Wie wird der 3D-Druck bei BMW genutzt?
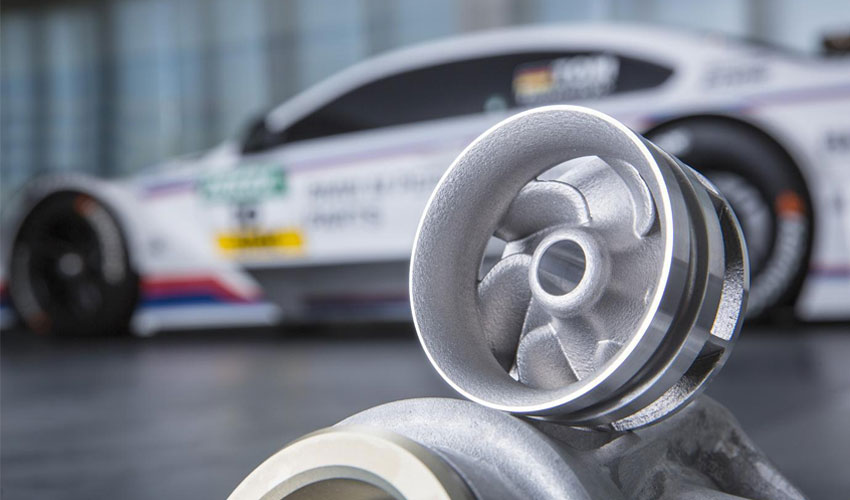
Von BMW haben wir bereits einiges hinsichtlich der additiven Fertigung gehört. Erst letztens gewannen sie für die Anwendung der neuen Technologie beim BMW i8 Roadster den Altair Enlighten Award. Es ist nicht verwunderlich, dass sie innerhalb der neuen Technologie so erfolgreich sind. Bereits 25 Jahre beschäftigt sich das Unternehmen mit der additiven Fertigung und entwickelten zahlreiche spannende Projekte, unter anderem den Campus für additive Fertigung, eine komplex gestaltete Motorradkarosserie und der personalisierte MINI.
Der Entwicklung ist noch lange kein Ende gesetzt und um mehr über den 3D-Druck bei BMW zu erfahren, haben wir uns mit Dr. Jens Ertel unterhalten, dem Leiter des Additive Manufacturing Centers der BMW Group. Er ist seit 1995 bei BMW Group tätig und wird zukünftig die Leitung des neuen Additive Manufacturing Campus übernehmen.
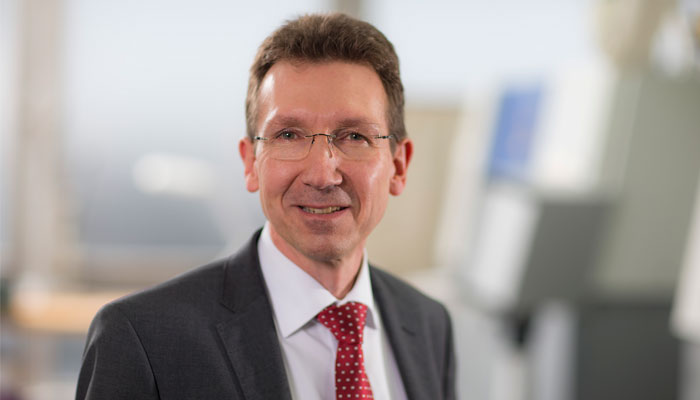
Dr. Jens Ertel
Können Sie sich kurz vorstellen und uns erzählen, wie BMW mit der additiven Fertigung in Berührung kam?
Additive Fertigungsverfahren setzen wir bei der BMW Group bereits seit 1991 – also schon seit über 25 Jahren – ein. Damals haben wir mit der Produktion von Prototypenteilen für Konzeptfahrzeuge angefangen. Dieser sehr frühe Einsatz von additiven Verfahren hat uns in den vergangenen Jahren zu einem enormen Vorsprung im 3D-Druck-Bereich verholfen.
In welchen Bereichen nutzt BMW gezielt die additive Fertigung? Welche Vorteile bietet der Einsatz von 3D-Druck insbesondere im Automobilbereich gegenüber herkömmlichen Fertigungsprozessen?
Heute ist unser Aufgabenbereich sehr viel vielfältiger und reicht von Ersatzteilen für klassische Fahrzeuge über Werkzeuge bis hin zu Teilen, die wir für die Serienproduktion von Fahrzeugen produzieren. Durch die hohe Gestaltungsfreiheit von additiv gefertigten Bauteilen, ergeben sich neue Konstruktionsansätze, die neue Designs und Funktionen ermöglichen. Seit neuestem haben unsere MINI-Kunden sogar die Möglichkeit, die Dekorleiste für die Beifahrerseite im Innenraum und die Einleger des Seitenblinkers selbst zu designen. Die Teile werden dann bei uns individuell gedruckt. Im Vergleich zu herkömmlichen Produktionsmethoden sind Bauteile innerhalb von wenigen Tagen verfügbar. Bei herkömmlichen Verfahren müssen wir immer die Herstellungszeit von Werkzeugen einkalkulieren.
