Die spannendsten 4D-Druck Projekte
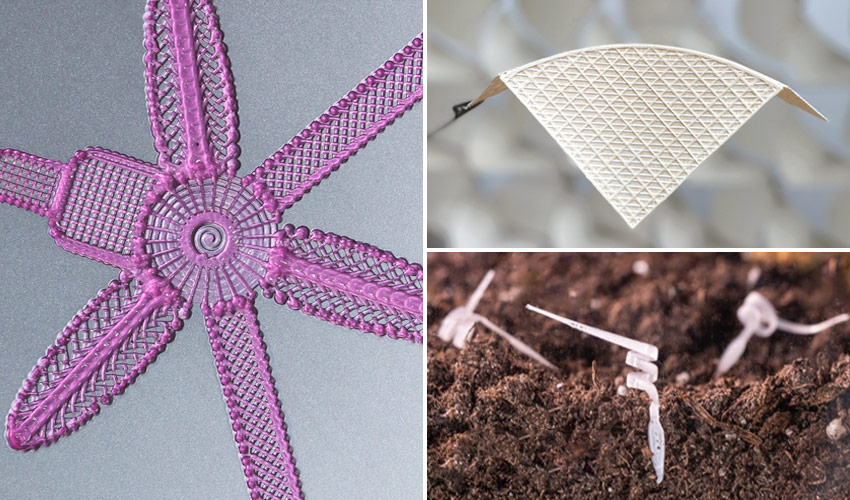
Haben Sie schon vom 4D-Druck gehört? Der 4D-Druck baut auf dem herkömmlichen 3D-Druck auf und bezieht eine weitere Dimension ein: die Zeit. Das bedeutet, dass das fertige Objekt nicht statisch bleibt, sondern nach einem externen Stimulus seine Form, Farbe oder Größe ändern kann. Die Ursprünge des 2013 eingeführten 4D-Drucks gehen auf Sklyar Tibbs vom Self-Assembly Lab des MIT zurück, der auch heute noch zu den aktivsten Projektleitern gehört, auch wenn sich das Gebiet inzwischen stark weiterentwickelt hat. Aber welche Projekte gibt es? In unserer neuesten Auflistung haben wir verschiedene erfolgreiche Beispiele für den 4D-Druck in diesem Bereich, einschließlich der Anwendungen und Materialien, näher betrachtet.
Mizzou Engineering entwickelt Implantat aus intelligentem Material
Einem Forscherteam von Mizzou Engineering ist es im Rahmen einer Anfang des Jahres veröffentlichten Studie gelungen, ein medizinisches Implantat per 4D-Druck zu entwickeln. Das Implantat kann vollständig personalisiert werden und fördert dank seiner Materialzusammensetzung auch die Regeneration des Weichgewebes. Ausschlaggebend für eine personalisierte Behandlungsmöglichkeit, sei der 4D-Druck des Implantats gewesen, heißt es von Seiten der Wissenschaftler. Beim 4D-Druck werden 3D-Drucktechnik und intelligente Materialien verbunden, welche ihre Funktionen in bestimmten Kontexten anpassen können. In diesem Fall wurde auf einen bioresorbierbaren Formgedächtniselastomer gesetzt. So konnte auf die Beschwerden des Pateinten eingegangen werden und eine optimale Behandlung aufgezeigt werden: „Wir haben ein In-vitro-Modell des Patienten entworfen und es intravaskulär in ein 3D-gedrucktes Herz des Patienten implantiert, um einen Proof of Concept zu zeigen, wie das Material für dieses Problem eingesetzt werden könnte,“ sagt Alireza Mahjoubnia, Doktorand im Fach Maschinenbau. „Das Material kann sein Verhalten je nach physiologischen Bedingungen ändern. Wir programmieren seine Form so, dass es durch einen Katheter passt, und nachdem es in das linke Herzohr gelangt ist, kann es seine Form wiederherstellen und zu seiner ursprünglichen Form zurückkehren, wobei es ein Formgedächtnisverhalten zeigt.“
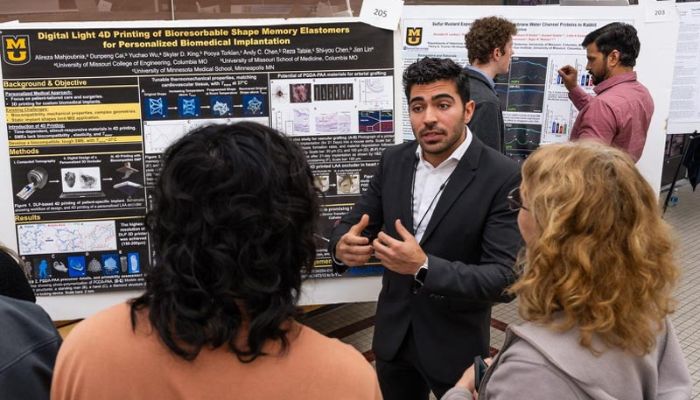
(Bild: University of Missouri)
