#3DExpress: Das war die 21. Ausgabe der rapid.tech 3D
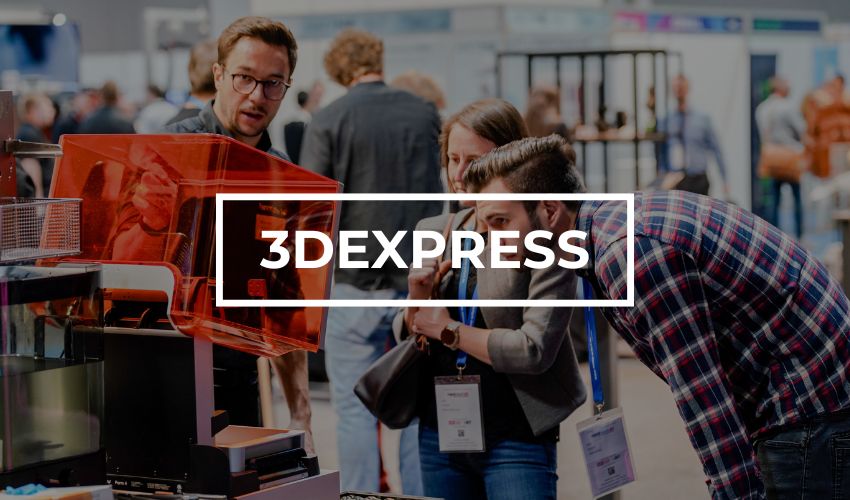
Wieder ist eine Woche um und in #3DExpress lesen Sie, was in den letzten Tagen los war. Dieses Mal auf dem Programm: Eindrücke von der rapid.tech 3D 2025 in Erfurt, das neue Prüflabor des Fraunhofer IMTE in Lübeck und der Easy Metal Printer. Abseits von Deutschland präsentieren wir Ihnen auch neue Materialien für den 3D-Druck im Weltraum und Entwicklungen beim holländischen Unternehmen MX3D. Viel Spaß beim Lesen von #3DExpress und einen guten Start ins Wochenende.
rapid.tech 3D 2025 lockt „die richtigen Besucher“
In den vergangenen Tagen ging die rapid.tech 3D 2025 in Erfurt über die Bühne. Rund 170 Aussteller waren präsent und demonstrierten neue Innovationen und Anwendungen. Darüber hinaus wurden auch zahlreiche Fachvorträge – vier Keynotes und 60 Vorträge – dargeboten. Die Mischung aus wissenschaftlichen Beiträgen und Anwendungs-orientierten Präsentationen deckten zahlreiche Sparten ab, sodass für jeden Besucher Mehrwert geboten wurde. Ein besonderes Interesse kam den Veranstaltern zufolge dem Thema „Qualifizierung von AM“ zu und dem günstigen 3D-Druck im Großformat oder Photonen-Bereich. Auch aktuelle politische und Branchen-interne Entwicklungen wurden diskutiert. Im Fokus: Wie wirken sich die Entscheidungen der US-Regierung auf die AM-Branche aus? Wie der Vormarsch Chinas in der Szene? Wie jedes Jahr wurden auch einige Auszeichnungen in unterschiedlichen Bewerben im Rahmen der rapid.tech 3D verliehen. Die 3D Pioneers Challenge kürte in diesem Jahr die innovativste Entwicklung seit Bestehen des Bewerbs und zeichnete den Pionier der Dekade aus. Das Team des Dvirs Lab der Tel Aviv University konnten diesen Wettbewerb mit einem 3D-gedruckten, schlagenden Herz aus Stammzellen für sich entscheiden. Die Physiker Dr. Dieter Schwarze und Dr. Matthias Fockele wurden als Wegbereiter des 3D-Metalldrucks mit dem „Big Five Award“ ausgezeichnet. Stefan Brenner von der Universität der Bundeswehr München hingegen erhielt den Best Paper Award. 2026 findet die rapid.tech 3D vom 5. Bis 7. Mai statt.
