Welche Anwendungen gibt es für die additive Fertigung im Verteidigungssektor?
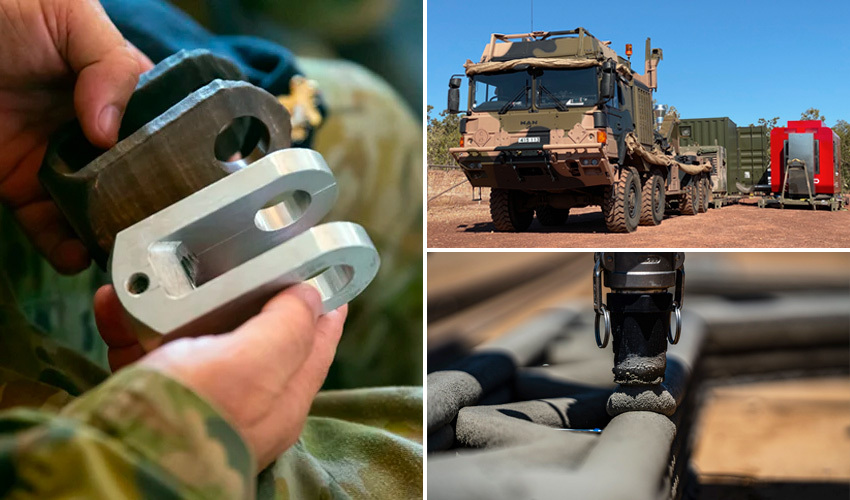
Die additive Fertigung ist in vielen Sektoren weit verbreitet, unter anderem in der Schifffahrt, der Luft- und Raumfahrt und der Automobilindustrie. Es sollte daher nicht überraschen, dass sie auch im Verteidigungssektor weltweit zunehmend eingesetzt wird. Es wird erwartet, dass die additive Fertigung im Verteidigungssektor bis 2027 einen Wert von 1,7 Mrd. US-Dollar haben wird, was die Bedeutung dieser Technologien verdeutlicht. In Anbetracht der Tatsache, dass im militärischen Bereich Geschwindigkeit, geringeres Gewicht und niedrigere Kosten von größter Bedeutung sind, spielt die additive Fertigung sicherlich eine Rolle. Wir haben uns einige der interessantesten Anwendungen für den 3D-Druck im Verteidigungssektor genauer angesehen, die im Folgenden in keiner bestimmten Reihenfolge aufgeführt sind.
ExOne und ihre Militär Pods
Mit dem Ziel die Entwicklung von starken und robusten 3D-Druck Fabrik-Pods zu beschleunigen, hat sich ExOne bei dieser Aufgabe mit der Zusammenarbeit mit mehreren Partnern mit eingebracht. Konkret ging es dabei um den Auftrag der Defense Logistics Agency (DLA), der einen Wert von 1,6 Mio. USD aufwies. Hierbei ging es um die Binderjet-Technologie von ExOne für den militärischen Einsatz zu nutzen, da sie auf Grund ihrer Geschwindigkeit, Flexibilität der Materialien und der einfachen Handhabung optimal die kritischen Bedürfnisse des Militärs deckt. Der speziell für das Militär entwickelte 3D-Drucker soll mehr als 20 Metall-, Keramik- und andere Pulvermaterialien im Binderjetting-Verfahren verarbeiten können – daneben soll das einzigartige Gehäuse und andere Merkmale ihn perfekt für ein militärtaugliches Produkt machen.
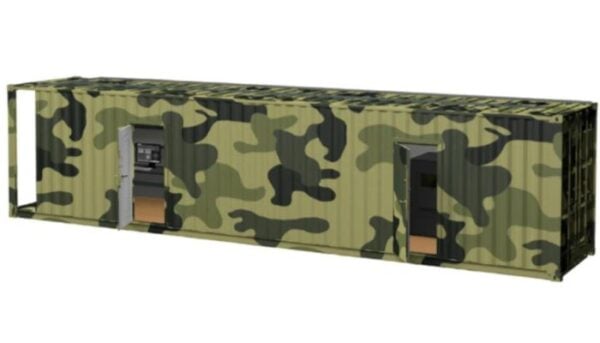
Bild: ExOne
3D-gedruckte Kaserne
Das 3D-Konstruktionsunternehmen ICON ist bereits dafür bekannt, Projekte mit dem Militär durchzuführen. Bei diesem Projekt hat sich das in Austin ansässige Unternehmen mit dem Texas Military Department, Logan Architecture und Fort Structures zusammengetan, um die größte 3D-gedruckte Struktur Nordamerikas zu schaffen: eine Trainingsbaracke im Camp Swift Training Center in Bastrop, Texas. Mithilfe des Vulcan-Konstruktionssystems von ICON, einem Tablet-gesteuerten Roboterdrucker, der mit zementbasiertem Material arbeitet, gelang es der Zusammenarbeit von Unternehmen und Militär, die erste 3D-gedruckte Kaserne zu bauen, in der Soldaten wohnen können. Die endgültige Konstruktion besteht aus einem 3.800 Quadratmeter großen Gebäude, in dem bis zu 72 Soldaten oder Luftwaffenangehörige untergebracht werden können, um sich auf ihre nächsten Einsätze vorzubereiten!