4D-Druck für die Knochenregeneration
In China untersuchte eine Gruppe von Forschern die Möglichkeit, intelligente biopiezoelektrische 4D-Gerüste für die Knochenregeneration zu schaffen. Die Piezoelektrizität in menschlichen Knochen ist ein Schlüsselfaktor für die Knochenregeneration. Daher haben biopiezoelektrische Materialien bei der Reparatur geschädigter Knochen große Aufmerksamkeit erlangt. Herkömmliche Herstellungsstrategien stoßen jedoch noch immer auf Grenzen bei der Herstellung maßgeschneiderter Gerüste, was ihre klinische Anwendung behindert. Die Forscher untersuchten daher den Einsatz von 3D- und 4D-Druck für die Herstellung von biopiezoelektrischen Gerüsten in komplexer geformten Strukturen. Insbesondere können 4D-Gerüste zeitabhängig programmierbares Gewebe als Reaktion auf externe Stimuli für die Knochenregeneration bereitstellen. Diese intelligenten Implantate verändern Form, Eigenschaften und Funktionalität beim Knochengewebe-Engineering und könnten daher als Implantate der nächsten Generation eingesetzt werden.
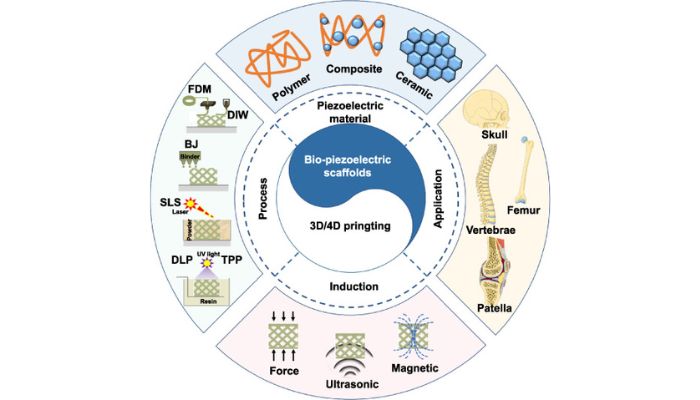
Piezoelektrische Materialien, Druckverfahren und mögliche Anwendungen für 4D-Implantate. (Bild: Annan Chen et al 2023 Int. J. Extrem. Manuf.)
4D-Geräte, die den Mechanismus von Pflanzen nachahmen
Die nächste Anwendung des 4D-Drucks stammt von einer Gruppe von Forschern des Wyss-Instituts und der School of Engineering and Applied Sciences, beides Einrichtungen der Harvard University. Das Team hat einen Weg gefunden, die dynamischen Veränderungen in Pflanzen und Blumen als Reaktion auf Feuchtigkeit und Temperatur mit Hilfe von 4D-gedruckten Hydrogel-Kompositen zu imitieren. Zu diesem Zweck entwickelten sie eine Tinte aus ausgerichteten Zellulosefibrillen, die aus Holz gewonnen und nach dem mathematischen Modell des 4D-Drucks konfiguriert wurden. Diese Tinte kodiert Ausdehnungs- und Steifigkeitseigenschaften, die es ermöglichen, das Ausdehnungsverhalten zu programmieren, wenn die Drucke in Wasser eingetaucht werden. Ebenso können verschiedene Hydrogelmaterialien verwendet und Zellulosefasern durch andere Füllstoffe, z. B. leitfähige, ersetzt werden. Zu den Anwendungen gehören medizinische Geräte, die bei Kontakt mit Körperflüssigkeiten programmierte Formen annehmen, intelligente Textilien, weiche Elektronik, Sensoren und elektrische Aktoren.
