Ford und Red Bull Powertrains optimieren Fahrzeuge für die Formel 1 durch 3D-Druck
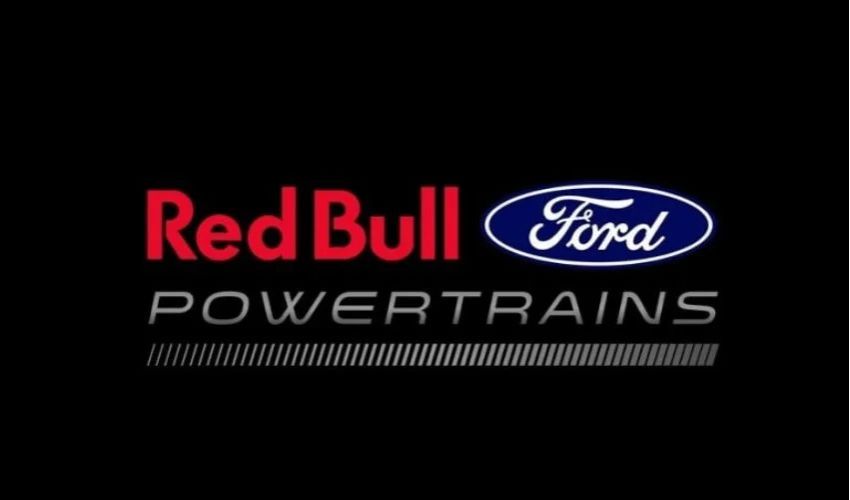
Im Jahr 2023 gab die Ford Motor Company bekannt, dass sie eine Partnerschaft mit Red Bull Powertrains eingegangen ist, um in die Formel 1 zurückzukehren. Tatsächlich war es zum damaligen Zeitpunkt mehr als 20 Jahre her, dass die Automarke auf Rennstrecken gefahren ist. Doch woraus besteht nun die Zusammenarbeit zwischen Ford und Red Bull? Der Zusammenschluss zwischen Ford und Red Bull Powertrains zielt auf die Entwicklung der nächsten Generation von Hybridantrieben für die Teams Oracle Red Bull Racing und Scuderia AlphaTauri ab. Auf diese Weise werden die Autos des Red Bull Racing-Teams die vom Internationalen Automobilverband FIA für die Formel 1 auferlegten Standards erfüllen, die 2026 in Kraft treten werden. Diese verlangen unter anderem, dass die Autos aerodynamischer werden und kohlenstoffneutrale Kraftstoffe verwenden. Damit die Fahrzeuge diese Normen erfüllen können, hat sich die Ford Motor Company auch für den Einsatz additiver Fertigungstechnologien entschieden.
Seit zwei Jahren setzt Ford 3D-Drucktechnologien ein, um seine Rennwagen zu verbessern und sie an die neuen FIA-Normen anzupassen. Bisher hat das Unternehmen bereits mehr als 1.000 3D-gedruckte Komponenten für Red Bull Powertrains hergestellt. Derzeit arbeitet Red Bull Powertrains, das Unternehmen, das die Red Bull-eigenen Antriebsstränge herstellt, mit Honda zusammen, aber von 2026 bis 2030 wird Ford der neue offizielle Partner sein. Die beiden Unternehmen arbeiten bereits gemeinsam an der Verbesserung von Rennwagen für die Formel 1. Das Ziel, das eine echte Herausforderung darstellt, besteht darin, die Antriebseinheit der Fahrzeuge des Red Bull Racing-Teams von Grund auf neu zu entwickeln und dabei das Beste aus der kurzen verfügbaren Zeit zu machen.
