Die additive Fertigung auf die Straße bringen: Wie BASF Forward AM Lösungen für die Automobilindustrie ermöglicht
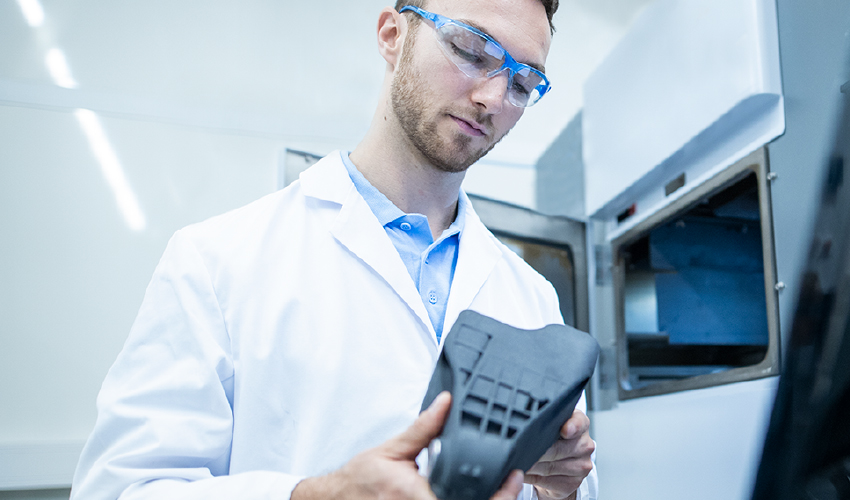
Die Automobilindustrie ist zweifelsohne einer der Sektoren, der additive Fertigungstechnologien am häufigsten einsetzt. Während die additive Fertigung zunächst für die Entwicklung von Prototypen eingesetzt wurde, hat sich der Anwendungsbereich mittlerweile auch auf die Herstellung von Endanwendungsteilen ausgeweitet. Laut einer von SmarTech Publishing veröffentlichten Studie wird erwartet, dass dieser Markt bereits im Jahr 2023 einen Umsatz von 5,3 Milliarden Dollar und im Jahr 2028 von 12,4 Milliarden Dollar erreichen wird.
In den nächsten 10 Jahren dürfte dieses Segment zum größten Markt in der weltweiten 3D-Druckindustrie werden und das so genannte « Additive Automotive » erreichen. Einer der Akteure, der dieses Wachstum wesentlich vorantreibt, ist Forward AM. Die Marke wurde vom deutschen Unternehmen BASF als Spezialist für die additive Fertigung gegründet. Als technologie-unabhängiger Materialexperte, beraten und begleiten sie Unternehmen, die in den 3D-Drucksektor einsteigen wollen, um automobile Innovationen zu erreichen.
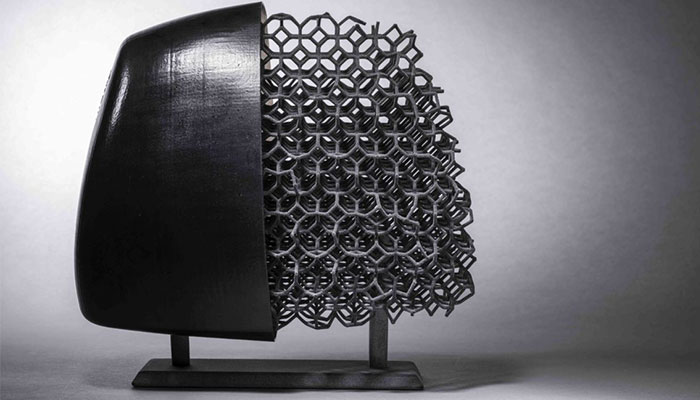
Die Entwicklung der Materialien hat die Einführung der additiven Fertigung im Automobilbereich gefördert | Bildnachweis : BASF Forward AM
Forward AM wurde mit dem Ziel gegründet, Hochleistungsmaterialien für den 3D-Druck zu entwickeln. Die 2017 ins Leben gerufene Division verfügt bereits heute über eine der größten Materialpaletten in diesem Sektor. Aufgrund ihres Wissens über Materialien und deren industrielle Anwendung haben sie auch Nachbearbeitungs- und Beratungslösungen für Unternehmen in allen Industriezweigen entwickelt, die ihre Anwendungen im Bereich der additiven Fertigung auf die nächste Stufe bringen wollen. Die in Paris angesiedelte BASF-Marke Sculpteo bietet auch für den industriellen 3D-Druck-Services online für die On-Demand-Produktion von Prototypen, individuellen Produkten sowie für die Herstellung von Kleinserien an.
Die additive Fertigung in der Automobilindustrie
Viele Automobilhersteller haben bereits damit begonnen, additive Fertigungstechnologien von Audi, BMW oder sogar Ferrari für ihre Formel-1-Fahrzeuge einzusetzen. Die Anwendungen der additiven Fertigung im Automobilsektor sind vielfältig, aber können in folgende drei Hauptgruppen eingeteilt werden:
- Prototyping: Auch heute noch das am weitesten verbreitete Anwendungsgebiet, da die additive Fertigung die schnelle Entwicklung und Erprobung verschiedener Teile ermöglicht.
- Endanwendungsteile: Entstanden vor einigen Jahren dank der Material- und Hardwareentwicklung. Dem neuesten “State of 3D Printing” Report von Sculpteo zur Folge, haben 50% der Unternehmen, die im letzten Jahr den 3D-Druck verwendet haben, dies auch für die Herstellung von Endanwendungsteilen getan.
