#3DStartup: Viewpointsystem über additive Fertigung ihrer Smart Glasses
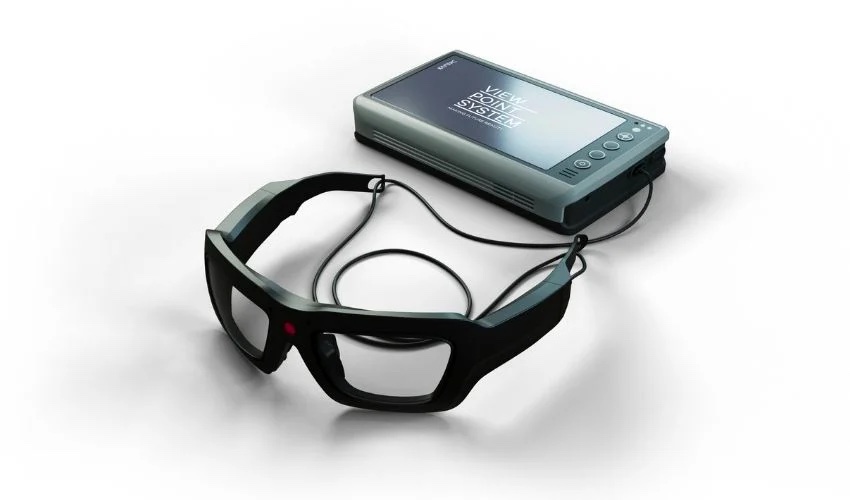
Um die Beziehung zwischen Mensch und Maschine Schritt für Schritt näher zusammen zu bringen hat das in Wien ansässige Start-up Viewpointsystem sich intensiv mit einer Lösung beschäftigt. Das Resultat: zukunftsweisende Smart Glasses mit wissenschaftlichem Knowhow im Bereich der Blickforschung. Welchen Beitrag die additive Fertigung bei einer solch hochtechnischen Errungenschaft leistet? Viele der für die Smart Glasses angefertigten Teile stammen aus dem 3D-Drucker! Somit kann eine menschliche und maschinelle Zusammenarbeit auf Distanz ermöglicht werden, die unter anderem bei Remote Support und Fernwartungen zum Einsatz kommen. Wir haben mit dem CTO von Viewpointsystem, Frank Linsenmaier, über den Einsatz der additiven Fertigung bei den Smart Glasses gesprochen und welche Vorteile sich daraus für das Unternehmen ergeben hat.
3DN: Können Sie sich und Viewpointsystem vorstellen?
Viewpointsystem ist junges Deep-Tech-Unternehmen aus Wien, das Smart Glasses für den B2B-Bereich entwickelt und produziert. Wir wurden 2016 aus einem Spin-off der Universität für Bodenkultur Wien heraus gegründet. Heute haben wir Kunden auf drei Kontinenten und rund 60 Mitarbeiter. Wir sind eines der ersten Unternehmen in Österreich, das bei der industriellen Serienproduktion auf die additive Fertigung setzt. Insgesamt zwölf Komponenten unserer Smart Glasses werden additiv hergestellt, vom Brillenrahmen bis hin zu den Nosepads und inneren technischen Teilen – Tendenz steigend. Ich selbst bin erstmals 2005 mit der additiven Fertigung in Berührung gekommen, und zwar im Bereich der Herstellung von Prototypen und Kleinserien für einen großen Automobilzulieferer. Im Vergleich zu anderen Technologien hatte die additive Fertigung immer die meisten Freiheitsgrade im Design, und Prototypen waren zeitlich schnell herstellbar. So hatten wir immer die Möglichkeit, rasch die Machbarkeit zu analysieren und neue Bausteile vorzuführen. Als ich 2016 zu Viewpointsystem kam, wurden unsere Bauteile noch im Spritzgussverfahren hergestellt. Uns war jedoch schnell bewusst, dass sich die additive Fertigung besser für unsere Produkte eignet. Sie bietet uns die Möglichkeit, die Dinge stabil und gleichzeitig beweglich zu designen, was bei einem Wearable ein großer Vorteil ist. Mithilfe der additiven Technologie konnten wir unser Produkt schnell in Serie überführen. Für die Zukunft sehen wir noch viele Möglichkeiten, die Grenzen dieser Technologie weiter auszureizen.
3DN: Welche Rolle spielt die additive Fertigung bei Viewpointsystem und welche Technologie/n und Material/ien nutzen Sie konkret?
