3D-gedruckte Träger aus recyceltem Kunststoff als Ersatz für Stahlbeton
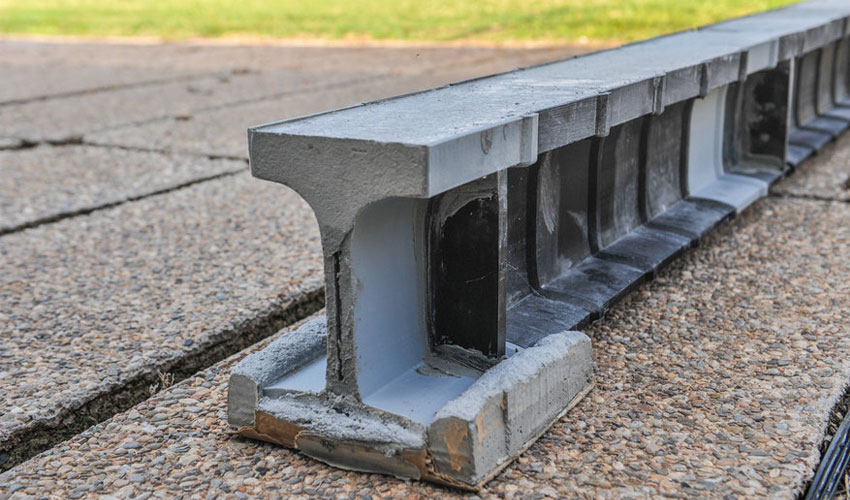
Ein Team der Polytechnischen Universität Valencia (UPV) hat eine Alternative zu den im Bausektor verwendeten Stahlbetonträgern entwickelt: 3D-gedruckte Träger, die aus recyceltem Kunststoff gefertigt werden. Das Ergebnis ist eine drastische Gewichtsreduzierung – denn diese Träger wiegen 80 % weniger als aktuelle Lösungen, was den Transport erheblich erleichtert und den Energieaufwand für die Montage reduziert. Die verschiedenen 3D-gedruckten Komponenten, die den Balken bilden, können so einfach wie LEGO-Steine zusammengesetzt werden.
Der im Bausektor sehr beliebte Stahlbeton besteht, wie der Name schon sagt, aus Beton und Metall (meist Stahl). Es handelt sich also um einen Verbundwerkstoff, der Zug- und Druckbelastungen standhält und in der Lage ist, erhebliche Lasten zu tragen. Zugleich ist es jedoch ein Material, das schwer zu transportieren ist, da Stahl das Gewicht des Trägers erheblich erhöht. Die Forscher haben deshalb versucht, diese Einschränkung so weit wie möglich zu reduzieren. Seit 3 Jahren arbeiten sie an diesem 3D-Druck-Projekt. José Ramón Albiol, Professor an der Technischen Hochschule für Bauwesen (ETSIE) der UPV, fügt hinzu: „Unser Ziel war es, eine Alternative zu den derzeitigen Stahlbetonstrukturen vorzuschlagen. Diese bestehen aus Profilen, die über die gesamte Länge des Raumes gebaut werden, was teure Installationen erfordert und schwer zu transportieren ist.„

Die verschiedenen 3D-gedruckten Blöcke können wie LEGOs zusammengesetzt werden. (Bildnachweis: UPV)
3D-gedruckte Träger inspiriert von menschlichen Knochen
Über das verwendete 3D-Druckverfahren bleiben die Forscher eher diskret. Eines ist jedoch sicher: Um den ökologischen Fußabdruck zu reduzieren, entschied sich das Forschungsteam bewusst für recycelten Kunststoff als 3D-Druck-Material. Außerdem ließen sie sich bei der Gestaltung ihrer 3D-Modelle von der Form der Knochen inspirieren. Ziel war es, die Struktur der Epiphyse, des Endstücks der Knochen, nachzubilden: Sie besteht aus mehreren Schichten, die ihr eine hohe Steifigkeit verleihen und nichtsdestotrotz ist sie zeitgleich recht leicht. Dank der additiven Fertigung konnten die Forscher diese Alveolenstruktur nachahmen und das Material dort einsetzen, wo es gebraucht wurde.
