Die interessantesten Metallanwendungen auf der Formnext 2024
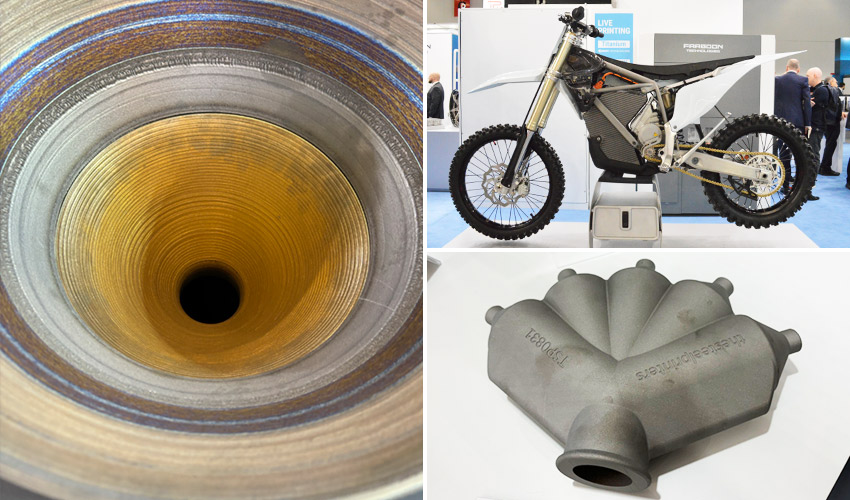
Es versteht sich von selbst, dass die Besucher der Formnext unglaubliche Lösungen sehen werden, sei es für den 3D-Druck, Software oder Materialien. Was aber auch nicht ignoriert werden sollte, sind die erstaunlichen Anwendungen, die verschiedene Unternehmen an ihren Ständen vorstellen. Auf der Formnext 2024 gab es insbesondere einige unglaubliche Metallanwendungen, die wir auf der Messe in verschiedenen Bereichen wie Luft- und Raumfahrt, Automobilbau, Zahnmedizin und vielen anderen gesehen haben. Deshalb haben wir beschlossen, einen Blick auf einige der coolsten Beispiele dieses Jahres zu werfen.
InssTek’s Multi-Material-Düse
Eine Anwendung, die uns auf der Formnext beeindruckt hat, ist zweifellos die Multi-Material-Raketendüse am Stand von InssTek. Die drei Tonnen schwere Raketendüse (301 x 201 x 567 mm groß und in 600 Stunden hergestellt) und die Verlängerung (432 x 270 x 169 mm groß und in 64 Stunden hergestellt) wurden in Zusammenarbeit mit dem Korea Aerospace Research Institute (KARI) mittels 3D-Druck mit gerichteter Energieabscheidung (DED) hergestellt. Der Multi-Material-Faktor ergibt sich aus der Tatsache, dass jedes Teil mit dem optimalen Material hergestellt wurde, eine einzigartige Eigenschaft, die mit der DMT-Technologie von InssTek möglich ist. In der Düse selbst besteht beispielsweise das Innenteil aus Al-Bronze mit einem Kühlkanal im Abstand von 1 mm, während das Außenteil aus Inconel 625 gefertigt ist. Die Verlängerung wurde aus C-103 hergestellt, einem der interessantesten Materialien, die derzeit in der Raumfahrtindustrie verwendet werden.
Die daraus resultierende einheitliche, leistungsstarke Einheit ist bemerkenswert, weil die Kombination dieser verschiedenen Metalle die Nutzung der Stärke jedes einzelnen ermöglicht, wodurch komplizierte Strukturen und Funktionen geschaffen werden können, die die Effizienz und Zuverlässigkeit von Raketentriebwerkskomponenten verbessern. Nach Angaben von InssTek ist dieser Durchbruch das Ergebnis strenger Tests, einschließlich erfolgreicher Verbrennungsversuche. Um die Zuverlässigkeit der Multi-Materialien zu gewährleisten, wurde beispielsweise jedes Teil nach einer Überprüfung durch Materialforschung im MX-Lab hergestellt, einschließlich Tests zur Zugfestigkeit und Wärmeleitfähigkeit. Es wird gehofft, dass der Erfolg dieser Teile den Weg für maßgeschneiderte Lösungen ebnen wird, die den komplexen Anforderungen der modernen Luft- und Raumfahrt gerecht werden. Eine unglaubliche Leistung des koreanischen Raumfahrtsektors, die hoffentlich den Weg für weitere Durchbrüche bei der Nutzung der additiven Fertigung für Raketenantriebe ebnen wird. Mehr über die Lösungen von InssTek erfahren Sie HIER oder auf dem InssTek-Stand D98 in Halle 12.0 auf der Formnext.