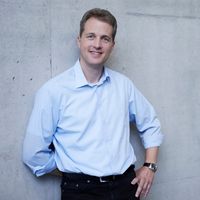
Frank Linsenmaier – CTO bei Viewpointsystem (Bild: Viewpointsystem)
In unserer Produktion in der Wiener Seestadt haben wir in Kooperation mit unseren Partnern HP und d4pro eine Fertigungsstraße für die Serienproduktion unserer Datenbrillen eingerichtet. Wir setzen auf die HP Jet Fusion Drucklösung. Das System ist für die industrielle Bauteilfertigung optimiert. Durch mehrere Built Units ist ein Tandembetrieb des Drucksystems möglich, und damit auch eine 24/7 Produktion. Nach dem Druckvorgang, der je nach Beladung zwischen acht und zwölf Stunden dauert und dem Abkühlen, wird der Brillenrohling weiterbearbeitet. Unsere Post-Processing Schritte sind klassisch: Perlstrahlen zur Restpulver-Entfernung und Oberflächenverdichtung und anschließende Imprägnier-Färbung. Alle verwendeten Materialien sind zertifiziert biokompatibel und damit nachweislich neutral zur Haut. Zum Einsatz kommt das Material PA 12. Das Multi Jet Fusion Verfahren liefert mit PA 12 exzellent formstabile Bauteile welche in allen Dimensionen uniform mechanisch belastbar sind. Für organische Formen, wie sie in unserer Brille vorkommen, ist das sehr vorteilhaft. Auch einer Prüfung nach EN 166 (Schutzbrille) hat das Material im finalen Aufbau standgehalten. Nach anfänglicher Skepsis zur Oberflächengüte haben wir festgestellt, dass gerade für ein Wearable die gleichmäßige Rauheit der Bauteile einen optimalen Tragekomfort bei längeren Sessions bietet.
Die additive Fertigung ermöglicht uns ein hohes Innovationstempo, was für uns als junges Unternehmen in einem dynamischen Technologieumfeld einen großen Wettbewerbsvorteil bedeutet. Wir können schnell Veränderungen vornehmen und auch mal Dinge außer der Reihe ausprobieren. Da wir ursprünglich unsere Produkte im klassischen Spritzguss gefertigt haben ist der unterschiedliche Zugang zu Innovationszyklen in unserer Organisation besonders gut sichtbar. Produktenwicklungen planen wir auf Wochen, nicht mehr auf Monate. Neben geringeren Entwicklungskosten ermöglicht uns ein solcher Ansatz deutlich mutigere Entscheidungen zu treffen und diese schnell zu validieren. Weitere wichtige Vorteile sind bedarfsgerechte Produktion und Nachhaltigkeit. Im Vergleich zur klassischen Produktion können wir in kleineren Serien produzieren, zu vergleichsweise überschaubaren Kosten. So müssen wir unsere Komponenten nicht auf Vorrat in großen Stückzahlen einkaufen und können Lagerkapazitäten einsparen – das ist so nachhaltig wie ökonomisch sinnvoll.
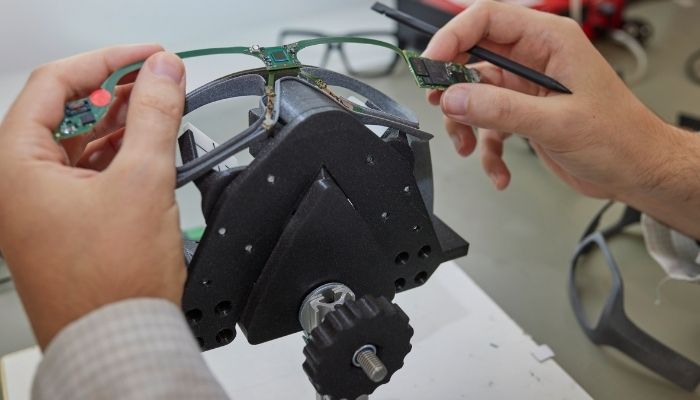
Selbst bei inneren technischen Teilen kommt die additive Fertigung zum Einsatz (Bild: Viewpointsystem)
3DN: Welchen Bedarf deckt die VPS 19 Smart Glasses genau ab? Und an wen adressiert sich Ihr Produkt?
Unsere Smart Glasses unterstützen Firmenkunden weltweit unter anderem bei der Fernwartung von Maschinen und Anlagen und beim Remote Support. In Zeiten steigenden Klimabewusstseins und vor dem Hintergrund der pandemiebedingten Kontaktbegrenzungen beobachten wir eine stark steigende Nachfrage nach Lösungen für die Zusammenarbeit auf Distanz. Mit unseren Smart Glasses können Unternehmen in Sekundenschnelle und ohne Reiseaufwand Mitarbeiter und Experten auf der ganzen Welt miteinander verbinden, beispielsweise bei der Reparatur von Maschinen. So kann beispielsweise ein Spezialist einen Produktionsmitarbeiter auf einem anderen Kontinent präzise an einer Anlage anleiten. Ohne zeitaufwendige und anstrengende Reisen. Das schont das Klima und das Budget. Dank integrierter Eye-Tracking-Technologie zeigt unsere Datenbrille auf dem Display diskret den Blickpunkt des Trägers an und lässt Sie in Echtzeit genau wissen, worauf die Person ihre Aufmerksamkeit richtet. Dies ermöglicht eine verlustfreie Kommunikation auch über Sprachbarrieren hinweg und in lauten Umgebungen. Unsere Datenbrillen werden auch für Trainings und Dokumentation eingesetzt, z.B. in der Industrie, aber auch in der Medizin und im Sicherheitsbereich. Außerdem kann mit ihnen Forschung & Analyse betrieben und menschliche Verhalten nachvollzogen werden.
