Welche Anwendung findet der 3D-Druck in der Automobilindustrie
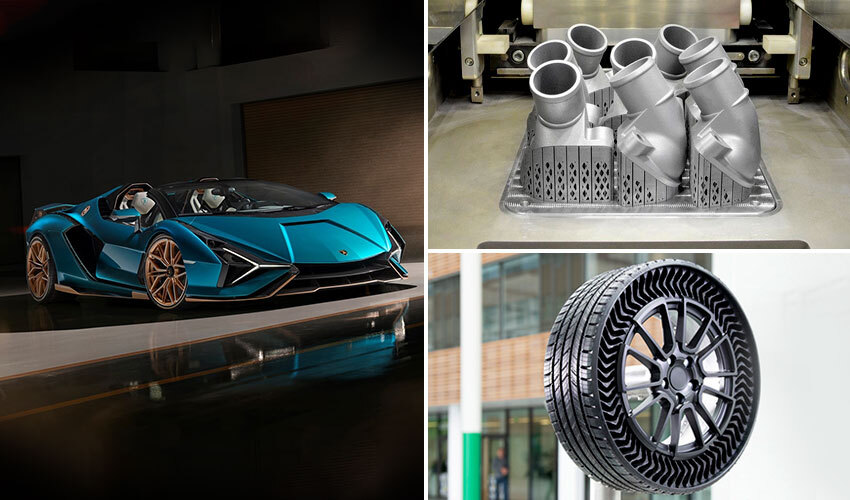
Unter den Anwendungsbereichen, in denen die additiven Fertigungstechnologien zum Einsatz kommen, ist die Automobilindustrie einer der Sektoren, der die Vorteile dieser Technologien am besten nutzt. Diese Technologie ermöglicht es großen Automobilunternehmen, bei der Herstellung komplexer Teile Kosten, Zeit und Gewicht zu sparen. Darüber hinaus ermöglicht die additive Fertigung auch eine stärkere Individualisierung auf der Designebene, wodurch Automodelle zu unvergesslichen Nutzererlebnissen werden. Mit dem bedeutenden Wachstum des 3D-Drucks in der Automobilindustrie wird erwartet, dass er bis 2028 12,4 Milliarden Dollar erreichen wird. Zum besseren Verständnis der Auswirkungen, die die Integration dieser Technologie auf die Branche hat, haben wir eine Liste der führenden Unternehmen zusammengestellt, die den 3D-Druck in der Automobilindustrie einsetzen, sowie die verschiedenen Anwendungen, die sie anbieten. Die Unternehmen sind in alphabetischer Reihenfolge aufgeführt.
Audi beschleunigt das Automobildesign
Audi ist ein deutsches multinationales Unternehmen, das sich auf die Herstellung von Sport- und Oberklassewagen spezialisiert hat und seit 1965 zum Volkswagen-Konzern gehört. Vor einigen Jahren entschied sich das Unternehmen für den Einsatz von Stratasys-Lösungen, um das Automobildesign zu beschleunigen. Die PolyJet-Technologie ermöglichte es Audi, verschiedene Prototypen zu entwickeln und zu bewerten, bevor Fahrzeugteile produziert wurden. Durch die Aufnahme des J750 3D-Druckers in seine Produktpalette konnte der Hersteller die Produktion von Teilen wie Radabdeckungen, Kühlergrills, Türgriffen oder sogar Rücklicht-Cabochons, die normalerweise aus klarem Kunststoff bestehen, erweitern. Mit Hilfe des 3D-Drucks konnte das Unternehmen das Design und die Herstellung der finalen Teile beschleunigen und die Nachfrage seiner Kunden erfüllen.
Bentley – bereits mehr als 15.000 3D-gedruckte Teile
Der britische Automobilhersteller Bentley ist nicht nur für seine renommierten Karossen bekannt, sondern innerhalb der additiven Fertigung ebenfalls für seine Ambitionen für den Ausbau des 3D-Drucks. Mit einer Investmentsumme von mehr als 3 Millionen Euro hat man im Jahr 2021 demnach mehr als 15.000 Bauteile in 3D herstellen können und somit Zeitersparnis bei Design und Herstellung sowie eine Minimierung des entstandenen Abfalls ermöglicht. Neben den prozesslichen und wirtschaftlichen Vorteilen, die sich durch die Nutzung der additiven Fertigung für Bentley ergibt, erfahren auch dessen Kunden einen Mehrwert dadurch: sie können dank 3D-Druck Komponenten ganz individuell und persönlich abgestimmt anfertigen lassen.
