3D-Druckanwendungen in der Öl- und Gasindustrie
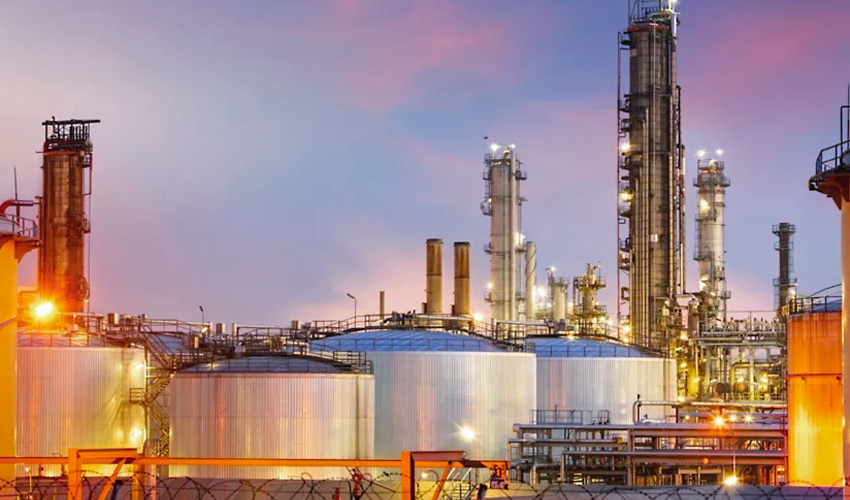
Die Öl und Gasindustrie ist einer der größten Industriezweige der Welt, da er ein wichtiger Teil des Energiesektors ist. Im Jahr 2021 werden weltweit etwa 4,2 Milliarden Tonnen Öl gefördert. Obwohl aufgrund des Klimawandels und der Probleme mit den Lieferländern, wie z. B. dem aktuellen Krieg in der Ukraine, viele nach alternativen Lösungen suchen, ist es nach wie vor die wichtigste Energiequelle, insbesondere zum Heizen. Daher ist es nicht verwunderlich, dass die Unternehmen nach Möglichkeiten suchen, Rohre und andere Komponenten effizienter zu gestalten, um Abfälle und Leckagen zu reduzieren. Eine davon ist, dass sich immer mehr Unternehmen der additiven Fertigung zuwenden, um geometrisch komplexe und kostengünstige Teile herzustellen, insbesondere wenn es um Ersatz- und Austauschteile geht. Wir werfen einen Blick auf einige der führenden Beispiele auf dem Markt.
3D Metalforge und Shell arbeiten bei der Herstellung von Wärmetauscherteilen zusammen
Sie haben sicher schon von Shell gehört, einem der größten Energieunternehmen der Welt. Aber wussten Sie, dass sie sich auch der additiven Fertigung zugewandt hat? Ende 2021 gab 3D Metalforge bekannt, dass das Unternehmen mit Shell Jurong Island, einer chemischen Produktionsstätte von Shell in Singapur, zusammengearbeitet hat, um 3D-gedruckte Wärmetauscherteile auf Anfrage zu liefern. Ausschlaggebend für die einmalige Vereinbarung war die Notwendigkeit für die Ingenieure von Shell Jurong Island, die Vorlaufzeit für die Herstellung von Wärmetauscherrohrkomponenten zu verkürzen, was dank des 3D-Drucks in einer Rekordzeit von nur zwei Wochen gelang. Wärmetauscherrohrkomponenten sind dünnwandige Rohre, die in das Einlassende von Kondensatoren und Wärmetauschern eingesetzt werden, um Wärme zu übertragen und ein Versagen der Rohre zu verhindern, was sie zu kritischen Komponenten in der Öl- und Gasindustrie macht. Durch die Zusammenarbeit mit AM konnte Shell Jurong Island die Lebensdauer der bestehenden Anlagen verlängern, indem es schnell kostengünstige Ersatzteile erhielt.
