Additive Fertigung von Metall verbessert mit E-2-Flüssigkeitsraketentriebwerk die wichtige Leistung von Raketentriebwerken
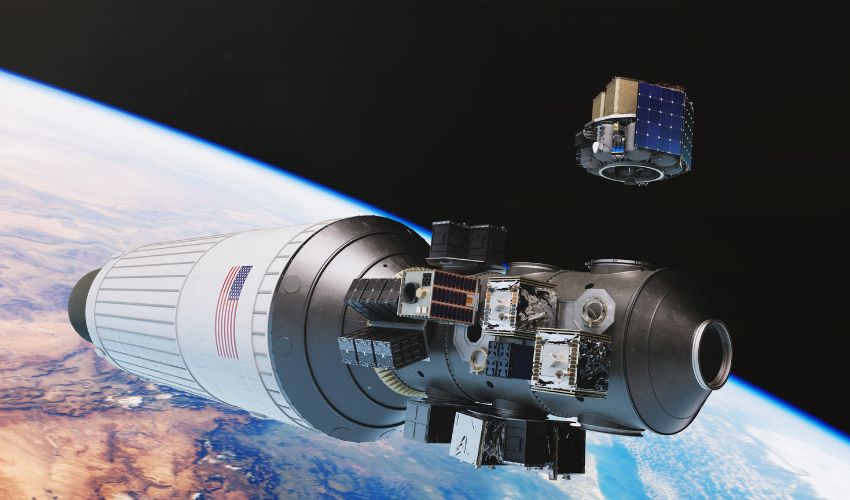
Es besteht kein Zweifel daran, dass Satelliten eine entscheidende Rolle in unserem Leben spielen. Sie liefern nicht nur Informationen über die Wolken, die Ozeane, das Land und die Luft auf der Erde (und ermöglichen so den Wissenschaftlern, Wetter und Klima vorherzusagen), sondern sind auch für die tägliche Kommunikation und vieles mehr unerlässlich. Aber wussten Sie, dass Satelliten immer kleiner werden? Heute sind Satelliten billiger zu produzieren, weil sie leichter sind als frühere Versionen, was zu geringeren Startkosten führt. Infolgedessen bemühen sich die Unternehmen auch um die Entwicklung kleinerer, kostengünstigerer Raketen, die sie tragen können. Eines der bemerkenswertesten Unternehmen auf dem Markt ist Launcher, die ein E-2-Flüssigkeitsraketentriebwerk hergestellt haben.
Das kalifornische Start-up-Unternehmen Launcher wurde 2017 gegründet, um die steigende Nachfrage nach Trägerraketen zu befriedigen, die das Angebot auf dem Markt für Satellitenstarts (der bis 2030 von 8 Mrd. USD auf 38 Mrd. USD anwachsen soll) übersteigt. Das Unternehmen kombiniert Flüssigkeitsantriebstechnologie und Metall-3D-Druck, um effiziente Raketen und Transferfahrzeuge zu entwickeln, die kleine Satelliten in die Umlaufbahn bringen. Das Unternehmen hat insbesondere das kostengünstige Raketentriebwerk Launcher Engine-2 (E2) entwickelt, das für die Massenproduktion optimiert wurde. Es soll das leistungsstärkste Flüssigkeitsraketentriebwerk seiner Klasse sein und ist als zentrale Schubkomponente für die Light-Rakete von Launcher vorgesehen. Um dieses innovative Design zu realisieren, wandte sich Launcher an Stratasys Direct Manufacturing und die Metall-AM-Technologie von Velo3D.
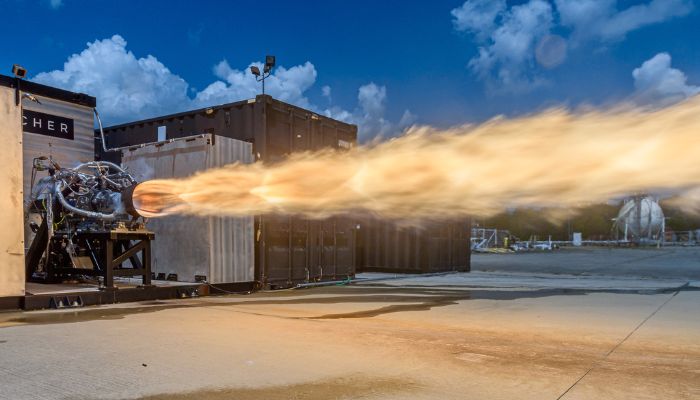
Testen des Antriebs (Bild: Launcher/John Kraus Photography)
Ein genauerer Blick auf den E-2-Flüssigkeitsraketentriebwerk
Wie bereits erwähnt, wurde das E-2-Flüssigkeitsraketentriebwerk als Teil der Hochleistungsraketen von Launcher entwickelt. Der mit LOX (Flüssigsauerstoff)/RP-1 (Kerosin) angetriebene 22.000 lbf (pound-force) Motor gilt als der weltweit leistungsstärkste Motor für kleine Starts. Das aus einer Kupferlegierung 3D-gedruckte Triebwerk hat einen Verbrennungswirkungsgrad von 98 % und eine Leistung von 365s Isp. Darüber hinaus kann sich das Laufrad der LOX-Pumpe dank seiner hohen Auswuchtung unter kryogenen Bedingungen mit 30.000 Umdrehungen pro Minute drehen und dabei flüssigen Sauerstoff transportieren.
