Ford setzt auf Formlabs und produziert Explorer mittels SLA- und SLS-3D-Drucktechnologie
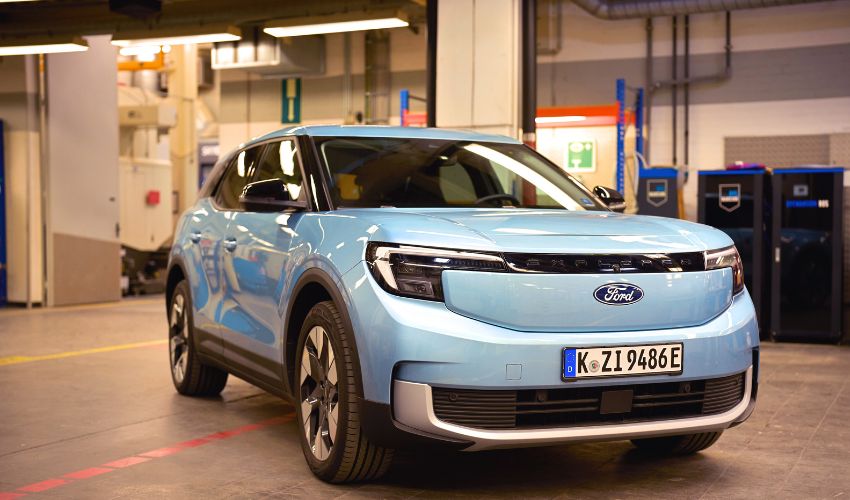
Ford, der sechstgrößte Automobilhersteller der Welt, hat sich ein ehrgeiziges Ziel gesetzt: Bis 2030 will das Unternehmen in Europa ausschließlich Elektrofahrzeuge verkaufen und damit die Automobilbranche nachhaltiger gestalten. Ein Beispiel für diesen Wandel ist der Ford Explorer, dessen Prototypen mit SLS– und SLA-3D-Druckern von Formlabs hergestellt wurden. Formlabs bietet hochmoderne 3D-Drucklösungen wie die SLA-Drucker Form 3+, Form 3B+, Form 3L und den Fuse 1+ SLS-Drucker. Diese Technologien sind ideal für Profis in Ingenieurwesen, Design und Fertigung. Auch Ford setzt bei der Produktion des Explorers auf den Form 4 und den Form 3L, die es ermöglichen, unterschiedliche Druckverfahren und Materialien zu nutzen, um Prototypen von Spiegeln, Griffen, Ladeanschlüssen und Teilen des Armaturenbretts zu fertigen. Formlabs und Ford gewährten einen Einblick in den 3D-Druckprozess zur Fertigstellung des Electric Explorer-Designs als Betatester des Formlabs Form 4 Druckers.
Das PD Merkenich Entwicklungszentrum ist für das Design von Fords Pkw-Modellen wie Fiesta, Focus und Kuga verantwortlich. Hier findet auch das Prototyping statt, das für die Ingenieure entscheidend ist, um Entwürfe zu überprüfen und Produktionsausfälle zu vermeiden, betont Sandro Prioddi, Leiter des Rapid Technology Centers bei Ford.
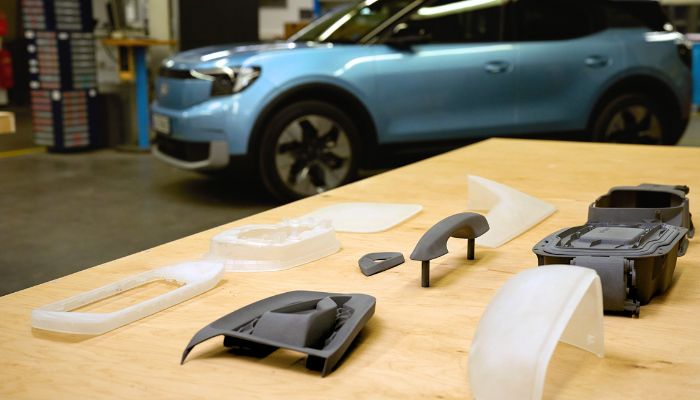
Die 3D-gedruckten Bauteile. (Bild: Ford/Formlabs)
Im Rapid Technology Center von Ford werden Prototypen in Originalgröße hergestellt, was den Einsatz verschiedener Maschinen erfordert. Aus diesem Grund verfügt das Zentrum über Spritzgussmaschinen, Umformwerkzeuge, verschiedene subtraktive Werkzeuge und natürlich 3D-Drucker. Seit 1994, als es als erstes Ford-Werk mit einem SLA-Drucker ausgestattet wurde, hat Ford die Verwendung der additiven Fertigung stetig erweitert und benutzt werden FDM-, SLA-, SLS-Polymer- und 3D-Metalldruck. Der erste Formlabs-Drucker im Einsatz war der Form 2, später folgten Desktop-Drucker, der Form 3L im Großformat und schließlich der Form 4 MSLA-Drucker.
