte Teile zu einer erhöhten Leistung. Das liegt auch daran, dass zum Teil maßgeschneiderte Materialien mit spezifischen Eigenschaften verwendet werden, die den Bedürfnissen der Industrie gerecht werden. Die genannten Vorteile treffen nicht nur auf Komponenten zu, sondern auch auf In-Space-Strukturen. Die additive Fertigung ist flexibel und bedarfsgerecht, sorgt für eine hohe Präzision bei geringem bis mittlerem Energieverbrauch und wird für ihre Materialeffizienz geschätzt, wie wir im Vortrag von Mohammad Azami von Concordia Aerospace Robotics Lab lernen konnten. Trotzdem werden traditionelle Verfahren wie Gießen und Sintern von Regolithbeton nach wie vor aufgrund ihrer Schnelligkeit für die Fertigung von Bauteilen mit einfachen Geometrien herangezogen.
AM-Verfahren für die Raumfahrt und bestehende Herausforderungen
Bleiben wir jedoch bei der additiven Fertigung, stellen wir fest, dass vor allem LPBF verwendet wird und mehr und mehr auf DED gesetzt wird. The Exploration Company etwa konzentriert sich derzeit auf das Pulverbettschmelzen, zieht aber DED für 2025 in Betracht. Das deutsche Unternehmen ponticon stellt industrielle High-Speed DED-Systeme her und sein Dynamic Material Deposition-Verfahren wurde für die Verkleidung des Antriebs der Ariane 6 verwendet. Bei diesem Verfahren wird das Pulver geschmolzen, wenn es noch in der Luft ist, und auf diese Weise kann eine bemerkenswerte Präzision erreicht werden.
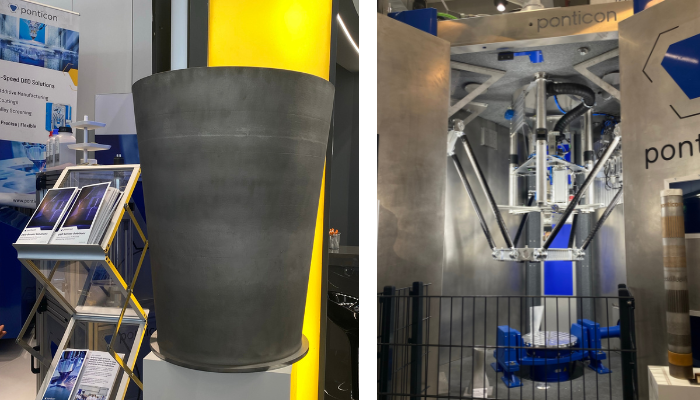
Am Stand von ponticon auf der Formnext. (Bild: 3Dnatives)
Das DED-Verfahren umgeht so ein Problem, das beim Pulverbettschmelzen im Raumfahrt-Sektor zu den größten Herausforderungen gehört, nämlich der Entpulverung komplexer Teile. Zwar können innere Kühlkanäle und anspruchsvolle Konstruktionen mittels AM umgesetzt werden, allerdings ist es schwierig, diese Kühlleitungen im Anschluss ordentlich zu reinigen. Bleibt Pulver in diesen Kanälen zurück, können die Flüssigkeiten nicht fließen, sodass die Gefahr besteht, dass das Triebwerk schmilzt oder zerstört wird. Auch die zunehmende Komplexität der Teile ist und bleibt eine Herausforderung. “Wir drucken 100 Kühlkanäle in ein Teil mit einer Wandstärke von 4 mm, das ist eine echte Herausforderung,” sagt Maximilian Strixner von The exploration Compnay, ein Unternehmen, das mit Nyx eine modulare und wiederverwendbare Raumkapsel entwickelt hat.
Für die additive Fertigung im Weltraum selbst sind die Rahmenbedingungen anders als für den Druck von Teilen auf der Erde und In-Space-Anwendungen stehen daher vor besonderen Anforderungen und Problemen. Auf dem Mond herrscht beispielsweise keine konstante Temperatur vor und die extremen Temperaturschwankungen erschweren die Herstellung von Teilen. Außerdem beeinträchtigen die Auswirkungen der geringen Schwerkraft die Produktion von Teilen und Baukonstruktionen.