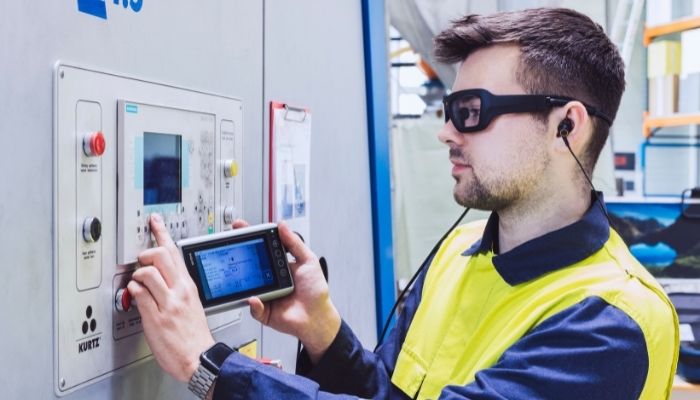
Die Smart Glasses von Viewpointsystem können vielfältig zum Einsatz kommen (Bild: Viewpointsystem)
3DN: Wie sieht die Zukunft von Viewpointsystem aus? Auf welche neuen Projekte dürfen wir uns freuen?
Wir werden die Produktion unserer Smart Glasses in diesem Jahr weiter nach oben skalieren, um die steigende Nachfrage nach Remote Support-Lösungen zu decken. Außerdem stehen bei uns einige Hardware-Weiterentwicklungen an, bei denen uns die additive Fertigung viele Möglichkeiten bietet. Zu viel kann ich hier noch nicht verraten, aber in Planung sind unter anderem auf den Träger maßgeschneiderte Nose Pads, die individuell nach 3D-Scans der Nase angefertigt werden- Stichwort mass-customization. So ist der perfekte Sitz der Datenbrille über viele Stunden garantiert. Ein weiteres spannendes Thema ist unsere neue Eye-Tracking-Modulserie, von der wir erste Prototypen bereits Ende letzten Jahres auf der AWE Augmented World Expo in Kalifornien vorgestellt haben. Mit diesen präkonfigurierten Modulen bieten wir Herstellern von Augmented & Virtual Reality Brillen die Möglichkeit, Augendaten und Eye Tracking-Funktionen schnell und einfach in ihre Systeme zu integrieren. Eye Tracking ist essenziell für viele Extended Reality-Funktionen wie zum Beispiel Foveated Rendering, aber auch wichtig, um zu erfassen, an welchen Informationen der Träger in einem bestimmten Moment interessiert ist.
3DN: Haben Sie abschließende Worte für unsere Leserschaft?
Ich kann abschließend nur noch einmal unterstreichen, dass wir bei Viewpointsystem ohne additive Fertigung heute nicht da wären, wo wir sind. Als junges Deep-Tech Unternehmen arbeiten wir oft an der Grenze des technologisch Machbaren, und dank additiver Fertigung hat sich eine komplett neue “Denkschule” in unserem Unternehmen etabliert. Mit technischer Neugier, Mut und schnellen Iterationen entstehen Produktinnovationen, mit denen wir uns oft selbst überraschen. Additive Manufacturing wird bei uns intern auch „addictive manufacturing“ genannt. Es ist so motivierend, die Kolleg*innen in der Konstruktion und Fertigung zu sehen, wie sie sich täglich neuen Herausforderungen stellen und Verbesserungen für die heutigen sowie Ideen für zukünftige Produkte realisieren. Die Entscheidungsfindung mit echten Bauteilen in den Händen ist viel aussagekräftiger, als diese nur auf dem Bildschirm zu sehen. Mehr Informationen zu Viewpointsystem gibt es HIER.
Was denken Sie über die Smart Glasses von Viewpointsystem? Teilen Sie uns Ihre Meinung mit und kontaktieren Sie uns. Möchten Sie eine Zusammenfassung der wichtigsten Neuigkeiten im 3D-Druck und der additiven Fertigung direkt und bequem in Ihr Postfach? Registrieren Sie sich jetzt für unseren wöchentlichen Newsletter und folgen Sie uns auf Facebook und Twitter, um stets auf dem Laufenden zu bleiben! Außerdem sind wir auch auf XING und LinkedIN zu finden.
*Titelbildnachweis: Viewpointsystem