BMW druckt Roboter-Greifer für Produktionssystem
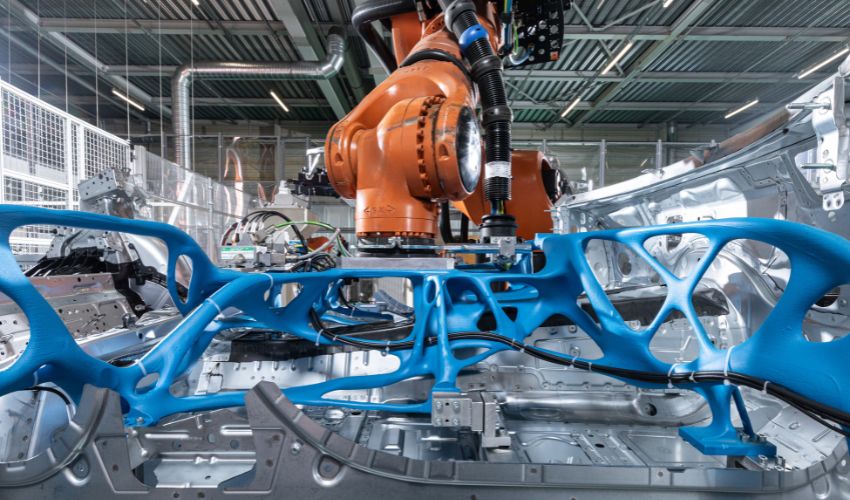
Die additive Fertigung hat bei der BMW Group mittlerweile Tradition. Seit mehr als 30 Jahren schon setzt der Automobilhersteller auf 3D-Druck in der Herstellung von Automobilteilen, Werkzeugen, Arbeitshilfsmitteln und in der Ausbildung. Eine zentrale Rolle bei dieser Entwicklung spielt der „Additive Manufacturing Campus“ in Oberschleißheim. Im vergangenen Jahr konnten dort insgesamt mehr als 300.000 Teile gedruckt werden, wobei verschiedene Verfahren zum Einsatz kamen. In diesem Zentrum ist auch ein großflächiges Greifer-Element per 3D-Druck entstanden, welches Kosten und Gewicht spart, und im Landshuter Leichtbau- und Technologiezentrum zum Einsatz kommt.
Dieser Roboter-Greifer wiegt rund 120 Kilogramm und wird in 22 Stunden gedruckt. Durch das additive Herstellungsverfahren ist das Endprodukt rund 20 % leichter, was positive Auswirkungen auf die Nutzungsdauer der Anlage hat. Bei der Herstellung werden zwei Verfahren sinnvoll kombiniert. Zum einen kommt das SLS-Verfahren zum Einsatz, um die Vakuumgreifer und die Halter der Nadelgreifer zu fertigen. Die großflächige Dachschale und die Tragstruktur werden per Large Scale Printing (LSP) hergestellt. Dieses Verfahren eignet sich aufgrund der Verwendung von Spritzgussgranulat aus recyceltem Kunststoff besonders für die günstige und nachhaltige Herstellung von großen Bauteilen. Dies führt dazu, dass der CO2-Ausstoß in der Fertigung des Greifers um 60 % reduziert werden konnte.
„Der vermehrte Einsatz von Additive Manufacturing im BMW Group Produktionssystem bringt zahlreiche Vorteile,“ erklärt Jens Ertel, Leiter des Additive Manufacturing Campus in Oberschleißheim, und fährt fort: „Wir sind damit zum Beispiel in der Lage, schnell, kostengünstig und flexibel selbst Produktionshilfsmittel und Handling-Greifer zu produzieren, die wir jederzeit individuell an die Bedürfnisse anpassen und dazu gewichtsoptimiert gestalten können. Weniger Gewicht ermöglicht höhere Geschwindigkeiten am Band, verkürzte Taktzeiten und reduzierte Kosten. Außerdem können mittelfristig kleinere Roboter eingesetzt werden, was ebenfalls CO2‑Emissionen und Kosten verringert.“
Damit gibt sich BMW noch nicht zufrieden und so wurde im Sommer letzten Jahres eine noch leichtere Greifer-Version eingeführt. Dabei handelt es sich um einen bionischen Roboter-Greifer. Diese Generation an Greifern wurde topologisch optimiert und weist eine Dachschale aus dem LSP-Drucker auf, Sauger, die per SLS gefertigt werden, und die bionisch optimierte Tragstruktur. Für diese Struktur wird im Sandguss eine Form gefertigt, die dann mit flüssigem Aluminium gefüllt wird. Durch die Kombination an Verfahren konnte das Gewicht nochmals verringert werden – und zwar um weitere 25 %. Da die Greifer vor allem in der Fertigung von CFK-Dächern für die Modelle von BMW M zum Einsatz kommen, kann die Anzahl der nötigen Roboter reduziert werden. Wurden beim vorherigen Modell noch drei Roboter benötigt, erfordert die überarbeitete Greifer-Version durch das geringere Gewicht nur noch einen Roboter zur Fertigung der CFK-Dächer. Mittlerweile setzt das Werk in Landshut dafür auf Doppel-Greifer, welche individuell im 3D-Druck gefertigt werden.
Doch BMW geht noch einen Schritt weiter. Im Werk in München werden nun bionische Greifer genutzt, welche die Bodengruppe eins BMW i4 greifen und bewegen können. Dieses Greifer-Modell ist nochmals überarbeitet und wiegt „nur“ 110 Kilogramm. Im Vergleich zum vorherigen, konventionellen Modell wird so eine Einsparung von 30 % an Gewicht erzielt. Dafür setzt die BMW Group auch auf das Software-Tool Synera, in welches sie auch investiert hat. Diese Software-Plattform findet bei BMW eine breite Anwendung, da sie eine schnelle und effiziente Optimierung von Bauteilen möglich macht.
Markus Lehmann, Leiter Anlagentechnik und Robotik im BMW Group Werk München ordnet ein: „Im Werk München bauen wir den Einsatz von additiv gefertigten Produktionshilfsmitteln kontinuierlich weiter aus. Im Bereich der Greifer- und Handlingssysteme nutzen wir den 3D-Druck, um unsere etablierten Greifer mit individuellen, gedruckten Anbauelemente auszustatten und ersetzten bereits komplette Greifersysteme durch hochintegrierte und gewichtsoptimierte Tragstrukturen. Beim Handling der kompletten BMW i4 Bodengruppe konnten wir so das Gewicht um 30 Prozent, für den kompletten Greifer um über 50 kg, verringern und entsprechend die Lebensdauer unserer Anlagen verlängern.“ Mehr dazu finden Sie HIER.
Was halten Sie von den additiv gefertigten Roboter-Greifern von BMW? Lassen Sie uns dazu einen Kommentar da, oder teilen Sie es uns auf Facebook oder LinkedIN mit. Möchten Sie außerdem eine Zusammenfassung der wichtigsten Neuigkeiten im 3D-Druck und der additiven Fertigung direkt und bequem in Ihr Postfach erhalten? Dann registrieren Sie sich jetzt für unseren wöchentlichen Newsletter.
*Bildnachweise: BMW Group