Eine weitere Challenge, mit der sich Anwender der additiven Fertigung im Raumfahrt-Sektor konfrontiert sehen – egal, ob auf der Erde oder im All – sind die Kosten. Dies liegt vor allem an den hohen Materialkosten mit ihren spezifischen, erforderlichen Merkmalen. Tobias Stiggen von ponticon GmbH erklärte in seinem Vortrag, dass rund zwei Drittel der Gesamtkosten des gezeigten Beispiels – die Verkleidung des Ariane 6-Antriebs – auf das Material zurückzuführen sind. Die Kosten der Hardware, in diesem Fall ein Drucksystem von ponticon, fielen im Vergleich dazu relativ gering aus.
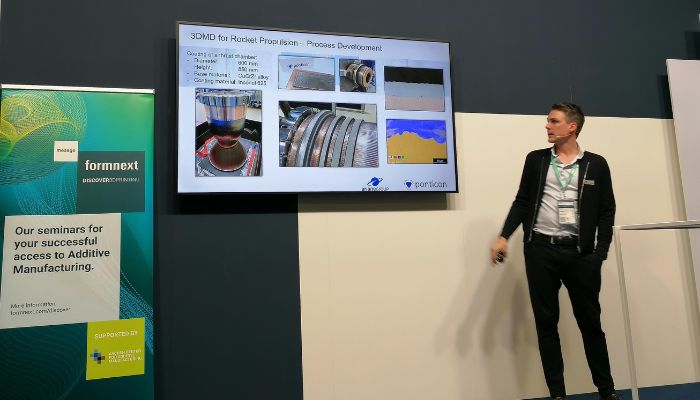
Tobias Stiggen erklärt die Vorteile der DED-Technologie für den Raketenantrieb. (Bild: 3Dnatives)
Ein weiterer Grund für die hohen Kosten ist, dass der Fokus der Luft- und Raumfahrt-Industrie auf leistungsstarken und leichten Teilen liegt. Konzentriert sich die Automobilbranche auf die Kostenoptimierung pro Teil, ist die Raumfahrt bestrebt, das Gewicht der Teile zu reduzieren. Bill Bihlman von SAE International merkte in seinem Vortrag zu “Material Qualification for Aerospace and Automotive AM Serialized Part Production” an, dass Teile für Luft- und Raumfahrt rund zehn mal mehr kosten, als Teile für die Automobilindustrie!
Leistungsstarke Materialvielfalt für Anwendungen in der Raumfahrt
Wenngleich der Preis eine wichtige Rolle spielt, steht die Leistung der eingesetzten Materialien und deren Beständigkeit an erster Stelle. So sehen wir diverse Metalle und Legierungen aber auch neu entwickelte Materialien und Verbundwerkstoffe in der Raumfahrt. The Exploration Company verwendet für seine Anwendungen etwa Kupferlegierungen wegen ihrer Wärmeleitfähigkeit und Legierungen auf Nickelbasis wegen ihrer mechanischen Festigkeit und chemischen Beständigkeit. SAE setzt ebenfalls auf Legierungen, aber auch auf Aluminium und für Kleinserienteile auf Titan.
Für die Fertigung im All kommen dort vorherrschende Materialien zum Einsatz oder Verbundwerkstoffe. Concordia Aerospace Robotics Lab etwa empfiehlt ein Kompositmaterial aus PEEK und Regolith. Dieses erfüllt die Anforderungen der NASA bezüglich der Abgasquote und weist eine hohe Strahlungs- und Chemikalienbeständigkeit auf. Durch die Einbindung von Regolith in PEEK konnten darüber hinaus die Kosten gesenkt werden, wie die Ergebnisse zeigen. Bei 50 % Gewichtsanteil Regolith in PEEK, entsprach die Kostenreduktion ebenfalls 50 %.
