Hochleistungspolymere ersetzen Metall in industriellen Anwendungen
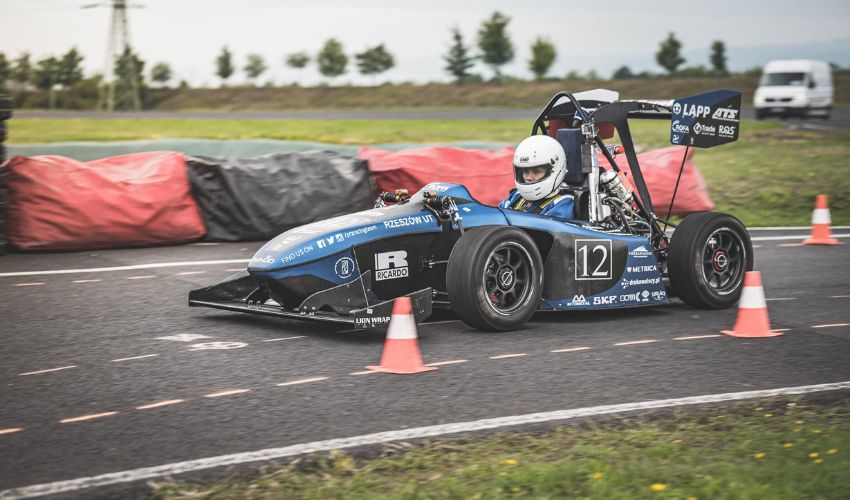
In der traditionellen Fertigung wird Metall u. a. für seine Festigkeit, Korrosionsbeständigkeit und Langlebigkeit geschätzt. Das wird sich zwar nicht so schnell ändern, aber die zunehmende Nutzung der additiven Fertigung mit Hochleistungspolymeren hat zu einer erstaunlichen Entwicklung geführt: der Möglichkeit, Metallteile durch Hochleistungspolymere zu ersetzen. Dies ist sogar in sicherheitskritischen Branchen wie der Luft- und Raumfahrt, der Automobilindustrie und dem Eisenbahnsektor möglich.
Doch welche Vorteile bietet der Austausch von Metallteilen gegen solche aus Hochleistungspolymeren? Und, was noch wichtiger ist, welche Werkzeuge sind erforderlich, um dies auch auf sichere Weise zu machen? Omni3D, bekannt für seine industrietauglichen 3D-Drucker, ist einer der Marktführer auf diesem Gebiet und arbeitet aktiv daran, zu zeigen, wie der Austausch von Metallen gegen Hochleistungspolymere in verschiedenen Bereichen möglich ist. Wir haben uns angeschaut, wie.
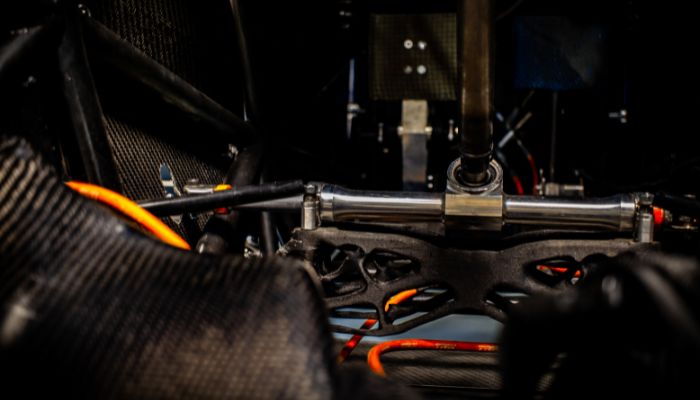
Ein Getriebeträger aus Polymer, hergestellt mit dem großformatigen 3D-Druck von Omni3D
Welche Vorteile hat die Verwendung von Hochleistungspolymeren gegenüber Metallen?
