Moderne Metall AM ermöglicht Mikroturbinen mit 40-fach höherer Effizienz
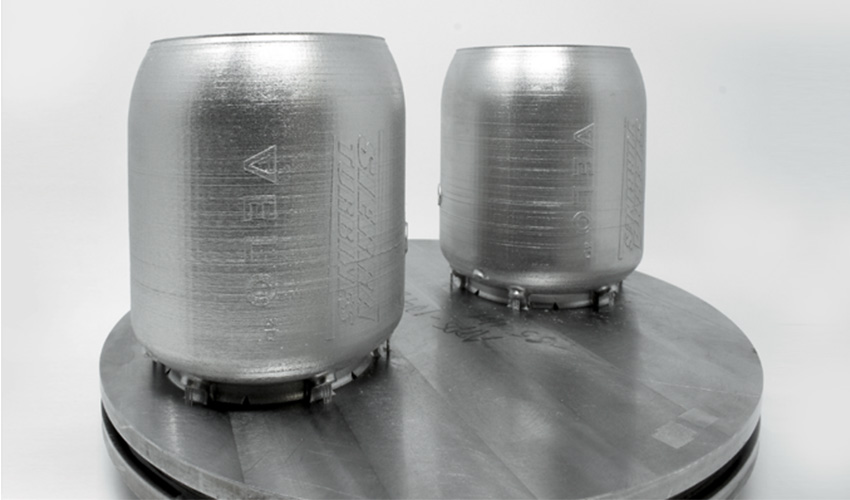
Eine Mikroturbine ist historisch gesehen eine vereinfachte Version einer Gasturbine, die für eine Vielzahl von Anwendungen geeignet ist: Sie werden in unbemannten Flugzeugen (UAVs) eingesetzt, um die Batterien zu laden und die Motoren anzutreiben als Range Extender oder in Hybrid-UAVs, die zwischen Batterien und Motoren wechseln. In den USA hat Sierra Turbines die Regeln der konventionellen Fertigung gebrochen, um die Leistung von Mikroturbinen zu verbessern. Roger Smith, Chief Executive Officer, erklärt, dass das Unternehmen plant, mindestens 95% seiner Komponenten für Mikroturbinen additiv zu fertigen, selbst wenn das Unternehmen die Großserienproduktion erreicht. Um dies zu erreichen, beschloss das Unternehmen, mit VELO3D zusammenzuarbeiten und sich dabei auf seine firmeneigene Technologie zur Herstellung von Metallzusätzen ohne Unterstützung zu verlassen. Ihr Ziel ist es, ihre Mikroturbinen 40x effizienter zu machen, indem sie eine 10x höhere Leistungsdichte bieten und das Gewicht im Vergleich zu herkömmlichen Mikroturbinen um 50% reduzieren.
Additive Fertigungstechnologien werden die traditionellen Herstellungsmethoden nicht ersetzen, aber sie können sicherlich die Leistung für Anwendungen steigern, bei denen das Design noch nicht optimiert wurde. Dies ist der Fall bei Mikroturbinen, wo Kostenbeschränkungen die Herstellung komplexer Merkmale, die die Leistung verbessern würden, schon immer verboten haben. Die Zeit zwischen den Überholungen (TBO) für die meisten kleinen Turbinentriebwerke beträgt durchschnittlich 40 bis 50 Stunden, aber Roger Smith beabsichtigt, diesen Wert auf über 1000 Stunden zu erhöhen, was dem von Verkehrsflugzeugen entspricht. Darüber hinaus plant er, das Gewicht der Triebwerke um die Hälfte zu reduzieren, den Lärm zu verringern und die Treibstoffeffizienz zu verbessern, während gleichzeitig die Turbinen einfacher herzustellen sind. Das sind ehrgeizige Ziele, gelinde gesagt!
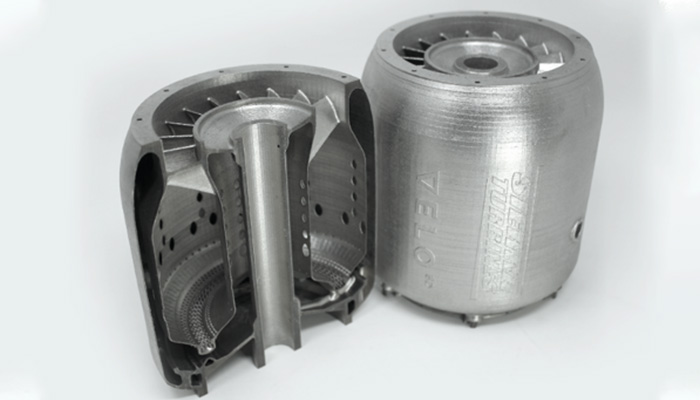
Querschnitt einer Brennkammer eines Sierra Turbines Triebwerks, der die Komplexität des Innenraums verdeutlicht. Beachten Sie die dünnen Luftfolien und das glatte Gitter, die der Brennkammer helfen, den Kraftstoff vor der Verbrennung effektiv zu versprühen. Bei der herkömmlichen Fertigung hätte dieses spezielle Teil die Montage von 61 einzelnen Komponenten erfordert, aber durch den 3D-Druck wurde es zu einer einheitlichen Geometrie mit feinen Details und Merkmalen konsolidiert, die mit keiner anderen Methode erreicht werden hätte können. Bildnachweis: VELO3D
Roger Smith erklärt, dass er zuversichtlich ist, dass sein Team dort Erfolg haben wird, wo andere gescheitert sind, dank einer Vielzahl von Konstruktionsverbesserungen, die nur mit Moderner Metall AM möglich sind. Hier kommt VELO3D ins Spiel. Heutzutage sind einige Designs mit pulverbasierten Metall-AM-Technologien ohne eine Stützstruktur nicht herstellbar, wodurch zusätzliche Nachbearbeitungsschritte zu ihrer Entfernung hinzugefügt werden, was die Kosten erhöht und die Designfreiheit einschränkt. Die Technologie von VELO3D ermöglicht die Herstellung komplexerer Komponenten, auch ohne Stützstruktur. Diese wird durch ihren dedizierten AM-Software-Flow vervollständigt.