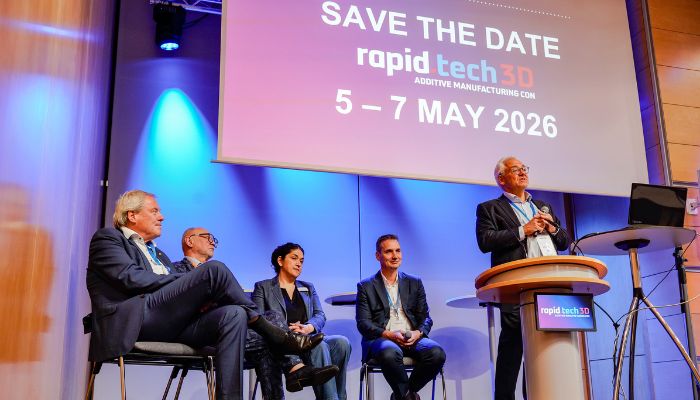
Im Abschluss-Panel der rapid.tech 3D diskutierten die Fachbeiratsmitglieder Michael Eichmann/Stratasys, Carl Fruth/FIT, Dr. Özlem Weiss/Expertants und Martin Neff/ARBURGadditive mit Moderator Dr. Eric Klemp/Whitecell Eisenhuth (v. L.) die Frage, wie man mit additiver Fertigung Geld verdienen kann. (Bild: Christian Seeling/Messe Erfurt)
Fraunhofer IMTE eröffnet Prüflabor für AM in der Medizin
3D-gedruckte medizinische Hilfsgeräte und Implantate müssen passgenau auf die Bedürfnisse des Patienten abgestimmt sein und aus Sicherheitsgründen zahlreichen Normen entsprechen. Um dies sicherzustellen, sind diverse Prüfungen erforderlich. Das Fraunhofer IMTE (Einrichtung für Individualisierte und Zellbasierte Medizintechnik) in Lübeck hat nun sein Prüflabor für AM in der Medizin in Lübeck eröffnet. Es wurde von der Deutschen Akkreditierungsstelle nach internationaler Norm ISO 17025 akkreditiert, d.h. es kann und darf Prüfergebnisse zuverlässig und genau bereitstellen. Das Labor ist aber nicht nur für die universitäre Forschung relevant, auch Kliniken und Unternehmen können auf die Dienste und Expertise zugreifen. „Die Personalisierung in der Gesundheitsversorgung kann nur gelingen, wenn neue Fertigungstechnologien wie der 3D-Druck verlässlich geprüft und validiert werden. Genau hier setzt dieses Labor an“, betonte Staatssekretärin Julia Carstens in ihrem Grußwort bei der Eröffnung. Prof. Dr. Thorsten M. Buzug, Direktor des Fraunhofer IMTE, setzt nach: „Nichts steht so exemplarisch für die Individualisierung in der Medizintechnik wie die Additive Fertigung. Doch Qualitätssicherung ist der Schlüssel zur Umsetzung. Mit diesem Prüflabor können wir nun nachweisen, dass exakt das produziert wurde, was geplant war.“
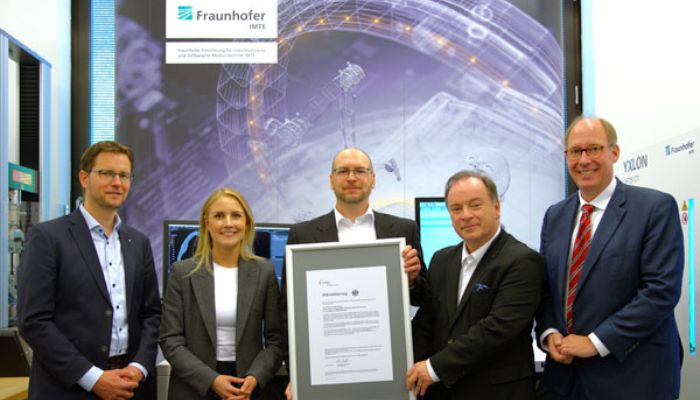
Prof. Philipp Rostalski, Staatssekretärin Julia Carstens, der Leiter der Prüflabors Dr. Thomas Friedrich, Prof. Thorsten Buzug und der Präsidenten der Universität zu Lübeck Prof. Helge Braun. (Bild: Fraunhofer)
Easy Metal Printer entsteht aus Zusammenarbeit von Forschung und Industrie in Stuttgart
Die Institute für Strahlwerkzeuge und Steuerungstechnik der Werkzeugmaschinen und Fertigungseinrichtungen der Universität Stuttgart entwickelten in enger Kollaboration mit Precitec GmbH & Co KG ein effizientes Metall-3D-Druck-Verfahren. Innovation wird laut den Beteiligten des Projektes nicht mehr nur in der Forschung oder in der Industrie geschaffen. Stattdessen müssen beide als Partner zusammenarbeiten, um schnell, wirklich innovative Lösungsansätze zu entwickeln. So Thomas Graf der Universität Stuttgart: „Die Zusammenarbeit ist für alle Beteiligten ein Gewinn. Unsere Erfahrung ist, dass sich die