Zunächst ist es wichtig zu wissen, was genau Hochleistungspolymere sind. Diese Thermoplaste zeichnen sich durch unglaubliche Eigenschaften wie Korrosionsbeständigkeit, ein hervorragendes Verhältnis von Festigkeit zu Gewicht, Langlebigkeit, thermische Stabilität, Kriechfestigkeit und chemische Beständigkeit aus, die je nach Material variieren. Für die additive Fertigung werden vor allem PEEK, PEKK und ULTEM verwendet, die unterschiedliche Vorteile bieten.
Einer der wichtigsten ist die Möglichkeit, Gewicht zu sparen. Trotz der vielen Vorteile von Metallen ist nicht zu leugnen, dass sie schwer sind. Hochleistungspolymere sind leichter und bieten aufgrund ihrer Eigenschaften eine vergleichbare Leistung wie Metalle. Diese Gewichtsreduzierung ist für Branchen wie die Luft- und Raumfahrt, die Automobilindustrie und die Eisenbahn entscheidend. Denn eine Gewichtsreduzierung führt direkt zu einer verbesserten Kraftstoffeffizienz, einer höheren Nutzlast und einer geringeren Umweltbelastung.
Und nicht nur das: Durch die Kombination von Hochleistungspolymeren mit der additiven Fertigung werden die Vorteile noch größer. Das liegt daran, dass die additive Fertigung die Herstellung von geometrisch viel komplexeren Teilen als bei der traditionellen Fertigung ermöglicht und dazu beiträgt, sich von alten Beschränkungen zu befreien. Dies kann vor allem dazu genutzt werden, die Konstruktionen zu optimieren und noch leichtere Teile zu schaffen.
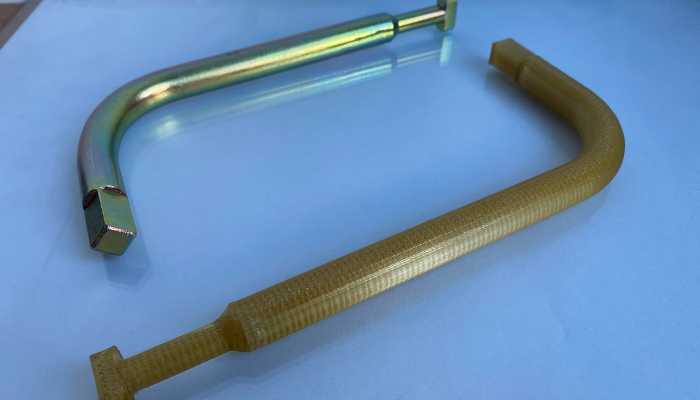
Ein Fahrzeug-Schachtschlüssel aus Metall (oben), den Omni3D durch eine Version aus Hochleistungspolymer ersetzt (unten)
Die additive Fertigung ist auch dafür bekannt, dass sie dank der Fähigkeit, Teile auf Abruf zu produzieren, die Lieferketten verbessern kann. Sie ist auch eine praktikable Alternative, wenn es um kaputte oder veraltete Komponenten geht, insbesondere solche aus Metall. Durch den Einsatz von Hochleistungspolymeren und der additiven Fertigung wird die Produktion erheblich beschleunigt und somit werden die Ausfallzeiten verringert.
Anforderungen an die Ausrüstung für Hochleistungspolymere
Es gibt jedoch einen Grund dafür, dass Hochleistungspolymere nicht für jedes einzelne per 3D-Druck hergestellte Teil verwendet werden können. Das liegt daran, dass nicht jede Lösung für die additive Fertigung geeignet ist. Um die Vorteile dieser Thermoplaste wirklich nutzen zu können und die Anforderungen der Großserienproduktion zu erfüllen, ist eine industrietaugliche Ausrüstung erforderlich.
Eine der wichtigsten Anforderungen ist natürlich die Materialkompatibilität. Wenn eine Maschine nicht über eine beheizte Kammer oder einen Extruder verfügt, der bestimmte Temperaturen erreichen kann, ist es unmöglich, mit Hochleistungspolymeren zu drucken. Eine präzise Temperaturregelung und eine gleichmäßige Erwärmung sind besonders wichtig für die Leistung.
