#3DStartup: LEAM entwickelt ein LED-basiertes Add-on zur Verbesserung der Lagendichte von 3D-gedruckten XXL-Bauteilen
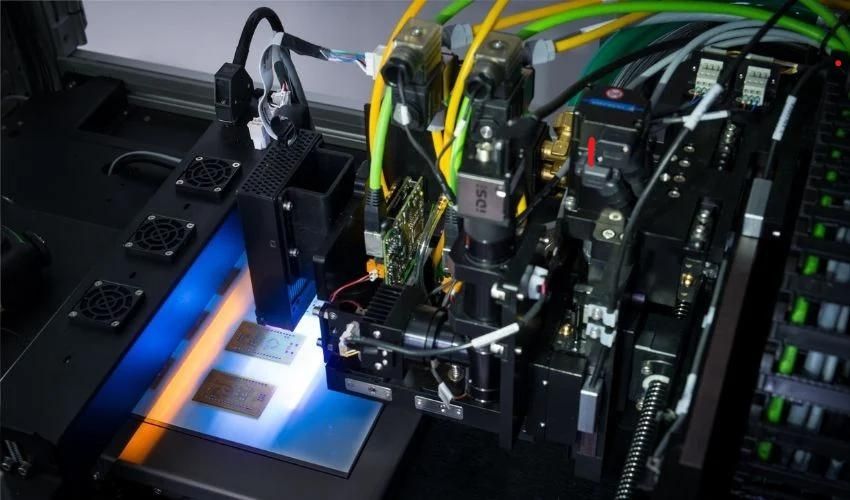
Von der Wissenschaft in den 3D-Druck und schließlich zum Business – so sah der bisherige Werdegang von LEAM aus. Das Spin-off der Technischen Universität München setzte nämlich bereits an der Hochschule den Grundstein für die nun marktreife Technologie. Mit seinem DEMEX-System bestreitet LEAM neue Wege in der AM-Branche, denn das Unternehmen nutzt nicht wie andere Startups Laser zum Schmelzen des Materials, sondern ein kontinuierliches Lichtspektrum. Das Material wird auf diese Weise kurz vor der Düse erhitzt und die Technologie sorgt zudem für eine bessere Haftung zwischen den Schichten. Das von LEAM entwickelte DEMEX-System ist als Add-on für großformatige 3D-Drucker erhältlich und das Jungunternehmen konnte bereits die ersten Kunden begeistern. Wir haben mit dem Team von LEAM gesprochen, um mehr über die bisherigen Etappen des Startups zu erfahren, seine Technologie näher kennenzulernen, und darüber zu sprechen, welche Pläne LEAM für die Zukunft verfolgt.
3DN: Könnten Sie sich kurz vorstellen und erzählen, wie Sie zum 3D-Druck gekommen sind?
Wir sind drei Gründer (Patrick Consul, Ting Wang und Benno Böckl) und wir beschäftigen uns mit dem Thema 3D-Druck bereits seit unserem Maschinenbaustudium bzw. seitdem wir unsere Tätigkeit als wissenschaftliche Mitarbeiter am Lehrstuhl für Carbon Composites (LCC) der Technischen Universität München begonnen haben, wo wir uns auch kennengelernt haben. Patrick hat bereits in seiner Masterarbeit versucht, Kerne für Sandwichstrukturen in der Luftfahrt aus PEEK im 3D-Druck herzustellen. Das war damals allerdings nicht möglich, da die notwendigen Festigkeiten nicht erreicht werden konnten. Das Thema hat er aber ab 2017 als wissenschaftlicher Mitarbeiter am Lehrstuhl für Carbon Composites weiterverfolgt. In den darauffolgenden Jahren hat er mehrere Forschungsprojekte beantragt und bearbeitet, in denen er das Thema weiter erforscht hat.