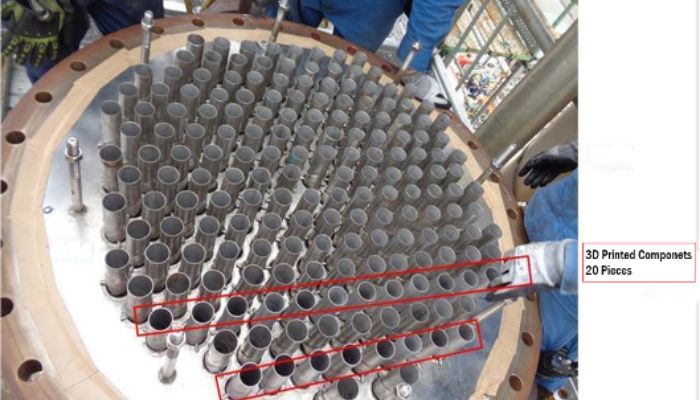
(Bild: 3D Metalforge)
Ein 3D-gedruckter Druckbehälter
AML3D ist ein australischer Hersteller von 3D-Metalldruckern, insbesondere von Geräten, die auf dem CED-Verfahren (Concentrated Energy Deposition) basieren. In diesem Sommer kündigte es ein neues Projekt mit dem US-amerikanischen Ölkonzern ExxonMobil an. Das Projekt umfasst die Konstruktion eines Metalldruckbehälters mit einer Länge von 8 Metern, einem Durchmesser von 1,5 Metern und einem Gesamtgewicht von 8 Tonnen im 3D-Druckverfahren. Es wäre der größte 3D-gedruckte Panzer, der auf dem Markt erhältlich ist. Mit seiner Technologie, die jetzt mit Aluminium-, Titan-, Stahl- und Nickellegierungen kompatibel ist, rechnet AML3D mit einer Produktionszeit von nur 12 Wochen für das Teil.
AML3D erstellt das weltweit größte Bauteil für Öl- und Gaspipelines
AML3D hat sich einen Namen bei der Herstellung großer Metallteile mit seinem drahtadditiven Fertigungsverfahren (WAM®) gemacht, das vom DED abgeleitet ist und einen elektrischen Lichtbogen mit einem zertifizierten Schweißdraht kombiniert. Im November 2021 schufen sie das ihrer Meinung nach größte verifizierte Metallbauteil für Hochdruck-Öl- und Gaspipelines mit Hilfe des 3D-Drucks in einem hybriden Ansatz. Man entschied sich für die additive Fertigung, weil man sich davon eine Verringerung der Umwelt-, Menschen- und Sicherheitsrisiken versprach. Außerdem war es das erste Mal, dass diese Art von Rohrspulenkomponente in 3D aus Metall gedruckt und unabhängig voneinander einem Drucktest unterzogen wurde.
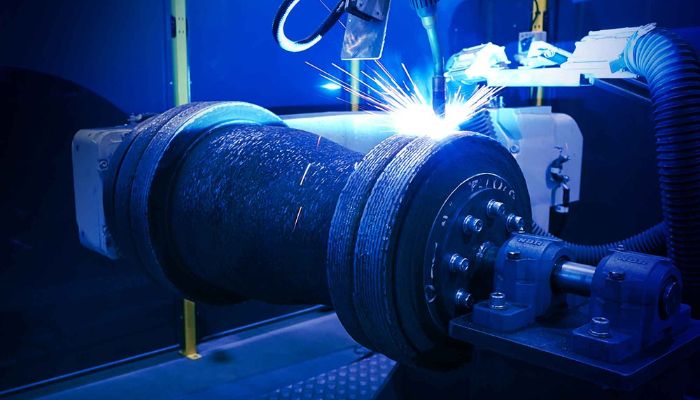
(Bildnachweis: AML3D)
Chevron
Um Probleme in der Lieferkette zu lösen, hat sich Chevron, der sechstgrößte Ölkonzern der Welt, dem 3D-Druck zugewandt. Zu diesem Zweck hat das US-Unternehmen die Dienste von Lincoln Electric in Anspruch genommen, einem Unternehmen, das auf die Herstellung von Produktionswerkzeugen spezialisiert ist. Lincoln Electric bietet nicht nur Schweiß- und Plasmaschneidlösungen an, sondern verfügt auch über eine der größten 3D-Metalldruckfabriken. Gemeinsam waren die beiden Unternehmen in der Lage, Chevrons Bedarf an bedarfsorientierter Fertigung zu decken.