Das Ergebnis ist eine Reduzierung des Gesamtgewichts durch eine bessere Verteilung des Materials und durch die Verwendung von Kunststoff anstelle von Stahl. José Ramón Albiol fährt fort: „Es handelt sich um eine Wabenstruktur, die es uns ermöglicht, den verwendeten Kunststoff – und damit das Gewicht – zu reduzieren, während die strukturelle Steifigkeit erhalten bleibt. Und genau das haben wir auf diese revolutionären Träger übertragen. Es ist ein sehr intelligentes natürliches System und seine Reproduktion in diesen Trägern gibt ihnen, bei einem geringen Strukturgewicht, eine sehr hohe mechanische Kapazität.„
Konkret druckten die Forscher 3D-Blöcke, die sich wie LEGO-Steine zusammenfügen lassen. Anschließend wird eine Schicht Beton hinzugefügt, um den endgültigen Träger zu bilden. Neben dem reduzierten Gewicht ermöglicht diese Methode eine Struktur, die je nach Bedarf und Bauprojekt moduliert werden kann. Die Blöcke sind leichter zu transportieren und die Installation erfolgt vor Ort, was den damit verbundenen Arbeitsaufwand vereinfacht.
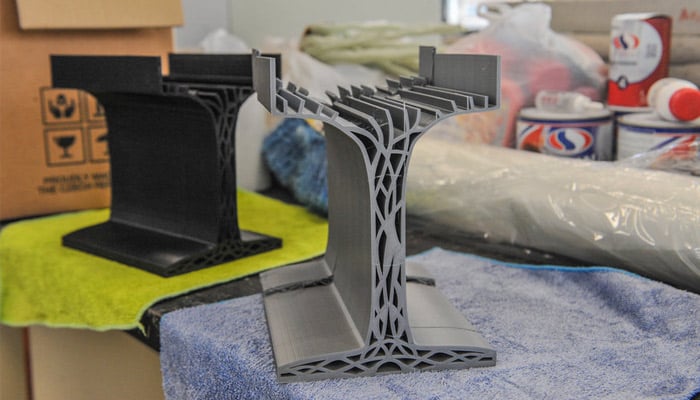
Die Gitterstruktur reduziert das Gesamtgewicht des Trägers.
Miguel Sánchez vom Fachbereich für Systeme und Informatik (DISCA) der UPV schlussfolgert: „Der 3D-Druck ermöglicht es, kundenspezifische Teile sehr nah am Einsatzgebiet herzustellen, was auch den Transport vereinfacht, die Kosten senkt und die Anpassung erleichtert. Durch die Möglichkeit, Träger vor Ort anzupassen, können die Eigenschaften jedes Trägers an die strukturellen Anforderungen an jedem Punkt der Konstruktion angepasst werden. Die Möglichkeit, polymere Materialien zur Herstellung der Träger zu recyceln, reduziert ihren ökologischen Fußabdruck erheblich.„
Was denken Sie über 3D-gedruckte Träger? Könnten Sie in Zukunft eine Alternative sein? Lassen Sie uns zu diesem Thema gerne einen Kommentar da, oder teilen Sie uns Ihre Meinung auf Facebook, Twitter, LinkedIN oder Xing mit. Möchten Sie außerdem eine Zusammenfassung der wichtigsten Neuigkeiten im 3D-Druck und der Additiven Fertigung direkt und bequem in Ihr Postfach erhalten? Dann registrieren Sie sich jetzt für unseren wöchentlichen Newsletter.
Das klingt sehr interessant und zukunftsfähig, wenn die Belastbarkeit dem Spannbeton in nichts nachsteht.
Womit wir beim Thema wären: Beim Spannbeton der 60er/70er-Jahre erleben wir ja heute zunehmend böse Überraschungen, weil es offenbar doch kein „Material für die Ewigkeit“ ist, wie man damals ernsthaft glaubte. Was mich deshalb interessiert: Wie steht es hier mit der Materialalterung; hat man Zeitrafferversuche machen können, ob der Kunststoff mit den Jahren altern wird, bzw. versprödet?
Ich fände es furchtbar, wenn uns in ein paar Jahren solche tollen Konstruktionen um die Ohren fliegen würden.