,,Die additive Fertigung ist für den Entwicklungsprozess sehr wichtig. Sie bietet die Möglichkeit, Teile sehr schnell und sehr effizient zu produzieren und die Kosten zu senken. Man hat auch die Möglichkeit, kurzfristig zu reagieren. Wenn man sich die Entwicklung in Richtung Elektrifizierung ansieht, werden die Entwicklungszeiten immer kürzer. Das bedeutet, dass die Zeit, die man für die Entwicklung von Teilen und die Überprüfung von Fahrzeugteilen hat, immer kürzer wird. Sie macht uns im Vergleich zu den Wettbewerbern viel wettbewerbsfähiger“, sagte Piroddi, Leiter des Rapid Technology Centers bei Ford.
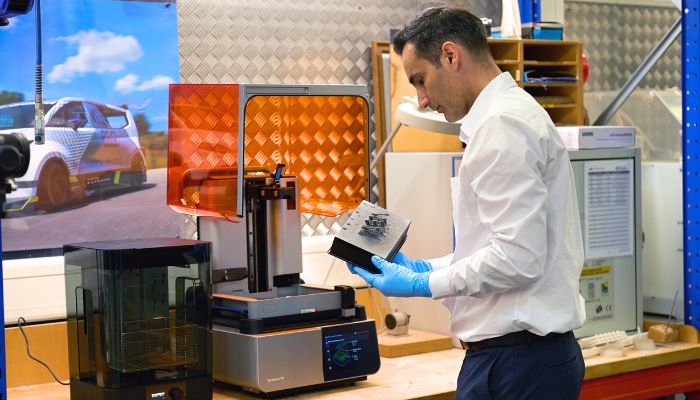
Die fertig 3D-gedruckten Teile für den Explorer werden dem Form 4 entnommen. (Bild: Ford/Formlabs)
Der Form 4 überzeugte Ford, als Betatesters, insbesondere durch seine Geschwindigkeit. Prototypen können schneller hergestellt und geliefert werden, sodass mehr Anfragen in weniger als einem Tag bearbeitet werden können. Prioddi beschreibt die Arbeit mit dem Form 4 als Wendepunkt und auch Bruno Alves, Additive Manufacturing Expert und Tooling Specialist bei Ford fügt hinzu: „Der Form 4 ist sehr schnell, ich denke, es ist die beste Maschine, die ich bis jetzt gesehen habe, was die Geschwindigkeit angeht. Es ist wirklich ein sehr gutes Upgrade im Vergleich zu den Vorgängermodellen. Sie ist einfacher zu bedienen, so dass es für die Bediener in unserer Werkstatt viel einfacher ist, die Arbeit mit der Maschine zu erlernen und Teile mit guter Qualität zu erhalten“.
Darüber hinaus wird auch SLA-Druck für Prototypenteile verwendet, die eine hohe Oberflächenqualität erfordern, und auch, um Design- und Innenteile des Explorers zu validieren. Der Form 3L-Drucker fertigt große Prototypen in einem Stück, wobei die Teile aus klarem Harz gedruckt und anschließend mit Fuse Blast gestrahlt werden. „Mit der Form 3L können wir große Teile drucken, beispielsweise Außenteile für die Karosserie des Fahrzeugs. Wir haben diese Spiegelkappe gedruckt, um ein Design zu validieren. Der 3D-Druck eignet sich für diese Anwendung, weil er schnell ist und wir im Vergleich zu Teilen aus der Massenproduktion eine sehr gute Qualität erzielen können“, so Alves.
