#3DExpress: Universitätsspital Basel stellt Gesichtsimplantat per 3D-Druck am Point-of-Care her
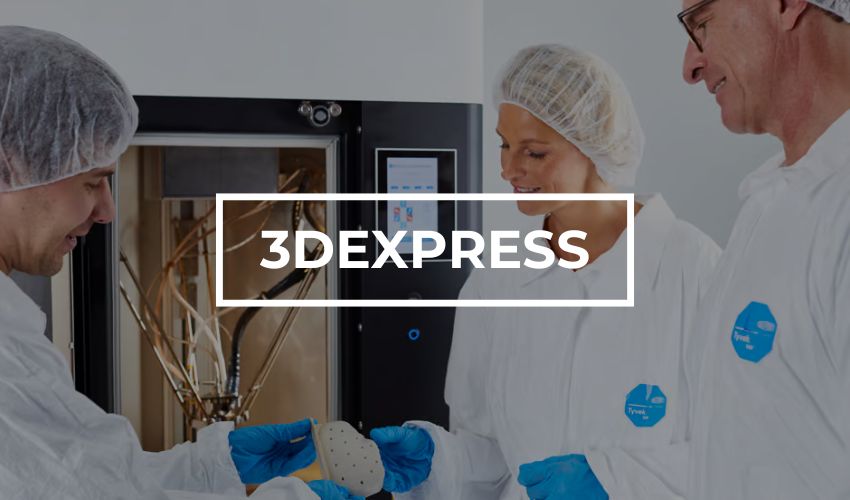
In dieser Ausgabe von #3DExpress präsentieren wir Ihnen erneut fünf spannende Nachrichten aus der Welt des 3D-Drucks, die diese Woche für Aufsehen gesorgt haben. Vorne weg: das 3D-gedruckte Gesichtsimplantat, welches das Universitätsspital Basel vor Ort auf einem medizinischen 3D-Drucker von 3D Systems gefertigt und erfolgreich eingesetzt hat. Außerdem beleuchten wir interessante Forschungsergebnisse des Würzburger SKZ zur nachhaltigen Herstellung on Keramiken. Anschließend werfen wir einen Blick in die Niederlande. Dort haben uns diese Woche gleich drei Projekte beeindruckt. Zum einen ein 3D-gedruckter Betonbogen, anschließend eine Unterwasserdrohne und zum Abschluss noch eine 3D-gedruckte Brücke aus einem Windturbinenblatt. Viel Spaß beim Lesen und einen schönen Start ins Wochenende!
Universitätsspital Basel druckt Gesichtsimplantat aus PEEK am Point-of-Care
Am 18. März wurde am Universitätsspital Basel das erste 3D-gedruckte Gesichtsimplantat in einer Operation eingesetzt. Das Implantat wurde direkt am Point-of-Care in Abstimmung mit den Patientendaten gefertigt. Dazu nutzte das Spital den medizinischen 3D-Drucker XT 220 MED von 3D Systems. Dieser Drucker wurde konzipiert, um im Reinraum speziell für medizinische Anwendungen genutzt zu werden. Die Nachbearbeitungsprozesse sind ebenfalls validiert. Das PEEK-Material stammt von Evonik, genauer gesagt wurde das Material VESTAKEEP® i4 3DF genutzt. In diesem Fall ermöglichte die vor-Ort-Fertigung, dass Ärzte und Techniker eng miteinander arbeiteten, sodass ein passgenaues Implantat für den Patienten gefertigt werden konnte. Prof. Florian Thieringer vom Universitätsspital Basel bringt die Vorteile des 3D-Drucks am Point-of-Care auf den Punkt: „Durch die direkte Einbindung hier im Krankenhaus sowohl in das Design als auch in die Herstellung patientenspezifischer Implantate können wir Behandlungen exakt auf individuelle Bedürfnisse abstimmen, schneller reagieren und die OP-Ergebnisse verbessern.“
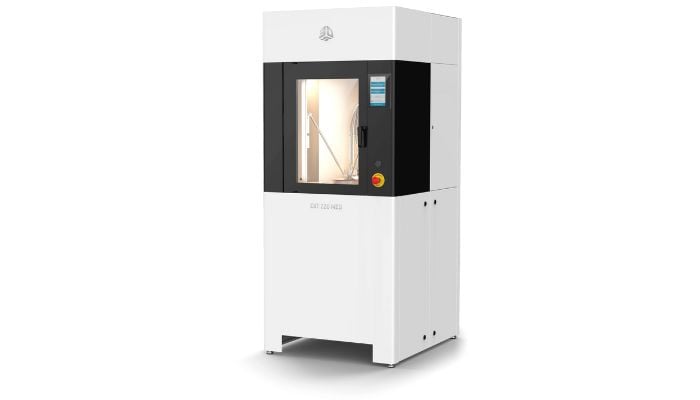
Bild: 3D Systems
SKZ erforscht Wege für nachhaltige Herstellung von SiSiC-Keramiken
Das in Würzburg ansässige SKZ arbeitete über beinahe drei Jahre hinweg an einem Projekt, um nachhaltige SiSiC-Teile herstellen zu können. Ende Januar 2025 wurde „3D-Druck von WPC zur Herstellung endkonturnaher komplexer SiSiC-Bauteile“ erfolgreich abgeschlossen werden. Um Bauteile aus siliziuminfiltrierten Siliziumkarbid-Keramiken zu erhalten, stüzten sich die Forscher auf den 3D-Druck von WPC (Wood-Plastic-Composite)-Grünkörpern. Diese wurden per FFF/FGF-Verfahren gedruckt, anschließend pyrolisiert und mit Silizium infiltriert. Auf diese Weise gelang des dem Team, hochwertige SiSiC-Keramiken zu erhalten. Darüberhinaus konnte der Pyrolyse-Prozess optimiert werden, sodass sich die Qualität der Bauteile zusätzlich verbesserte. In diesem Fall konnte gezeigt werden, dass AM die Herstellung von Teilen aus anspruchsvollen Materialien effizienter und nachhaltiger gestalten kann.