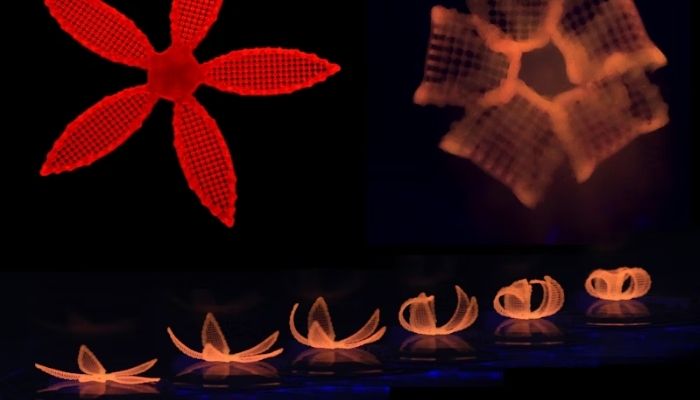
(Bild: Wyss-Institut)
4D-Drucktechnologie für die Robotik
Die Forscher Dr. Liwen Zhang und Dr. Ruirui Quiao an der University of Queensland haben eine 4D-Drucktechnologie entwickelt, die flüssige Metalle für die Robotik erzeugt, welche mithilfe von Nahinfrarotlicht ihre Form verändern. Die Metallpolymere, die durch Infrarotlaser mechanische Aufgaben erledigen können, befinden sich in der Forschungsphase, bieten aber Potential für die Luft- und Raumfahrt sowie für die Medizin, beispielsweise bei der Herstellung künstlicher Muskeln. Die Druckharze werden mit runden Metallnanopartikeln hergestellt, die auf Infrarotlicht reagieren. Dadurch können diese gesteuert und bewegt werden. Die neuen Herstellungsmethoden des Labors ermöglichen es, flexible Designs zu erzeugen, die gleichzeitig fest sind. Dr. Zhang betont: „4D-Druck erweitert den traditionellen 3D-Druck um eine neue Dimension – die Dimension der Zeit. Unsere Methode ermöglicht es uns, intelligente Flüssigmetalle herzustellen, die individuell angepasst, geformt und im Laufe der Zeit verändert werden können, ohne dass Kabel oder Schaltkreise erforderlich sind.“ Die Technologie soll darüber hinaus für die Softrobotik und verwandte Technologien genutzt werden, um natürliche Bewegungen und Interaktionen zu imitieren.
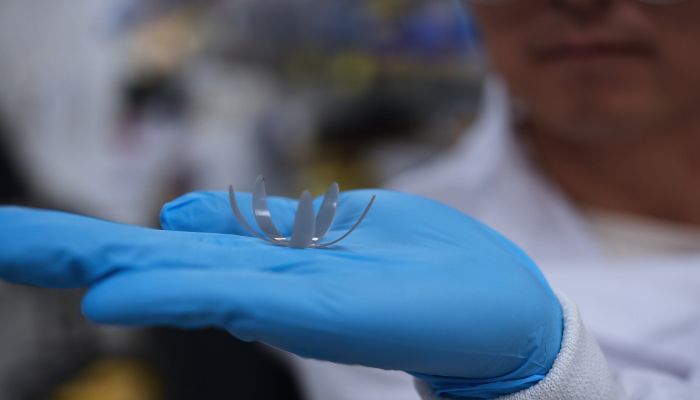
Die 4D-Struktur, die sich bei Nahinfrarotlicht in Bewegung setzt. (Bild: Australische Institut für Bioengineering und Nanotechnologie University of Queensland)
4D-Druck für die Raumfahrt
Zortrax, ein 3D-Drucker-Hersteller, arbeitete über ein Jahr an einem von der Europäischen Weltraumorganisation finanzierten 4D-Druckprojekt, um elektrische Mechanismen mittels 3D-Druck zu entwickeln, die Biegen, Drehen und Entfaltung ermöglichen. Bereits 2013 wurden 4D-einsetzbare Strukturen erforscht, die sich bei Wärme bewegen sollten. Jedoch brachte das Projekt viele Schwierigkeiten mit sich, da das Verfahren kaum kontrollierbar war und sich bereits bei 40°C aktivierte.Dieses Problem wurde nun durch den Einsatz neuer Materialien, Software und 3D-Drucker gelöst. Als Material wurden Formgedächtnispolymere verwendet, die eine Glasübergangstemperatur von 75°C haben, sowie das elektrisch leitfähige Filament FIBERFORCE NYLFORCE Conductive, das als Heizung fungiert und den Formgedächtniseffekt auslöst. Dieser Prozess beschreibt die Eigenschaft bestimmter Materialien, nach einer Verformung in ihre Ausgangsform zurückzukehren. Zudem wurde die Z-SUITE-Software und der Dual-Extrusions-3D-Drucker M300 Dual gewählt, der ein Bi-Material-3D-Druckverfahren einsetzt und mit zwei Druckköpfen gleichzeitig drucken kann. Das Design wurde federähnlich gestaltet, um genügend Drehmoment zu erzeugen, damit sich das 3D-gedruckte Chassis ohne Reibung drehen kann. Dieser Fortschritt bietet großes Potential in der Raumfahrt, da er das Gewicht von Antennen oder Sensoren verringern könnte und der Prozess auch auf größere Mechanismen angewendet werden kann. Derzeit befindet sich das Projekt noch in der Forschungsphase.