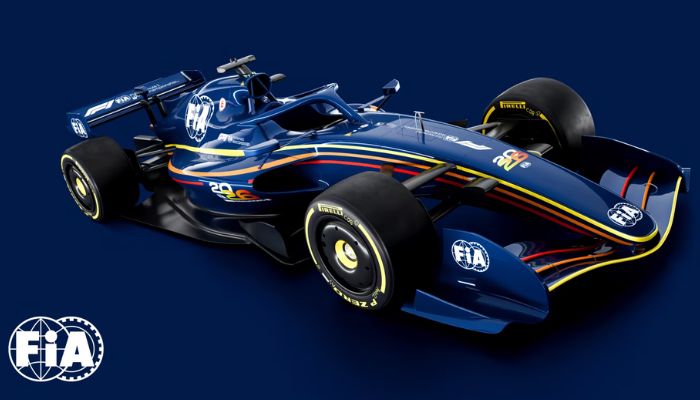
2024 präsentierte die FIA sowohl das neue Technische Reglement 2026 als auch die ersten Bilder, wie die neue Generation von F1-Autos aussehen soll. (Bild: FIA)
Die neuen Standards der FIA für die Formel 1
Um den Rennsport nachhaltiger zu machen und den Anforderungen der Moderne gerecht zu werden, wurden sehr hohe Standards festgelegt, die jeder Rennwagenhersteller bis 2026 erreichen muss. Die Autos müssen insgesamt und im Vergleich zu den aktuellen Abmessungen 30 kg leichter, 20 cm kürzer und 10 cm schmäler sein. Um das Überholen zu erleichtern, muss jedes Auto außerdem mit einem doppelten System aktiver Aerodynamik ausgestattet sein, sowohl hinten als auch vorne, das das derzeitige System zur Verringerung des Luftwiderstands (Drs) ersetzen wird. Auch die verwendeten Kraftstoffe müssen nachhaltig sein, und die Antriebseinheit des Autos muss halb hybrid und halb endotherm sein. Zusammenfassend lässt sich sagen, dass die Formel 1 den Millionen von Zuschauern nicht nur spannendere Rennen bieten will (die erhöhten Anforderungen an die Aerodynamik begünstigen Überholmanöver auch auf Stadtkursen wie in Monaco und Baku), sondern auch umweltfreundlichere Rennen. Um die hohen Anforderungen der FIA für die Formel 1 zu erfüllen, arbeiten Ford und Red Bull Powertrains zusammen und setzen fortschrittliche Technologien wie additive Fertigung, Oracle Cloud Computing und die industrielle Software-Suite Xcelerator von Siemens ein, um die Prozesse zu optimieren.
Röntgen- und CT-Scanner für die Prüfung von Hochleistungskomponenten
Um die Rennwagen von Red Bull Racing zu verbessern, hat Ford bereits mehr als 1.000 3D-gedruckte Komponenten hergestellt, welche die Antriebseinheit der Rennwagen effizienter machen sollen und die neuen Vorschriften erfüllen. Ford hat Hochleistungskomponenten hergestellt, bei denen sowohl Materialien wie Metall als auch Polymere verwendet werden, die besonders extremen Umgebungen standhalten müssen, in diesem Fall Geschwindigkeiten von über 300 km/h und folglich großer Hitze. Diese Teile müssen daher auf mechanische Festigkeit, Härte und geometrische Konformität geprüft werden. Ford hat für Redbull Powertrains Komponenten wie Batteriekühlplatten und Kühlplatten für andere Systeme hergestellt, die mit Röntgenstrahlen und Computertomographie (CT) untersucht wurden.
Es handelt sich dabei um sehr nützliche Instrumente für die analytische Bewertung der inneren Struktur von Bauteilen dank der Erstellung digitaler Modelle der Teile, die auf der Grundlage der aus den Scans gewonnenen Daten erstellt werden. Die CT-Scans ermöglichen es, sowohl das Vorhandensein von Hohlräumen innerhalb des Formteils als auch Bereiche mit Delaminierung zu erkennen, ein Phänomen, bei dem sich die durch den Druck erzeugten Schichten voneinander trennen. Die durch diese Scans gewonnenen Daten ermöglichen es also, eventuelle Probleme, die bei den verschiedenen mechanischen Prüfungen der Teile auftreten können, effizienter zu behandeln und somit die Produktion zu optimieren und zu beschleunigen. Die additive Fertigung in Verbindung mit fortschrittlichen 3D-Prüfverfahren ermöglicht also die Herstellung von leistungsfähigen und sicheren Teilen. Ford setzt jedoch nicht nur das Scannen ein, um 3D-gedruckte Teile zu prüfen: Alle gefertigten Teile werden im Metrologielabor des Unternehmens zusätzlichen Tests unterzogen.