Ersatzteile in einem einsatzbereiten gepanzerten Fahrzeug
Die australische Armee nutzte die additive Metallfertigung und insbesondere die von SPEE3D entwickelten Lösungen, um ein Dutzend Ersatzteile für eines ihrer gepanzerten Fahrzeuge zu konstruieren. Diese wurden für den Einsatz im Feld getestet und zertifiziert, wodurch die Beweglichkeit der australischen Armee verbessert werden konnte. Zu den gedruckten Komponenten gehörte beispielsweise eine Radlagerabdeckung, die in nur 29 Minuten mit Gesamtkosten von 100 australischen Dollar erstellt wurde. Die in diesem Fall verwendete Maschine ist die WarpSPEE3D, die ein Druckvolumen von 1000 x 700 mm und eine Geschwindigkeit von 1 Kilogramm pro Minute bietet. Durch die Hinwendung zur additiven Fertigung im Verteidigungssektor ist das Militär in der Lage, die Ausfallzeiten seiner gepanzerten Fahrzeuge zu verringern und so besser auf Notsituationen reagieren zu können.
General Lattice und seine Helme für das US-Militär
Das Unternehmen für 3D-Designsoftware General Lattice und die US-Armee haben einen Vertrag unterzeichnet, um die Aufpralldämpfung der Kampfhelme der Armee durch 3D-Druck und fortschrittliche Gittergeometrien zu verbessern. Im Rahmen dieses Projekts wird das Unternehmen eine Reihe von Prognosemodellierungswerkzeugen entwickeln, um Materialien für den Helm zu entwerfen und herzustellen. Um den Schutz der Soldaten im Einsatz zu verbessern und die Überlebenswahrscheinlichkeit nach einem Kopfaufprall zu erhöhen, werden die 3D-gedruckten Materialien in realen Umgebungen getestet, um die Leistungsanforderungen des Soldier Development Command’s Soldier Centre zu überprüfen.
additive Fertigung im Verteidigungssektor: Der größte Metall-3D-Drucker
Das US-Militär ist von den Vorteilen der additive Fertigung im Verteidigungssektor so überzeugt, dass es im vergangenen Jahr ankündigte, den größten Metall-3D-Drucker der Welt zu bauen. Das U.S. DEVCOM Army Ground Vehicle Systems Center arbeitet am Bau des Druckers mit Hilfe von ASTRO America, Ingersoll Machine Tool, Siemens und MELD Manufacturing im Rock Island Arsenal – Joint Manufacturing and Technology Center. Der Drucker wird Teil des Jointless Hull Project sein, dessen Ziel es ist, monolithische (einteilige) Rümpfe für Kampffahrzeuge zu drucken. Bei der Ankündigung wurde geschätzt, dass das Projekt etwa 14 Monate dauern würde und der Drucker am Ende in der Lage sein würde, Metallteile zu drucken, die 30 Fuß lang, 20 Fuß breit und 12 Fuß hoch sind. Obwohl es in letzter Zeit keine Neuigkeiten dazu gab, ist es wahrscheinlich, dass das Projekt in naher Zukunft abgeschlossen werden kann.
Astro America entwickelt 3D-gedruckten Kampffahrzeugrumpf
Die Applied Science & Technology Research Organization, auch bekannt als ASTRO America, wurde von der US-Armee für das „Jointless Hull Project“ ausgewählt. Dieses Programm wird vom US -Verteidigungsministerium begünstigten Institut für Fertigungsinnovation unterstützt und ist Teil eines Bestrebens, mithilfe des 3D-Drucks ein Rumpfwerkzeug für Kampffahrzeuge zu entwickeln und bereitzustellen. Sie hoffen so die Herstellungszeit verringern zu können und gleichzeitig die Produktionskosten zu senken, während sie das Gewicht des Fahrzeuges reduzieren und die Leistung und dessen Überlebensfähigkeit steigern.