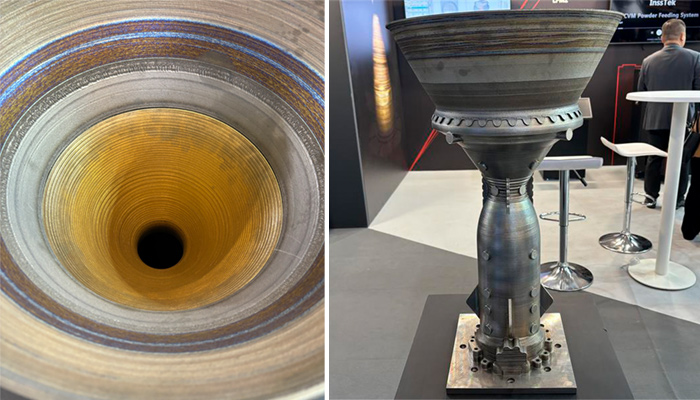
Die Multi-Material-Raketendüse von InssTek mit Innen- (links) und Außenansicht (rechts).
3D-Metalldruck eines Premium-Elektro-Motorradrahmens
Eine weitere Anwendung, die wir Ihnen von der Formnext aus vorstellen möchten, stammt von Farsoon Europe. Das Unternehmen, das sich auf die Entwicklung von 3D-Drucklösungen für Metalle und Polymere spezialisiert hat, hat sich mit Stark Future zusammengetan. Ziel dieser Zusammenarbeit ist die Entwicklung von skalierbaren, leistungsstarken Fertigungslösungen für den Markt der Premium-Elektromotorräder. Ein anschauliches Beispiel dafür ist ein kompletter Motorradrahmen, der mit einer Titanlegierung auf dem 3D-Drucker FS721M-H-8-CAMS von Farsoon Europe hergestellt wurde, einer industriellen Metalllösung, die für großformatige Produktionsanforderungen ausgelegt ist. Mit einem Bauvolumen von 720 x 420 x 650 mm und ausgestattet mit acht leistungsstarken 1000-W-Faserlasern maximiert der FS721M-H-8-CAMS die Produktivität und reduziert gleichzeitig die Teilekosten. Das System beinhaltet auch die Continuous Additive Manufacturing Solution (CAMS) von Farsoon, die ein einzigartiges Fördersystem und eine Strategie für austauschbare Kartuschen einsetzt, um den Druckprozess kontinuierlich laufen zu lassen und die Ausfallzeiten zwischen den Bauvorgängen zu minimieren. Wenn Sie dieses Motorradteil aus Metall persönlich sehen möchten, besuchen Sie Farsoon Europe auf der Formnext am Stand E11 in Halle 11.0. Weitere Informationen finden Sie auf der Website von Farsoon HIER.
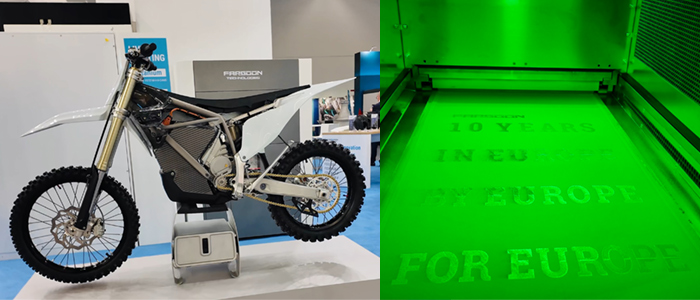
Das Fahrrad von Farsoon (links) und seine Technik (rechts).
FIDENTIS und sein Multi-Material-Metallzahnersatz
Additive Fertigungsanwendungen in der Zahnmedizin sind kein neues Phänomen. Was jedoch ein wenig aus der Norm fällt, ist der 3D-Druck von Metall in diesem Sektor. Hier kommt FIDENTIS ins Spiel. Das aus dem Fraunhofer IGCV ausgegründete Startup hat eine Multi-Material-Laser-Pulverbettfusionslösung entwickelt, die sich besonders gut für die Herstellung von Zahnersatz eignet. Bei dieser Technologie gibt es ein Laserpulverbett und einen Roboter, der zusätzliche Materialien für die gleichzeitige Bearbeitung von zwei oder mehr verschiedenen Legierungen auftragen kann. Für diese spezielle Anwendung wird es aus CoCr mit auf der Reibfläche aufgeschmolzenem Gold hergestellt. Das Unternehmen stellt fest, dass dieses Verfahren 20 Mal schneller und 60 % billiger ist als herkömmliche Methoden. Die Metallanwendung ist so gut angekommen, dass FIDENTIS auch Finalist beim neuen Rookie Award auf der Formnext 2024 ist. Die Besucher können den Multi-Material-Zahnersatz am Stand des Fraunhofer IGCV besichtigen.