Weitere ideale Eigenschaften sind ein größeres Bauvolumen für die Herstellung größerer und komplexerer Teile, fortschrittliche Steuersysteme und Präzisionsmechanismen und natürlich die Fähigkeit zum Dauerbetrieb mit minimalen Ausfallzeiten. Offene Materialsysteme sind auch deshalb zu bevorzugen, weil sie es den Anwendern ermöglichen, mit einer breiten Palette von Filamenten und Materialien zu experimentieren, was für die Optimierung der Teileeigenschaften und die Erforschung neuer Anwendungen von entscheidender Bedeutung ist.
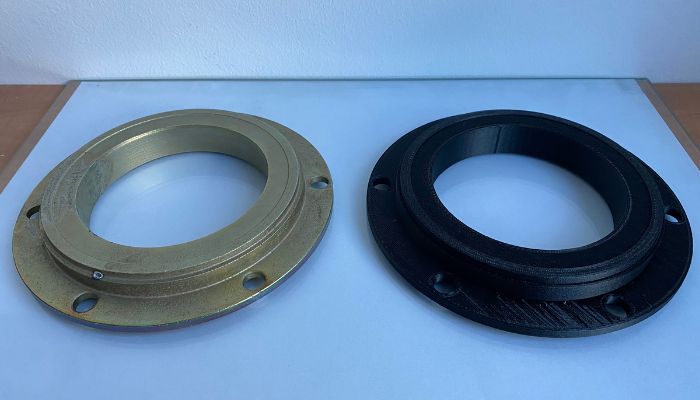
Ein Metallradlager (rechts) und die von Omni3D hergestellte Hochleistungspolymerversion für NATO-Fahrzeuge.
Ein gutes Beispiel für eine solche geeignete Ausrüstung kommt von Omni3D, einem führenden Unternehmen im industriellen 3D-Druck. Die Großformatdrucker des Unternehmens sind mit beheizten Kammern ausgestattet, die für eine präzise Temperaturregelung über das Bauvolumen sowie für eine gleichmäßige Erwärmung und die Vermeidung von kalten Stellen konzipiert wurden. Dies trägt dazu bei, dass das Material optimal kristallisiert und Verformungen und andere Defekte an den Teilen minimiert werden.
Diese Eigenschaften bedeuten, dass die Drucker in der Lage sind, die anspruchsvollen thermischen Anforderungen von Materialien wie PEEK, PEKK und ULTEM zu erfüllen. Darüber hinaus sorgt die geschlossene Regelung dafür, dass auch bei langen Druckaufträgen genaue Temperatureinstellungen beibehalten werden. Diese Eigenschaften sind ideal für den Druck mit Hochleistungspolymeren. Auch wenn es noch Probleme gibt, die überwunden werden müssen.
Wenn diese Faktoren zusammenkommen, können mit Hochleistungspolymeren einige unglaubliche Teile hergestellt werden. Ein Beispiel von Omni3D aus dem Verteidigungssektor: Der großformatige 3D-Druck mit Hochleistungspolymeren half der NATO bei der Wartung einer Flotte von BMP-1-Fahrzeugen. Diese Panzer sind für die NATO-Streitkräfte von zentraler Bedeutung, können jedoch eine erhebliche logistische Herausforderung darstellen, da die Beschaffung von Ersatzteilen für sie sowohl zeitaufwändig als auch teuer ist. Insbesondere lange Vorlaufzeiten können die Einsatzbereitschaft gefährden.
Omni3D konnte zeigen, dass die NATO hochfeste, funktionale Teile für die Panzer direkt vor Ort herstellen kann. Durch die Kombination mit einer digitalen Bibliothek von BMP-1-Komponenten konnten die NATO-Streitkräfte Verzögerungen in der Lieferkette umgehen und einen kontinuierlichen Fahrzeugbetrieb mit minimalen Ausfallzeiten gewährleisten. Insgesamt konnte die NATO durch den Einsatz der additiven Fertigung die Wartung der Flotte erheblich verbessern.