wissenschaftlichen und industriellen Perspektiven ideal ergänzen“. Die Zusammenarbeit resultierte in dem sogenannten Easy Metal Printer, welcher in kürzester Zeit im Rahmen der InnovationChallenge des InnovationsCampus Mobiltät der Zukunft (ICM) gefertigt wurde. Der Drucker funktioniert mittels des koaxialen Laserdrahtauftragschweißens. Hier wird Metall in Drahtform punktgenau geschmolzen und schichtweise auf ein Trägermaterial gedruckt. Im Gegensatz zu Pulverbettverfahren ist der Material- und Energieverbrauch deutlich geringer. Zudem ermöglicht die Technologie neue Designfreiheiten für die Herstellung komplexer technischer Komponenten.
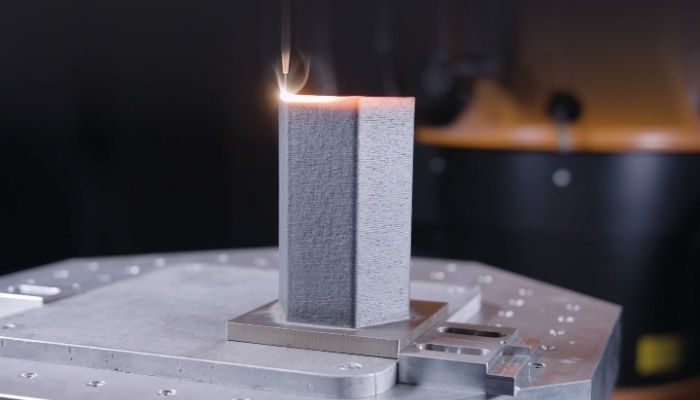
Das Verfahren ganz nah – Hier sehen Sie die Herstellung eines Bauteils im Easy Metal Printer (Bild: Precitec)
Testen von Materialien für den 3D-Druck im Weltraum
An der Universität Glasgow bewegt sich etwas im Bereich der additiven Fertigung, insbesondere in der Materialforschung. So wurde gerade der Start einer Einrichtung angekündigt, in der Materialien für den 3D-Druck im Weltraum, d. h. in der Schwerelosigkeit, getestet werden sollen. Diese Anlage soll die Bedingungen im Weltraum nachbilden, um zu verstehen, wie sich ein bestimmtes Material verhält, wenn es in 3D gedruckt wird. Die Anlage, die den Namen NextSpace Testrig trägt und von Dr. Gilles Bailet entworfen wurde, enthält eine speziell entwickelte Vakuumkammer, die Temperaturen zwischen -150 °C und +250 °C erzeugen kann. Die Ingenieure, die hinter dem Projekt stehen, sind natürlich von den Vorteilen der additiven Fertigung im Weltraum überzeugt. Sie warnen jedoch vor den Risiken, die sie mit sich bringen kann: „Allerdings geht dieses Potenzial auch mit einem erheblichen Risiko einher, das noch verstärkt wird, wenn die Bemühungen, den 3D-Druck im Weltraum einzuführen, überstürzt statt angemessen getestet werden. Objekte bewegen sich in der Umlaufbahn sehr schnell, und wenn sich ein Stück einer schlecht gefertigten Struktur löst, wird es schließlich mit der Geschwindigkeit einer Gewehrkugel um die Erde kreisen. Wenn es auf ein anderes Objekt wie einen Satelliten oder ein Raumfahrzeug trifft, kann es katastrophale Schäden verursachen und das Risiko von Kaskadenproblemen erhöhen, da die Trümmer von jeder Kollision weitere Schäden an anderen Objekten verursachen.“ NextSpace Testrig zielt daher darauf ab, diese Risiken zu verringern – bislang wurden zahlreiche Materialien getestet. Die Anlage kann tatsächlich 20 Kilonewton Kraft aufbringen, um die Proben zu zerbrechen und ihre Eigenschaften unter Mikrogravitationsbedingungen zu analysieren. Sie können auch extremen Temperaturen ausgesetzt werden, ähnlich denen, die im Weltraum herrschen werden.