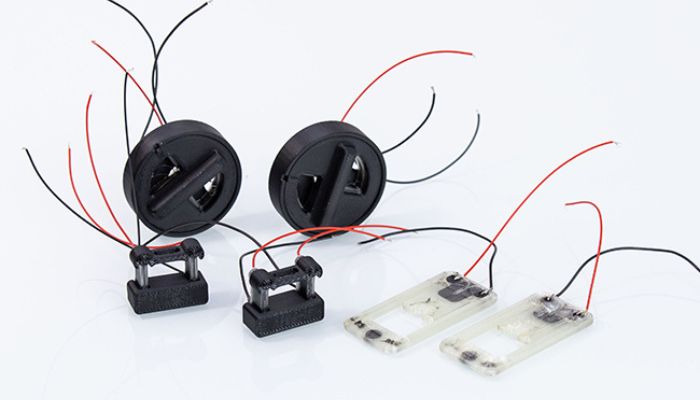
Demonstratoren der 4D-Drucktechnologie. (Bild: Zortrax)
Der I-Seed-Roboter
Forscher des Italienischen Instituts für Technologie (ITT) haben mit Hilfe des 4D-Drucks den weichen Roboter I-Seed entwickelt. Dieser von Pflanzensamen inspirierte Roboter ist in der Lage, Temperatur und Feuchtigkeit von Boden und Luft zu analysieren und zu überwachen sowie das Vorhandensein von Schadstoffen zu erkennen. Konkret wurde I-Seed durch Nachahmung der Funktionsweise einer südafrikanischen Geranie gebaut und ist in der Lage, seine Form zu verändern, wenn er Feuchtigkeit aufnimmt. Die Forscher druckten den Roboter im FDM-Verfahren mit biologisch abbaubaren Polymeren auf Polycaprolactonbasis. Bei der Entwicklung von I-Seed haben sie die biomechanischen Eigenschaften der afrikanischen Pflanze nachgeahmt, damit er in seinen Abmessungen und seiner Leistung einem echten Samen so nahe wie möglich kommt.
4D-gedruckte, sich selbst zusammensetzende Objekte vom MIT
Wie bereits erwähnt, lassen sich die Ursprünge des 4D-Drucks auf Skylar Tibbs und das MIT Self-Assembly Lab zurückführen. Daher sollte es nicht überraschen, dass das Labor im Bereich des 3D-Drucks mit vielen verschiedenen Projekten, darunter ein älteres Projekt (aus dem Jahr 2013!), das jedoch in der Branche Kultstatus genießt, nach wie vor äußerst wichtig ist: 4D-gedruckte, sich selbst zusammensetzende Würfel. Diese bestehen aus hydroreaktiven Verbundpolymeren mit hydrophilen Elementen und nicht aktiven, starren Elementen. Wenn die Kette mit Wasser in Berührung kommt, ist sie in der Lage, eine neue Form anzunehmen, nämlich einen Würfel. Seitdem hat das Labor seine Arbeit fortgesetzt und in jüngster Zeit unter anderem ein 4D-Strickkleid entwickelt.
4D-gedruckte, bistabile Strukturen
4D-Druck wird in Fachkreisen als „Upgrade“ des 3D-Drucks gehandhabt, da er die Komponente der Zeit miteinbezieht. Aus diesem Grund konzentriert sich die innovative Forschung auch darauf, Materialien für den 4D-Druck zu testen und mit Designs für 4D-Druck zu experimentieren. So auch an der EHT Zürich, wo sich Doktorand Tim Chen im Rahmen eines Forschungsprojekts mit dem Entwurf von gedruckten, einsetzbaren und aktiven Systemen befasste. Er konzentrierte sich zunächst auf das Erforschen des Designs für diese 4D-gedruckten Strukturen und zielte darauf ab, seine Materialien so zu steuern, dass die Teile auf die Umgebung reagieren würden. Er setzte auf bistabile Verbindungen innerhalb seiner Strukturen, welche eine Formveränderung der Strukturen herbeirufen können. Solche gewünschten Änderungen der Formen könnten sich als gewinnbringend für diverse Anwendungen herausstellen, darunter Architektur, Softrobotik, Raumfahrt und Automobilbranche.