Ein weiteres Beispiel, bei dem Metallteile mithilfe der Lösungen von Omni3D durch Hochleistungspolymere ersetzt wurden, stammt von Luk-Plast. Hier hatte das Unternehmen ein Problem, bei dem die Rotoren der Vakuumpumpe aus Messing aufgrund der rauen Bedingungen, denen sie ausgesetzt waren, wie aggressive Chemikalien, Wasser und Gas, verschleißen. Dies führte in Verbindung mit dem Hochgeschwindigkeitsbetrieb und dem Dauerbetrieb, der eine zusätzliche mechanische Belastung mit sich brachte, zu häufigen Auswechslungen und längeren Ausfallzeiten. Dies führte zu Ineffizienzen in den Eisenbahnsystemen.
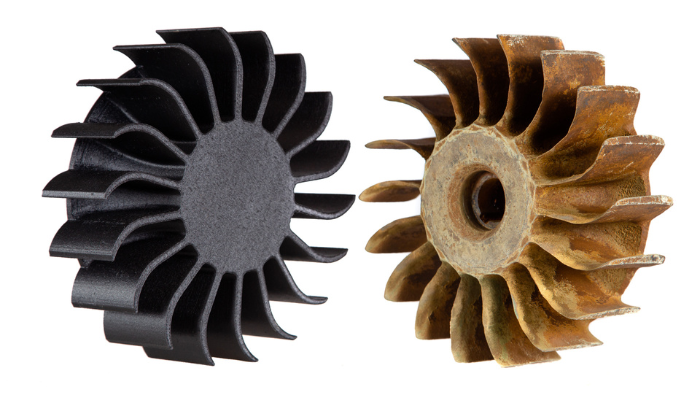
Die Rotoren der Vakuumpumpe aus Messing (rechts) und Hochleistungspolymer (links)
Auch hier war Omni3D in der Lage, das Problem mit Polymerteilen zu lösen. Genauer gesagt wurden der Omni Pro 3D-Drucker und CF PA-12 verwendet, um haltbare Teile zu erstellen, die diesen extremen Bedingungen standhalten konnten. Das Unternehmen wies darauf hin, dass das 3D-gedruckte Bauteil dank der präzisen Temperaturkontrolle in der beheizten Kammer seine Festigkeit und Stabilität auch bei aggressiven Chemikalien und hoher mechanischer Belastung beibehalten konnte. Am Ende hatte der 3D-gedruckte Rotor eine deutlich längere Lebensdauer, wodurch die Wartungsintervalle verkürzt und die Ausfallzeiten minimiert wurden.
In ähnlicher Weise konnte Omni3D im Automobilsektor einen Ansaugkrümmer, eine Getriebehalterung und eine Gelenkabdeckung aus Metall für das PRz Racing Team durch 3D-Druck, CF PA-12 und TPU-93A ersetzen. Die resultierenden Polymerteile waren leicht, haltbar und hitzebeständig. Der Einsatz der additiven Fertigung ermöglichte ein flexibles Design und eine schnelle, kostengünstige Produktion sowie leichtere Teile. Das Gewicht des Ansaugkrümmers wurde im Vergleich zum Aluminium-Pendant um 1,5 kg reduziert.
Diese und andere Beispiele zeigen, was durch den Einsatz von technischen und Hochleistungspolymeren als Metallersatz erreicht werden kann. Vor allem, wenn sie durch additive Fertigung hergestellt werden. Das bedeutet jedoch nicht, dass es keinen Raum für Verbesserungen gibt.
Was ist für die zukünftige Entwicklung erforderlich?
Es gibt noch einen weiteren Faktor, der bei der Arbeit mit Hochleistungspolymeren von entscheidender Bedeutung ist: die menschliche Komponente. Gegenwärtig verfügen Ingenieure und Techniker nicht immer über das notwendige Wissen, um AM für industrielle Anwendungen zu nutzen, insbesondere wenn es darum geht, Metallteile durch Hochleistungspolymere zu ersetzen. Dies ist ein weiterer Bereich, in dem führende Unternehmen der Branche wie Omni3D eine wichtige Rolle zu spielen haben.
