Max-Planck-Institut und Fraunhofer erforschen Druck mit Damaszener Stahl
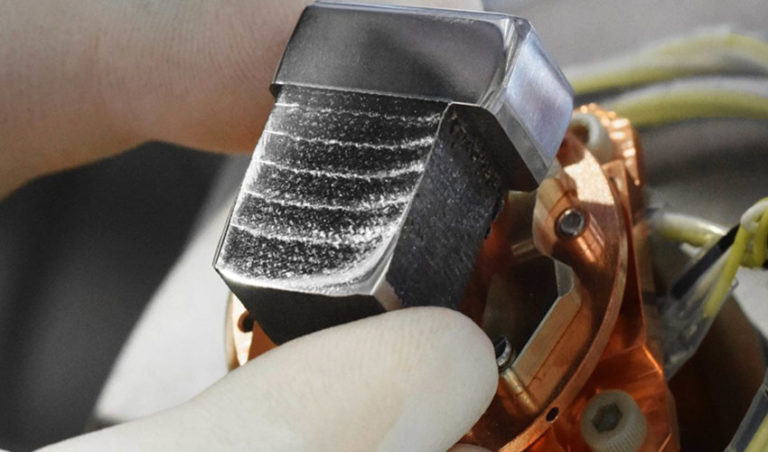
Damaszener Stahl ist eine Stahlsorte, die im Altertum für Schwertklingen verwendet wurde. Nun haben das Max-Planck-Institut für Eisenforschung (MPIE) und das Fraunhofer-Institut für Lasertechnik (ILT) ein Verfahren entwickelt, das den Druck von Damaszener Stahl Schicht für Schicht per 3D-Laserdrucker ermöglicht, wobei jede Schichtdicke einzeln festgelegt werden kann. Damaszener Stahl ist dafür bekannt, dass er besonders fest und zäh ist, weil er aus Schichten verschiedener Eisenlegierungen zusammengesetzt ist, aber zugleich über einen weichen Kern verfügen kann. Dank des entwickelten 3D-Druckverfahrens könnten nun Bauteile oder Werkzeuge für die Luft-und Raumfahrt von den positiven Eigenschaften des Stahls profitieren. Andere Stahlsorten mit vergleichbaren Eigenschaften können bisher nicht für die additive Fertigung verwendet werden, weshalb die Entwicklung des Drucks mit Damaszener Stahl als Verbundwerkstoff einen Umbruch darstellen könnte.
Keltische Schmiede verwendeten verschiedene Eisenlegierungen und konnten so Schwerter mit unterschiedlichen Eigenschaften von weich und zäh bis fest und spröde fertigen. Das Verfahren wurde stetig weiterentwickelt bis schließlich sehr dünne Schichten Eisenlegierung aufgetragen wurden, um die mechanischen Eigenschaften zu optimieren. Aus diesem Grund ist Damaszener Stahl für dessen Maserung bekannt, bei der sich die verschiedenen Legierungen abzeichnen. Heutzutage ist es möglich, aus nur einem einzigen Material mittels feiner Schichtung einen Stahl zu entwickeln, der Damaszener Stahl gleicht.
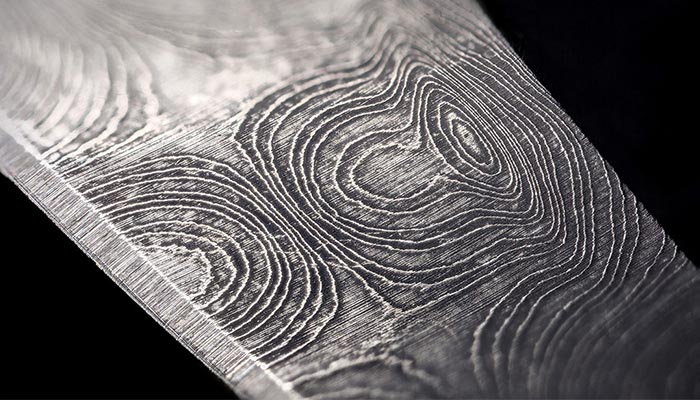
Damaszener Stahl lässt sich an dessen Maserung erkennen (Bildnachweis: Frank Vinken)
Die Entwicklung eines Verbundwerkstoffes mit variabler Schichthärte
Der erste Schritt des Prozesses bestand darin, eine Legierung zu entwickeln, mit der die gewünschten Eigenschaften erreicht werden konnten. Folglich haben die Forscher einen Verbundwerkstoff aus Eisen, Nickel und Titan entwickelt. Um die gewünschten Metallstrukturen erzeugen zu können, haben die Forscher den 3D-Druckprozess nach jeder neu aufgetragenen Schicht für eine gewisse Zeit den Druckprozess pausiert. „Damit können wir bereits während des 3D-Drucks gezielt die Mikrostruktur der einzelnen Schichten verändern, sodass das finale Bauteil die gewünschten Eigenschaften erhält – und dies ganz ohne nachträgliche Wärmebehandlung des Stahls“, erklärt Philipp Kürnsteiner, Postdoktorand am Max-Planck-Institut für Eisenforschung.