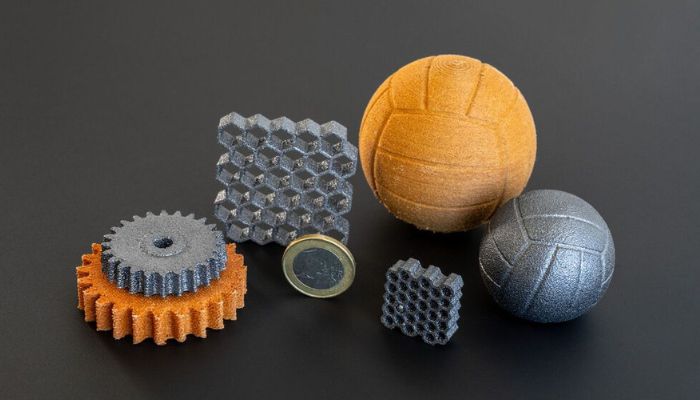
Hier die Demonstratoren (holzfarbene Bauteile), sowie die daraus entstandenen SiC-Keramiken nach der Silizierung (silberfarbene Bauteile). (Bild: SKZ / L. Hoffmannbeck)
Vertico und Zaha Hadid Architects drucken einen Bogen aus Beton
Das niederländische Unternehmen Vertico stellte diese Woche sein neues 3D-Druckprojekt vor: In Zusammenarbeit mit Zaha Hadid Architects entwarf es einen Bogen mit dem Namen Aevum für die INTERNI-Ausstellung ‚Cre-Action‘ an der Universität Mailand La Statale. Es handelt sich um eine 6 x 6 Meter große Struktur, die zwei Bögen kombiniert: Einer ist aus Marmor und wurde auf traditionelle Weise hergestellt, während der andere aus Beton in 3D gedruckt wurde. Laut Vertico dauerte es nur zwei Wochen vom Erhalt des CAD-Modells bis zur Lieferung aller Komponenten, d. h. 21 Stück. Der Druck selbst soll nur 48 Stunden gedauert haben. Mit dieser Struktur soll gezeigt werden, dass es in der Architektur möglich ist, handwerkliches Können mit modernster Technologie zu kombinieren. Volker Ruitinga, CEO von Vertico, fügte hinzu: „Dieses Projekt ist ein echter Meilenstein, denn es begründet die Legitimität von 3D-gedrucktem Beton, indem es ihn neben die Handwerkskunst des Marmors stellt. Die Schnelligkeit, die niedrigen Kosten, die Formfreiheit und die kurzen Lieferzeiten, die die additive Fertigung verspricht, werden hier deutlich.„
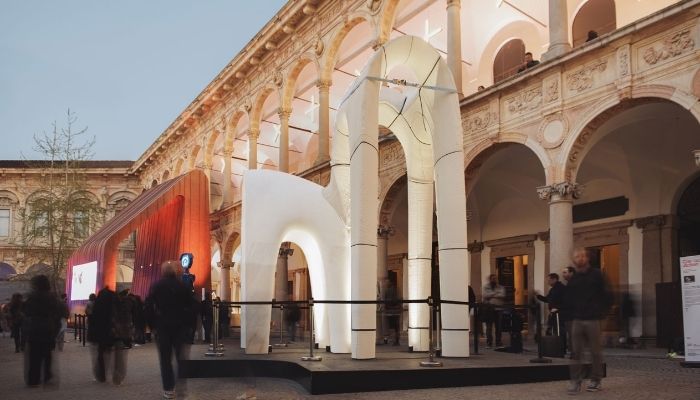
Bild: Vertico
ROYAL3D stellt Prototyp einer Wasserdrohne für maritime Einsätze vor
Bleiben wir in den Niederlanden: Royal3D, ein niederländisches Unternehmen, das sich auf 3D-Druckdienstleistungen spezialisiert hat, hat den Prototyp der ShearWater Aquatic Drone vorgestellt, einer autonomen Drohne, die für Einsätze im maritimen Bereich konzipiert wurde. Diese modulare und parametrische Drohne soll den maritimen Betrieb verbessern, indem sie die Überwachung, Datenerfassung und Risikominderung in extremen Umgebungen erleichtert. Das Projekt wurde teilweise durch das CrossRoads-Programm der Europäischen Union unterstützt und zeichnet sich durch die Verwendung der fortschrittlichen 3D-Drucktechnik von Royal3D aus, bei der Infrarotkameras eingesetzt werden, um die Haftung der Schichten während des Herstellungsprozesses genau zu kontrollieren. Der ShearWater besteht aus Polymeren, die mit PETG-Fasern verstärkt sind, was ihm eine Kombination aus Leichtigkeit, Steifigkeit und Haltbarkeit verleiht. Darüber hinaus sind alle verwendeten Materialien recycelt und wiederverwertbar. Obwohl es sich bei der Drohne nur um einen Prototyp handelt, hat Royal3D erklärt, dass sie ein Sprungbrett für Unternehmen ist, die ihre eigenen autonomen Systeme in den maritimen Betrieb integrieren wollen.