Der innovative und leistungsstarke Charakter der E-2-Rakete bedeutet jedoch, dass sie nicht so einfach herzustellen ist. Die Turbopumpe, einschließlich des Laufrads, stellt eine besondere Herausforderung dar. Max Haot, Gründer und CEO von Launcher, erläuterte die Schwierigkeit des Projekts: „Bei jedem Flüssigkeitsraketentriebwerk, das eine Umlaufbahn erreichen kann, ist die Turbopumpe einer der schwierigsten Teile des Projekts … oder zumindest die Hälfte der Herausforderung. Und wenn es sich um eine Turbopumpe für einen geschlossenen Zyklus mit Stufenverbrennung handelt, wird diese Herausforderung noch größer.“
Und obwohl für das Projekt die additive Fertigung von Metallen gewählt wurde, sind Fehler auf diesem hohen Leistungsniveau nicht möglich. Haot fügte hinzu: „Ich möchte betonen, wie bedeutsam dies ist. Wir haben es mit flüssigem Sauerstoff und einem Laufrad zu tun, das sich mit 30.000 Umdrehungen pro Minute dreht, um eine Leistung von etwa einem Megawatt aus der Turbine zu erzeugen. In einer solchen Umgebung mit einem Druck von 4.000 psi kann jede Anomalie, jede Reibung zwischen Rotor und Stator, zu einer sofortigen, schnellen und ungeplanten Demontage führen.“ Innovative Technologien wären also der Schlüssel.
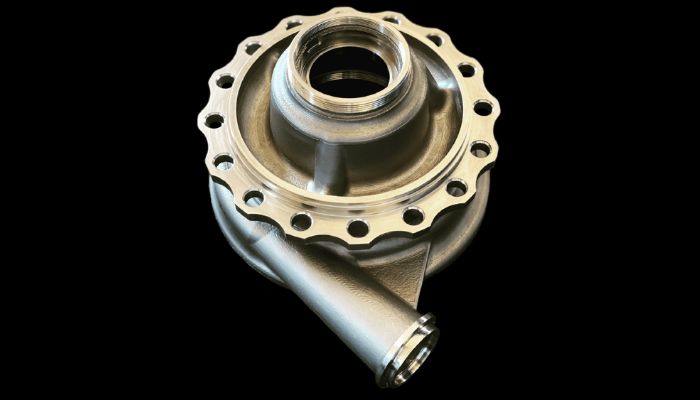
Spiralteil der Flüssigsauerstoffpumpe zur Versorgung des E-2-Triebwerks (Bild: Launcher)
Launcher wandte sich daher an Stratasys Direct Manufacturing, die ihrerseits die Sapphire®-Lösung von Velo3D verwendeten, um den gut ausbalancierten Inducer-Impeller zu erstellen. Diese wichtige Komponente beschleunigt das LOX und treibt es in die Brennkammer, wodurch ein größerer Flüssigkeitsstrom und mehr Schub für die Rakete erzeugt wird. Genauer gesagt wurde der Impeller der E-2 durch die Integration von zwei separaten 3D-gedruckten Teilen, einem Inducer und einem Impeller, in ein gemeinsames und effizientes Bauteil hergestellt. Als Material wurde INCONEL 718 gewählt, ein korrosionsbeständiges Material mit guter LOX-Kompatibilität und ausgezeichneter mechanischer Festigkeit bei kryogenen Temperaturen.
Warum entschied man sich für die additive Metall-Fertigung?
Wenn Launcher natürlich jede beliebige Technologie wählen könnte, warum haben sie sich dann für Metal AM und insbesondere für die Lösung von Velo3D entschieden? Nun, die additive Fertigung von Metallen hat, wie zu erwarten, mehrere Vorteile, insbesondere in Bezug auf niedrigere Kosten und Designfreiheit. Allerdings ist nicht jede Lösung geeignet. Um die erforderlichen Eigenschaften zu erreichen, konnte das Teil nicht mit internen Stützen oder durch Kippen hergestellt werden. Deshalb entschied sich Stratasys Direct für das Velo3D Sapphire®-System, da es Teile ohne Stützen drucken kann.
Vor allem die Möglichkeit, flach zu drucken, war für das Team von entscheidender Bedeutung, da ein Kippen des Teils während des Druckvorgangs verhindert hätte, dass ein gut ausbalanciertes drehendes Bauteil hergestellt werden konnte. Bei anderen Lösungen wäre dies nicht möglich, da die Benutzer das Teil im Allgemeinen kippen müssen, wenn sie interne Stützen vermeiden wollen (die bei vielen komplexen Geometrien für viele 3D-Drucklösungen aus Metall erforderlich sind). Das ist bei dem Sapphire®-System nicht der Fall.