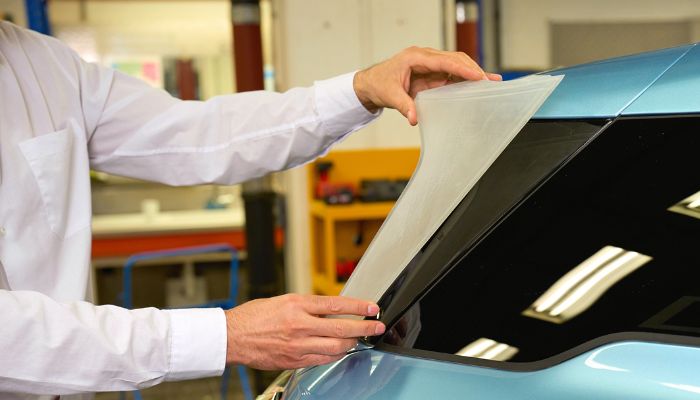
Die Form 3L druckte große Prototypen, wie z. B. äußere Merkmale aus klarem Harz. (Bild: Ford/Formlabs)
Der Fuse 1+ wird laut Alves bevorzugt, da er schneller ist als die Konkurrenz und einfach zu bedienen. „Wir versuchen immer, Materialien zu testen und zu validieren, die den in der Massenproduktion verwendeten Materialien ähnlicher sind. Der Fuse 1+ verwendet das Material PA12, das den spritzgegossenen Teilen aus der Massenproduktion sehr ähnlich ist“, so Alves.
Zudem testete das Unternehmen die automatisierte Reinigungs- und Polierlösung Fuse Blast-SLS Workflow, die die Nachbearbeitung deutlich vereinfacht. „Das Blast-System beschleunigt unseren Prozess enorm, weil der Bediener die Teile jetzt nicht mehr manuell reinigen muss. Er legt sie einfach in die Box und startet die Maschine. Früher haben sie das manuell gemacht, und das war sehr zeitaufwändig. In dieser Zeit können die Bediener nun andere Dinge tun, und wir beschleunigen den Prozess“, erklärt Alves.
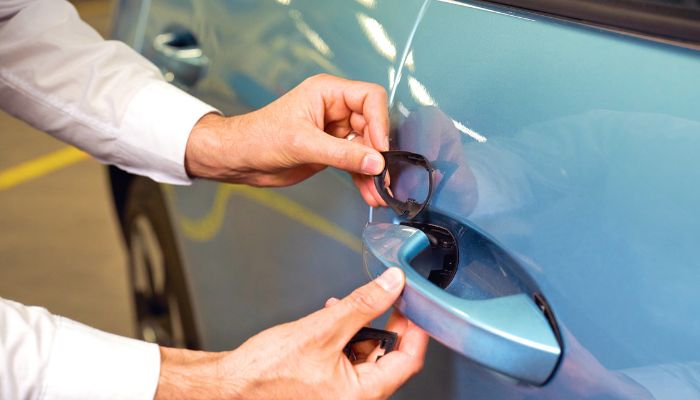
Jeder Türgriff verfügt über zwei Gummikomponenten zur Dämpfung und Isolation. (Bild: Ford/Formlabs)
Der Ladeanschluss wurde hingegen mit dem Fuse 1 + 300 W hergestellt. „Für diese Ladeabdeckung war es wichtig, SLS zu verwenden, da wir ein funktionales Teil benötigten, mit dem wir die Mechanismen testen konnten. Es handelt sich um ein wirklich komplexes Design, das wir auf andere Weise nicht herstellen können. Wir können dieses Teil nicht fräsen. Wir können auch nicht im Spritzgussverfahren nur einige Muster herstellen. Der beste Weg ist also, ein Material zu drucken, das wir physisch testen können“, so Alves.