Ford und der Einsatz von 3D-Druck über die Formel 1 hinaus
Ford nutzt den 3D-Druck nicht nur zur Herstellung von Komponenten für die Rennfahrzeuge, die in der Formel 1 antreten werden, sondern setzt die Technologie schon seit Jahren für verschiedene Zwecke ein. Im Jahr 2023 eröffnete das Unternehmen das Cologne Electrification Center in Deutschland, ein Zentrum, das auf den Einsatz von 3D-Druck spezialisiert ist, um die Produktion der ersten Serie von 100 % elektrischen Fahrzeugen in Europa zu unterstützen. Zwölf Hightech-3D-Drucker werden im Cologne Electrification Center eingesetzt, um eine Vielzahl von Polymer- und Metallteilen zu produzieren. Diese Teile können von wenigen Zentimetern Länge und einem Gewicht von nur 30 Gramm bis hin zu 2,4 Metern Länge und 15 Kilogramm Gewicht reichen.
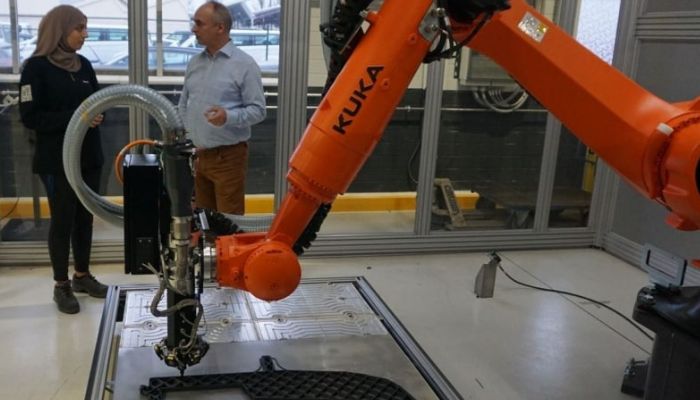
Foto aus dem Cologne Electrification Center, dem Ford-Werk in Deutschland. (Bild: Ford Media Center)
Aber Ford ist sicherlich kein Neuling auf dem Gebiet der technologischen Experimente. Am deutschen Sitz des Unternehmens wird bereits seit den 1990er Jahren mit dem 3D-Druck gearbeitet. Damals begannen die Ingenieure im Entwicklungszentrum in Merkenich, Teile für Testfahrzeuge und Prototypen in 3D zu drucken. Doch damit nicht genug: 2019 wurde im Ford Forschungs- und Innovationszentrum in Michigan das größte jemals im 3D-Druck hergestellte Metallteil produziert. Das Team reproduzierte einen Aluminium-Ansaugkrümmer für den Motor eines Ford F-150. Im Ford-Werk Valencia in Spanien wurde dagegen ein Katalog mit 5.000 3D-druckbaren Teilen erstellt, um innovative Lösungen für die verschiedenen Stufen des Produktionsprozesses im Werk anzubieten. Allein im Jahr 2021 sollen insgesamt 20.000 gedruckte Teile entstehen. Schließlich setzt Ford den 3D-Druck zur Automatisierung von Produktionsprozessen ein.
Wir müssen uns also nur bis 2026 gedulden, um die aus der Zusammenarbeit zwischen Red Bull Powertrains und Ford hervorgegangenen Autos auf den Formel-1-Strecken fahren zu sehen. Es ist wahrscheinlich, dass Ford im Laufe der Monate weitere 3D-gedruckte Komponenten entwickeln und einführen wird, um die Rennleistung der Rennwagen des nächsten Jahres zu verbessern. Sicher ist, dass Ford in der Zwischenzeit weiter in die additive Fertigung investieren wird, nicht nur, um Hochleistungskomponenten zu entwickeln, sondern auch, um die Automobilindustrie im Allgemeinen effizienter zu machen – dank seiner fast hundertjährigen Erfahrung und seiner Fähigkeit, sich die neuesten Technologien zunutze zu machen.
Was halten Sie von der Zusammenarbeit zwischen Ford und Red Bull Powertrains? Lassen Sie uns dazu einen Kommentar da, oder teilen Sie es uns auf Facebook oder LinkedIN mit. Wenn Sie mehr zum 3D-Druck in der Automobilbranche lesen möchten, schauen Sie auf unserer Landing Page vorbei. Möchten Sie außerdem eine Zusammenfassung der wichtigsten Neuigkeiten im 3D-Druck und der additiven Fertigung direkt und bequem in Ihr Postfach erhalten? Dann registrieren Sie sich jetzt für unseren wöchentlichen Newsletter.
*Titelbildnachweis: Ford Media Center