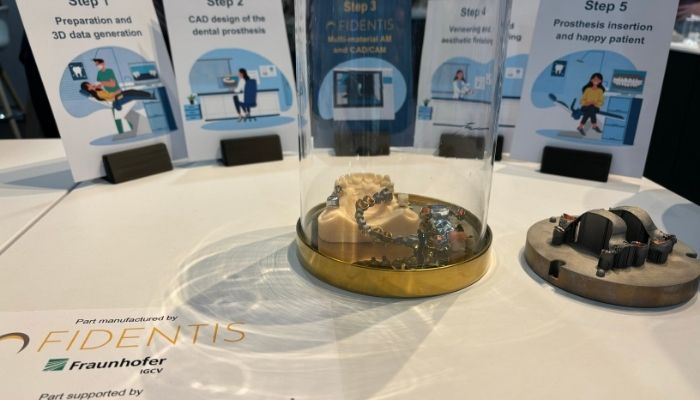
Die auf der Formnext ausgestellten Metallprothesen.
In-Ear-Monitore für Musiker
In-Ear-Monitore sind für jeden Musiker oder Sänger ein unverzichtbarer Bestandteil der Technik, da sie ihm ermöglichen, auf der Bühne zu hören. Aber wussten Sie, dass sie nicht nur im 3D-Druckverfahren, sondern auch aus Metall hergestellt werden können? Auf dem Stand von Bright Laser Technologies (BLT) stehen In-Ear-Monitore im Rampenlicht, die mit Metall-AM, genauer gesagt mit dem BLT A160 500W Metall-3D-Drucker, hergestellt wurden. Die 160 mm x 160 mm x 160 mm großen In-Ear-Monitore aus Titan wurden von der Firma EarFit entwickelt, die sich auf akustische High-Fidelity-Lösungen für Musiker spezialisiert hat, um personalisierten, hochwertigen und kristallklaren Klang für alle zugänglich zu machen. Die additive Fertigung wurde gewählt, um kosteneffiziente, zuverlässige und praktische Lösungen zu schaffen, die noch weiter gehen als die traditionelle Fertigung. Musik in unseren Ohren!
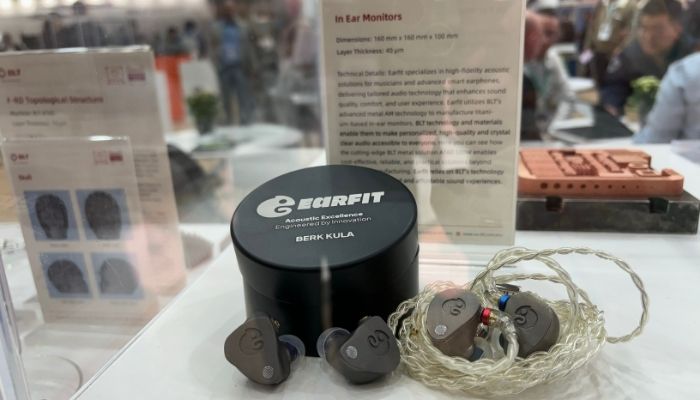
Die In-Ear-Monitore aus Titan am Stand der BLT.
Renishaws Fahrrad mit Olympia-Medaille
Paris 2024 mag vorbei sein, aber auf der Formnext können Sie immer noch eine der aufregendsten Anwendungen der additiven Fertigung sehen, die von der Veranstaltung kommen. Der britische Hersteller Renishaw zeigt das Bahnrad, das zusammen mit Lotus Engineering und Hope Technology für British Cycling entwickelt wurde und dazu beitrug, bei den diesjährigen Olympischen Spielen acht Medaillen zu gewinnen. Es ist für uns besonders interessant, weil es Teile enthält, die mit Renishaws RenAM 500Q aus Titan 3D-gedruckt wurden. Dabei handelt es sich vor allem um die Sattelstütze und die Kurbel, aber auch kleinere Komponenten wie eine Sitzbrücke und Ausfallenden wurden 3D-gedruckt. Die Fahrradkurbel wurde aus Ti6Al4v hergestellt und mit einer internen Gitterstruktur versehen, um die Festigkeit des Teils zu erhalten und gleichzeitig die Anforderungen an das Gewicht des Fahrrads zu erfüllen. Das Fahrrad zeigt eindrucksvoll, wie der 3D-Druck zur Verbesserung der Ausrüstung im Radsport eingesetzt werden kann.
