#3DExpress: Neuer Leiter des AM Campus der BMW Group
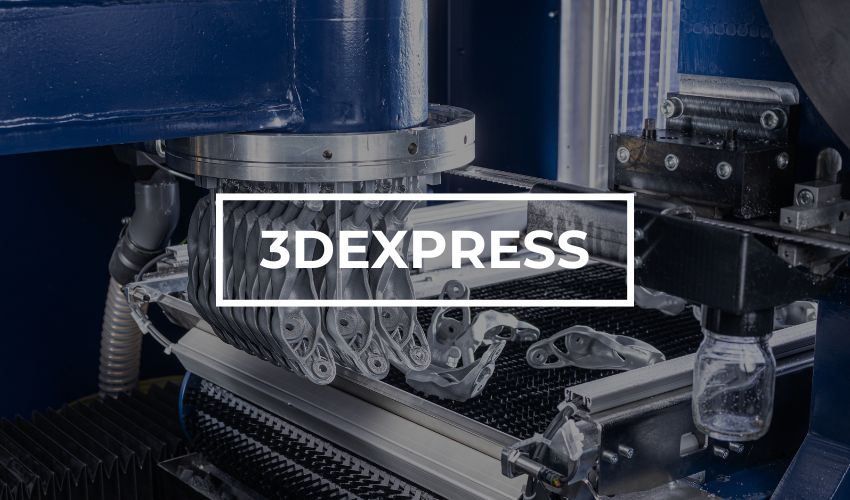
Pünktlich vor dem Wochenende liefern wir Ihnen eine Zusammenfassung davon, was diese Woche in der Welt der additiven Fertigung passiert ist. Wie jeden Freitag lesen Sie in #3DExpress fünf relevante Neuigkeiten aus der AM-Industrie. Diese Woche sprechen wir über die Nachfolge von Jens Ertl als Head of Additive Manufacturing bei der BMW Group. Außerdem erfahren Sie, wie Forward AM trotz der aktuellen Herausforderungen weiterhin seine Kundschaft auf dem nordamerikansichen Markt betreuen möchte. Anschließend berichten wir von einem spannenden Projekt, wie 3D-Scanning zur Erhaltung von Brücken eingesetzt werden kann. Zum Abschluss lernen Sie das neue Material von LEHVOSS kennen und, wie das ATILA-Projekt voranschreitet. Lassen wir die vergangene Woche gemeinsam Revue passieren, bevor es ins Wochenende geht! Viel Spaß beim Lesen!
Timo Goebel tritt Nachfolge von Jens Ertl als Leiter des AM Campus der BMW Group an
BMW startete vor über 30 Jahren seine ersten Versuche mit dem 3D-Druck. Heute wird die additive Fertigung auf vielfältige Weise beim Automobilhersteller eingesetzt, von Fertigungshilfen über Werkzeuge bis hin zu einzelnen Bestandteilen der Autos. Einer, der diesen Weg wesentlich mitgestaltet hat war Jens Ertl. 30 Jahre lang war er bei der BMW Group beschäftigt und hielt in den letzten zwölf Jahre die Position als Head of Additive Manufacturing inne. Die BMW Group konnte im Bereich des 3D-Drucks unter seiner Leitung beeindruckende Fortschritte und Ergebnisse erzielen, darunter die Implementierung von WAAM für großformatige Teile oder einen 3D-gedruckten Roboter-Greifer für die Produktion, um nur einige Beispiele der jüngsten Vergangenheit zu nennen. Nun wird Ertl in den Ruhestand gehen. Auf ihn folgt Timo Goebel, der den AM Campus von nun an leiten wird.
