Cockpit für Full-Flight-Simulator aus dem 3D-Drucker
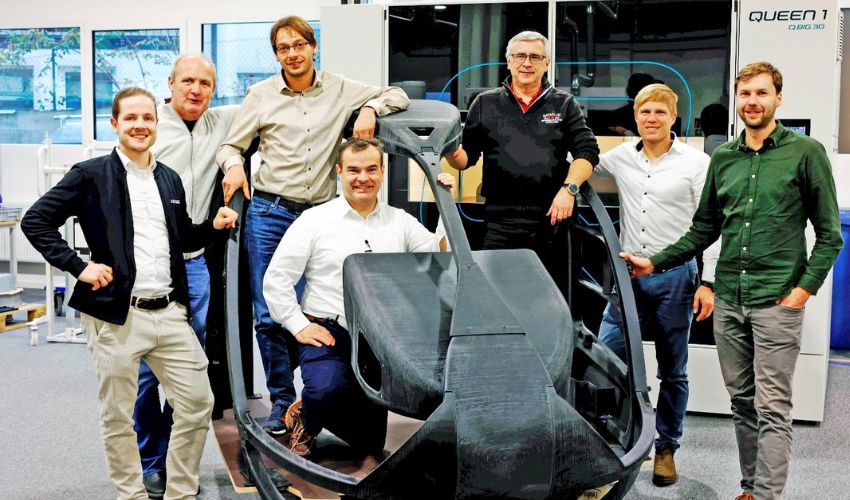
Ein revolutionärer Schritt in Richtung fortschrittlicher Flugsimulation: Während FDM-Drucktechnologie hauptsächlich für Prototypen genutzt wurde, erleben Extrusionsverfahren nun auch eine Anwendung im Bereich der Luft- und Raumfahrt, und zwar durch die VFGF-Systemtechnologie (Variable Fused Granulate Fabrication) von Q.Big 3D. So beauftragte die Reiser Simulation and Training GmbH aus Berg bei Starnberg die Murtfeldt Additive Solutions GmbH (Murtfeldt AS) mit der Fertigung eines Cockpits für einen Full-Flight-Simulator (FFS) von Hubschraubern.
Die Fertigung des Cockpits erfolgte auf einer Queen 1-Anlage von Q.Big 3D bei Murtfeldt AS. Diese werkzeuglose Fertigung mit einem 3D-Extrusionsdrucker ermöglichte zeitnahe Time-to-Market-Strategien. Für den Cockpitrahmen wurde das Material Q.mid GF25 (teilweise aromatisches Polyamid mit 25% Glasfaseranteil) verwendet, was eine hohe Dimensionsstabilität, Temperaturbeständigkeit bis zu 200°C, Steifigkeit und gute Lackierbarkeit ermöglicht. Der matte schwarze Lack des Cockpits wurde verwendet, um Lichtreflexionen im Simulator zu vermeiden.
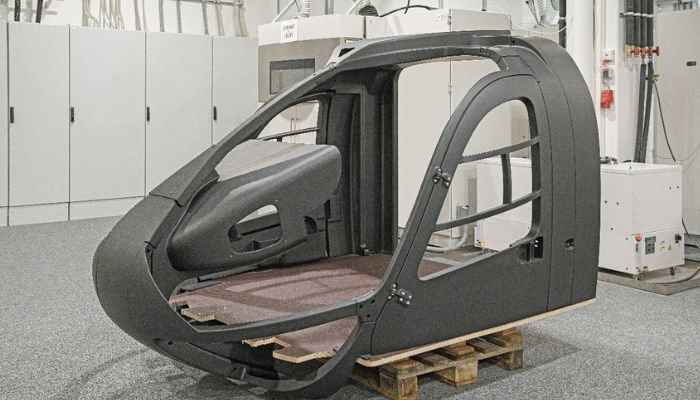
Das Cockpit hat Abmessungen von 2.260 mm (x), 1.780 mm (y) und 1.705 mm (z) und wiegt nur 200 kg dank ressourcensparendem Leichtbau durch 3D-Druck. (Bild: Q.Big 3D)
Die Vorteile der VFGF-Systemtechnologie von Q.BIG 3D bei großen Bauteilen
Die Variable Fused Granulate Fabrication (VFGF) revolutioniert den XXL 3D-Druck mit Granulat, indem sie eine hohe Auflösung dank veränderbarer Düsen für schnelle Bauzeiten und verschiedene Druckmodi anpasst. Das VFGF-Verfahren ermöglicht zudem die Verarbeitung technischer Kunststoffe mit maßgeschneiderten Eigenschaften. Durch die automatische Düsenanpassung können ausgewählte Bereiche in hoher Auflösung gedruckt werden, was gut lackierbare Oberflächen und die Kombination verschiedener Features in einem Baujob zulässt. Die Verwendung von preiswertem Kunststoffgranulat in Rohform sorgt für eine kostengünstige Fertigung ohne teure Werkzeuge und reduziert die Lieferzeit durch eine vollständig digitale Prozesskette vom 3D-Design bis zum fertigen Produkt und der Laminierung.
Im Vergleich zu FDM-Druckern, die aufgrund unwirtschaftlicher Aufbauraten und höherer Materialkosten keine großen Bauteile fertigen können, bietet die Queen 1-Technologie die additive Fertigung übergroßer SLS-Bauteile und hat entscheidende Vorteile, wie das Vermeiden von Funktionalitätseinbußen, ungenauer Passgenauigkeit und die Erschließung neuer Anwendungsbereiche mit hoher Wiederholgenauigkeit und Bauteilqualität. Johannes Matheis, der Geschäftsführer bei Murtfeldt AS, kommentiert: “Mit dieser innovativen Technologie können wir gezielt weitere Anwendungsbereiche erschließen und komplexe, große 3D-Komponenten mit hoher Wiederholgenauigkeit und Bauteilqualität herstellen.“ Mehr dazu finden Sie HIER.
Was halten Sie von der VFGF-Systemtechnologie? Haben Sie das Cockpit aus dem 3D-Drucker bereits gesehen? Lassen Sie uns dazu gerne einen Kommentar da oder teilen Sie uns Ihre Meinung auf Facebook oder LinkedIN mit. Möchten Sie außerdem eine Zusammenfassung der wichtigsten Neuigkeiten im 3D-Druck und der additiven Fertigung direkt und bequem in Ihr Postfach erhalten? Dann registrieren Sie sich jetzt für unseren wöchentlichen Newsletter.
*Bildnachweise: Q.Big 3D