Darüber hinaus kombiniert Ford traditionelle Fertigungsmethoden mit 3D-gedruckten Werkzeugen, um je nach Anwendung die besten Verfahren auszuwählen und Materialeinsatz, Kosten, Effizienz und Geschwindigkeit zu optimieren. So wurden beispielsweise Gummikomponenten für die Türgriffbaugruppe des Explorers mithilfe von 3D-gedruckten Formeinsätzen und Spritzgießmaschinen gefertigt. „Dies war ein komplexer Prozess, da wir mehrere Einsätze verwenden und es auch mehrere verschiedene Designs gibt, die jeweils mehrere Iterationen erfordern können. Normalerweise dauert das externe Spritzgießen vielleicht zwei oder drei Monate. Mit der internen additiven Fertigung können wir den Prozess auf zwei bis maximal drei Wochen verkürzen. Hätten wir für dieses Projekt externe Werkzeuge verwenden müssen, wäre es viel zeitaufwändiger gewesen und wir hätten die Teile nicht rechtzeitig liefern können“, erklärt Alves.
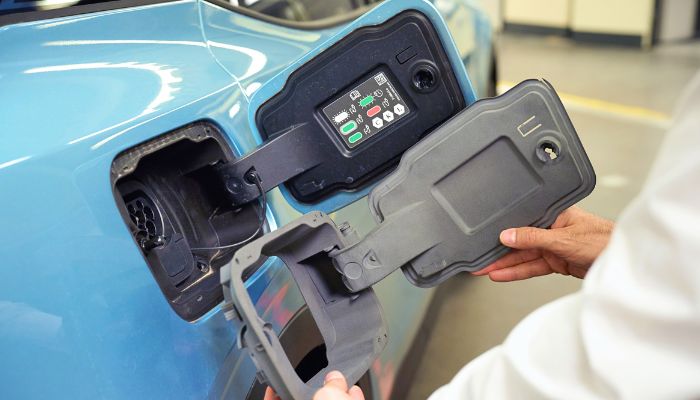
Der Ladeanschluss ist eine komplexe Baugruppe, die mit einer anderen Methode unmöglich zu prototypisieren gewesen wäre. (Bild: Ford/Formlabs)
Ford plant, weiterhin neue Spritztechnologien und Prozesse zu erproben, darunter auch neue Materialien, Verfahren und Maschinen. Da die Wettbewerber den Entwicklungsprozess stetig beschleunigen, sieht Ford die Notwendigkeit, ebenfalls schneller zu produzieren. Die additive Fertigung spielt dabei eine entscheidende Rolle, um mit der Konkurrenz mithalten zu können und die Entwicklungszeiten zu verkürzen.
Mehr über das nachhaltige Ziel des Automobilherstellers erfahren Sie HIER und mehr über Formlabs und den Form 4 erfahren Sie HIER.
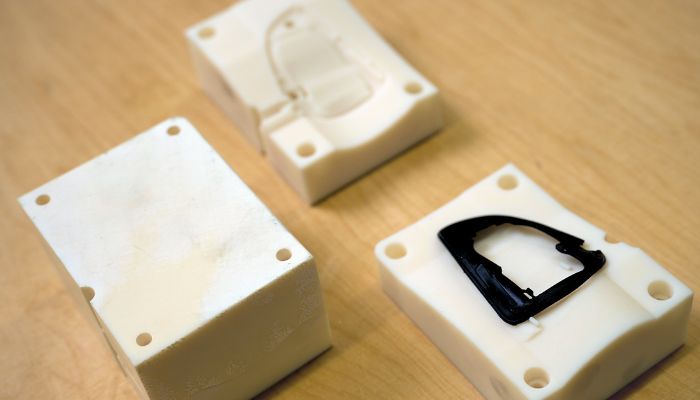
Das Team produzierte die Spritzgusseinsätze aus Rigid 10K-Harz auf SLA-Druckern und Nylon 12-Pulver auf SLS-Druckern. (Bild: Ford/Formlabs)
Was halten Sie von dem Ford Explorer? Lassen Sie uns einen Kommentar da, oder teilen Sie es uns auf Facebook oder LinkedIN mit. Möchten Sie außerdem eine Zusammenfassung der wichtigsten Neuigkeiten im 3D-Druck und der additiven Fertigung direkt und bequem in Ihr Postfach erhalten? Dann registrieren Sie sich jetzt für unseren wöchentlichen Newsletter.
*Alle Bildnachweise: Ford und Formlabs