3D-Druck von Verbundwerkstoffen erschließt Anwendungen in der Luft- und Raumfahrt und Robotik in China
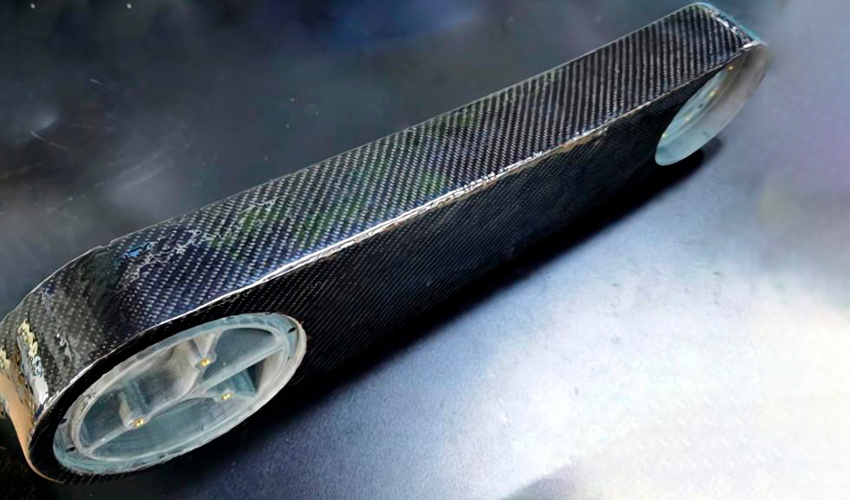
Obwohl der 3D-Druck mit Polymeren und Metallen in den letzten Jahren stark in den Vordergrund gerückt ist, gibt es eine Materialfamilie, die im Bereich der additiven Fertigung ein immenses Wachstum verzeichnet: Verbundwerkstoffe. Verbundwerkstoffe für den FFF-3D-Druck sind so stabil wie Metall und so leicht wie viele Polymere und bestehen häufig aus einer Polymermatrix und Füllstoffen wie Glas- oder Kohlenstofffasern. Sie sind inzwischen so weit verbreitet, dass der weltweite Markt für den 3D-Druck von Verbundwerkstoffen bis 2030 voraussichtlich 490,47 Millionen US-Dollar erreichen wird, nachdem er 2023 bereits einen Wert von 198,31 Millionen US-Dollar erreicht hat. Die Bedeutung von Verbundwerkstoffen für den 3D-Druck wurde nun auch vom Institute of Industrial New Materials in Dezhou, China, erkannt.
Das im Januar 2021 gegründete Institut widmet sich der Erforschung, Entwicklung und Vermarktung von Verbundwerkstoffen für Anwendungen in Bereichen wie Schifffahrt, 5G-Kommunikation, fortschrittliche Fertigungsverfahren und High-End-Geräte. Als provinzielle „F&E-Einrichtung neuen Stils“ in China hat es auch den Vorteil der Hinwendung zum 3D-Druck erkannt. In Zusammenarbeit mit INTAMSYS führt das Institut zwei Initiativen zur Anwendung des 3D-Drucks bei der Entwicklung von Produktteilen aus Verbundwerkstoffen an.
Traditionelle Fertigung von Formteilen durch 3D-Druck ersetzt
Es ist nicht neu, dass der 3D-Druck als Ersatz oder sogar als Ergänzung zu vielen traditionellen Produktionsverfahren angepriesen wird. Der Grund dafür ist, dass sich mit dem 3D-Druck komplexe Geometrien leichter realisieren lassen. Außerdem kann das Design noch weiter optimiert werden, um Kosten und Durchlaufzeiten zu reduzieren.
In einem Fall wurde das Institut mit der Entwicklung von Ansaugrohren für ein bestimmtes Flugzeugtriebwerk beauftragt. Ansaugkrümmer sind kritische Komponenten innerhalb von Triebwerkssystemen, die sich direkt auf die Gesamtleistung des Motors auswirken, da sie den Zylindern Frischluft zuführen und so das richtige Gemisch aus Luft und Kraftstoff gewährleisten, das in einem Motor verbrannt wird. Die Entwicklung kann sich jedoch aufgrund ihres komplexen Designs sowie der Schwierigkeiten bei der Herstellung von Formen, der hohen Kosten und des zeitaufwändigen Vibrationsschweißverfahrens schwierig gestalten. An dieser Stelle kam der 3D-Druck ins Spiel.
Das Institut beschloss, diese Ansaugrohre im FFF-3D-Druckverfahren herzustellen. Genauer gesagt nutzte man den 3D-Drucker 610HT und PEEK-CF von INTAMSYS. Diese wurden aufgrund der Materialleistung, der Ausrüstungsmöglichkeiten und der Serviceunterstützung ausgewählt.
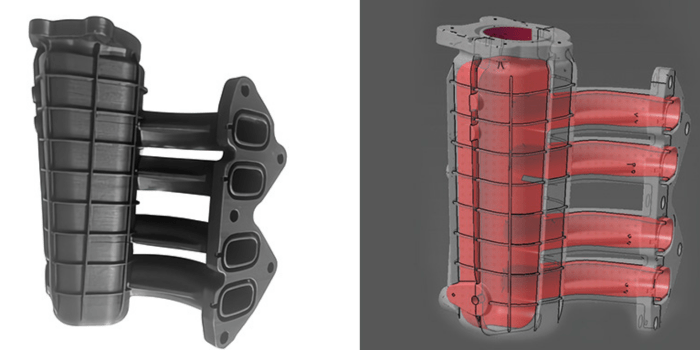
Der fertige (linke) Konstruktionskrümmer und die Konstruktion des Teils einschließlich des Innenraums (rechts)
Wir haben Ihnen bereits über den FUNMAT PRO 610HT berichtet. Der großformatige 3D-Drucker mit zwei Düsen wurde für den Druck von Hochtemperatur-Thermoplasten wie PEEK, ULTEM und PPSU entwickelt und kann eine breite Palette von Materialien verarbeiten, darunter auch kundenspezifische Polymere. Möglich wird dies durch Düsen, die eine Temperatur von bis zu 500 °C erreichen können, und eine Kammer, die auf 300 °C erhitzt werden kann. Dies ermöglicht den Druck von Hochleistungsmaterialien ohne Verformung.
