DLP trägt zur Herstellung verbesserter Gummiteile bei
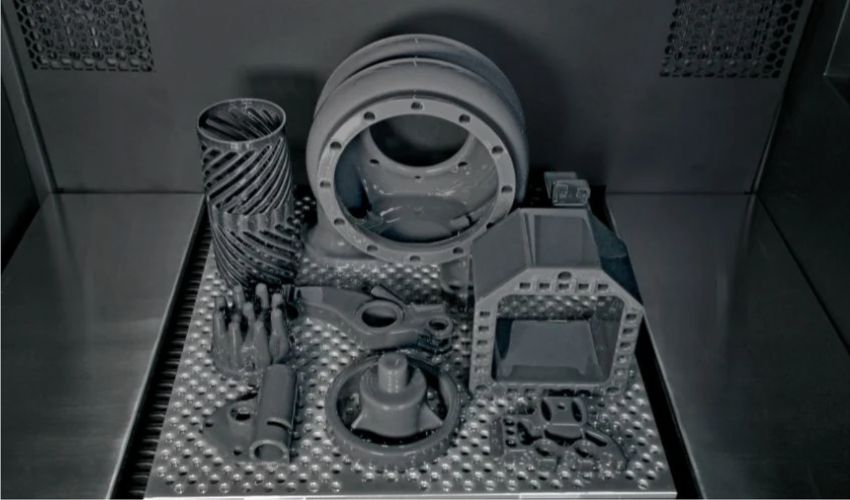
Digital Light Processing (DLP) ist eine der wichtigsten heute verfügbaren 3D-Drucktechnologien. Sie ist eine Art der Photopolymerisation und besteht im Wesentlichen aus der Verwendung eines Videoprojektors, um lichtempfindliche Harze auszuhärten. Die Technologie ist sowohl wegen ihrer Schnelligkeit als auch wegen ihrer Genauigkeit beliebt und kann in einer Vielzahl von Branchen eingesetzt werden. Und sie wird ständig verbessert.
Das erste Unternehmen, das diese Technologie kommerziell nutzte, EnvisionTEC, hat im Laufe der Jahre große Fortschritte gemacht. Und seit der Übernahme durch Desktop Metal im vergangenen Jahr, bei der das Unternehmen in Desktop Health und ETEC aufgeteilt wurde, hat es seine aufregendsten Innovationen in diesem Bereich gezeigt, darunter Top-Down-DLP, die Entwicklung neuer Materialien wie Gummi und vieles mehr. Aber wie funktioniert DLP? Was genau sind die Innovationen, die ETEC in diesem Bereich entwickelt hat? Und vor allem, welche Anwendungen gibt es für diese Technologie? Wir haben uns das genauer angesehen.
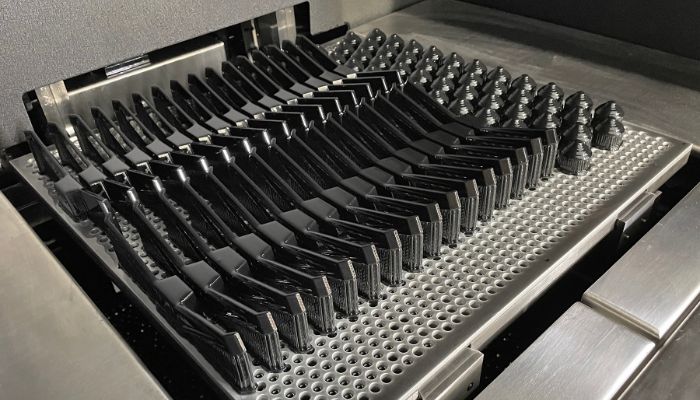
ETEC Extreme 8K DLP Bauplatte (Bild: ETEC)
Wie funktioniert der Vorgang im Detail?