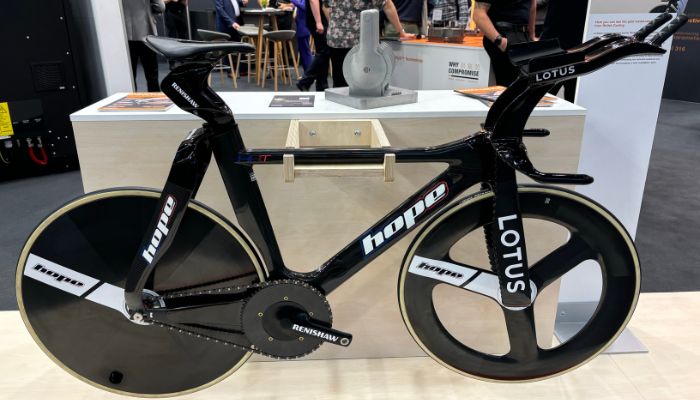
Das mit der Goldmedaille ausgezeichnete Fahrrad mit der Metallkurbel dahinter.
Finnlands größtes 3D-gedrucktes Metallteil
Als die nordischen Länder auf der Formnext 2023 im Rampenlicht standen, haben wir gesehen, wie AM in dieser Region wächst. Und jetzt sind sie mit einem neuen Pavillon in Halle 11.1 auf der Formnext 2024 zurück, und hier können Sie eine relativ bemerkenswerte Anwendung finden. Dieser Druckbehälter ist nicht nur Finnlands größter 3D-Druck aus Metall, sondern wurde auch nach der Druckbehälternorm EN 13445-3 getestet. Bemerkenswert ist, dass das 300 kg schwere Teil aus WAAM und säurebeständigem Edelstahl hergestellt wurde. Das Teil hat einen Durchmesser von 900 mm und eine Höhe von 1600 mm und hielt in den Tests bis zu einem Druck von 111 bar stand, eine unglaubliche Leistung, wenn man bedenkt, dass es ursprünglich für einen Betriebsdruck von 10 bar ausgelegt war. Es ist das Ergebnis der Zusammenarbeit zwischen ANDRITZ Savonlinna Works Oy und dem FAME-Ökosystem mit den von der LUT-Universität durchgeführten zerstörungsfreien und zerstörenden Tests.
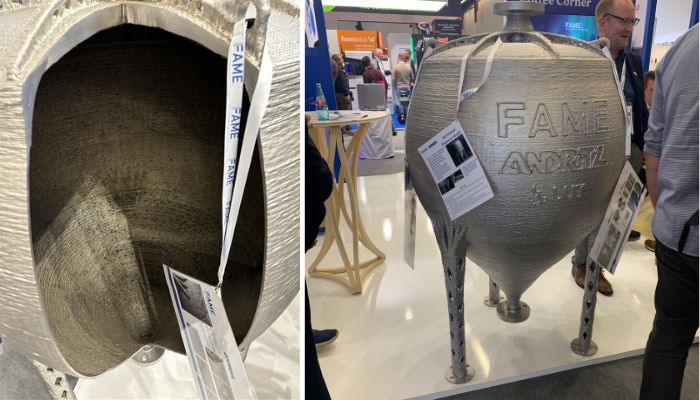
Der Teil, der die Innenseite (links) und die Außenseite (rechts) zeigt.
Eplus3D und LEAP 71 zeigen das größte metallgedruckte Raketentriebwerk der Welt
Wenn wir an Metall-AM-Teile denken, kommt uns natürlich als erstes die Luft- und Raumfahrt in den Sinn. Und auf der Formnext gab es dieses Jahr einige bemerkenswerte Beispiele. Neben der Multi-Materialdüse von InssTek waren wir auch von diesem Raketentriebwerk von Eplus3D und LEAP 71 beeindruckt. Das 200-kN-Triebwerk, von dem die Unternehmen behaupten, es sei das weltweit größte 3D-gedruckte Raketentriebwerk aus Metall, wurde aus einem einzigen Stück gefertigt und ist mehr als 1,3 Meter hoch. Das mit kryogenem Flüssigsauerstoff und Kerosin betriebene Triebwerk ist eine Weiterentwicklung des Noyron TKL-5 Raketentriebwerks, das LEAP 71 im Juni erfolgreich heiß abgefeuert hat, aber offenbar 40 Mal leistungsfähiger ist. Es wurde mit AlSi10Mg, einer Hochleistungsaluminiumlegierung, auf einem Eplus3D EP-M650-1600 Metal Powder Bed Fusion Drucker hergestellt. Besonders faszinierend daran ist, dass er die vielen verschiedenen Teile eines Raketentriebwerks, die Brennkammer, die Düse, die Kühlkanäle, die Verteiler und die Strukturelemente in ein einziges Teil integrieren kann. Dies wird voraussichtlich dazu beitragen, den Zeitaufwand für die Qualitätssicherung zu verringern, da nicht mehr jedes Bauteil einzeln geprüft werden muss.
