Verbesserung der Leistung von Anwendungen im Energiesektor mit 3D-Metalldruck
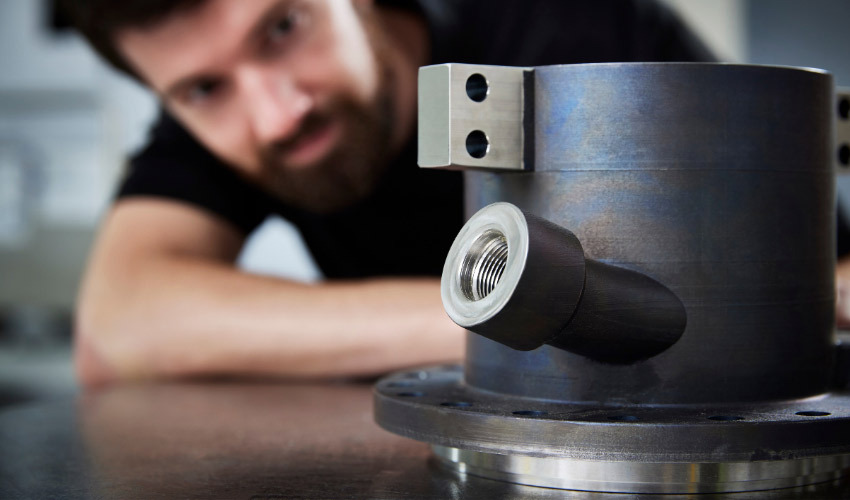
Die additive Metallfertigung wird zunehmend zur Entwicklung der nächsten Generation von Turbomaschinen eingesetzt. Dies sind Maschinen, die Energie zwischen einem Rotor und einem Fluid übertragen, einschließlich Turbinen und Kompressoren. Um in diesem Bereich innovative Designs zu produzieren, ohne lange und teure Entwicklungszyklen in Kauf nehmen zu müssen, investieren Unternehmen in neue Technologien. Zum Beispiel hat Mohawk Innovative Technology vor kurzem die Metalltechnologie von VELO3D in das Kompressordesign eines vom U.S. Department of Energy (DOE) geförderten Concentrated Solar Power (CSP) Projekts integriert. Die Herstellung des Kompressors mit herkömmlichen Methoden, wie Formenbau und Gießen, hätte etwa 20 Wochen gedauert und mehr als 90.000 Dollar gekostet. Stattdessen produzierte Mohawk ein Teil, von Anfang bis Ende, in einem kürzeren Zeitrahmen. Das reduzierte die Kosten um das 2,5-fache. Wie wirkt sich also der 3D-Metalldruck auf den Energiesektor aus?
1994 legten die Mitbegründer Jim Walton und Dr. Hooshang Heshmat ihr Fachwissen in den Bereichen Luft- und Raumfahrt sowie Metallurgie zusammen und gründeten Mohawk Innovative Technology, Inc. Das Unternehmen entwickelt ölfreie Lagertechnik, die in anspruchsvolle Komponenten für die Energie-, Kraftwerks-, Verteidigungs-, Luft- und Raumfahrtindustrie und andere Branchen eingebaut wird. Nach einigen erfolgreichen Projekten, wie z.B. der Entwicklung eines Gussmetall-Radialkompressors für ein Wasserstoff-Transportsystem, haben sie sich für ein neues DOE-gefördertes Projekt qualifiziert.
