EHLA-Verfahren von Fraunhofer ITL bietet eine nachhaltige Alternative zum Fräsen
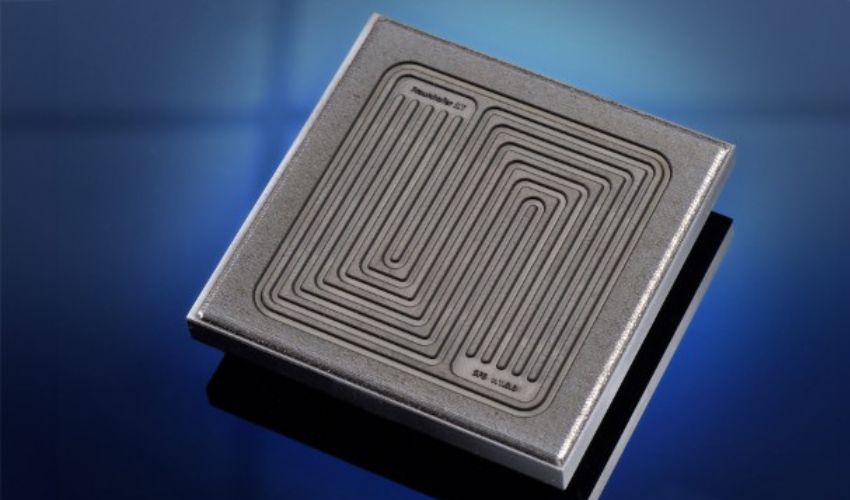
Um eingesetzte Umformwerkzeuge vor Verschleiß zu schützen, werden diese traditionell aus Metalllegierungen gefräst. Ein Prozess, der kostenintensiv und energieaufwendig ist. Das Fraunhofer ITL, das weltweit zu den bedeutendsten Auftragsforschungs- und Entwicklungsinstituten im Bereich der Laserentwicklung sowie Anwendung zählt, hat mit dem Extremen Hochgeschwindigkeits-Laserauftragschweißen (EHLA) eine nachhaltigere Lösung entwickelt, die verschleißfeste Schichten direkt auf das Baustahl aufträgt, um den Prozess des Fräsens zu vermeiden. Das im Luft-und Raumfahrt sowie Automobilbereich bereits erfolgreich getestete 3D-EHLA-Verfahren ist Teil des H2GO-Projekts, das im Mai 2022 startete und vom Bundesministerium für Digitales und Verkehr (BMDV) mit 80 Millionen Euro gefördert wurde. Ziel des Projekts ist es, kosteneffiziente Produktionsmethoden für Brennstoffzellen herzustellen, die den Schwerlastverkehr auf emissionsfreie Antriebe umstellen sollen. Dora Maischner, Projektleiterin am Fraunhofer ILT berichtet: „Wir verfolgen einen ganz neuen Ansatz. Bisher wurden Umformwerkzeuge für Bipolarplatten in stundenlangen Prozessen aus hochwertigem Werkzeugstahl gefräst. Wir bringen eine verschleißfeste Funktionsschicht endkonturnah auf kostengünstigen Werkstoff auf.”
Bei dem Verfahren, welches einen Ansatz für die Herstellung und Reparatur von Umformwerkzeugen für Bipolarplatten bietet, wird eine verschleißfeste Schicht von circa 1,2 mm mittels digitaler Steuerung präzise auf den Baustahl aufgetragen. Bereits im Laserstrahl, also bevor das Pulver auf das Bauteil trifft, wird dieses geschmolzen und somit flüssig auf dessen Oberfläche abgelagert. Dadurch kommt es zu einer geringeren thermischen Belastung des Materials. Der dreidimensionale Materialaufbau lässt sich darüber hinaus sehr exakt steuern, wodurch die verschleißfeste Schicht der beabsichtigten Endkontur sehr nahekommt. Statt einer stundenlangen Fräsung muss das Umformwerkzeug schlussendlich nur gezielt endbearbeitet werden. Viktor Glushych, Gruppenleiter für Beschichtung LMD und Wärmebehandlung am Fraunhofer ILT, erklärt: „Im EHLA-Prozess absorbiert nicht das Bauteil, sondern das Pulver einen Großteil der Laserenergie, ehe es auf das Werkstück trifft.“ Schichten aus dem Schnellarbeitsstahl 1.3343 oder Ferro55 können so eine Härte von bis zu 830 HV erreichen, und moderne EHLA-Anlagen bieten sogar Geschwindigkeiten von 30 Metern pro Minute, was den Auftragsprozess gegenüber herkömmlichen Laserauftragschweiß-Prozessen erheblich beschleunigt.
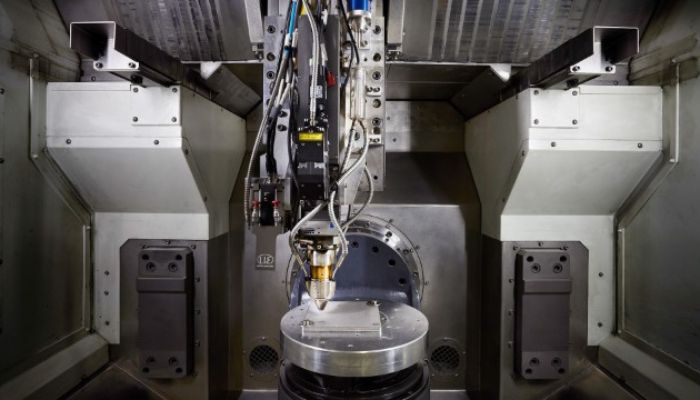
Das Fraunhofer ILT nutzt eine EHLA-Anlage, um Bauteile für Brennstoffzellen effizient und genau mit Verschleißschutzschichten zu versehen, und schafft damit die Grundlage für die Serienfertigung. (Bild: Fraunhofer ITL)
Aber nicht nur die Geschwindigkeit ist ein Vorteil des EHLA-Verfahrens. Dank der Reparatur von Werkzeugen werden Rohstoffe, Energie und Transportaufwand eingespart, da diese nicht eingeschmolzen, sondern einfach ausgebessert und erneuert werden können. Diese Wiederverwendung fördert die Kreislaufwirtschaft und trägt somit zur Nachhaltigkeit bei. Darüber hinaus gibt es auch im PKW-Bereich weitere Vorteile, denn die EHLA-Beschichtung senkt die Feinstaubbelastung, und bei Bremsscheiben konnten die dünnen EHLA-Schutzschichten den Abtrieb bereits deutlich verringern, was zur Reduktion von Feinstaub beiträgt. Mehr über den EHLA-Methode von Fraunhofer erfahren Sie HIER.
Was halten Sie von dem EHLA-Verfahren? Lassen Sie uns dazu gerne einen Kommentar da oder teilen Sie uns Ihre Meinung auf Facebook oder LinkedIN mit. Möchten Sie außerdem eine Zusammenfassung der wichtigsten Neuigkeiten im 3D-Druck und der additiven Fertigung direkt und bequem in Ihr Postfach erhalten? Dann registrieren Sie sich jetzt für unseren wöchentlichen Newsletter.
*Titelbildnachweis: Fraunhofer ITL, Titelbildunterschrift: Demonstrator zur EHLA-Technologie