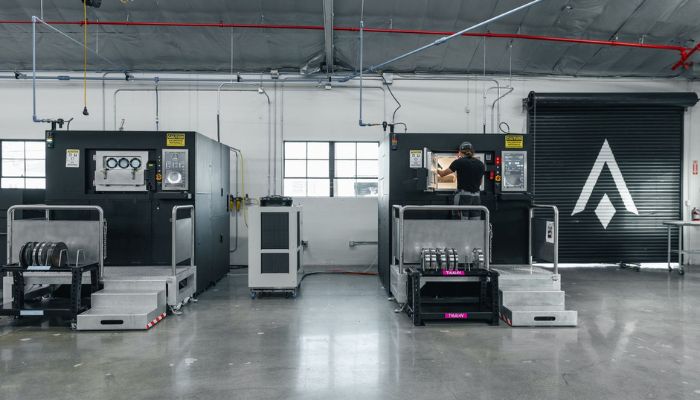
Die beiden Sapphire-Drucker von Launcher (Bild: Launcher)
Wie wir bereits erwähnt haben, ist die Lösung von Velo3D aufgrund ihrer Designfreiheit einzigartig im Bereich AM und verkörpert das Motto des Unternehmens „Drucken Sie das Teil, das Sie wollen und brauchen – ohne Kompromisse“. Diese Freiheit ist das Ergebnis mehrerer Faktoren, einschließlich der Tatsache, dass Velo3D eine fortschrittliche, vollständig integrierte Metall-AM-Lösung anbietet, welche seine Flow™-Druckvorbereitungssoftware und Assure™-Software zur Qualitätsvalidierung inkludiert. Darüber hinaus ist das System in der Lage, niedrige Winkel von bis zu null Grad zu drucken. Letzteres war für Launcher besonders wichtig, da das Teil so flach gedruckt werden konnte.
Ein Kippen des Teils hätte die Qualität aufgrund von Spannungsakkumulationen während des Drucks beeinträchtigt und die Herstellung eines gut ausbalancierten Spinning-Bauteils verhindert. Laut Stratasys Direct war es mit dem Velo3D-System möglich, die Laufräder in der idealen Ausrichtung zu drucken und gleichzeitig die Notwendigkeit interner Stützen zu vermeiden, die das fertige Teil ebenfalls hätten beschädigen können. Andre Ivankovic, Maschinenbauingenieur bei Launcher, erklärte weiter: „Indem wir das Teil flach gedruckt haben, erhielten wir eine schöne symmetrische Massenverteilung des Teils in Bezug auf die zentrale Rotationsachse.“
Was war das Ergebnis?
Das resultierende Teil musste umfassende, kundenspezifische Nachbearbeitungs– und Validierungsschritte durchlaufen, bevor es fertiggestellt werden konnte. Zu diesem Zweck bearbeitete Stratasys Direct das Bauteil teilweise, um das gesamte Pulver aus den inneren Kanälen zu entfernen, bevor es einer zertifizierten Wärmebehandlung unterzogen wurde. Der nächste Schritt war die Bestätigung, dass das Laufrad die Anforderungen an die Materialdichte und -integrität vor den thermischen Prozessen erfüllt.
Die Kombination aus der AM-Expertise von Stratasys Direct und der strengen sekundären Nachbearbeitung mit der Fähigkeit von Velo3D, ohne Stützen zu drucken, gewährleistete die erfolgreiche Herstellung eines hochkomplexen und funktionalen Teils. Und die bisherigen Tests sind erfolgreich verlaufen. Vor kurzem hat Launcher die Turbopumpe des E-2-Triebwerks für die U.S. Space Force in einer Kampagne im NASA Stennis Space Center erfolgreich getestet. Dort konnte das E-2-Testteam im Verlauf von 11 Tests alle Ziele in Bezug auf Leistung, Eingangs- und Ausgangsdruck, Effizienz und Vibration erreichen oder übertreffen. Mehr darüber, wie der E-2 mit der Sapphire®-Lösung von Velo3D hergestellt wurde, erfahren Sie HIER.
Was ist Ihre Meinung zu dem E-2-Flüssigkeitsraketentriebwerk? Teilen Sie es uns mit und kontaktieren Sie uns. Möchten Sie eine Zusammenfassung der wichtigsten Neuigkeiten im 3D-Druck und der Additiven Fertigung direkt und bequem in Ihr Postfach? Registrieren Sie sich jetzt für unseren wöchentlichen Newsletter und folgen Sie uns auf Facebook und Twitter um stets auf dem Laufenden zu bleiben! Außerdem sind wir auch auf LinkedIN und auf Youtube zu finden.
*Titelbildnachweis: Launcher