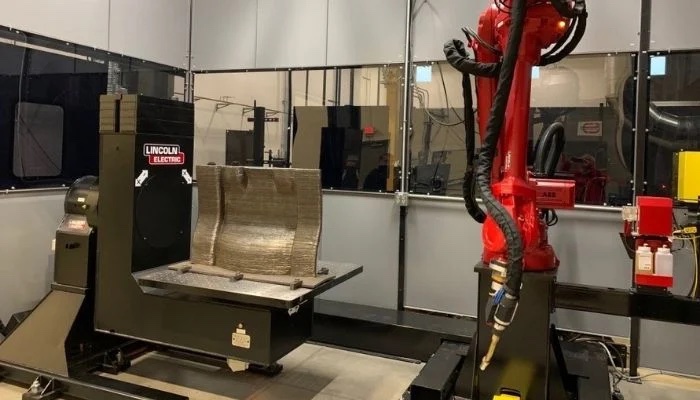
(Bild: Lincoln Electric)
Die Partnerschaft von Velo3D und Duncan Machine Products
Der Hersteller von Anlagen für die additive Fertigung, Velo3D, kündigte für 2020 eine Partnerschaft mit einem wichtigen Akteur der Öl- und Gasindustrie an: Duncan Machine Products (DMP). DMP ist ein wichtiger Lieferant für die Öl- und Gasindustrie sowie für die Luft- und Raumfahrtindustrie und bietet hochpräzise Bearbeitungsdienstleistungen an. Im zweiten Quartal 2020 übernahm DMP das komplette Velo3D-System, das die Flow™-Prepress-Software, den Sapphire® 3D-Drucker und die Assure™-Qualitätsmanagement-Software umfasst. Benny Buller, CEO und Gründer von Velo3D, sagt: „Die additive Fertigung von Metallen ist ein kompatibles Verfahren für die Öl- und Gasindustrie mit ihren komplexen technischen Anforderungen. Mit dieser 3D-Metalldrucklösung will DMP auf die wachsende Marktnachfrage reagieren, die Ausbeute an fertigen Teilen erhöhen und die Vorlaufzeiten verkürzen.
GKN und Hydraulikblöcke
Geschäftsentwicklungsmanager Ümit Aydin, Geschäftsentwicklungsmanager bei GKN, berichtete, dass durch den Einsatz der additiven Fertigung in der Konstruktionspraxis bei GKN eine Gewichtseinsparung von 80 % bei Hydraulikblock-Baugruppen (Adapterblöcken) durch additive Fertigung erreicht wurde. Die Anwendung des 3D-Drucks in hydraulischen Anwendungen ist eine großartige Alternative zu herkömmlichen Fertigungsmethoden, da sie viel leichter sind und an die jeweiligen Anforderungen angepasst werden können. Dieses additive Fertigungsverfahren in Verbindung mit der GKN-Technologie ermöglichte ein Design mit freier Geometrie ohne das Risiko von überlappenden Bohrungen. Während es bei der additiven Fertigung möglich ist, jederzeit Konstruktionsanpassungen vorzunehmen, ist bei herkömmlichen Verfahren ein neues Werkzeug erforderlich, wenn Sie die Position der Öffnungen ändern möchten, um den Ölfluss zu optimieren.