BMW setzt auf die additive Fertigung
Das deutsche Unternehmen BMW mit Sitz in München nutzt die additive Fertigung seit mehr als 25 Jahren und war eines der ersten Automobilunternehmen, das diese Technologie integriert hat. Für sie ist der 3D-Druck in der Automobilbranche ein Erfolgsrezept. Im Juni 2020 eröffneten sie schließlich ihr eigenes Zentrum für additive Fertigung mit dem Ziel, ihre Produktionskompetenzen zu bündeln. Dieser Campus hat mehr als 80 Mitarbeiter und mehr als 50 industrielle Fertigungslösungen. Neben dem Zentrum hat BMW bei zahlreichen Gelegenheiten seine Fähigkeiten unter Beweis gestellt, zum Beispiel mit dem Sportwagen i8 Roadster. In dieses Modell sind Teile integriert, die viel leichter sind, als wenn sie mit herkömmlichen Methoden hergestellt worden wären. Teile wie die Halterung der Motorhaubenabdeckung sind jetzt stabiler und gleichzeitig leichter. Eine fortschrittliche Methode zur Optimierung der Automobilproduktion.
Bugatti Bolide ist ein leichtes und schnelles Fahrzeug dank 3D-Druck
Um sein bisher leichtestes und schnellstes Fahrzeug zu bauen, hat sich der französische Automobilhersteller Bugatti an AM gewandt. Der Bolide, wie dieser Sportwagen mit einer Reihe neuer Technologien genannt wird, verfügt über 3D-gedruckte Teile, die das Gewicht seiner Komponenten erheblich reduzieren. Der Hersteller integrierte viele der mit AM hergestellten Einzelteile, die er zuvor enthüllt hatte. Ein aus Titan gedruckter Bremssattel, eine Spoilerhalterung und ein von SLM Solutions gefertigter Motorträger sind nur einige Beispiele für die vielen 3D-gedruckten Teile des innovativen Fahrzeugs. Die Integration des 3D-Drucks war vor allem für Teile mit komplexen Formen wichtig und trug dazu bei, den Bugatti Bolide zu einem leichten und damit deutlich schnelleren Sportwagen zu machen.
Dallara und seine 3D-gedruckten Wärmetauscher
Der italienische Automobilhersteller Dallara hat Conflux Technology mit der Herstellung von Wärmetauschern für seine Formel-3-Autos beauftragt. Das Unternehmen nutzt die additive Fertigung, um effizientere und hitzebeständigere Teile herzustellen. Genauer gesagt, werden EOS-Laserschmelzanlagen auf einem Pulverbett eingesetzt. Die Besonderheit dieses Projekts liegt in der Größe der Wärmetauscher: Dallara benötigte kleine Komponenten, die den Anforderungen des Motorsports gerecht werden. Daher erstellte Conflux Technology mehrere CAD- und CFD-Entwürfe und druckte mehrere Iterationen, um die Geometrie zu validieren und die Eigenschaften des Teils, wie z. B. die Oberflächenrauheit, zu untersuchen.
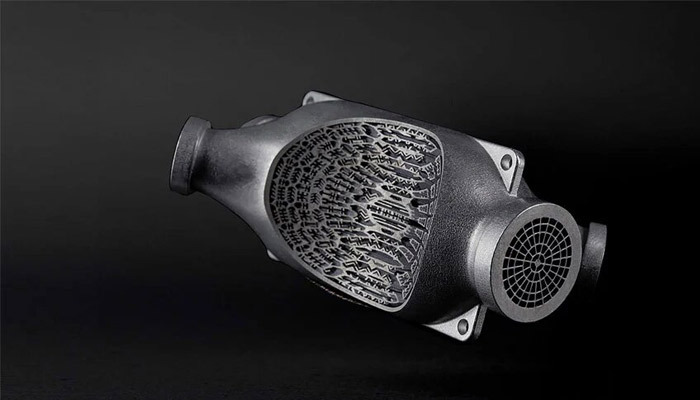
Bild: Tecnología Conflux
Additive Fertigung von Ferrari
Der Druck spielt in der Automobilindustrie eine Schlüsselrolle, da er es ermöglicht, leichtere, stärkere und effizientere Teile in viel kürzerer Zeit zu entwickeln. Der italienische Hersteller Ferrari nutzte diese Technologie, insbesondere den 3D-Druck von Metall, um sich die Kolben für einen seiner Motoren vorzustellen. Ferrari erklärt, dass es eine EOS-Maschine und Titanpulver verwendet hat und dass die additive Fertigung es ihm ermöglicht hat, sich ein viel komplexeres, stärkeres und leichteres Teil herustellen, insbesondere dank der topologischen Optimierung. Diese Methode erhöht auch die Anzahl der möglichen Iterationen: Das Unternehmen konnte sich so viele Entwürfe erstellen, wie es brauchte, und die Prototyping-Phase beschleunigen. Der Automobilhersteller hat auch 3D-gedruckte Bremspedale mit einer hohlen Struktur entwickelt, ein Ergebnis, das mit herkömmlichen Fertigungsmethoden nicht möglich gewesen wäre.
