#3DExpress: NEVO3D und KIMYA führen kostengünstiges 3D-Druckmaterial für die Bahnindustrie ein
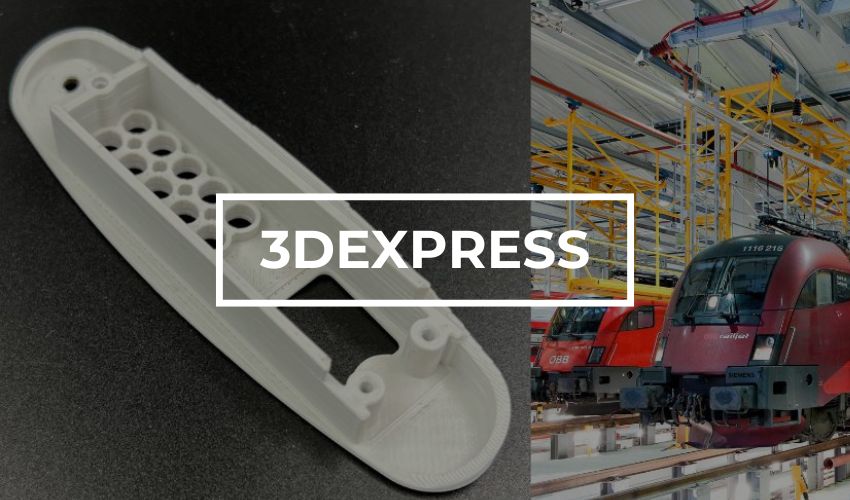
Es ist mal wieder Freitag und Zeit für #3DExpress, dem Format, in dem wir einige wichtige Nachrichten aus der Welt der additiven Fertigung bündeln. Mit #3DExpress bleiben Sie auf dem Laufenden und erfahren in aller Kürze, was in der Industrie vor sich geht. Diese Woche berichten wir über NEVO3D und KIMYA, die mit neuen Materialien für die Bahnindustrie aufzeigen. Außerdem erfahren Sie, wie es mit dem Startup Apium Additive Technologies weitergehen wird. Bevor es ins Wochenende geht, lesen Sie noch von Solukon und der Aufrüstung seiner Nachbearbeitungsanlage und von Prodways, das mit dem amerikanischen Unternehmen Honeywell kooperiert. Zum Schluss dieser #3DExpress-News stellen wir Ihnen auch noch ein Projekt zur Erhaltung der Ozeane durch 3D-Druck vor. Viel Spaß beim Lesen und ein schönes Wochenende!
NEVO3D und KIMYA führen neues Material für die Bahnindustrie ein
Wie wir wissen, wird der 3D-Druck bei der Bahn immer häufiger eingesetzt, da durch die additive Fertigung Reparaturen umgesetzt werden können und Bauteile gedruckt werden können, die nicht mehr herkömmlich hergestellt werden. Dies trägt dazu bei, die bestehenden Elemente in den Zügen noch länger nutzen zu können und 3D-Druck ermöglicht eine effektive Wartung. Die verwendeten Materialien müssen allerdings den vorherrschenden Normen entsprechen, vor allem Brandschutzstandards nach EN-45545-2 R1/HL3 sind relevant. NEVO3D (ehemals EVO-tech) hat sich mit dem Materialhersteller KIMYA zusammengetan, um die ÖBB bei der Anwendung der additiven Fertigung in den Zügen mit einem zertifizierten Material zu unterstützen. Die neue Lösung der Partner basiert auf Polycarbonat und E-140 und erreicht eine Kostenersparnis von bis zu 80 %. Dies wird einerseits durch die geringeren Materialkosten erreicht, andererseits auch durch die niedrigeren Anforderungen an die verarbeitenden 3D-Drucker. Ziel der Partner, ist es, die ÖBB bei ihren Zielen zu unterstützen und vielversprechende Materiallösungen für die Bahnindustrie anzubieten. Sebastian Otto, Leiter Additive Fertigung bei ÖBB Technische Services GmbH skizziert den Einsatz von 3D-Druck und die Ziele der ÖBB: „Schon heute fahren über 40.000 3D gedruckte Bauteile auf österreichischen Schienen. Wir haben bereits knapp 1000 3D druckfähige Bauteile in unserem virtuellen Ersatzteil- und Modernisierungslager. Unser Ziel ist es, bis 2028 die Anzahl auf 5000 digitalisierte Bauteile zu erhöhen.“