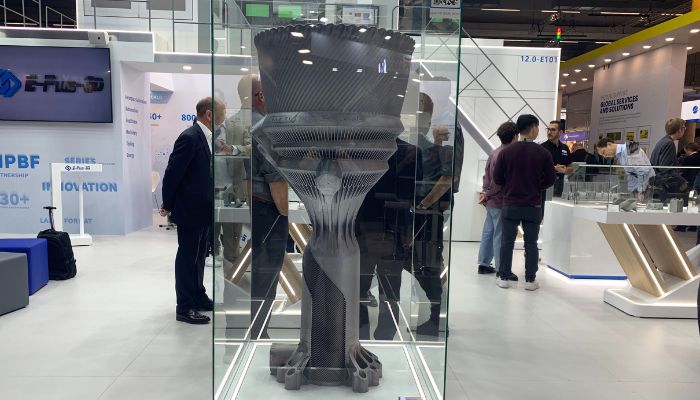
Das auf der Formnext 2024 ausgestellte Raketentriebwerk, eine der spannendsten Anwendungen, die wir gesehen haben.
Ein Stutzen mit fünf Auslässen für Koksbatterien
Die letzte Metallanwendung von Formnext, die wir vorstellen wollen, ist eine Düse für Koksbatterien. Für diejenigen, die sich in dieser Branche nicht auskennen: Eine Koksofenbatterie ist eine Reihe von Öfen, die Kohle zu Koks verarbeiten. Dieser Brennstoff hat einen hohen Kohlenstoffgehalt und ist in Bereichen wie der Eisenerzverhüttung sowie als Brennstoff in Öfen und Schmieden wichtig. Bei diesem Teil handelt es sich um eine von ArcelorMittal und TheSteelPrinters speziell entwickelte Düse mit fünf Auslässen, die so konzipiert wurde, dass fünf einzelne Düsen in einem einzigen Bauteil zusammengefasst werden können, um den Wartungsaufwand für das Teil zu verringern. Es wurde nicht nur maßgeschneidert und verkürzte die Vorlaufzeit auf drei Wochen im Vergleich zu vier Monaten, sondern auch das Material ist bemerkenswert. AdamIQ3167L wurde von TheSteelPrinters, einem 3D-Metalldruck-Dienstleister, entworfen, für LPBF optimiert und wird nun kommerziell vermarktet. Das resultierende Teil wiegt 8 kg und misst 73 x 300 x 228 mm. Sie können es am Stand von ArcelorMittal in Halle 11.0 sehen.
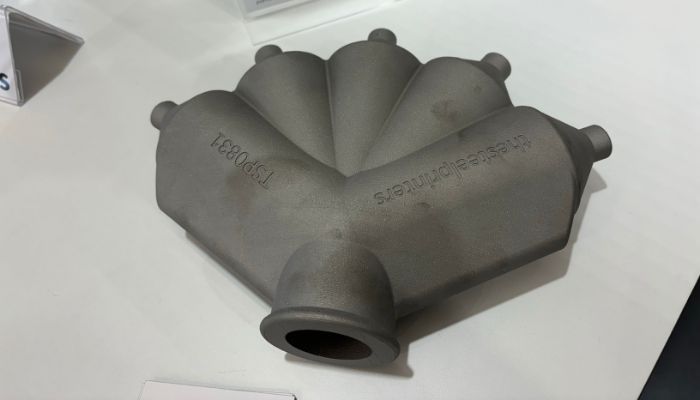
Ein genauerer Blick auf die 5-Düsen-Komponente.
Was halten Sie von den Metallanwendungen, die auf der Formnext 2024 ausgestellt werden? Lassen Sie uns dazu einen Kommentar da, oder teilen Sie es uns auf Facebook oder LinkedIN mit. Möchten Sie außerdem eine Zusammenfassung der wichtigsten Neuigkeiten im 3D-Druck und der additiven Fertigung direkt und bequem in Ihr Postfach erhalten? Dann registrieren Sie sich jetzt für unseren wöchentlichen Newsletter.