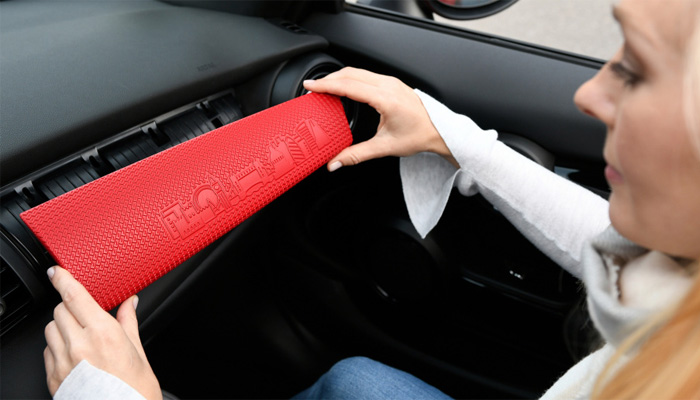
personalisiert Dekorleiste im neuen MINI
Mittlerweile bearbeiten wir in unserem Additive Manufacturing Center jährlich etwa 30.000 Prototypenaufträge und produzieren mehr als 140.000 Bauteile. Hierzu setzen wir auf der einen Seite „state-of-the-art“ 3D-Drucktechnologien ein, aber wir forschen auch gemeinsam mit externen Partnern an neuen Technologien.
Können Sie uns etwas genauer in das Projekt des 3D-gedruckten Motorradrahmens einführen? Welche Technologien, Materialien und Prozesse wurden für dieses spezifische Projekt verwendet?
Unsere Experten von BMW Motorrad, aus dem Fachbereich der Additiven Fertigung sowie des Generative Designs haben an einer Konzeptstudie gearbeitet und gemeinsam Ideen entwickelt, wie Motorradrahmen künftig aussehen können. Basierend auf den Anforderungen hinsichtlich der Steifigkeit und des Gewichts des Bauteils haben sie mithilfe von Generative Design-Algorithmen eine komplexe Struktur entwickelt. Da die Geometrie dieses Bauteils sehr komplex ist, kam für uns nur die Herstellung im 3D-Druck-Verfahren in Frage. Die Konzeptstudie wurde einmalig durch selektives Laserstrahlschmelzen aus Aluminium hergestellt.
Es handelt sich um ein Forschungsprojekt und das Motorrad kann nicht käuflich erworben werden.
Vor kurzem kündigte Ihr Unternehmen die Eröffnung eines additiven Fertigungscampus im Jahr 2019 an. Welche Visionen stehen dahinter? Und global gesehen, wie sehen Sie die Zukunft von 3D-Druck in der Automobilindustrie (Mass Customization, Herstellung Ersatzteile, On Demand Supply Chain …)
Im neuen AM Campus werden wir unsere Kompetenz in der additiven Fertigung weiter ausbauen. Schwerpunkt des Campus wird die Produktion von Teilen für die Prototypenfertigung, für die Serienproduktion und von individualisierten Fahrzeugteilen sein. In eigenen Vorentwicklungsbereichen werden neue Technologien von Tech Start-Ups wie Desktop Metal oder Carbon erprobt und zur Serienreife gebracht. Wir werden dort auch neue Automatisierungskonzepte umsetzen, die die wirtschaftliche Fertigung von Serienkomponenten ermöglichen und damit bei der Beschleunigung der Fahrzeugentwicklung helfen.
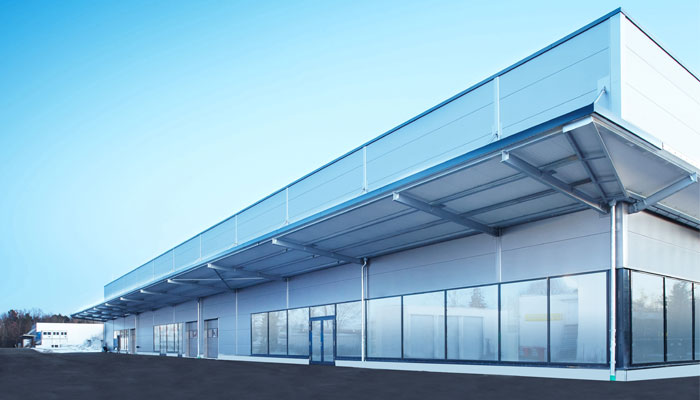
Zukünftiger Campus für die additive Fertigung
Synergien erwarten wir aus gemeinsamen Projekten in der gesamten Prozesskette, angefangen vom Werkstoff über Anlagentechnik bis hin zu IT-Systemen. Unsere Partner lernen dadurch die Anforderungen aus der Automobilproduktion kennen und wir lernen – durch einen frühen Zugang zu neuen Technologien – verfahrensspezifische Besonderheiten von Anfang an zu berücksichtigen.
Innerhalb unseres Produktionsnetzwerks wird der neue Campus wie ein Pilotwerk neue Technologien der additiven Fertigung vorantreiben und diese dann dem Netzwerk zur Verfügung stellen.
Um mehr über den 3D-Druck bei BMW zu erfahren, besuchen Sie Ihre offizielle Website und verfolgen Sie die neusten Pressemitteilungen.
Was halten Sie von der Umsetzung der 3D-Technologie bei BMW? Teilen Sie uns Ihre Meinung mit und hinterlassen Sie uns ein Kommentar unten oder auf Facebook, Twitter oder Google+. Und denken Sie daran sich für unseren wöchentlichen Newsletter kostenlos anzumelden, um keine Neuigkeiten im 3D-Druck mehr zu verpassen!