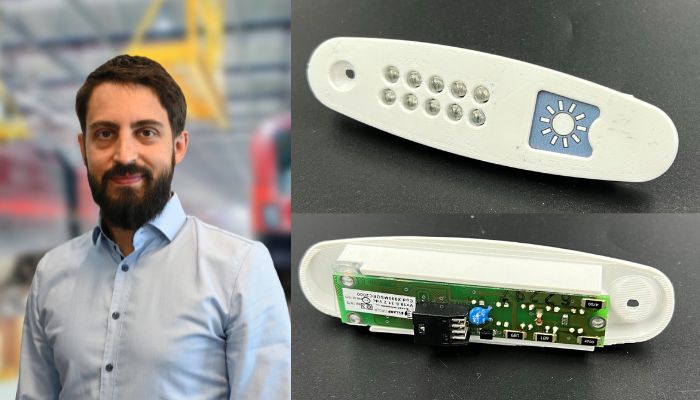
Sebastian Otto, Leiter Additive Fertigung bei der ÖBB (Bild: ÖBB)
Apium Additive Technologies bereitet Neustart vor
Das 2016 gegründete Startup Apium Additive Technologies konzentrierte sich bislang auf die Herstellung von FDM-Maschinen mit einer hauseigenen Technologie. Diese patentierte Technologie verarbeitet Hochleistungsthermoplasten zu medizinischen Implantaten, welche einen schnelleren Behandlungserfolg für die betroffenen Patienten ermöglichen. Nun kann der derzeitige Investor keine Mittel mehr bereitstellen, um das Unternehmen weiter zu unterstützen, seinen Apium P400 Extrusions-3D-Drucker für den medizinischen Markt zu qualifizieren. Das Jungunternehmen, das rund 15 Mitarbeiter beschäftigt, hat sich daher dazu entschlossen, ein Insolvenzverfahren einzuleiten und sich mit neuen Investoren neu aufzustellen. „Wir brauchen frisches Kapital, um diesen Schritt zu wagen. So können wir die Früchte unserer Entwicklungsarbeit der letzten Monate ernten. Unser derzeitiger Investor kann uns dafür jedoch keine zusätzlichen Mittel zur Verfügung stellen“, erklärt Apium-Geschäftsführer Lars Pfotzer. „Wir haben uns daher entschlossen, unser junges Unternehmen im Insolvenzverfahren zu sanieren und die Suche nach Investoren wieder aufzunehmen.“
Solukon rüstet seine SFM-AT350-Lösung auf
Die von Solukon entwickelte Nachbehandlungslösung SFM-AT350, die im Oktober 2021 auf den Markt kam, wurde aufgerüstet und bietet nun eine höhere Kapazität. Das Entstaubungssystem ist nun in der Lage, größere und schwerere Strukturen zu bearbeiten. Während ursprünglich nur Werkstücke bis 60 kg und 350 mm in der X-Achse bearbeitet werden konnten, kann die neue Version nun Werkstücke bis zu 100 kg und Abmessungen von 400 x 400 x 400 x 400 mm oder 500 x 280 x 400 mm bearbeiten. Dank der Anpassung des Armdesigns bleiben das ursprüngliche Kammervolumen und der Inertgasverbrauch bei diesem neuen Upgrade erhalten. Die Lösung SFM-AT350 ist nun mit 3D-Druckern wie der EOS M 400 und der Nikon SLM® 500 kompatibel und eignet sich somit für mittelgroße Teile in der additiven Fertigung. Laut dem Solukon-Team positioniert diese Verbesserung das SFM-AT350 als optimale Lösung für komplexe Bauteile in Branchen wie der Luft- und Raumfahrt und der Medizintechnik.