Bei Sierras Mikroturbinen wurden die Brennkammer, das Herzstück der Aurelius-Mikroturbinen, speziell für die additive Fertigung entwickelt. Das Bauteil enthält Hunderte von kleinen Löchern, feine netzartige Gewebe, Dutzende von internen Kühlkanälen und eine Reihe von dünnen, überaus hohen Wänden. Der ursprüngliche Entwurf enthielt 61 einzelne Teile, die mit DfAM-Techniken zu einem einzigen zusammengefügt wurden. Es ist dieses hochentwickelte Design, das Smith verschiedenen Herstellern von Zusatzgeräten präsentierte, bevor er sich für VELO3D entschied. Er forderte sie auf, das Teil aus Hastelloy® X zu bauen, einem hochbeständigem, kriecharmen Metall, das es dem Motor ermöglichen würde, Temperaturen zu erreichen, die normalerweise in Mikroturbinen unerreichbar sind.
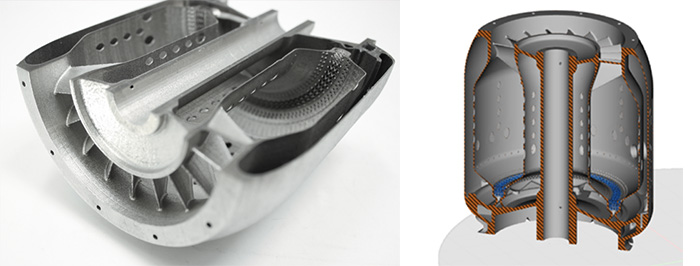
Querschnitte des gedruckten 3D-Triebwerkkerns zeigen feine Details. Links sehen sie das Objekt gedruckt und rechts als CAD-Modelll. Der blaue Teil im CAD-Modell definiert eine nahtlos ineinander übergehende Gittergeometrie, die mit der Optimierungssoftware von nTopology entworfen wurde und die die einzigartige Fähigkeit besitzt, die Gittergröße und -dicke räumlich zu variieren, um die Motorleistung und -performance zu maximieren. Bildnachweis: VELO3D und Sierra Turbines.
Über seine Zusammenarbeit mit VELO3D sagt Roger Smith: „Das Team von VELO3D hat mit uns am Design gearbeitet und die Dinge so optimiert, dass sie besser herstellbar sind, aber es war ihre Flow-Software, die vielleicht am meisten dazu beigetragen hat. Sie enthält eine Reihe spezieller Werkzeuge, die wertvolles Feedback während des gesamten Druckvorbereitungsprozesses liefern.“ Am Ende dauerte der 3D-Druck von 2 Brennkammern der Mikroturbinen etwa 50 Stunden – herkömmliche Herstellungsmethoden hätten Monate in Anspruch genommen.
Darüber hinaus konnte das Team von Sierra Turbines durch den Wegfall von Stützstrukturen an flachen Überhängen, auch den Bedarf an sekundärer Bearbeitung und anderen Nachbearbeitungsverfahren reduzieren, was ziemlich teuer sein kann. Schließlich dokumentiert die Qualitätssicherungssoftware des Systems, Assure, alle kritischen Sensordaten, die sich auf die Teilequalität auswirken, und erstellt einen umfassenden Baubericht zur Rückverfolgbarkeit. Ausgestattet mit Datenpunkten zu Vorsprüngen, Sauerstoffgehalt, Filterlebensdauer und Laserausrichtung ist Sierra Turbines zuversichtlich, dass das gebaute Teil dem Standard entsprach.
Roger Smith merkt an, dass er, sobald die Brennkammer gründlich getestet und einem Benchmarking unterzogen worden ist, weitere Leistungsverbesserungen anstrebt. Er fügt hinzu: „VELO3D ist davon überzeugt, dass Sie die additive Fertigung für die Serienproduktion einsetzen können, und das bin ich auch. Für die zukünftige Turbinenentwicklung wollen wir die Möglichkeiten der additiven Fertigung nutzen, um Funktionen wie einen effizienzsteigernden Rekuperator, aufgedruckte Sensoren und neuere Isolier- und Kühlgeometrien zu integrieren.“
Im Wesentlichen konnte die fortschrittliche Metall-AM-Technologie die Kosten senken und die Vorlaufzeiten verkürzen, indem sie es ermöglichte, Dutzende und Aberdutzende von Komponenten in einem einzigen gedruckten 3D-Stück zu konsolidieren. So entstand ein Teil mit geringerer Masse und größerer mechanischer Integrität als bei der geschweißten und montierten Alternative. Roger Smith geht davon aus, dass er auch alle anderen Ziele, die er sich gesetzt hat, in naher Zukunft erfüllen wird! Weitere Informationen finden Sie auf der offiziellen Website von VELO3D.
Möchten Sie eine Zusammenfassung der wichtigsten Neuigkeiten im 3D-Druck und der Additiven Fertigung direkt und bequem in Ihr Postfach? Registrieren Sie sich jetzt für unseren wöchentlichen Newsletter und folgen Sie uns auf Facebook und Twitter um stets auf dem Laufenden zu bleiben! Außerdem sind wir auch auf LinkedIN, Xing und auf Youtube zu finden.