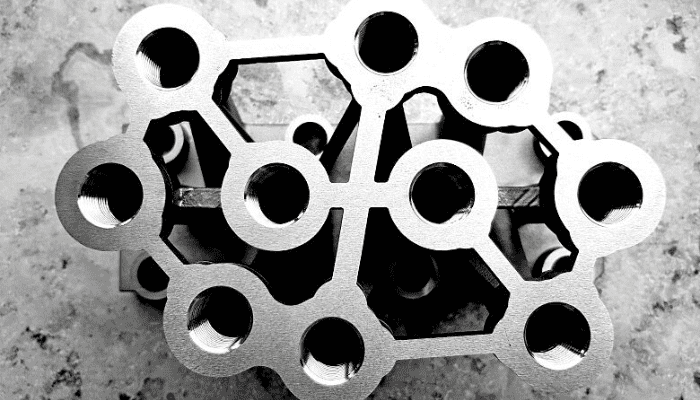
(Bild: GKN)
General Electric
General Electric hat 2018 ein weiteres Projekt, sogar einen Weltrekord, in der Gasindustrie mit additiver Fertigung realisiert. Das US-Unternehmen stellte die größte und wohl auch effizienteste Gasturbine namens Harriet her. Dies führte zu einer Steigerung der Effizienz um 64 %. Dank AM war General Electric in der Lage, komplexe Geometrien wie die Kühlkanäle im Inneren der Gasturbinenschaufeln herzustellen, und auch das Design des Verbrennungssystems des Triebwerks wurde mit 3D-gedruckten Metallteilen optimiert. Dass der maximale Wirkungsgrad erreicht werden konnte, lag vor allem an der Herstellung der komplexen Geometrien, die es den Ingenieuren ermöglichten, die Vormischung von Luft und Kraftstoff in der Turbine selbst zu verbessern.
Markforged entwickelt Klebeband-Pads
Ein weiteres Beispiel für die verschiedenen Anwendungsmöglichkeiten des 3D-Drucks im Öl- und Gassektor ist der Fall eines kanadischen integrierten Öl- und Gasunternehmens, das sich an Markforged wandte, um eine automatisierte Handhabungsmaschine zu entwickeln, die mit Glasfaserverstärkungsbändern umgehen kann. Das Unternehmen hatte Schwierigkeiten, weil die Pads zwischen 115 und 230 Pfund wogen und damit zu schwer waren, um von einer Person gehandhabt zu werden. Die Pad-Handling-Maschine wäre jedoch in der Herstellung zu teuer, obwohl sie den Durchsatz des Werks um 15 Prozent erhöhen sollte. Stattdessen wandte man sich an Markforged Mark Two und den Endlosfaser-3D-Druck, um kundenspezifische Teile für die Maschine zu wesentlich geringeren Kosten herzustellen. Am Ende konnte das Unternehmen 27.000 Dollar an CAD-Kosten einsparen und auch Öl- und Gasanwendungen abseits der Pipelines präsentieren.
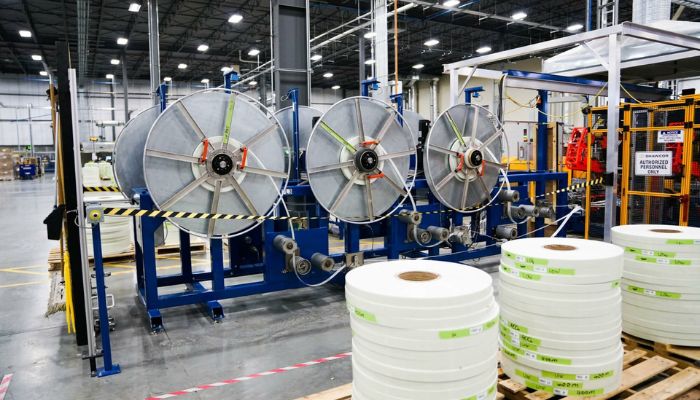
(Bild: Markforged)
3D-gedruckte Rohrschelle von MX3D
MX3D AM hat eine 3D-gedruckte Rohrschelle für die Öl- und Gasindustrie entwickelt. Das Teil wurde in Zusammenarbeit zwischen MX3D, Team Industries und TiaT hergestellt und getestet. Es wurde ein hybrider Ansatz verwendet, bei dem das robotergestützte WAAM-Verfahren (Wire Arc Additive Manufacturing) von MX3D zum Einsatz kam. Die 3D-gedruckte Rohrschelle wurde bereits getestet und mit einem hohen Sicherheitsniveau zertifiziert, was den Nutzen von WAAM im Öl- und Gassektor belegt.