Ford führt 3D-Druckprojekte durch
1988 hatte der Automobilhersteller Ford bereits in drei 3D-Drucker investiert; 2015 schätzte er seine Produktion von 3D-gedruckten Teilen auf 500.000 Dollar, was beweist, dass die Technologie für das US-Unternehmen einen wichtigen Platz eingenommen hatte. Aus gutem Grund hat das Unternehmen starke Partnerschaften mit bestimmten Herstellern wie Desktop Metal oder Carbon geschlossen. Ein Blick auf die von Ford hergestellten Teile zeigt den Aluminium-Lufteinlasskrümmer, eines der größten 3D-gedruckten Metallteile für das Auto. Er wiegt 6 Kilogramm und wurde in nur 5 Tagen entwickelt. In jüngerer Zeit hat Ford spezielle Muttern entwickelt, um Räder vor Diebstahl zu schützen. Diese auf EOS-Maschinen gedruckten Muttern sind der Stimme des Fahrers nachempfunden: Diese wird in ein 3D-Modell umgewandelt und in die Mutter gedruckt. Eine wirksame Methode zur Bekämpfung von Diebstählen, da nur die Stimme des Fahrers das Lösen der Muttern zulassen würde.
Fraunhofer IAPT und ihr “Design to Cost”-Ansatz
Die Fraunhofer-Einrichtung für Additive Produktionstechnologien (Fraunhofer IAPT) hat es sich zur Aufgabe gemacht, ihren Teil zur 3D-gedruckten Serienproduktion beizutragen. Daher hat das in Deutschland angesiedelte Forschungsinstitut mithilfe einer selbst entwickelten Software, welche aus einem Spin-off mit 3D Spark entstand, sich zum Ziel gesetzt sowohl den Kostenfaktor, wie auch die Wirtschaftlichkeit und Effizienz zu optimieren. Dieser Türöffner für die Serienproduktion in der Automobilindustrie verspricht daher einen neu strukturierten Prozess: Reduzierung von Stützstrukturen, Materialbedarf, Fertigungs- und Nachbearbeitungszeiten. Mit der Verfolgung dieses “Design to Cost”-Ansatzes könnte somit eine insgesamt 80 %iger günstigere Fertigung von automobilen Teilen entstehen. So arbeitete man auch bereits mit Luxusautohersteller Bugatti zusammen.
Lamborghini individualisiert seinen Sian Roadster
Lamborghini ist der Inbegriff von Luxussportwagen. Die Gründe für die Wahl der additiven Fertigungstechnologien zur Herstellung des Sian Roadster waren daher sicherlich nicht Kosten zu senken oder schneller zu produzieren. Was waren also ihre Beweggründe? Für Lamborghini steht die additive Fertigung vor allem für eines: unbegrenzte Möglichkeiten zur Individualisierung. Die Anpassungsmöglichkeiten sind so grenzenlos, wie man es sich nur vorstellen kann. Lamborghini bietet jedem Käufer des Sian Roadster die volle Kontrolle über den Innenraum sowie eine Auswahl an Lackierungen. Die neu gestalteten Belüftungsdüsen wurden in 3D gedruckt und ermöglichen den Kunden eine individuelle Gestaltung, indem sie u. a. ihre Initialen in das Design integrieren – ein einzigartiges Nutzererlebnis!
McLarens neuer Hybrid-Supersportwagen Artura
Wie viele andere Automobilmarken ist auch der Luxusautohersteller McLaren von den Vorteilen von AM überzeugt. Für seinen Hochleistungs-Hybrid-Supersportwagen Artura, bei dessen Entwicklung McLaren auf eine Kombination aus Technologie, Design und konkurrenzloser Leistung setzte, entschied sich das Unternehmen für den 3D-Druck von Metall. Der britische Automobilhersteller nutzte diese innovative Methode, um den Motorblock und die Zylinderkopfkerne so zu gestalten, dass eine bessere Motorkühlung und damit eine höhere Leistung möglich ist. Das übergeordnete Ziel des Unternehmens bei der Entwicklung des Supersportwagens war es, ihn im Vergleich zu anderen ähnlichen Fahrzeugen leichter zu machen. Um dies zu erreichen, verwendete das Designteam Kohlefaser, um ein leichteres Chassis zu konstruieren. Außerdem wurden 3D-gedruckte Kerne in den Motorblock und die Aluminium-Zylinderköpfe eingearbeitet, die ohne den Einsatz von AM nicht so detailliert hätten hergestellt werden können.