Mit Hilfe eines Lasers, wird, ähnlich wie beim Laserschmelz-Verfahrens, schmilzt der Laserstrahl das Material, um es in in die gewünschte Form zu bringen. Kürnsteiner erklärt den Grundgedanken des Laserdruckverfahrens folgendermaßen: „Unter bestimmten Voraussetzungen bilden sich jedoch kleine Nickel-Titan-Mikrostrukturen, die dann für eine besondere Härte sorgen.“ Um dies zu erreichen, pausieren die Forscher den Druckvorgang nach jeder Schicht bis die Temperatur des Metalls auf unter 195 °C gesunken ist. Bei dieser Temperatur findet im Stahl eine Umwandlung der Kristallstruktur statt. Nachdem diese Umwandlung stattgefunden hat, wird die nächste Schicht abgeschieden, welche die erstarrte Schicht folglich erneut erwärmt, was zur Bildung von aushärtenden Ausscheidungen führt. Bei dieser Temperatur findet im Stahl eine Umwandlung der Kristallstruktur statt. Nachdem diese Umwandlung stattgefunden hat, wird die nächste Schicht abgeschieden, die die erstarrte Schicht wieder erwärmt, was zur Bildung von Ausscheidungen führt. Wie Philipp Kürnsteiner erklärt, sind es diese Mikrostrukturen, die den Stahl härten. Wenn die nächste Schicht direkt und ohne Unterbrechung hinzugefügt wird, bleibt die Schicht weicher. Am Ende besteht das geformte Teil aus einem Verbundwerkstoff, der aus Schichten mit unterschiedlichen Eigenschaften besteht, indem sie in ihrer Härte variieren.
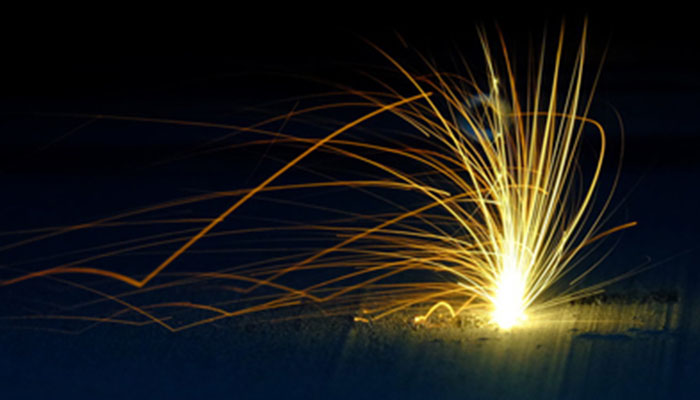
Es können Schichten verschiedener Härtegrade erzeugt werden (Bildnachweis: Philipp Kürnsteiner, Max-Planck-Institut für Eisenforschung GmbH)
Anzufügen ist an dieser Stelle, dass es noch zahlreiche weitere Parameter gibt, die während des 3D-Druckprozesses Einfluss auf die Mikrostrukturen nehmen können. So spielen beispielsweise die Laserenergie, der Fokus und die Druckgeschwindigkeit eine bedeutende Rolle in der Bildung von Ausscheidungen. Den Forschern ist es gelungen, würfelförmige Werkstücke mit Seitenlängen von wenigen Zentimetern als Prototypen für Objekte mit komplexeren Geometrien herzustellen. Eric Jägle, Leiter der Gruppe „Legierungen für die Additive Fertigung“ am MPIE, folgert: „Dank unseres Konzepts der lokalen Kontrolle ließe sich das in einem einzigen Fertigungsschritt realisieren – ganz ohne die bisher für eine Oberflächenhärtung nötigen weiteren Verfahrensschritte.“
*Nachweis Beitragbild: Frank Vinken.
Was denken Sie über die Erzeugung des Damaszener Stahls mittels der additiven Fertigung? Welche Chancen bietet dies für die Luft-und Raumfahrt? Möchten Sie eine Zusammenfassung der wichtigsten Neuigkeiten im 3D-Druck und der Additiven Fertigung direkt und bequem in Ihr Postfach? Registrieren Sie sich jetzt für unseren wöchentlichen Newsletter und folgen Sie uns auf Facebook und Twitter um stets auf dem Laufenden zu bleiben! Außerdem sind wir auch auf LinkedIN und auf Youtube zu finden!
Die Entwicklung in diesem Bericht ist recht interessant, davon hätte ich gerne mehr erfahren.