Die Photopolymerisation, d. h. die Aushärtung lichtempfindlicher Harze mit UV-Licht, kann als Vorläufer der additiven Fertigung angesehen werden. Wie Sie vielleicht wissen, war die allererste 3D-Drucktechnologie in den 80er Jahren die Stereolithografie. Doch schon bald danach kamen neue Technologien auf, um die Probleme der SLA-Technologie zu lösen. Dazu gehört die DLP-Technologie, die 1999 aufkam.
Dank des Einsatzes eines DLP-Chips konnte die digitale Lichtverarbeitung das Licht eines Projektors nutzen, um lichtempfindliche Harze im flächendeckenden 3D-Druck auszuhärten. Die Technologie ist schneller als das SLA-Verfahren, da sie es ermöglicht, den gesamten Bauplatz mit UV-Licht zu bestrahlen, anstatt nur einen einzigen Aushärtungspunkt wie bei einem Laser, und gleichzeitig eine hohe Oberflächenqualität und definierte Kanten zu erzielen. Dies macht die Technologie zum Maßstab unter den Küvettenpolymerisationsverfahren.
Ein herkömmliches DLP-Gerät arbeitet im Wesentlichen von unten nach oben, mit einem Projektor, der sich unter der Wanne befindet. Dieses Verfahren wurde bei dem allerersten kommerziellen DLP-Drucker, dem EnvisionTEC Perfactory, eingesetzt. Da sich der Projektor an der Unterseite befindet, kann das Licht des Projektors durch den Boden der Wanne in das Harz eindringen, so dass die Schichthöhe schnell und genau kontrolliert werden kann. Die Schale ist mit einem durchsichtigen Boden versehen, der die Übertragung von Licht ermöglicht. Ähnlich wie bei anderen Harztechnologien bewegt sich die Bauplatte dann in der Z-Achse auf und ab in die Harzwanne und erzeugt eine dünne Schicht, die ausgehärtet werden kann.
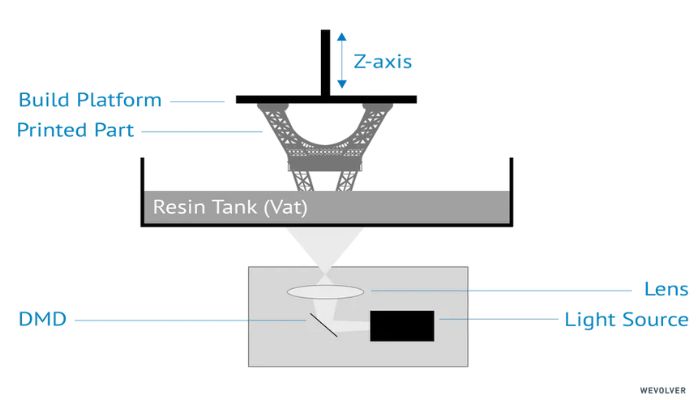
Das traditionelle DLP-Verfahren, das ursprünglich von EnvisionTEC vermarktet wurde (Bild: Wevolver)
Seit diesem ersten Drucker hat es eine Reihe von Fortschritten auf diesem Gebiet gegeben. Im Jahr 2015 wurde mit dem CLIP-Verfahren, bei dem eine Sauerstoffschicht durch eine sauerstoffdurchlässige Folie zugeführt wird, die Notwendigkeit beseitigt, jede ausgehärtete Schicht zu trennen, was die Geschwindigkeit erheblich erhöht. Die Anwendung dieser „toten Zone“ wurde von EnvisionTEC 2016 mit einem neuen Verfahren namens CDLM (Continuous Digital Light Manufacturing) eingeführt.
Im Jahr 2021, nach der Übernahme von EnvisionTEC durch DM, wurde eine weitere neue Technologie, Hyperprint, eingeführt, die die Notwendigkeit von Sauerstoffschichten eliminiert. Nach Angaben von Desktop Metal nutzt Hyperprint Wärme, um die Viskosität der Harze zu verringern und so den Druck zu beschleunigen. Darüber hinaus wurde das Closed-Loop-Printing mit CLP-Sensoren eingeführt, um zu erkennen, wann sich die Teileschicht vollständig von der Folie des Harzbottichs gelöst hat.