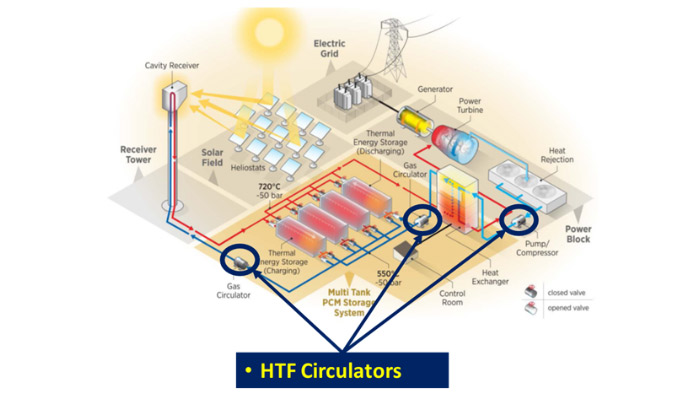
Eine schematische Darstellung der CSP-Anlage. Die Zirkulatoren zur Wärmeübertragung (HTF Cirulators) integrieren Kompressorgehäuse | Bildnachweis: DOE
In diesem Projekt mussten sie Zirkulatoren zur Wärmeübertragung für ein Concentrated Solar Power (CSP)-System entwerfen, das mit der konventionellen Stromerzeugung konkurrenzfähig sein sollte. In einem bestimmten Zusammenhang verwenden CSP-Systeme Spiegel, um das Sonnenlicht zu reflektieren und auf einen Receiver zu konzentrieren. Dort wird das Licht gesammelt und in thermische Energie umgewandelt, die zur Stromerzeugung genutzt wird. In diesem Fall lag die thermische Energie in Form von überkritischem CO2 (s-CO2) vor, das ist der flüssige Zustand von CO2 (wenn CO2 bei oder über seiner kritischen Temperatur und seinem kritischen Druck gehalten wird). Bei extrem hohen Drücken hat s-CO2 die Dichte einer Flüssigkeit, aber die Viskosität eines Gases. Das macht ihn zu einem idealen Leiter für Wärme und Strom, der viel mehr Leistung als Dampf liefert. Es kann auch durch Wärmetauscher komprimiert und in Tanks transportiert werden, um für den Energiebedarf in Spitzenzeiten gespeichert zu werden. Aus diesem Grund begann Mohawk mit der Entwicklung eines Kompressorgehäuses speziell für s-CO2. Darüber hinaus passte die ölfreie Lagertechnologie von Mohawk perfekt, da Öl mit s-CO2 reaktiv ist und eine Korrosion verursacht.
„Unser Ziel war es, die Kosten für die Maschinen zu senken und diese Anlagen rentabler zu machen. Ein einziger Kompressor für ein 100-Megawatt-CSP-System kann zwischen 7 und 20 Millionen Dollar kosten, so dass es eine echte Chance für Designinnovationen zur Unterstützung alternativer Energien gibt. Als das DOE begann, nach Möglichkeiten zu suchen, die Herausforderungen von s-CO2 in CSP anzugehen, wussten wir, dass wir Antworten liefern können.“, erklärt Mr. Walton.
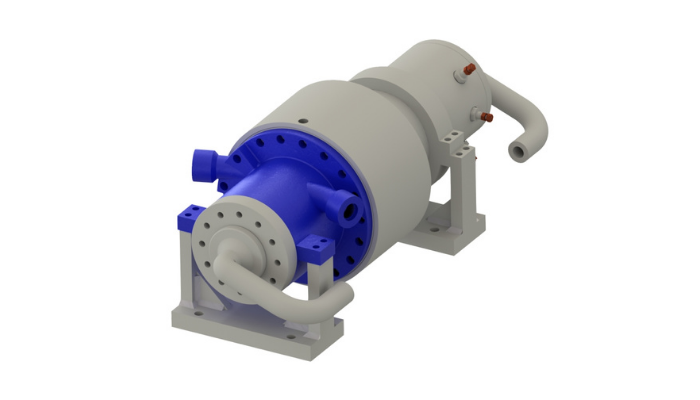
Kunststoffmodell eines HTF-Zirkulators für ein von Mohawk entworfenes CSP-System. Das Teil in Blau ist das Kompressorgehäuse, das in 3D auf dem Sapphire-Drucker von VELO3D gedruckt wurde (Bildnachweis: Mohawk Innovative Technology).
Komplexe Geometrie führt zu einem Umdenken bei Materialien und Fertigung
Das Gehäuse musste nicht nur eine frei drehende Welle tragen, sondern auch Voluten (gekrümmte Kanäle) enthalten, die ein schnelles Ansaugen und Ausstoßen von s-CO2 durch den Kompressor ermöglichen. Chefingenieur Jose Cordova erklärt: „Um so viel Funktionalität in einem konventionellen Kompressordesign zu bieten, wäre eine Kombination aus drei separaten Teilen erforderlich gewesen. Darüber hinaus wussten wir, dass wir angesichts der Drücke und der extremen Temperaturen (50-550°C), denen das in diesem System zirkulierende s-CO2 ausgesetzt ist, eine Superlegierung auf Nickelbasis wie Inconel verwenden mussten. Diese ist bekanntermaßen schwer zu gießen.“ So wurde dem Team schnell klar, dass sie dieses Teil nicht mit traditionellen Methoden herstellen konnten. Und selbst bestehende 3D-Druckverfahren würden Rauigkeiten erzeugen, die die Effizienz beeinträchtigen.