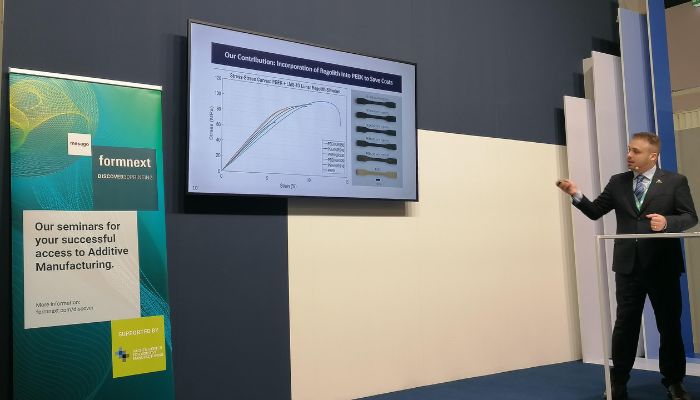
Mohammad Azami von Concordia Aerospace Robotics Lab (Bild: 3Dnatives)
In der gesamten AM-Branche war im letzten Jahr ein verstärkter Trend hin zum 3D-Druck mit Silikon festzustellen. Dieses Material hält auch Einzug in die Raumfahrt. In einem eigenen Beitrag auf der Formnext 2024, “Transforming Aerospace with silicone and soft composites 3D printing”, stand dieses Material im Mittelpunkt. Julien Barthes von 3DEUS DYNAMICS stellte dessen Pulververfahren mit Silikon vor und wie das Unternehmens während des Druckprozesses neue weiche Verbundwerkstoffe entwickelt. Der Vorteil dabei ist, dass herkömmliches Spritzguss-Silikon auch für den 3D-Druck verwendet werden kann und kein Abfall anfällt, da recyceltes Pulver wiederverwendet werden kann. Außerdem wied Barthes darauf hin, dass während des AM-Prozesses die Möglichkeit besteht, das Material zu wechseln, sodass ein einziges Teil mit zwei Texturen und maßgeschneiderten mechanischen Eigenschaften sowie komplexen Geometrien gefertigt werden kann. „Sie können während des Druckprozesses Pulver hinzufügen, das Material manipulieren und während des Prozesses Verbundwerkstoffe herstellen,“ fasste Barthes zusammen und erklärte, dass das Unternehmen auf diese Weise einen neuen flammhemmenden und weichen Verbundwerkstoff herstellte, der sich für Bauteile eignet, welche Feuer ausgesetzt sind, wie das in der Raumfahrt der Fall ist.
Ein Blick in die Zukunft
Mit dem umfangreichen Formnext-Aufgebot an Anwendungen und Fachbeiträgen zum Thema Aerospace steht unweigerlich fest, dass die additive Fertigung mehr und mehr in diesen Sektor einzieht. Auch wenn wir dieses Jahr einige bemerkenswerte Innovationen in der Raumfahrt beobachten durften – den Start von Ariane 6, das weltweit größte metallgedruckte Raketentriebwerk von Eplus3D und LEAP 71 und viele mehr – bleiben einige Herausforderungen bestehen, wie wir weiter oben gesehen haben. Dennoch birgt AM in der Raumfahrt ein beachtliches Potential, das noch nicht vollends ausgeschöpft ist. Neben Leichtbau, hochkomplexen Geometrien und leistungsstarken neuen Materialien, die Raketen schneller, effizienter und nachhaltiger machen, werden wir in naher Zukunft auch immer häufiger von 3D-Druck im Weltraum selbst lesen und hören.
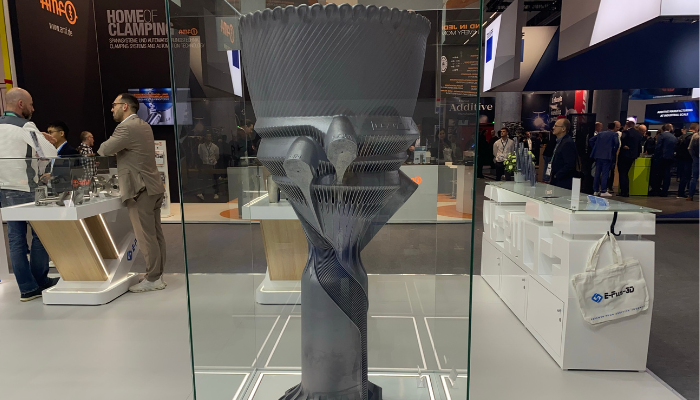
Im Rahmen der Formnext 2024. wurde das bisher weltweit größte metallgedruckte Raketentriebwerk von Eplus3D und LEAP 71 präsentiert. (Bild: 3Dnatives)
Was halten Sie vom verstärkten Einzug der additiven Fertigung in die Raumfahrt? Teilen Sie uns Ihre Meinung mit und kontaktieren Sie uns. Möchten Sie eine Zusammenfassung der wichtigsten Neuigkeiten im 3D-Druck und der additiven Fertigung direkt und bequem in Ihr Postfach? Registrieren Sie sich jetzt für unseren wöchentlichen Newsletter und folgen Sie uns auf Facebook, um stets auf dem Laufenden zu bleiben! Außerdem sind wir auch auf LinkedIN zu finden.
*Titelbildnachweis: Pixabay