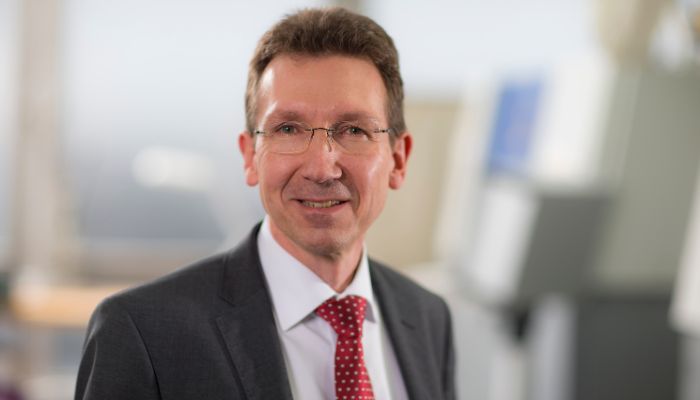
Jens Ertl, langjähriger Head of Additive Manufacturing bei der BMW Group (Bild: BMW Group)
Forward AM verbündet sich mit RP America
Es war ein turbulentes Jahr 2024 für Forward AM. Mitte des Jahres löste sich das Unternehmen durch ein Buy-Out von BASF und konnte als selbstständige Marke auftreten, Ende des Jahres kam es aber zu Turbulenzen. Der Anbieter von 3D-Druckmaterialien musste Insolvenz anmelden und befindet sich in der Umstrukturierung. Eine neue Partnerschaft mit RP America, soll nun dafür sorgen, dass der nordamerikanische Markt weiter bedient werden kann. RP America ist ein Vertriebs- und Serviceanbieter, der sich auch in der Sparte AM bewährt hat, und soll die Verfügbarkeit von Forward AM-Lösungen in den USA, Kanada und Mexiko sicherstellen.

Bild: Forward AM
3D-Scannen im Dienste von Brücken
Brücken sind weltweit verbreitete Bauwerke, die oft von Stahlträgern getragen werden, die mit der Zeit verfallen können. Der Einsturz einer Brücke kann sehr gefährlich sein und in manchen Fällen sogar tödlich enden. Um dies zu verhindern, haben Forscher der Technischen Universität Dresden und der University of Massachusetts in Amherst mithilfe von 3D-Scans, insbesondere mit dem Artec Leo 3D-Scanner, eine Methode zur Inspektion von Brücken entwickelt. Die erhaltenen Daten sind viel detaillierter und der Prozess läuft sehr schnell ab, was eine schnelle Reaktion ermöglicht. Simos Gerasimidis, außerordentlicher Professor an der Universität von Massachusetts in Amherst, erklärt: „Korrosion betrifft normalerweise die Träger, die die Brückendecke stützen. Für eine vollständige Untersuchung eines Trägers muss man eine Seite scannen, anhalten, die Schaufel bewegen und dann die andere Seite scannen. Daher ist es sehr wichtig, dass das Gerät tragbar, vielseitig und leicht zu bewegen ist. Leo zeigt Ihnen auch an, ob Sie zu nah oder zu weit weg sind, sodass Sie vor Ort feststellen können, ob der Scan gut ist oder nicht. Mit Leo sammeln Sie Hunderttausende von Punkten in nur fünf Minuten. Wenn man herkömmliche Methoden anwendet, erfasst man einen Punkt in drei Minuten.“ Aufbauend auf den gescannten Daten gingen die Forscher noch einen Schritt weiter und gaben sie in eine Analysesoftware ein, um Überlastungsszenarien zu entwerfen. Diese dienten als Material, um eine KI so zu trainieren, dass sie sofort die Fähigkeit eines Pulvers, Lasten zu tragen, beurteilen kann.
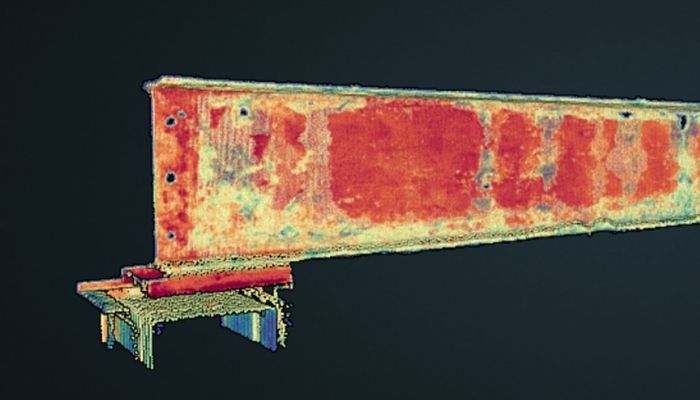
Die Forscher können die Festigkeit von Brückenträgern schneller analysieren (Bild: Artec 3D)
LEHVOSS stellt neue Materialreihe vor
Der Chemiker LEHVOSS hat die Einführung neuer Hochleistungsmaterialien angekündigt, die in Granulatform erhältlich sein werden. LUVOPRINT heißt die Produktreihe, die sich besonders für die Herstellung von Formen, Komponenten und Schablonen für verschiedene Industriezweige eignet. Die Gruppe hat vier Polymertypen entwickelt: ECO PC/ABS, das eine gute Dimensionsstabilität bietet und leicht zu bedrucken ist; ECO PA6, das eine ausgezeichnete Abrieb-, Verschleiß- und Stoßfestigkeit aufweist; ECO PPS, das flammhemmend ist und eine gute chemische Beständigkeit besitzt; und PESU, das ebenfalls flammhemmend ist und eine sehr gute thermische Stabilität und mechanische Festigkeit aufweist. Das Ziel von LEHVOSS ist es, die Einführung der additiven Fertigung zu fördern und Materialien anzubieten, die eine gute Reproduzierbarkeit aufweisen und somit eine Massenproduktion gewährleisten. Die Gruppe wird ihre Granulate offiziell auf der JEC vorstellen, die am 4. März beginnt.