Deshalb entschied sich Mohawk für eine Partnerschaft mit VELO3D, dem Entwickler der stützfreien additiven Metall-Fertigungstechnologie auf Basis des Laserschmelzens. Nach erfolgreichen Zugtests an 3D-gedruckten Inconel-Rohlingen erhielt das Projekt grünes Licht von Dr. Heshmat. Gene Miller, Anwendungstechniker bei VELO3D, sagt: „Es gab viele schwierige Winkel, die typischerweise Stützkonstruktionen erforderten, was nur weitere Kompromisse für das Design und die Leistung bedeutete. Unsere Technologie ermöglicht es, Null-Grad-Winkel ohne Unterstützung zu drucken, was für die Innenspiralen notwendig war.“ Mit dem 3D-Druck waren sie auch in der Lage, ein einziges Verbunddesign zu erstellen, anstatt drei Teile zu kombinieren. Das zeigt das Potenzial, das der 3D-Metalldruck für den Energiesektor birgt.
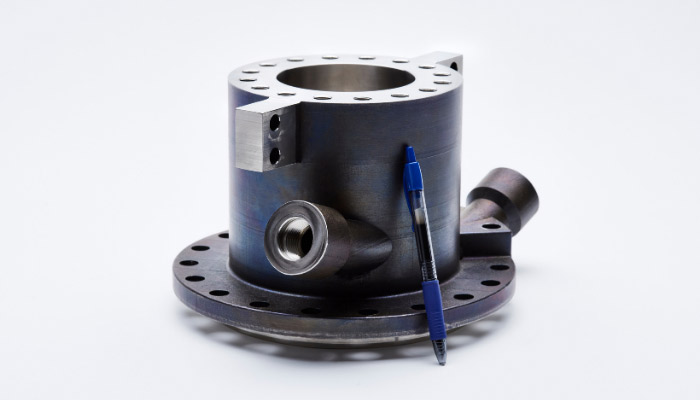
Ein Teil des Kompressorgehäuses, das auf der VELO3D Sapphire-Maschine dank der metallischen additiven Fertigungstechnologie ohne Hilfsstrukturen in 3D gedruckt wurde.
VELO3Ds additiver Fertigungsablauf
Um das Design für den 3D-Druck einzurichten, wurde die native CAD-Datei vor dem Druck in VELO3Ds Software Flow eingeführt. Nachdem das Design in der Software eingerichtet war, wurde das Inconel-Teil in etwa 3,5 Tagen auf dem Sapphire-System von Duncan Machine Products (dem Auftragshersteller für dieses Projekt) gedruckt. Die Software Assure von VELO3D überwachte den Prozess und meldete kritische Aspekte in Echtzeit, sowie nicht-normale Messungen. Die Software erfasst die relevanten Datenpunkte zusammen mit einer Trendanalyse in einem umfassenden Konstruktionsbericht, der dem Endanwender wichtige Informationen liefert. Reproduzierbare und wiederholbare Ergebnisse sind für Endanwender essentiell, um Vertrauen in den additiven Fertigungsprozess zu haben. Deshalb hat sich VELO3D auf die Entwicklung und Verbesserung dieser Softwarelösung konzentriert.
3D-Metalldruck: die Zukunft der grünen Technologien?
Die Mohawk-Ingenieure erklärten, dass sie vom Potenzial der additiven Fertigung begeistert sind und glauben, dass sie in Zukunft einen großen Einfluss auf ihr Geschäft haben könnte. Walton kommentiert: „Der 3D-Druck eröffnet uns neue Märkte und passt perfekt zu uns, da wir uns auf maßgeschneiderte Maschinen spezialisiert haben. Es schafft zweifellos neue Möglichkeiten für kostengünstiges Prototyping sowie die kostengünstige Herstellung von Produktionsteilen für kundenspezifische Systeme.“ In der Tat mussten die Ingenieure keine Kompromisse bei der Designabsicht eingehen. Mit dem 3D-Metalldruck waren sie in der Lage, schneller zu innovieren und die Herstellungskosten zu senken, während sie gleichzeitig die Leistung erhöhten, was den Weg für Anwendungen im Energiesektor ebnet! Weitere Informationen über die Technologie und die Anwendungen von VELO3D finden Sie auf der offiziellen Website des Unternehmens.
Kann der 3D-Metalldruck den Energiesektor verbessern? Lassen Sie uns dazu einen Kommentar da, oder teilen Sie es uns auf Facebook, Twitter, LinkedIN oder Xing mit. Möchten Sie außerdem eine Zusammenfassung der wichtigsten Neuigkeiten im 3D-Druck und der Additiven Fertigung direkt und bequem in Ihr Postfach erhalten? Dann registrieren Sie sich jetzt für unseren wöchentlichen Newsletter.