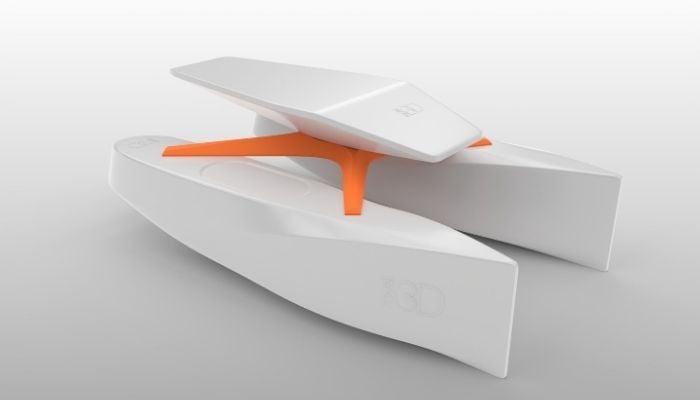
Bild: ROYAL3D
Eine 3D-gedruckte Brücke aus einem Windturbinenblatt
Ist es ein Propeller, ein Windturbinenblatt oder eine Brücke? Ein niederländisches Unternehmen hat etwas ziemlich Bemerkenswertes getan, indem es ein ausgemustertes Windturbinenblatt zur Herstellung einer modularen 3D-gedruckten Brücke umfunktioniert hat. Die endgültige Struktur wurde von Poly Products, einem Unternehmen, das für seine Expertise in der Verarbeitung von Verbundwerkstoffen bekannt ist, im Rahmen des Circular Viaduct Project hergestellt, einer Initiative des niederländischen Ministeriums für Infrastruktur und Wasserwirtschaft. Das Ziel? Eine innovative Brücke zu schaffen und gleichzeitig die Flügel eines nahe gelegenen Windparks wiederzuverwenden, der stillgelegt wurde. Das Ergebnis ist eine Brücke mit einer Spannweite von zwölf Metern und einer Breite von drei Metern, die Lasten von bis zu fünf Tonnen tragen kann. Und das Beste daran? Bei dem Projekt konnte das Potential der Windturbinenflügel voll ausgeschöpft werden, die stark, leicht und äußerst witterungsbeständig sind – also genau das, was für eine Brücke benötigt wird – und dazu beitragen, den Einsatz neuer Rohstoffe zu minimieren. Das nennen wir reduzieren, wiederverwenden, recyceln!
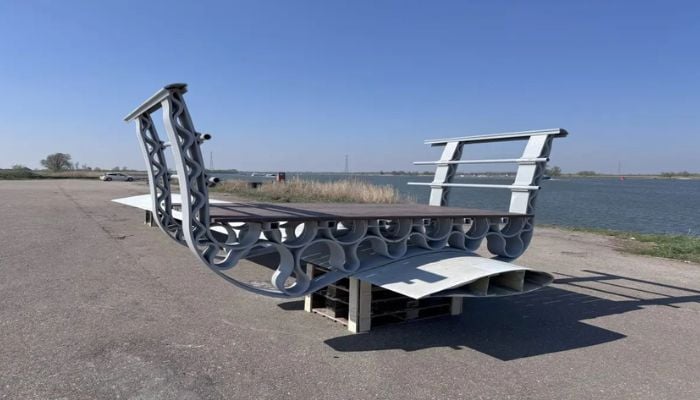
Bild: Poly Products
Was halten Sie vom 3D-gedruckten Gesichtsimplantat am Universitätsspital Basel? Lassen Sie uns dazu einen Kommentar da, oder teilen Sie es uns auf Facebook oder LinkedIN mit. Wenn Sie mehr zum 3D-Druck in der Medizin lesen möchten, schauen Sie auf unserer Landing Page vorbei. Möchten Sie außerdem eine Zusammenfassung der wichtigsten Neuigkeiten im 3D-Druck und der additiven Fertigung direkt und bequem in Ihr Postfach erhalten? Dann registrieren Sie sich jetzt für unseren wöchentlichen Newsletter.
*Titelbildnachweis: 3D Systems