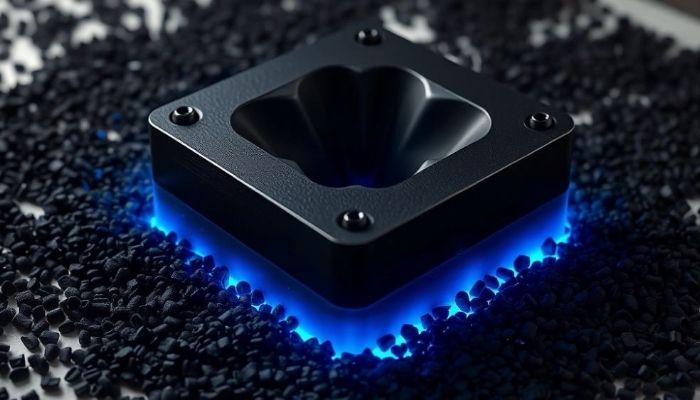
Bild: LEHVOSS
Fortschritte im ATILA-Projekt
Das von der Europäischen Union und dem Ministerium für Wissenschaft und Innovation geförderte Projekt ATILA hat bedeutende Fortschritte bei der Herstellung biomedizinischer Implantate mittels 3D-Druck von Titan erzielt. Durch den Einsatz der Meltio-Technologie, die auf Drahtschweißen anstelle von herkömmlichem Metallpulver basiert, zielt das Projekt darauf ab, Abfall zu reduzieren und die Effizienz zu verbessern. Diese Technik der direkten Abscheidung von Metallenergie ermöglicht die Herstellung hochwertiger Implantate, die auf die spezifischen Bedürfnisse der Patienten zugeschnitten sind. Im Gegensatz zu anderen additiven Fertigungsverfahren fällt bei der Meltio-Technologie weniger Materialabfall an, so dass sie wirtschaftlicher und nachhaltiger ist. Seit Beginn des Projekts hat das Projektkonsortium die geometrischen und thermografischen Grenzen des Verfahrens erforscht und die Herstellung komplexer Implantate für verschiedene Körperteile vorangetrieben. Diese Fortschritte eröffnen neue Möglichkeiten für die individuelle Gestaltung medizinischer Implantate mit hoher Präzision und Effizienz.
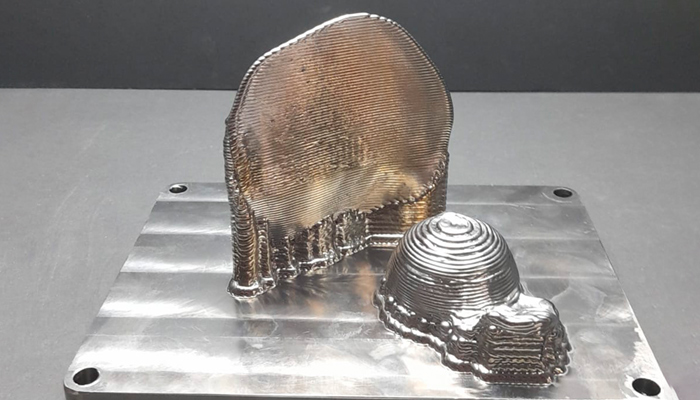
Bild: Meltio
Was halten Sie von unseren #3DExpress-Nachrichten der Woche? Lassen Sie uns dazu einen Kommentar da, oder teilen Sie es uns auf Facebook oder LinkedIN mit. Möchten Sie außerdem eine Zusammenfassung der wichtigsten Neuigkeiten im 3D-Druck und der additiven Fertigung direkt und bequem in Ihr Postfach erhalten? Dann registrieren Sie sich jetzt für unseren wöchentlichen Newsletter.
*Titelbildnachweis: BMW Group