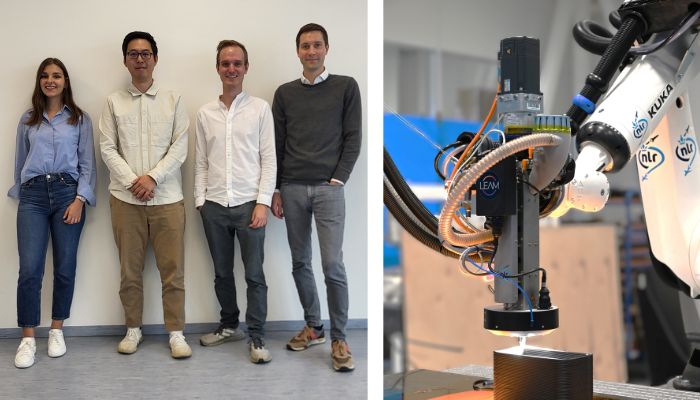
Links: Das LEAM-Team. Rechts: Das entwickelte DEMEX-System
Ein Forschungsprojekt, in dem gezielt die Erwärmung des Substrats untersucht werden sollte, um so eine bessere Anbindung der darauffolgenden Schicht zu erreicht, wurde von Ting Wang bearbeitet. Ting hat also in seiner Zeit als wissenschaftlicher Mitarbeiter bereits die ersten konkreten Vorarbeiten geleistet, auf die die weiteren Entwicklungen des DEMEX-Systems aufbauten. Benno war ebenfalls mehrere Jahre als wissenschaftlicher Mitarbeiter am Lehrstuhl für Carbon Composites beschäftigt und hat sich hier mit dem Automated-Fiber-Placement-Verfahren zur Fertigung von Carbon-Bauteilen beschäftigt. Dieses besitzt gewisse Ähnlichkeiten zum 3D-Druck. Wir sind also über die Wissenschaft zum 3D-Druck gekommen und haben dadurch die Herausforderungen des Verfahrens gut kennengelernt. Das ermöglicht uns heute Lösungen zu erarbeiten, die dem 3D-Druck neue Möglichkeiten in der Bauteilfertigung eröffnen.
3DN: Wie kam es zur Gründung von LEAM und was waren bisher die größten Meilensteine?
Patrick hat in seinen Forschungsprojekten unterschiedlichste Ansätze untersucht, um die Lagenanhaftung und somit die Bauteilfestigkeit im Extrusions-3D-Druck zu steigern. Es hat sich dabei immer deutlicher herauskristallisiert, dass der einzige wirklich erfolgversprechende Ansatz das Erwärmen und punktuelle Aufschmelzen der darunterliegenden Schicht ist. Diesen konkreten Ansatz hat Ting in einem Forschungsprojekt untersucht und einen ersten Prototyp unseres späteren DEMEX-Systems entwickelt, der allerdings noch Laser als Energiequellen genutzt hat. Der Ansatz hat vielversprechende Ergebnisse geliefert, allerdings war die Kommerzialisierbarkeit fraglich, da die Kosten und die benötigten Schutzeinrichtungen das Produkt unwirtschaftlich gemacht hätten. Wir kamen dann auf die Idee, statt Laser weiße LEDs mit breitbandigem Spektrum zu nutzen. Diese sind wesentlich sicherer und kostengünstiger als Laser und nachdem erste Vorversuche gezeigt haben, dass es funktionieren kann, haben wir uns dazu entschlossen eine Firma zu gründen, die das System als Produkt anbietet.
Ein wichtiger Meilenstein war anschließend der Erhalt der Förderung im Rahmen des Exist-Forschungstransfers. Damit konnten wir uns die ersten 18 Monate finanzieren und LEAM so weit aufbauen, dass wir als Firma bestehen können. Letztes Jahr haben wir auch die Zusage des ESA Business Incubation Centres Bavaria erhalten, das unser Vorhaben unterstützt. Ein weiterer Meilenstein war das erste Proof of Concept mit einem Kunden, das nicht nur gezeigt hat, dass unser System funktioniert, sondern auch, dass große Marktpotentiale bestehen. Wir konnten dann auch die ersten Systeme an Kunden verkaufen und installieren. Mitte letzten Jahres haben wir unsere erste Vollzeit-Mitarbeiterin eingestellt, die bei uns als Entwicklungsingenieurin tätig ist, wodurch wir nun auch zum Arbeitgeber geworden sind. Schließlich konnten wir für unsere Technologie eine Patentanmeldung einreichen, was für die weitere Entwicklung der Firma entscheidend ist.
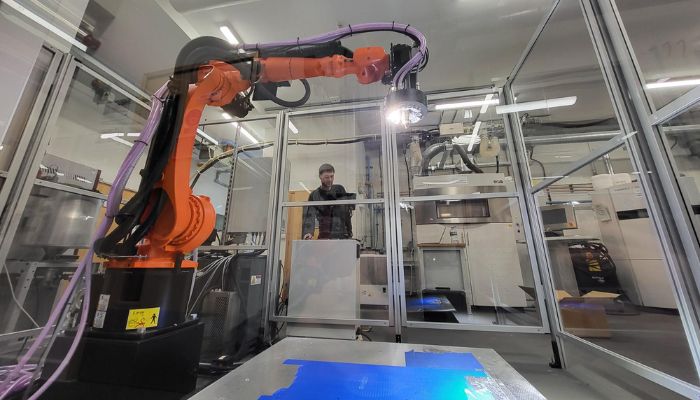
LEAM hat mittlerweile ein Patent für sein DEMEX-System angemeldet.