Mercedes und die Einsatzmöglichkeiten der additiven Fertigung
Da die Automobilindustrie nicht nur Fahrzeuge für den Personentransport, sondern auch Fahrzeuge für den Gütertransport umfasst, erschien es uns wichtig, über die LKW von Mercedes zu sprechen. Nachdem sich Mercedes zunächst erfolgreich auf den 3D-Druck von Kunststoffteilen konzentriert hat, stellt das Unternehmen nun auch Lkw-Teile aus Metall her. Durch den Einsatz der additiven Metallfertigung werden die Ersatzteile widerstandsfähiger und flexibler. Ein weiterer Vorteil ist, dass Mercedes die Möglichkeit hat, diese Teile in kleinen Mengen und zu geringen Kosten herzustellen. Mercedes ist zwar das erste Unternehmen, das sich auf die Herstellung von Lkw-Ersatzteilen konzentriert, nutzt die Technologie aber auch, um einige seiner Autos zu optimieren. Bei einem seiner neuesten Fahrzeuge, dem EQXX, setzte die deutsche Marke 3D-Technologien ein, um das Gewicht der Bauteile zu reduzieren und die Herstellungskosten und -zeiten zu begrenzen.
Michelin und sein 3D-gedruckter Reifen
Der französische Reifenhersteller Michelin hat 2019 seinen ersten Reifenprototypen vorgestellt, der additive Fertigungstechnologien verwendet. Diese Reifen, die Uptis (Unique Puncture-proof Tire System) genannt werden, sollen luftlos sein, um das Risiko von Reifenpannen zu verringern. Das Unternehmen hat bei der Entwicklung des 3D-gedruckten Prototyps mit dem US-amerikanischen Unternehmen General Motors zusammengearbeitet. Das Unternehmen erklärte, dass die additive Fertigung auch dazu verwendet werden könnte, den Gummistreifen, der das Risiko einer Reifenpanne verringert, bei Bedarf zu reparieren. Die Uptis-Reifen, die Abfall reduzieren und eine nachhaltige Mobilität fördern, haben ihre ersten Kilometer im Jahr 2021 zurückgelegt. Nach diesem Erfolg will das Unternehmen bis 2024 mit der Vermarktung beginnen. Bisher wurde der 3D-Druck nur zur Entwicklung des Prototyps eingesetzt, wobei erneuerbare und biobasierte Materialien verwendet wurden. Sollte die Produktion jedoch größere Mengen erreichen, könnte diese Technologie auch in größerem Maßstab eingesetzt werden. Die Uptis-Reifen, die Abfall reduzieren und eine nachhaltige Mobilität fördern, beinhalten eine flexible, glasfaserverstärkte und gummiartige Struktur, die auf einem Aluminiumrad angebracht ist.
MINI Strip wird dank 3D-Druck nachhaltiger
Der britische Automobilhersteller MINI verstärkt seine Bemühungen, seine Fahrzeuge nachhaltiger zu gestalten. Zu diesem Zweck hat sich das Unternehmen mit dem Designer Paul Smith zusammengetan, der ihm bei der Entwicklung eines minimalistischeren Automodells geholfen hat: dem MINI Strip. Aber welche Rolle spielt die additive Fertigung bei all dem? Um einen Teil dieses Nachhaltigkeitsziels zu erreichen, wandte sich Paul Smith dem 3D-Druck recycelter Polymere zu, um Teile herzustellen, die in das Auto eingebaut werden. Komponenten wie Untertürverkleidungen und Radabdeckungen wurden aus recyceltem Kunststoff in 3D gedruckt. Diese und viele andere Teile, die aus recycelten Materialien hergestellt wurden, verleihen dem MINI Strip eine vereinfachte Geometrie, ein sauberes Design und eine größere Umweltverantwortung.