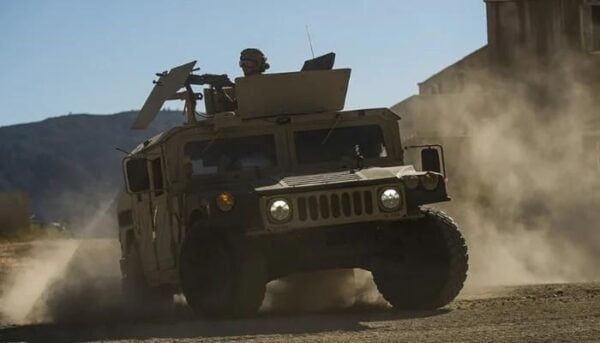
Bild: ASTRO America
Additive Fertigung im Verteidigungssektor: Eine 3D-gedruckte Landebahn
Eine weitere Anwendung der additiven Fertigung im Verteidigungssektor stammt von ITAMCO (Indiana Technology and Manufacturing Companies), die mit Hilfe des 3D-Drucks eine Start- und Landebahn für militärische Expeditionsflugplätze entwickelt haben. Diese Landebahnmatten sind ein wesentlicher Bestandteil von Expeditionsflugplätzen (EAF). Ihre Aufgabe ist es, auf den schwächsten Bodenoberflächen eingesetzt zu werden und die Landung und den Start von Militärflugzeugen zu ermöglichen. Bislang wurde eine tragbare Start- und Landebahn aus Aluminiumbrettern verwendet, die jedoch veraltet war, so dass eine innovative Lösung gefunden werden musste. Der M290 3D-Drucker der deutschen Firma EOS wurde eingesetzt, um ein wesentlich leichteres und haltbareres Modell für die militärische Ausrüstung der US-Luftwaffe herzustellen.
3D-gedruckter U-Boot-Rumpf
Im Laufe der Jahre hat der Verteidigungssektor Wege gefunden, den 3D-Druck in vielen Bereichen einzusetzen – zu Lande, in der Luft und auf See. Mit diesem neuesten Projekt taucht die US-Armee buchstäblich in ein für den 3D-Druck relativ unbekanntes Gebiet ein: Unter dem Meer. Für dieses neue Projekt hat sich das Oak Ridge National Laboratory (ORNL) mit dem Disruptive Technology Lab der US-Marine zusammengetan, um einen 3D-gedruckten U-Boot-Rumpf zu entwickeln – den ersten in der Militärgeschichte. Mit Hilfe der FDM Big Area Additive Manufacturing (BAAM)-Technologie des ORNL produzierte das Team einen 30-Fuß-Konzeptrumpf mit sechs Abschnitten aus Kohlefaserverbundwerkstoffen, der schneller und kostengünstiger hergestellt werden konnte als mit herkömmlichen Fertigungsmethoden. Obwohl sich das Projekt noch in der Erprobungsphase befindet, stehen die Zeichen gut, dass bald weitere 3D-gedruckte U-Boote durch die Weltmeere tauchen werden.
Marine und ihr 3D-gedrucktes Werkzeug
Die US-amerikanische Marine macht sich ebenfalls die additive Fertigung zu Nutze. Marineinfanteristen haben dank des 3D-Drucks die Möglichkeit entdeckt, innovatives Werkzeug für ihre Fahrzeugwartungen herzustellen. Gezielt geht es hierbei um die Zusammenarbeit der Marine Corps System Command mit dem Supply Battalion und Industriepartnern zur Herstellung von additiv hergestellten Vorrichtungen zum Entfernen von Lenkrädern aus Metall – ein häufiges Problem, welches es oft bei der Fahrzeugwartung der Marine zu lösen gilt! Mit den Vorteilen der verkürzten Wartungszeit und erhöhten Einsatzbereitschaft profitiert man sehr stark von der additiven Fertigung, bedenkt man vor allem, dass die eigentliche Wartezeit für solche Teile rund 25 Tage beträgt.