Ingenieure, die mit Hochleistungspolymeren arbeiten, sollten in einer Vielzahl von Bereichen kompetent sein. Dazu gehören die Fähigkeit, Teileentwürfe auf ihre Druckbarkeit hin zu bewerten, 3D-Scannen und Reverse Engineering zu beherrschen, CAD-Entwürfe zu erstellen, die für die Fertigung optimiert sind, die am besten geeigneten Werkstoffe auf der Grundlage der Anforderungen des Teils und des verwendeten AM-Verfahrens auszuwählen, die Druckparameter zu optimieren und die erforderlichen Nachbearbeitungstechniken zu verstehen. All dies ist wichtig, um die Technologien wirklich nutzen und ihre Vorteile ausspielen zu können.
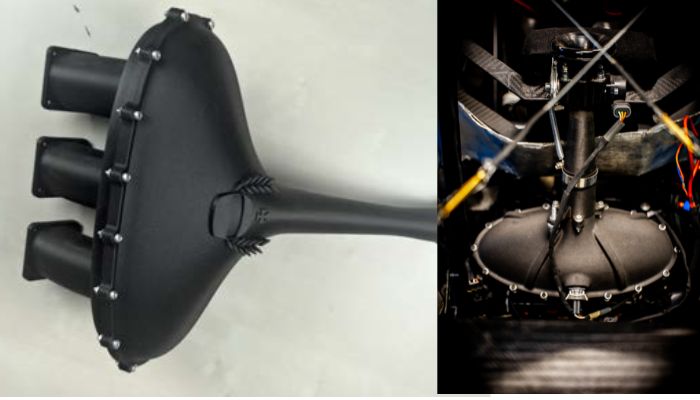
Ein Ansaugkrümmer, der für PRz Racing mit den Lösungen von Omni3D und CF PA-12 hergestellt wurde
Aber wie ist das möglich? Nun, eine Möglichkeit besteht darin, sicherzustellen, dass die Systeme offen sind. Omni3D zum Beispiel hat immer darauf hingewiesen, dass es wichtig ist, sie offen zu halten, um die Ausrüstung, die für den Ersatz von Metallteilen durch 3D-gedruckte Ersatzteile verwendet wird, zukunftssicher zu machen. Open-Source-Plattformen und -Software werden dazu beitragen, die Akzeptanz zu erhöhen, da technische Teams AM-Technologien in ihrem eigenen Tempo nutzen und testen können.
Ein weiterer Aspekt ist die stärkere Betonung von Bildung und Unterstützung. Beides hat Omni3D in den letzten Jahren fokussiert. Durch praktische Workshops, Online-Ressourcen für das Lernen im eigenen Tempo, technische Unterstützung bei Problemen und sogar anpassbare Schulungsprogramme hofft das Unternehmen, Organisationen in die Lage zu versetzen, das Potential von AM in der Industrie zu nutzen.
Dieser Schwerpunkt auf Ausbildung und Unterstützung ist einer der wichtigsten Faktoren, die dazu beitragen werden, den Wechsel von Metallen zu Hochleistungspolymeren auch für sicherheitskritische Teile voranzutreiben. In Verbindung mit den Werkstoffen selbst und der entsprechenden Ausrüstung wird es möglich, den Einsatz der additiven Fertigung zu maximieren und Innovationen voranzutreiben. Mehr darüber, wie Omni3D dies tut, erfahren Sie in dem kostenlosen Whitepaper, das Sie HIER herunterladen können.
Haben Sie bereits Erfahrung mit dem Ersetzen von Metall durch Hochleistungspolymere? Lassen Sie uns dazu einen Kommentar da, oder teilen Sie es uns auf Facebook oder LinkedIN mit. Möchten Sie außerdem eine Zusammenfassung der wichtigsten Neuigkeiten im 3D-Druck und der Additiven Fertigung direkt und bequem in Ihr Postfach erhalten? Dann registrieren Sie sich jetzt für unseren wöchentlichen Newsletter.
Viele Anwendungen werden nach der ersten Euphorie scheitern, weil der Dehnungskoeffizient von Kunststoffen bis zu 10 mal höher als Stahl ist!