3DN: Könnten Sie Ihr DEMEX-System kurz vorstellen? Welche Vorteile bietet die Technologie im Vergleich zu anderen Verfahren?
Beim DEMEX-System handelt es sich um eine Add-on Komponente für Großformat-3D-Ducker. Das System kombiniert LED-Emitter und Infrarotkameras, die um die Düse des Extruders verteilt angeordnet sind. Mithilfe der LED-Emitter kann das DEMEX-System das Substrat ganz gezielt und sehr lokal begrenzt vor der Düse erwärmen und somit sicherstellen, dass eine perfekte Verschweißung der Lagen erfolgt. Das Erreichen der gewünschten Zieltemperatur wird durch einen geschlossenen Regelkreis mit den Infrarotkameras sichergestellt. Statt der bisher maximal erreichbaren z-Festigkeit von 60 %, kann das Bauteil 100 % der im Datenblatt des Materialherstellers angegebenen Festigkeit erreichen – und das in alle Richtungen! Zudem können wesentlich günstigere Material-Grades verarbeitet werden, wie bspw. Spritzguss-Materialien, die bisher völlig ungeeignet für den 3D-Druck waren, da keine Lagenanhaftung erreicht werden konnte. Das DEMEX-System kommuniziert mit der Steuerung des Druckers und weiß daher stets, in welche Richtung sich der Drucker aktuell bewegt und welcher Bereich zu erwärmen ist. Es muss daher auch nicht bei der Erstellung des G-Codes berücksichtigt werden, wodurch die bisherigen Abläufe bei der Nutzung des Druckers nicht gestört werden.
Mit unserer Technologie setzen wir bei gängigen Problemen im 3D-Druck an. Ein häufig gewählter Ansatz im 3D-Druck sind etwa beheizte Bauräume. Diese haben jedoch den Nachteil, dass die Temperatur nicht beliebig hoch gewählt werden kann, da das Bauteil sonst instabil wird und in sich zusammenfällt. Dieses Problem besteht bei unserem DEMEX-System nicht, da wir nur eine sehr dünne Schicht an der Oberfläche in einem sehr begrenzten Bereich vor der Düse erwärmen. Somit können wir bis über die Schmelztemperatur des Materials gehen, wodurch wir wesentlich höhere Festigkeiten erreichen. Ein anderer Ansatz ist der Einsatz von Infrarotstrahlern, die verteilt im Bauraum oder lokal an der Düse installiert sind. Diese haben jedoch den Nachteil, dass Infrarotstrahler sehr lange Reaktionszeiten von ein bis drei Sekunden haben, was sie sehr schlecht regelbar macht. Die Leistung unseres LED-basierten Systems hingegen kann innerhalb von Millisekunden angepasst werden und die erreichte Leistungsdichte ist auch höher als bei Infrarotstrahlern. Gegenüber Lasern haben unsere LEDs außerdem einen ganz klaren Preisvorteil. Einerseits sind die Energiequellen an sich schon 90 % günstiger als ein vergleichbares Lasersystem. Andererseits entfallen die notwendigen Schutzeinrichtungen, die bei einem großformatigen 3D-Drucker gegebenenfalls schon mehr kosten können als das ganze von uns angebotene DEMEX-System.
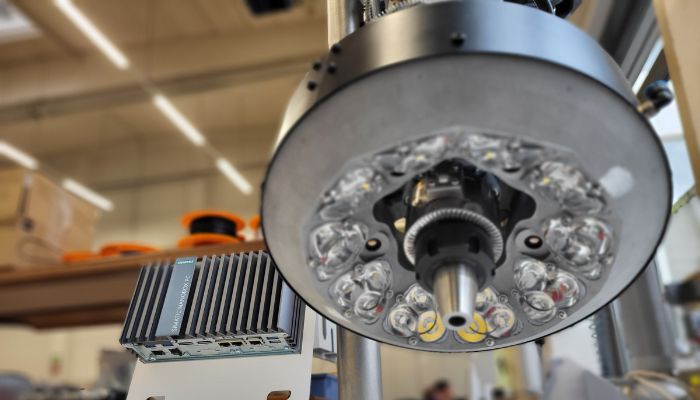
LEAM nutzt bei DEMEX LEDs und keine Laser. Die LEDs können schnell adaptiert werden und sind auch kostengünstiger als Laser.
3DN: An wen richtet sich das DEMEX-System und welche Anwendungen profitieren am meisten davon?