Der jüngste Fortschritt des Unternehmens liegt im Bereich des Top-Down-DLP. Obwohl das Bottom-Up-DLP-Verfahren in den letzten 20 Jahren der Standard war, hat ETEC den Xtreme 8K Top-Down-DLP-Drucker auf den Markt gebracht, um eine Reihe von Einschränkungen zu beseitigen, die beim Bottom-DLP-Druck bestanden. Dieses neueste Gerät bietet den Anwendern eine Reihe von Vorteilen, darunter ein erweitertes Materialportfolio für noch mehr Anwendungen, und repräsentiert die neueste DLP-Technologie.
Was sind die Vorteile des Xtreme 8K DLP-Druckers?
Der Xtreme 8K DLP 3D-Drucker von ETEC bietet den Anwendern eine Reihe von Vorteilen, die über die allgemeinen Vorteile der DLP-Technologie wie Geschwindigkeit und komplexe Geometrien hinausgehen. Bei der Verwendung von Bottom-up-DLP waren die Anwender bisher beispielsweise mit Einschränkungen bei der Anzahl der zu druckenden Teile konfrontiert, da das Gewicht, das vertikal von einer Bauplatte getragen werden kann, begrenzt war und eine große Anzahl von Trägern erforderlich war, um die Haftung zu gewährleisten. Darüber hinaus gab es erhebliche Einschränkungen bei den verwendbaren Harztypen, da für die Wiederbeschichtung Harze mit einer niedrigen Viskosität erforderlich waren. Dadurch wurden der Durchsatz und die endgültigen Materialeigenschaften eingeschränkt.
Der Xtreme 8K DLP-Drucker ist in der Lage, diese Hindernisse zu überwinden, da er dank des Top-Down-DLP-Verfahrens die größte DLP-Baufläche (450 x 371 x 399 mm – 166.950 mm2) unter den kommerziellen DLP-Druckern in Produktionsqualität bietet. Er ist in der Lage, große Teile oder in hohen Stückzahlen mit neuen Materialien zu drucken, die laut DM direkt mit den Duroplasten konkurrieren können, die beim herkömmlichen Kunststoffspritzguss verwendet werden.
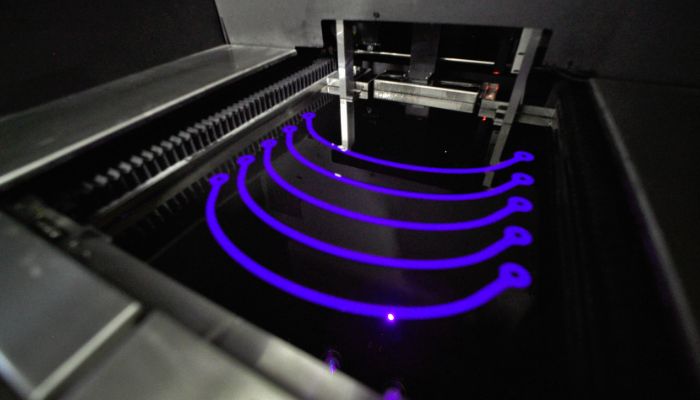
Details des Xtreme 8K top-down DLP Druckers (Bild: ETEC)
Diese Fortschritte bei den Materialien wurden insbesondere durch die Forschungs- und Entwicklungsarbeit von DM über die Tochtergesellschaft Adaptive 3D ermöglicht. Diesem Unternehmen ist es gelungen, eine neue Materialfamilie, die DuraChain Photopolymere, zu entwickeln. Dabei handelt es sich um einteilige Ein-Topf-Photopolymere, die die durch Photopolymerisation induzierte Phasentrennung (Photo PIPS) nutzen. Einige Beispiele sind Schaumstoffe und Gummimaterialien. Diese und andere Eigenschaften haben Druckern, die DLP verwenden, viele neue Anwendungen in einer Vielzahl von Branchen eröffnet.