Darüber hinaus optimierten die Experten des Instituts und von INTAMSYS mithilfe von DfAM das Design und den Druckprozess für die Herstellung des 218,4 × 216,4 × 95,4 mm großen Teils. Dies führte zu einer Gewichtsreduzierung von 30 %, wobei die Dicke der dünnsten Wand nur 1,7 mm beträgt. Die Abmessungen des Teils konnten für eine präzise Passform gesteuert werden, und Tests ergaben eine mechanische Festigkeit von 100 mPA, die herkömmliche spritzgegossene PA66-GF-Produkte um mehr als 30 % übertrifft, während sie gleichzeitig Langzeittemperaturen von 114 °C standhält.
In Anbetracht der Tatsache, dass mit herkömmlichen Spritzgussverfahren hergestellte Teile (einschließlich Werkzeugbau) etwa 27.803 US-Dollar gekostet hätten, bei einer Vorlaufzeit von 45 Tagen, wurde der Wert des 3D-Drucks sofort deutlich. Das Institut war in der Lage, die Ansaugkrümmer als ein einziges integriertes Teil herzustellen, wodurch die Kosten auf ein Zehntel der Kosten für herkömmliche Verfahren gesenkt und die Produktionsvorlaufzeit auf nur 4-7 Tage verkürzt werden konnte.
Hybride Fertigung mit 3D-Druck von Verbundwerkstoffen
Natürlich ist der 3D-Druck von Verbundwerkstoffen nicht nur als Ersatz für traditionelle Verfahren geeignet. Er kann auch in bestehende Prozesse integriert werden. Dies hat das Institut in Zusammenarbeit mit einer chinesischen Universität getan, um einen Roboter-Manipulatorarm aus Verbundwerkstoffen zu entwickeln.
Zur Herstellung des Manipulatorarms wurden beispielsweise der FUNMAT PRO 610HT und PEEK-CF für die interne Stützstruktur verwendet. Das resultierende Bauteil war nicht nur groß, sondern wies auch gekrümmte Oberflächen, ein hohes Verhältnis von Steifigkeit zu Gewicht und eine außergewöhnliche spezifische Festigkeit auf. Dies zeigt die Fähigkeit des 3D-Drucks von Verbundwerkstoffen zur Herstellung komplexer, leistungsstarker Teile.
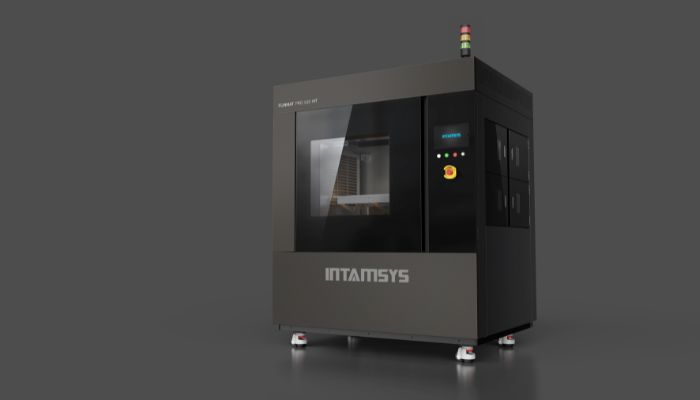
Der FUNMAT PRO 610HT wurde sowohl für die Ansaugrohre als auch für das Roboterarmteil verwendet.
Die Universität verwendete dann eine vorimprägnierte Schichtmethode, um die 3D-gedruckte Struktur mit Kohlenstofffasern zu umhüllen. Dies ermöglichte die kostengünstige und schnelle Herstellung eines leichten, robusten Manipulatorarms aus Verbundwerkstoff durch 3D-Druck. Und das Beste daran? Es war möglich, den kostspieligen Formenbau zu umgehen und dennoch eine strukturelle Festigkeit zu erreichen, die mit der von Aluminiumlegierungen vergleichbar ist. Darüber hinaus konnte der 3D-Druck von Verbundwerkstoffen auch mit anderen traditionellen Techniken wie dem traditionellen Aufwickeln von Filamenten, dem automatisierten Layup und dem Formpressen kombiniert werden.
In jedem Fall hat das Institut für Neue Industrielle Werkstoffe die Vorteile aufgezeigt, die sich aus dem Ersatz und der Ergänzung herkömmlicher Verfahren durch den 3D-Druck von Verbundwerkstoffen ergeben. Nämlich durch die Steigerung der Effizienz und die Senkung der Kosten bei der Herstellung von Verbundwerkstoffteilen.
Was halten Sie vom Institut für Neue Industrielle Werkstoffe und den 3D-Druck von Verbundwerkstoffen? Lassen Sie uns dazu einen Kommentar da, oder teilen Sie es uns auf Facebook oder LinkedIN mit. Möchten Sie außerdem eine Zusammenfassung der wichtigsten Neuigkeiten im 3D-Druck und der Additiven Fertigung direkt und bequem in Ihr Postfach erhalten? Dann registrieren Sie sich jetzt für unseren wöchentlichen Newsletter.
*Titelbildnachweis: Das Bauteil des Roboterarms, gedruckt im 3D-Verbunddruckverfahren (Bild: INTAMSYS)