Porsche optimiert die Kolben seiner Sportwagen
Der Hersteller Porsche nutzt die Technologie der additiven Fertigung bereits seit den frühen 1990er Jahren. In diesem Sommer hat der Automobilriese zum ersten Mal Motorkolben im 3D-Druckverfahren hergestellt. Die mit dieser Technologie hergestellten Komponenten wurden für den Hochleistungsmotor des Porsche 911 GT2 entwickelt. Der 3D-Druck ermöglichte es, die Kolben zu optimieren und dieses wichtige Motorelement um 10 Prozent leichter zu machen als herkömmlich hergestellte Kolben. Porsche verwendete für die Mahle-Gusskolben eine spezielle Aluminiumlegierung, um die besten Eigenschaften für diese spezifische Anwendung zu erhalten. Das Team musste neue Parameter für den Druckauftrag entwickeln, der von dem Fertigungspartner Trumpf ausgeführt wurde.
SEAT eröffnet ein Zentrum für additive Fertigung
Der spanische Hersteller SEAT hat kürzlich einen neuen, 3.000 m2 großen Standort angekündigt, an dem alle Prozesse und Aktivitäten vor der Massenproduktion eines neuen Modells vereinheitlicht werden sollen. Ein großer Bereich des neuen Zentrums wird für 3D-Druckprojekte reserviert sein. Das additive Fertigungszentrum von SEAT beherbergt mehrere 3D-Lösungen – neun, um genau zu sein. Dazu gehören ein HP Multi Jet Fusion, eine SLS-Maschine, sechs FDM-3D-Drucker und eine PolyJet-Lösung. Dank der Vielfalt dieser Technologien ist SEAT in der Lage, Teile mit größerer Detailgenauigkeit, wichtigen mechanischen Eigenschaften und fortschrittlichen Funktionalitäten herzustellen. Die Maschinen arbeiten 24 Stunden am Tag und produzieren durchschnittlich 50 Teile pro Tag. Nach Angaben des Herstellers handelt es sich bei 80 % der Teile um Prototypen, die zur schnelleren Entwicklung von Fahrzeugen verwendet werden, der Rest sind hauptsächlich Werkzeug- und Anpassungsbauteile.
Vital Auto: Entwerfen Sie die Autos der Zukunft in 3D
Das britische Industriedesign-Studio Vital Auto verfügt über einen großen Erfahrungsschatz was die Automobilindustrie betrifft. Zu den illustren Kunden des Unternehmens gehören viele der weltweit führenden Automobilhersteller wie Volvo, Nissan und McLaren. Vital Auto verwendet die Form 3L- und Fuse 1-Drucker von Formlabs, um qualitativ hochwertige Prototypen zu erstellen. Vom Design bis zur Produktion hat das Unternehmen die additive Fertigung in seinen gesamten Produktionsprozess integriert. Die Fachleute von Vital Auto erklärten: „Wir haben vom ersten Tag an den 3D-Druck eingesetzt, nicht nur, um die Kosten zu senken, sondern auch, um dem Kunden mehr Vielfalt bei seinen Entwürfen und Ideen zu bieten. Das Interessanteste an 3D-Druckern ist ihre Vielseitigkeit, die Möglichkeit, das Material in weniger als fünf Minuten zu wechseln, und die Variabilität dieser Materialien von weich und flexibel bis hart und starr ist für uns von unschätzbarem Wert.“
YOYO – das 3D-gedruckte Elektrofahrzeug
Zum Abschluss dieser Auswahl zum 3D-Druck in der Automobilindustrie wollen wir über das YOYO-Projekt sprechen. Da die globale Erwärmung weltweit zu einem immer größeren Problem wird, entscheiden sich immer mehr Menschen für umweltfreundlichere Alternativen zu herkömmlichen Produkten, darunter auch Elektroautos. Und der 3D-Druck ist in dieser Hinsicht keine Ausnahme. Zum Beispiel YOYO, das vollelektrische Stadtauto von XEV. Das Auto wird größtenteils mit 3D-Druck hergestellt, genauer gesagt mit großformatiger additiver Fertigung. Nach Angaben des Unternehmens ist YOYO dank eines 100%igen Elektromotors die nachhaltigste Lösung für die urbane Mobilität, und natürlich wurde der 3D-Druck aufgrund seiner nachhaltigeren Natur im Vergleich zu herkömmlichen Herstellungsverfahren gewählt.
Welches Projekt aus der Automobilindustrie gefällt Ihnen am besten? Teilen Sie uns Ihre Eindrücke und Erfahrungen mit und kontaktieren Sie uns. Möchten Sie eine Zusammenfassung der wichtigsten Neuigkeiten im 3D-Druck und der additiven Fertigung direkt und bequem in Ihr Postfach? Registrieren Sie sich jetzt für unseren wöchentlichen Newsletter und folgen Sie uns auf Facebook und Twitter, um stets auf dem Laufenden zu bleiben! Außerdem sind wir auch auf XING und LinkedIN zu finden.