4D-Hydrogel-Strukturen für präzise Implantation
Eine kürzlich in der Fachzeitschrift Nature Communications veröffentlichte Studie beschreibt die Entwicklung von dynamischen, duroplastischen Polyurethanen für den 4D-Multimaterialdruck mit dem Ziel, Stützstrukturen zu schaffen, die minimalinvasiv implantiert werden können. Das Forscherteam entwickelte Strukturen mit einem Formgedächtnis, das durch die Körpertemperatur aktiviert wird und sich bei Kontakt mit Wasser verformt. Die Anwendung dieser Stützen funktioniert folgendermaßen: Es wird ein 2D-Muster gedruckt, das vorübergehend auf eine eindimensionale Form reduziert werden kann, um das Einsetzen durch einen Katheter zu erleichtern. Nach der Implantation kehrt das Material durch die Körpertemperatur in seine ursprüngliche 2D-Form zurück. Nach der Hydratation dehnt sich das Material aus und verwandelt sich in die gewünschte 3D-Struktur, da es nicht mehr aufquillt. Diese Kombination aus Formgedächtnis, programmierbarer Verformbarkeit sowie Ausdehnungs- und Steifigkeitseigenschaften macht die entwickelten duroplastischen Polyurethane vielversprechend für die Herstellung von Füllmaterialträgern für minimalinvasive Implantate.
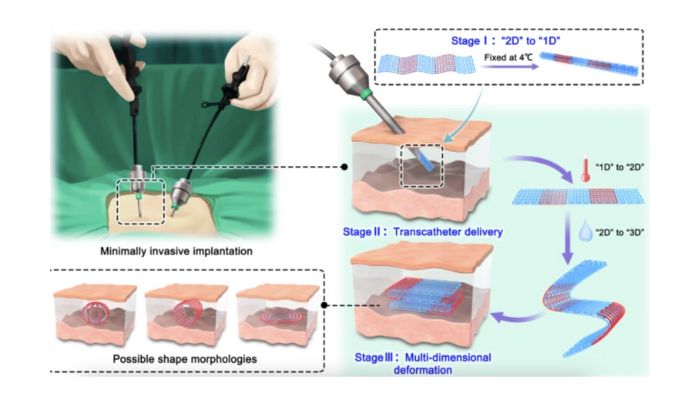
(Bild: Nature Communications)
4D-Druck von Formgedächtnisharzen
Diesmal berichten wir Ihnen von einem Forschungsprojekt mit Formgedächtnisharz. Die Forscher haben ein Material entwickelt, das auf einem lichtempfindlichen Harz und Flüssigkristallen basiert. Diese sorgen dafür, dass sich das zukünftige 3D-Druckteil unter Temperatureinfluss verändert. Konkret mischen sie 5 Gewichtsprozent der Kristalle in einem Tank und Toluol bei einer Temperatur von 70 °C. Die Mischung wird über Nacht abgekühlt, wodurch das Toluol verdampfen kann. Das entstandene Material wird dann mit einem DLP-3D-Drucker verwendet. Und die Ergebnisse können sich sehen lassen! Wenn sie höheren Temperaturen ausgesetzt werden, verformen sich die 3D-gedruckten Teile und kehren dann in ihre ursprüngliche Form zurück, wenn die Temperatur sinkt.