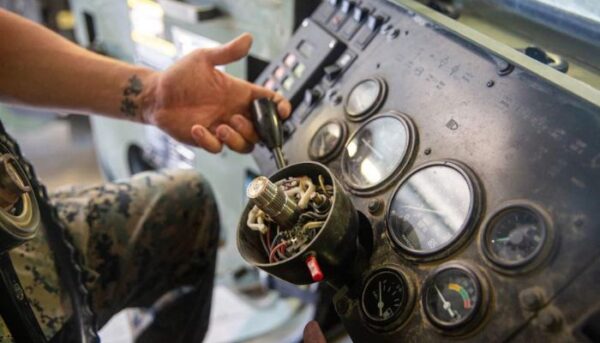
Bild: US Marine
Die US-Marine und die additive Fertigung im Verteidigungssektor
Die US-Marine führt bereits seit einigen Jahren mehrere Projekte zur additiven Fertigung im Verteidigungssektor durch. Ziel ist es, die Agilität und Effizienz der Teams zu verbessern, die auf Missionen mitten im Ozean gehen, insbesondere wenn es um die Herstellung von Ersatzteilen geht. Aus diesem Grund hatte die Naval Postgraduate School (NPS) in die Xerox ElemX Metallmaschine investiert. Sie verwendet sie, um Ersatzteile für ihre U-Boote und Schiffe, aber auch Werkzeuge zu entwerfen. So kann sie sich auf eine viel kürzere Lieferkette verlassen und Bauteile nach Maß herstellen.
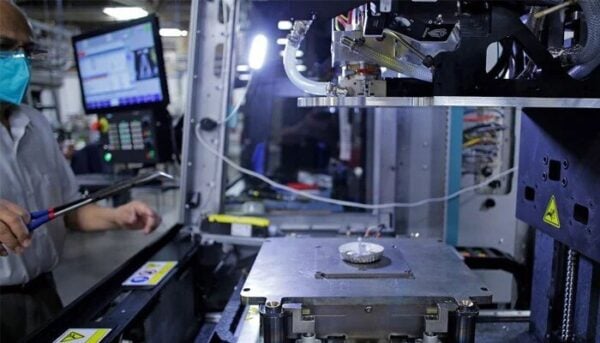
Bild: Xerox
Die NPS ist nicht die einzige, die 3D-Druckprojekte im maritimen Bereich startet. Das Unternehmen MatterHackers hat einen Fünfjahresvertrag mit der US-Marine abgeschlossen, um ihr alle benötigten 3D-Geräte, aber auch Schulungen und Wartungsarbeiten zur Verfügung zu stellen. MatterHackers unterstützte die Marine bei der Einführung von Ultimaker S5 3D-Druckern, damit sie maßgeschneiderte Ersatzteile und andere Anwendungen entwerfen kann.
Spanische Luftwaffe modernisiert ihre Prozesse mit 3D-Druck
Die additive Fertigung verleiht den hergestellten Teilen Eigenschaften wie Härte, Festigkeit und Leichtigkeit. Dank der internen Faserverstärkung wurden verschiedene Werkzeuge und Endteile entwickelt, die den anspruchsvollen Leistungsbedingungen in einem Umfeld standhalten, in dem die Belastung der Komponenten sehr hoch ist und in dem es keinen Spielraum für Fehler gibt. In Madrid erklärt der Leiter der Hubschrauberwerkstatt der spanischen Luftwaffe, dass heutzutage bei jeder Anforderung an ein Teil die additive Fertigung in Betracht gezogen und die traditionelle Fertigung vermieden wird. Erwähnenswert sind beispielsweise ein Messgerät zur Leckagekontrolle für das Fahrwerk des Hubschraubers oder ein maßgeschneiderter Schlüssel für den Hauptrotor des Hubschraubers.
Additive Fertigung im Verteidigungssektor: The Future Energetics Project
Das Future Energetics Project aus Großbritannien arbeitet in den Bereichen der Forschung, Sprengstoffversuchen, neuartige Energetikherstellung, Explosionsmodellierung, chemischen Synthese, thermischen Charakterisierung und Gefahrentests. Die Ziele des Projektes bestehen darin, neue energetische Materialien und diagnostische Methoden zur Validierung neuer Materialien zu entwickeln. Die additive Fertigung wird dabei zur Entwicklung neuer Sprengstoffformulierungen eingesetzt. Dies bietet potenziellen Anwendern zahlreiche Vorteile, darunter die Reduzierung von Lager- und Transportkosten und eine verbesserte Leistung. Ladungen können genau auf die Anforderungen abgestimmt und in neuartigen und komplizierten Designs hergestellt werden, was zuvor undenkbar gewesen wäre. Zur Herstellung wird dabei ein LabRAM-Resonanz-Akustikmischer verwendet, welcher akustische Energie anstelle von physischen Klingen zum Mischen von Materialien verwendet, was den Prozess sicherer macht. Das 3D-Druckprojekt befindet sich derzeit noch in der Testphase.