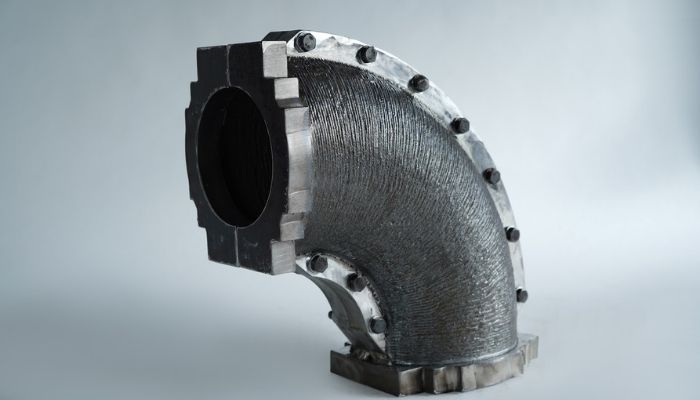
(Bildn: MX3D)
PGV Oil Tools und Desktop Metall
PGV Oil Tools mit Sitz in Karnes City ist ein Fertigungsunternehmen, das sich seit mehr als drei Jahrzehnten auf die Konstruktion und den Bau von Bohrlochwerkzeugen spezialisiert hat. Das 1983 gegründete texanische Unternehmen hat Anlagen für eine Vielzahl von Branchen hergestellt, darunter Öl und Gas, Luft- und Raumfahrt, Robotik und Automatisierung. Das Unternehmen setzt zwar weiterhin auf traditionelle Fertigungsmethoden wie die CNC-Bearbeitung, hat sich aber auch für den 3D-Metalldruck entschieden und nutzt die Vorteile innovativer additiver Fertigungstechnologien voll aus. Für die Herstellung seiner Bohrlochwerkzeuge hat sich PGV für das System Desktop Metal Shop entschieden, mit dem das Unternehmen seine Werkzeuge kostengünstiger und in kürzerer Zeit als mit herkömmlichen Methoden herstellen kann. Darüber hinaus wird durch den Einsatz des 3D-Drucks die Abfallmenge in der Produktion reduziert.
Ersatzteile 3D und Ocyan
Diese beiden Unternehmen, Spare 3D und Ocyan, haben sich zusammengeschlossen, um die additive Fertigung in der Öl- und Gasindustrie zu beschleunigen. Der brasilianische Anbieter von Offshore-Öl- und Gaslösungen Ocyan wandte sich an Spare 3D, ein französisches Unternehmen mit Sitz in Paris, das auf die digitale Inventarisierung von Ersatzteilen für die additive Fertigung spezialisiert ist. Sie nutzen die umfassende DigiPART-Software, die es ihnen ermöglicht, die additive Fertigung auf Ersatzteile anzuwenden, indem sie Veralterung, Vorlaufzeiten, Mindestbestellmengen oder Lagerbestände reduzieren. Es ist ihnen gelungen, diese Software in ihre Ersatzteillieferkette zu integrieren. Dies war das erste von dem Unternehmen gebaute Teil, mit dem ein gemeinsamer Rahmen für die Entwicklung einer Roadmap für die Einführung der additiven Fertigung von Ersatzteilen geschaffen wurde. Die beiden Unternehmen analysierten 17.000 Teile aus dem Bestand von Ocyan, um ihr Potenzial für die Produktion mit additiver Fertigung zu bewerten. Das Ergebnis sind lebensfähige Teile, die 11 % der insgesamt analysierten Teile ausmachen.