Der Nutzen des DEMEX-Systems zeigt sich besonders bei Anwendungen, in denen Hochleistungskunststoffe zum Einsatz kommen bzw. bei sehr großen Bauteilen, bspw. in der Luft- und Raumfahrt oder Oil & Gas Industrie. Hier wirken sich die Probleme, die wir lösen, besonders stark aus. Wenn wir beispielsweise ein großes Bauteil betrachten, bei dem es während des Drucks zu einer Unterbrechung kommt, ist das Teil bisher Ausschuss mit damit verbundenen Kosten, die in die Tausende gehen können. Mithilfe von DEMEX kann der Druck nach der Unterbrechung einfach fortgesetzt werden, da die Anbindung an die darunterliegende Schicht sichergestellt ist. Das System ist aber auch für andere Industrien geeignet, in denen technische Kunststoffe oder faserverstärkte Kunststoffe zum Einsatz kommen. Grundsätzlich profitiert jeder, der Bauteile drucken möchte, die mechanischen Belastungen ausgesetzt sind, für die die bisher mit 3D Druck erzielten Festigkeiten nicht ausreichen. Denkbar ist hier z.B: der Schiffsbau, Schienenfahrzeugbau oder auch die Automobilindustrie.
3DN: Was waren Ihre bisher spannendsten Projekte?
Besonders spannend war mit Sicherheit die Installation unserer ersten beiden Systeme. Den ersten DEMEX haben wir beim NLR installiert, dem niederländischen Pendant zum Deutschen Zentrum für Luft- und Raumfahrt (DLR). Kurz danach konnten wir das zweite System bei der University of Exeter in England in Betrieb nehmen. Aber auch die aktuell laufenden Projekte sind unglaublich interessant. Zudem gibt es immer wieder neue Anfragen aus Branchen, an die man niemals gedacht hätte. Bspw. sind wir aktuell in Gesprächen mit Kunden aus der Baubranche, es gibt aber sogar Interessenten die Fischzucht betreiben, dem Ganzen sind also echt keine Grenzen gesetzt.
3DN: Haben Sie noch einige letzte Worte zu Ihren weiteren Zielen?
Der nächste Schritt, den wir gehen mit unserem System gehen wollen, ist die Anpassung an kleinere Drucker. Aktuell können wir nur großformatige 3D-Drucker bedienen, da wir noch einen gewissen Bauraum benötigen. Wir arbeiten aber bereits daran die einzelnen Komponenten zu verkleinern und wir wollen im Laufe dieses Jahres so weit sein, auch Filamentdrucker mit dem DEMEX-System ausstatten zu können. Wir haben immer wieder Anfragen in diese Richtung erhalten, es gibt hier also eine starke Nachfrage. Zudem rollen wir in den kommenden Wochen die Umstellung auf Siemens Industrial Edge aus. Das beinhaltet neue Hard- und Software-Komponenten in unserem System, die ganz neue Möglichkeiten in den Punkten Wartung und Systemupdates, aber auch Zuverlässigkeit bieten.
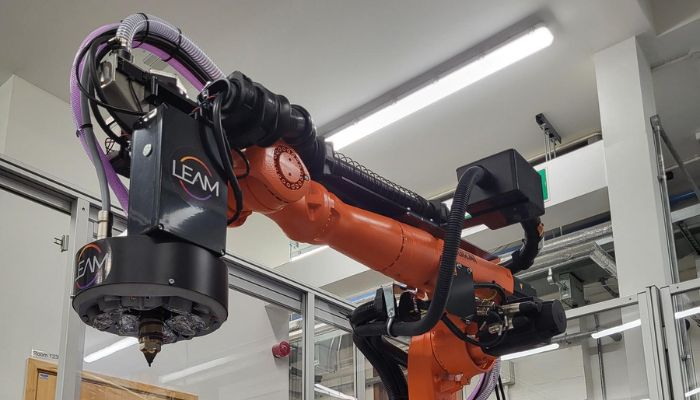
Derzeit ist das DEMEX-System nur für großformatige 3D-Drucker verfügbar.
Was halten Sie von LEAM und seinem DEMEX-System? Lassen Sie uns dazu einen Kommentar da, oder teilen Sie es uns auf Facebook oder LinkedIN mit. Möchten Sie außerdem eine Zusammenfassung der wichtigsten Neuigkeiten im 3D-Druck und der additiven Fertigung direkt und bequem in Ihr Postfach erhalten? Dann registrieren Sie sich jetzt für unseren wöchentlichen Newsletter.
*Bildnachweise: LEAM