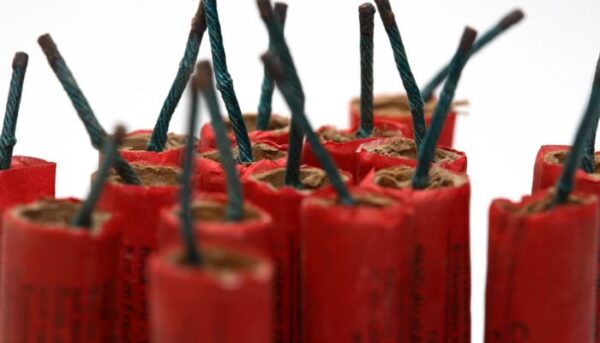
Bild: Fotolia.com
Die Partnerschaft zwischen der US Army und der Central Florida University
Die US-Armee arbeitet regelmäßig mit Unternehmen zusammen, um die Technologie nach und nach zu übernehmen, aber die US-Truppen gehen auch Partnerschaften mit Universitäten ein. Vor kurzem gelang es Wissenschaftlern der Central Florida University, eine Magnesiumlegierung namens WE43 im 3D-Druckverfahren herzustellen. Es ist kein Zufall, dass sich die Forscher für dieses Material entschieden haben. Da amerikanische Soldaten gezwungen sind, extrem schwere Taschen und Ausrüstungsgegenstände zu tragen, ist es heute notwendig, sie von diesem Gewicht zu entlasten. Mit Hilfe von WE43 und dem Laser-Pulverbett-Schmelzverfahren könnten die US-Armee und die Universität Central Florida die Lösung gefunden haben.
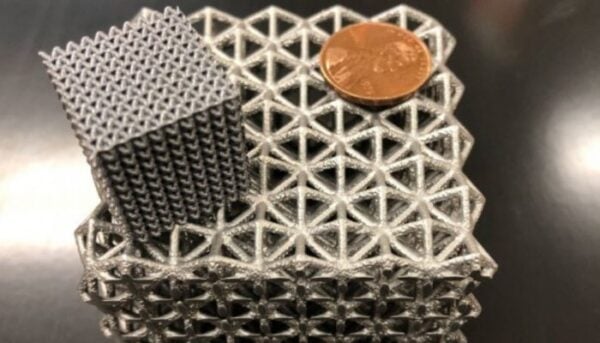
Bild: U.S. Army DEVCOM Army Research Laboratory
Ein Schiffspropeller aus dem 3D-Drucker
Das bekannte französische Unternehmen Naval Group setzt nun schon seit mehreren Jahren den 3D-Druck ein, um die unterschiedlichsten Anforderungen zu erfüllen. Im Jahr 2021 hat die Naval Group dank der additiven Fertigung und insbesondere des WAAM-Verfahrens (Wire Arc Additive Manufacturing) einen Propeller in 3D gedruckt. Der Propeller, der aus fünf 200 kg schweren Flügeln besteht, wurde anschließend auf dem Minenjagdschiff Andromeda eingesetzt. Die Projektteams erklärten, dass sie mithilfe der Technologie die Bauzeit drastisch verkürzen und die Menge an verwendeten Materialien minimieren konnten.
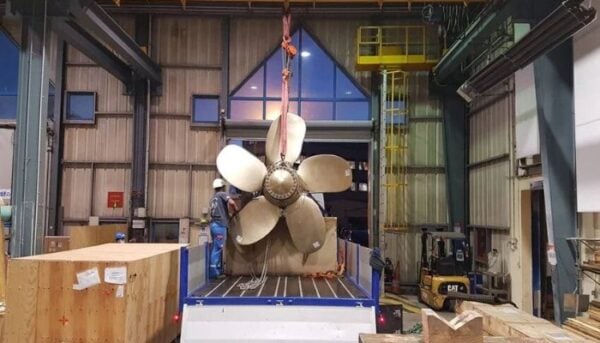
Bild: Naval Group