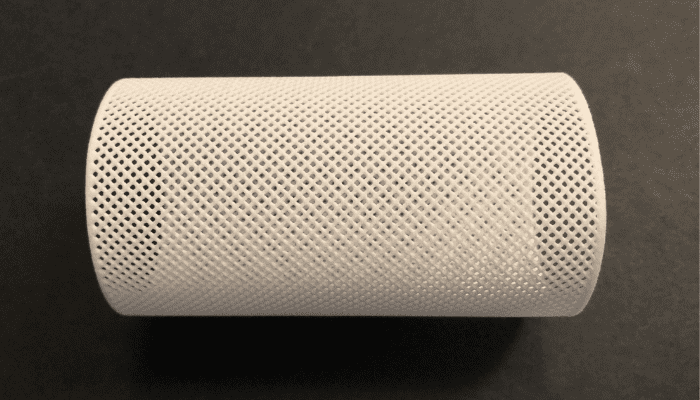
(Bild: Spare Parts)
Eine 3D-gedruckte Offshore-Komponente
Im Mai 2021 gaben die französischen Partner Vallourec und Total zum ersten Mal die erfolgreiche Installation von 3D-gedruckten Wasserbüchsen in der Nordsee bekannt. Zur Erinnerung: Ein Waterbushing ist ein Bauteil, das in der Öl- und Gasbohrindustrie verwendet wird, um Kohlenwasserstoffspitzen aus Bohrlöchern während deren Bau zu blockieren. Sie ist daher ein Schlüsselelement zur Gewährleistung der Sicherheit der Mitarbeiter auf der Baustelle. Die beiden französischen Gruppen haben sich daher der additiven Fertigung zugewandt, insbesondere dem WAAM-Verfahren, um ein Teil zu entwickeln, das 1,2 Meter hoch ist und 220 Kilo wiegt, d. h. eine Reduzierung um 50 %.
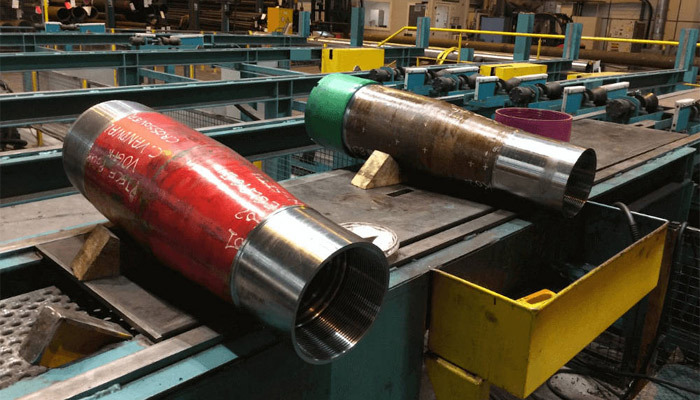
(Bild: Vallourec)
Was halten Sie von dieser Rangliste der 3D-Druckanwendungen im Öl- und Gassektor? Lassen Sie uns dazu gerne einen Kommentar da oder teilen Sie es uns auf Facebook, Twitter, LinkedIN oder Xing mit. Möchten Sie außerdem eine Zusammenfassung der wichtigsten Neuigkeiten im 3D-Druck und der Additiven Fertigung direkt und bequem in Ihr Postfach erhalten? Dann registrieren Sie sich jetzt für unseren wöchentlichen Newsletter!
*Titelbildnachweis: Ansys