- Jigs & Fixtures: Allgemein als Werkzeugteile bekannt, beschleunigen sie die Produktion. Jigs sind Montagewerkzeuge, die das Schneid- oder Bearbeitungswerkzeug in einer Produktionslinie führen, und Fixtures sind Montagewerkzeuge, die das Werkstück mit dem Maschinenbett genau an der gewünschten Stelle halten.
Die additive Fertigung kann für alle Arten von Fahrzeugteilen verwendet werden | Bildnachweis: BASF Forward AM
Der Einsatz von 3D-Druck-Technologien ermöglicht eine höhere Produktion und niedrigere Kosten, hat aber auch die Tür zur Massenanpassung geöffnet, so dass OEMs (Original Equipment Manufacturers) einzigartige Teile anbieten und gleichzeitig den Endverbraucher mit maßgeschneiderten Teilen für ihre Autos erreichen können.
Forward AM und sein Engagement für die Automobilindustrie
Obwohl sich Forward AM auf 3D-Druck Materialien spezialisiert, sammelte das Unternehmen durch die Zusammenarbeit mit verschiedenen Herstellern und den mit diesen Herstellern zusammenarbeitenden OEMs zahlreiche Erfahrungen in der Automobilindustrie. Um Endanwender zu unterstützen, bietet das deutsche Unternehmen Dienstleistungen in den Bereichen Simulation, virtual Engineering und Nachbearbeitung an. So begleitet das Unternehmen die Anwender bei der Einführung von additiver Fertigung Schritt für Schritt und ermöglicht eine erfolgreiche Implementierung. In der Tat war BASF Forward AM an zahlreichen Projekten im Automobilsektor beteiligt; zwei davon haben unsere Aufmerksamkeit besonders auf sich gezogen:
Forward AM und Daimler: Entwicklung von Motorträgern in kürzerer Zeit
Die Beziehung zwischen Daimler und Forward AM geht viele Jahre zurück. Sie begann als der deutsche Autobauer den Entwicklungsprozess von Motorenteilen mit einem lasttragenden Motorträger beschleunigen wollte. Um den Übergang vom Spritzguss zu 3D-Druck zu ermöglichen, begann die Zusammenarbeit mit Materialtests. Ein klares Ziel bestand darin, die Kosten durch die Zeit der Entwicklungszyklen zu senken.
Nach zahlreichen Tests, fiel die Wahl auf das leistungsfähigste Material Ultrasint® PA6 MF, ein Polyamid mit mechanischer und thermischer Stabilität, das mit der Powder Bed Fusion (PBF)-Technologie anzuwenden ist. Mit dem Einsatz von Ultrasint® PA6 MF konnten in kurzer Zeit Prototypen entwickelt werden. Die Zeitersparnis war im Vergleich zur Entwicklung im Spritzgussverfahren beträchtlich.
Forward AM und OECHSLER: Optimierung des Designs von Motorradsätteln
OECHSLER, ein Spezialist für Polymerverarbeitung, und Forward AM haben ihre Kräfte gebündelt, um Motorradsattel der neuesten Generation zu entwickeln. Angestrebt wurde die Entwicklung eines Prototyps, um das Design des Motorradsattels zu verbessern. Dank der Designvorteile des 3D-Drucks konnte der Sattel in einem Stück mit einer Gitterstruktur gefertigt und die Fertigungs- und Montagezeit reduziert werden. Verwendet wurde Ultrasint® TPU01 von Forward AM, ein Material, das sich ideal für die Herstellung von Teilen eignet, die eine ausgezeichnete langfristige Stoßdämpfung und Flexibilität erfordern. Seine Eigenschaften machen dieses Pulver perfekt für die Serienentwicklung mit der HP Multi Jet Fusion-Technologie. Der Montageprozess war in der Tat viel einfacher und kürzer. Es konnte auf Klebeprozess verzichtet werden, und die obere Abdeckung musste nicht mit Metallklammern befestigt werden. Darüber hinaus wurde das Gewicht des Sattels um 25 % reduziert, was mit einer Materialreduzierung einhergeht.
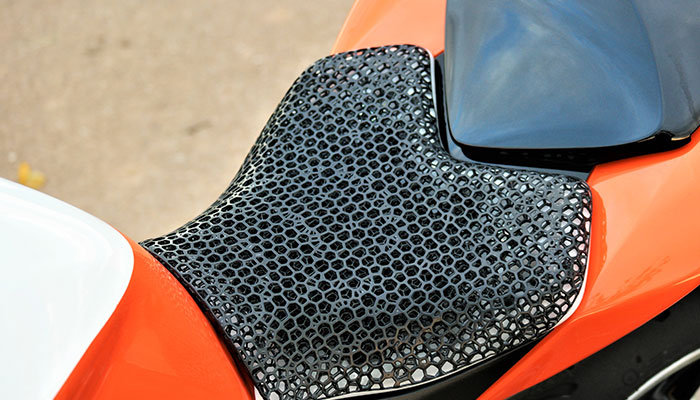
Optimierter Sattel dank additiver Fertigung und Materialien | Bildnachweis: BASF Forward AM
Forward AM hat an verschiedenen Automobilprojekten mitgearbeitet, um es einer wachsenden Anzahl an Unternehmen zu ermöglichen, die Vorteile des 3D-Drucks durch die erfolgreiche Implementierung der Technologie zu nutzen. Weitere Informationen finden Sie in einem vertiefenden Webinar über ihre Lösungen für die Automobilindustrie oder kontaktieren Sie sie HIER.