DLP wird zur Revolutionierung von Gummiteilen eingesetzt
Eine der spannendsten Anwendungen für ETECs Top-Down-DLP ist die Herstellung von Gummiteilen. Aerosport Additive, ein in Ohio ansässiges Dienstleistungsunternehmen, das Prototypen und Arbeitsmodelle für Kunden aus der Automobil-, Luft- und Raumfahrt- sowie der Elektronikbranche herstellt, entdeckte, dass die DLP-Technologie von ETEC und der Top-Down-DLP-Drucker Xtreme 8K der Schlüssel für die Herstellung besserer Gummiteile sind.
Vor der Einführung von DLP musste Aerosport Additive entweder auf Urethanguss für Prototypen und Kleinserien oder auf Spritzguss für die Massenproduktion von Gummiteilen zurückgreifen. Das lag daran, dass die Herstellung von Gummiteilen in der additiven Fertigung schon immer eine Herausforderung darstellte, da es fast unmöglich war, Materialien herzustellen, die das Aussehen, das Gefühl und die Leistung von echtem Gummi hatten. Dies ist nun nicht mehr der Fall.
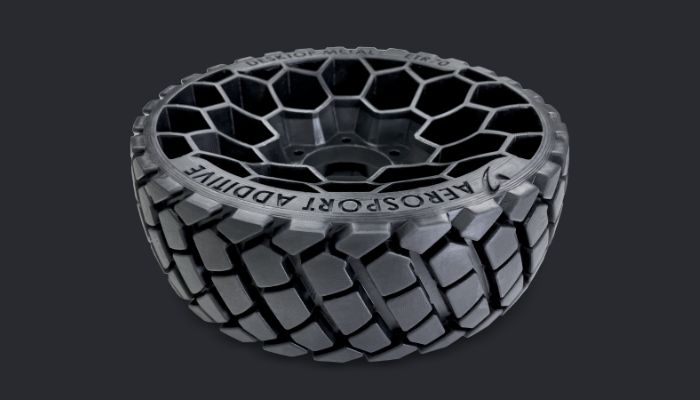
Dank des Xtreme 8K Top-Down DLP 3D-Druckers und neuer Materialien ist Additive Aerosport in der Lage, Teile aus Gummi herzustellen (Bild: ETEC)
Durch den Einsatz des Xtreme 8K und des Elastic ToughRubber von Adaptive3D war das Unternehmen in der Lage, schnell und kostengünstig Teile aus Gummi mit einer Shore-Härte von A70 herzustellen. Ein Beispiel dafür war die Herstellung von Vierweg-Schaltern, die an den Steuerknüppeln von Flugzeugen befestigt werden und für die Feineinstellung der Trimmung des Flugzeugs entscheidend sind.
Wie Sie sich vorstellen können, werden diese Teile in der Regel in kleineren Mengen hergestellt, aber die Umstellung auf Urethanguss war ein langsamer und teurer Prozess. Mit dem ETEC Xtreme 8K kann Aerospace Additive nun bis zu 150 Schalter in einer einzigen 2,5-stündigen Fertigung herstellen, was sowohl Zeit als auch Kosten spart. Die additive Fertigung ermöglicht es außerdem, das Design zu ändern oder fein abzustimmen, um es an die Bedürfnisse der verschiedenen Kunden anzupassen. Diese und andere Anwendungen zeigen, wie die DLP-Verfahren von ETEC in den kommenden Jahren noch mehr Branchen beeinflussen könnten. Mehr über ETEC und seine DLP-Lösungen erfahren Sie HIER.
Was ist Ihre Meinung zur DLP-Technologie? Teilen Sie uns Ihre Meinung mit und kontaktieren Sie uns. Möchten Sie eine Zusammenfassung der wichtigsten Neuigkeiten im 3D-Druck und der additiven Fertigung direkt und bequem in Ihr Postfach? Registrieren Sie sich jetzt für unseren wöchentlichen Newsletter und folgen Sie uns auf Facebook und Twitter, um stets auf dem Laufenden zu bleiben! Außerdem sind wir auch auf XING und LinkedIN zu finden.