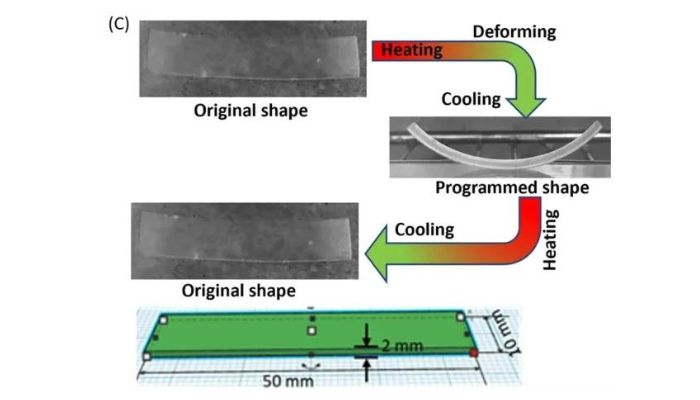
(Bild: Nature)
Aktuatoren in magnetoaktiven Polymeren
Ein Team von Wissenschaftlern des CEA-Iramis in Frankreich hat durch 4D-Drucken intelligenter Materialien Aktuatoren aus magnetoaktiven Polymeren entwickelt. Zunächst führten sie Experimente und Simulationen durch, um zu analysieren, wie sich Magnetit-Nanopartikel in lichtempfindlichen Harzen selbst zu verdrahteten Strukturen anordnen. Die mechanischen Eigenschaften der Fotopolymere lassen sich durch Variation der Harzzusammensetzung einstellen, und die magnetische Reaktion kann durch Anpassung der Nanopartikel-Beladung in der gedruckten Schicht verändert werden. Die Wissenschaftler haben einen DLP-3D-Drucker so angepasst, dass während der Herstellung jeder Schicht ein Magnetfeld unterschiedlicher Stärke und Richtung angelegt wird. Auf diese Weise produzierten sie eine Reihe von Objekten mit programmiertem Verhalten, wie z. B. Aktoren, die sich auf Befehl drehten oder bogen. Sie kombinierten auch magnetische Räder mit nichtmagnetischen Elementen, um lineare Aktoren oder aktive Greifer zu schaffen.
Ein 4D-Druckverfahren für hygromorphe Strukturen
Hygromorphes Verhalten wird von Harvard definiert als „Reaktion auf Veränderungen der Umweltfeuchtigkeit durch Veränderung der Geometrie“. Daher sind hygromorphe intelligente Strukturen aufgrund ihrer vielfältigen Anwendungsmöglichkeiten – von wetterabhängigen architektonischen Häuten bis hin zu adaptiven Wearables – sehr gefragt. Und jetzt könnte es möglich sein, diese Strukturen mit Hilfe des 4D-Drucks herzustellen. In einem kürzlich erschienenen Forschungsartikel zeigen Forscher, wie die Fused Filament Fabrication mit biobasierten, zellulosegefüllten Filamenten mit unterschiedlicher Steifigkeit und Feuchtigkeitsempfindlichkeit in Kombination mit einer mesoskaligen Strukturierung der gedruckten Elemente zu einer feuchtigkeitsabhängigen Betätigung beitragen kann. Mit einem standardmäßigen FFF-3D-Drucker mit zwei Extrudern konnten Teile hergestellt werden, die auf die relative Luftfeuchtigkeit in der Umgebung reagierten und sich in sich selbst falten konnten. Ein interessanter Prozess zur Herstellung von 4D-gedruckten, auf Feuchtigkeit reagierenden Strukturen.
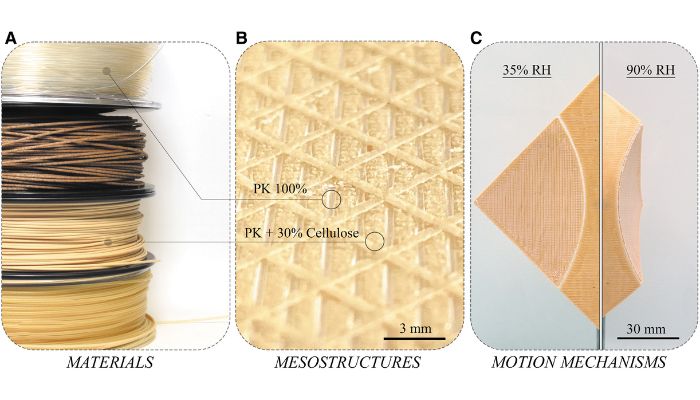
Ein Diagramm, das die verwendeten Materialien, das Design der Mesostrukturen und die Ergebnisse der hygromorphen Strukturen zeigt. (Bild: Tahouani et al.)
Was halten Sie von den 4D-Druckprojekten und welches der Projekte finden Sie am spannendsten? Lassen Sie uns dazu einen Kommentar da, oder teilen Sie es uns auf Facebook oder LinkedIN mit. Möchten Sie außerdem eine Zusammenfassung der wichtigsten Neuigkeiten im 3D-Druck und der additiven Fertigung direkt und bequem in Ihr Postfach erhalten? Dann registrieren Sie sich jetzt für unseren wöchentlichen Newsletter.