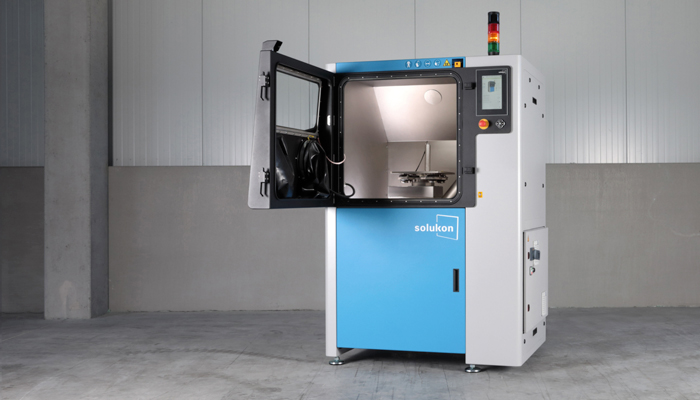
Bild: Solukon
Honeywell wendet sich an Prodways
Das US-amerikanische Unternehmen Honeywell, das für seine Lösungen in den Bereichen Kernkraft, Luft- und Raumfahrt und Bauwesen bekannt ist, hat sich an den französischen Hersteller Prodways gewandt, um den Herstellungsprozess seiner Turboprop-Triebwerke zu verbessern. Das Unternehmen interessierte sich für die 3D-Keramikdrucktechnologie, um Formen für die Herstellung von Turbinenschaufeln zu entwerfen. Vor dem Einsatz der additiven Fertigung verwendete Honeywell das herkömmliche Wachsausschmelzverfahren, das viel zeitaufwändiger und teurer ist. Die Teams erklärten, dass sie eine Turbinenschaufel jetzt in 7 bis 8 Wochen herstellen können, während sie früher ein bis zwei Jahre gebraucht hätten. Außerdem seien die 3D-gedruckten Formen widerstandsfähiger gegen Verschleiß und Korrosion und würden eine ganze Reihe von Tests und Validierungen viel einfacher machen.
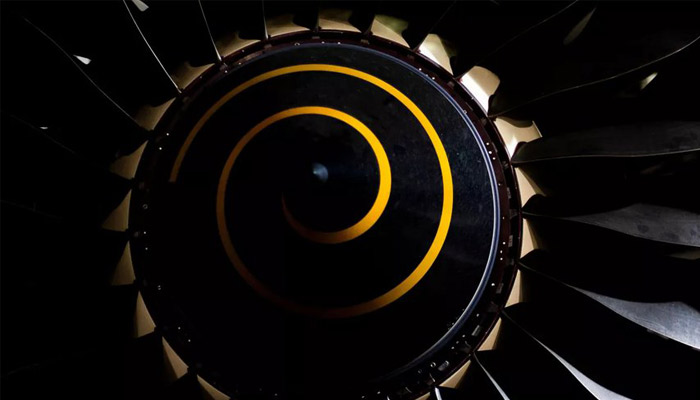
Bild: Honeywell
3D-Druck und die Erhaltung unserer Ozeane
Es ist kein Geheimnis mehr, dass der 3D-Druck immer häufiger eingesetzt wird, um unseren Planeten zu schützen, Recyclinglösungen zu finden oder unsere Ozeane und die Artenvielfalt zu retten. Das Projekt von Eke Panuku und QOROX in Neuseeland ist ein weiteres Beispiel für die Möglichkeiten, die die 3D-Technologie, hier speziell der 3D-Betondruck, bietet. Die beiden Partner stellten sich künstliche Banales, d. h. Meereskrustentiere, vor, die Mikrohabitate bilden und somit als Rückzugsort für verschiedene Meerestiere dienen. Dabei griffen sie auf das von CyBe Construction entwickelte Verfahren zurück.
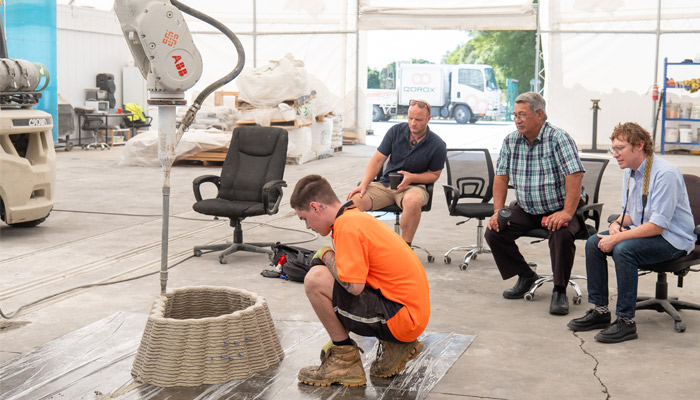
Bild: CyBe Construction
Was halten Sie von unseren #3DExpress-Nachrichten der Woche? Lassen Sie uns dazu einen Kommentar da, oder teilen Sie es uns auf Facebook oder LinkedIN mit. Möchten Sie außerdem eine Zusammenfassung der wichtigsten Neuigkeiten im 3D-Druck und der additiven Fertigung direkt und bequem in Ihr Postfach erhalten? Dann registrieren Sie sich jetzt für unseren wöchentlichen Newsletter.