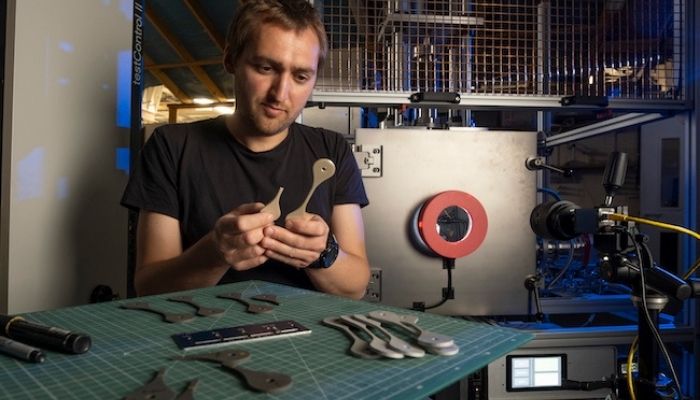
Charlie Patterson untersucht Proben von 3D-gedruckten Materialien (Bild: University of Glasgow)
7 Millionen Euro für MX3D
In einem unsicheren wirtschaftlichen Umfeld, auch wenn sich das Marktwachstum stabilisiert zu haben scheint, hat das niederländische Unternehmen MX3D gerade eine erfolgreiche Kapitalbeschaffung in Höhe von 7 Millionen Euro bekannt gegeben. Das Unternehmen ist auf die Entwicklung von robotergestützten 3D-Drucklösungen spezialisiert, genauer gesagt auf das WAAM-Verfahren, mit dem großformatige Metallteile hergestellt werden können. Diese Finanzierung wurde von EDF Pulse Ventures, dem Risikokapital-Investitionsarm des führenden französischen Energieunternehmens EDF, angeführt. Die Finanzierungsrunde sollte es dem niederländischen Hersteller ermöglichen, seine internationale Entwicklung zu beschleunigen und neue Nutzer aus allen Branchen zu gewinnen. Julien Villeret, Direktor für Innovation der EDF-Gruppe, fasst zusammen: „Die Investition von EDF Pulse Ventures in MX3D zeigt unser Engagement für die Förderung von Spitzentechnologien, die eine kohlenstoffneutrale Zukunft unterstützen. Bei EDF sehen wir mehrere Vorteile in der Nutzung der additiven Metallfertigung in unserer Branche, darunter Kosten- und Zeitersparnisse. Daher sind wir stolz darauf, zur weltweiten Expansion von MX3D beizutragen.“

Bild: MX3D
Waren Sie auf der rapid.tech 3D 2025? Lassen Sie uns dazu einen Kommentar da, oder teilen Sie es uns auf Facebook oder LinkedIN mit. Wenn Sie mehr zum 3D-Druck in der Medizin lesen möchten, schauen Sie auf unserer Landing Page vorbei. Möchten Sie außerdem eine Zusammenfassung der wichtigsten Neuigkeiten im 3D-Druck und der additiven Fertigung direkt und bequem in Ihr Postfach erhalten? Dann registrieren Sie sich jetzt für unseren wöchentlichen Newsletter.